Workflow Integration: Metal Fabrication in Electronics Manufacturing
We’re diving deep into how metal fabrication fits into the broader electronics production workflow. Whether you’re a designer sketching prototypes or a decision-maker calling the shots, understanding this integration can make or break your project.
2/26/20256 min read
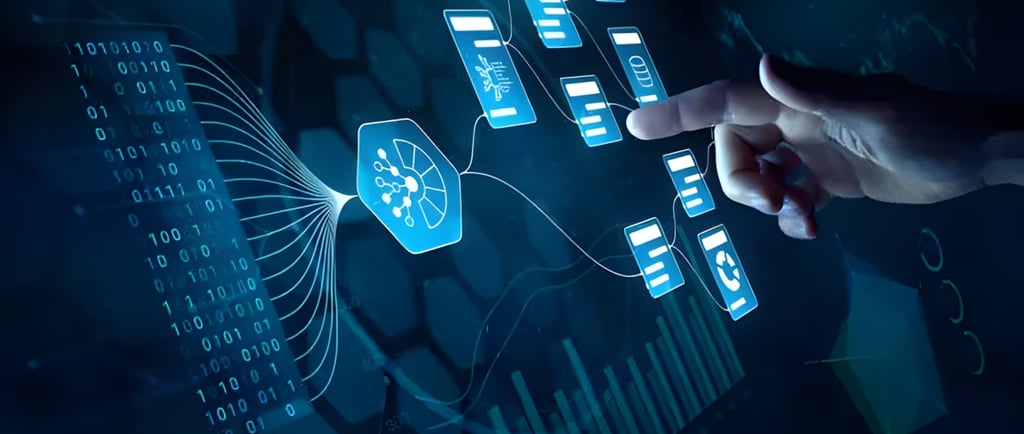
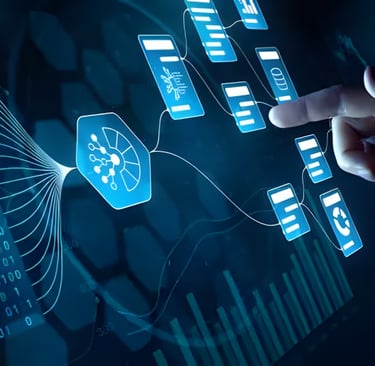
Picture this: You’re designing the next big thing in electronics—a sleek, powerful device that’s about to change the game. You’ve got the circuits mapped out, the software humming, and a vision that’s keeping you up at night (in a good way). But then comes the reality check: How do you house it, cool it, and make it last? That’s where metal fabrication swoops in—not just as a sidekick, but as a core player in the electronics manufacturing process. From assembly to testing, it’s the unsung hero that turns your brilliant ideas into tangible, market-ready products.
In this article, we’re diving deep into how metal fabrication fits into the broader electronics production workflow. Whether you’re a designer sketching prototypes or a decision-maker calling the shots, understanding this integration can make or break your project. Let’s explore how it all comes together—step by step, challenge by challenge, and innovation by innovation.
Understanding Metal Fabrication in Electronics
If you’ve ever bent a paperclip into a new shape, you’ve got the basic gist of metal fabrication—except swap the paperclip for high-grade aluminum or copper, and add some serious precision. Metal fabrication is the art and science of cutting, bending, welding, and shaping metal into components that fit your design like a glove. In electronics, we’re talking about parts like enclosures to protect delicate circuits, heat sinks to keep things cool, or connectors that make everything click.
The metals themselves are the stars of the show. Aluminum’s lightweight and corrosion-resistant, perfect for portable devices. Copper’s a conductivity champ, ideal for heat dissipation. Steel? Tough as nails for structural support. Each one brings something to the table, and as a designer, you’re the one picking the lineup based on what your device demands.
Think of your latest project—maybe it’s a rugged IoT sensor or a shiny new smartphone. Those metal bits aren’t just decorative; they’re functional necessities born from fabrication. And that’s just the starting line.
Metal Fabrication in the Design and Prototyping Phase
Let’s rewind to the early days of your project. You’re sketching concepts, tweaking CAD files, and dreaming up something groundbreaking. Here’s where metal fabrication first steps in—not as a final act, but as a collaborator. Prototyping is all about testing your ideas, and fabricated metal parts help you see if your vision holds up in the real world.
Imagine you’re designing a drone. You need a lightweight frame that’s still strong enough to handle a crash landing (because, let’s be honest, prototypes crash). You sketch it, send it to your fabrication team, and soon you’re holding a custom-cut aluminum chassis. It’s not perfect yet—maybe it’s too heavy or the mounting holes don’t align—but that’s the point. You tweak, they re-cut, and suddenly you’re iterating faster than you can say “version 2.0.”
This phase is a dance between you, the engineers, and the fabricators. You’re specifying tolerances tighter than a budget meeting, and they’re figuring out how to make it happen with CNC machines or laser cutters. It’s messy, it’s creative, and it’s where the magic starts. As a decision-maker, this is also where you see the value of investing in a solid fabrication partner—because a sloppy prototype can derail your timeline before you’ve even begun.
Integration into the Assembly Process
Fast forward to assembly. Your prototype’s approved, and now it’s time to build the real thing. This is where metal fabrication shifts from concept to concrete, slotting into the production line like a puzzle piece. Those enclosures you designed? They’re now cradling circuit boards. The brackets you tweaked? They’re holding components in place while the soldering irons buzz.
Take a laptop, for example. The sleek metal body isn’t just for looks—it’s a fabricated shell that aligns perfectly with the motherboard, battery, and screen. During assembly, workers (or robots) snap these parts together, relying on the fabricators’ precision to ensure everything fits. One misaligned screw hole, and you’re looking at delays or rework—nightmares for any project lead.
This stage is all about teamwork. The assembly crew needs fabricated parts delivered on time and spec’d right, while you, the designer, are counting on those parts to perform as promised. It’s a high-stakes relay race, and metal fabrication is passing the baton without dropping it.
Enhancing Functionality Through Fabrication
Here’s where things get fun. Metal fabrication isn’t just about structure—it’s about making your device work better. Let’s talk heat sinks. You’ve got a processor running hot enough to fry an egg, and without a well-crafted copper or aluminum heat sink, your device is toast (literally). Fabrication shapes those fins just right, maximizing surface area to wick heat away.
Or consider shielding. Electromagnetic interference (EMI) can turn your gadget into a glitchy mess. A fabricated metal enclosure—say, a steel or aluminum box—acts like a Faraday cage, keeping those pesky waves out. It’s not optional; it’s essential, especially if you’re aiming for regulatory approval.
And don’t get me started on miniaturization. You’re designing wearables or tiny sensors, right? Fabrication techniques like precision stamping or micro-welding let you shrink components without sacrificing strength. It’s like fitting a full orchestra into a single violin case—challenging, but doable with the right tools.
As a designer, this is your playground. You’re dreaming up solutions, and fabrication makes them real. As a decision-maker, it’s your ROI—better performance, happier customers, fewer returns.
Quality Control and Testing Phase
You’ve assembled your masterpiece, but it’s not ready for the spotlight yet. Testing is where metal fabrication proves its worth—or gets sent back to the drawing board. Every part gets put through the wringer: Does the enclosure hold up under a drop test? Can the heat sink handle a thermal stress run? Are the connectors conducting as they should?
This isn’t just about checking boxes. Standards like IPC or ISO loom large, and regulators don’t mess around. Your fabrication team’s precision—down to the micrometer—ensures your device passes muster. I’ve seen projects where a slightly warped chassis threw off alignment, failing vibration tests and costing weeks. Quality control catches that before it’s a crisis.
You’re in the loop here, too. Maybe you’re reviewing test data with the QA team, or maybe you’re the one signing off on the final green light. Either way, fabrication’s role is clear: It’s the backbone that lets your device survive the gauntlet and hit the market strong.
Challenges and Solutions in Workflow Integration
Of course, it’s not all smooth sailing. Integrating metal fabrication into electronics workflows comes with headaches. Tolerances are a big one—your design might call for a 0.01mm gap, but the cutting tool’s off by 0.02mm, and suddenly nothing fits. Material compatibility can trip you up, too—pair the wrong metals, and you’ve got corrosion eating away at your product.
Then there’s speed. You’re on a tight deadline, but fabrication’s bottlenecked because the shop’s swamped. Sound familiar? These are the moments that test your patience—and your team.
But here’s the good news: Solutions abound. Advanced tools like CNC machining and laser cutting nail those tight tolerances every time. Automation speeds things up, churning out parts while you sip your coffee. And real-time communication—think cloud-shared CAD files or daily check-ins—keeps everyone aligned. I’ve seen teams turn chaos into clockwork by leaning on these fixes, and it’s a game-changer for any project lead.
The Future of Metal Fabrication in Electronics Manufacturing
So, where’s this all headed? The future’s looking shiny—literally. Additive manufacturing, like 3D metal printing, is shaking things up. Imagine printing a custom heat sink with intricate lattice designs you couldn’t machine before. It’s not sci-fi; it’s happening now, and it’s cutting waste while boosting performance.
Smart materials are creeping in, too—think metals that adapt to temperature or stress. And sustainability? Fabricators are recycling scraps and optimizing cuts to shrink their footprint, which matters if your brand’s going green.
For you, the designer, this means more freedom to innovate. For you, the decision-maker, it’s efficiency and cost savings wrapped in a bow. The workflow’s evolving, and metal fabrication’s leading the charge.
Conclusion
From the first sketch to the final test, metal fabrication is the thread weaving through electronics manufacturing. It’s there in the prototypes you tweak, the assemblies you oversee, and the devices your customers love. It’s not just a step—it’s a partnership, one that demands precision, creativity, and a little grit.
So, next time you’re dreaming up a gadget or crunching production numbers, give a nod to the fabricators making it happen. Better yet, dive into these advancements yourself—whether it’s a new tool or a fresh approach. Your project deserves it, and the results might just surprise you.