Plastic Injection Molding: Precision Manufacturing Solutions
Plastic injection molding is a cornerstone of modern manufacturing, delivering high-precision, repeatable, and cost-effective solutions for producing complex plastic parts. We specialize in transforming your ideas into reality with state-of-the-art technology, expert craftsmanship, and a commitment to quality that meets the demands of industries like automotive, medical, consumer goods, and beyond.


Tooling
Our expert engineers craft durable, precision molds tailored to your project’s requirements.
Injection Molding
State-of-the-art machines inject molten plastic into molds with pinpoint accuracy
Design & Prototyping
We collaborate with you to design molds using advanced CAD software, followed by rapid prototyping to test concepts
Finishing & Quality Control
Parts undergo rigorous inspection and finishing processes to ensure flawless performance.
Delivery
Fast turnaround times get your products to market quickly and reliably.
Advantages of Our Plastic Injection Molding Services
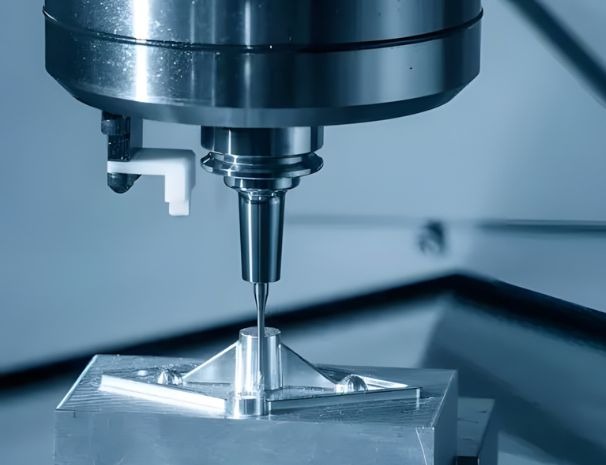
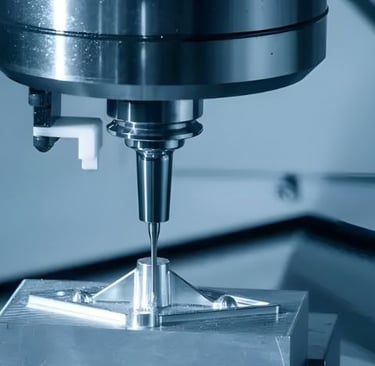



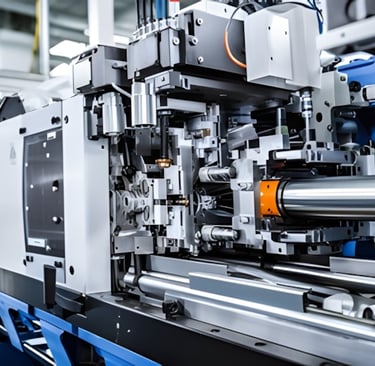
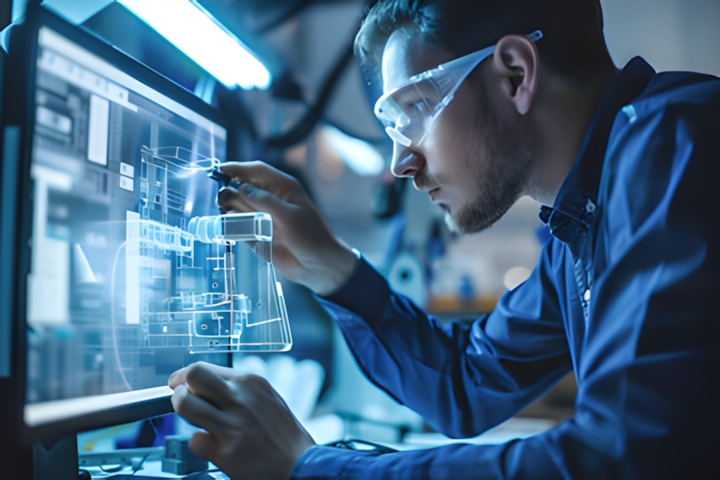
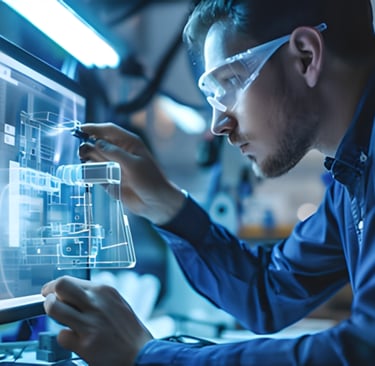
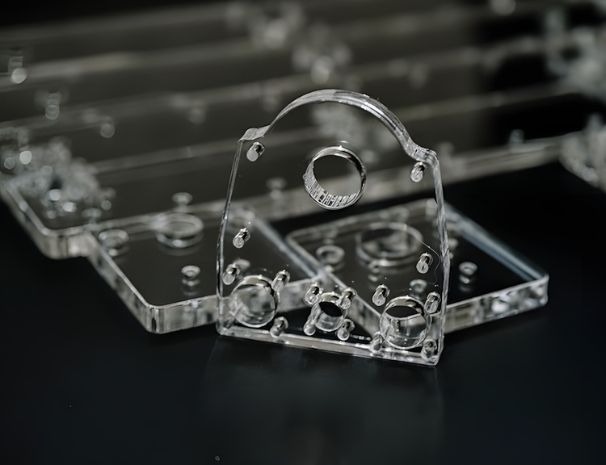
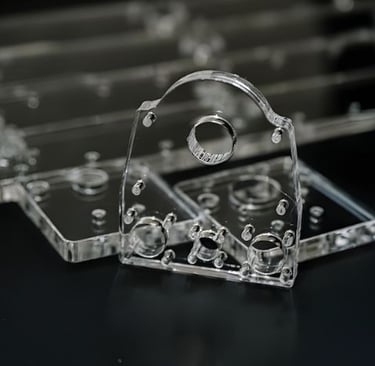


We set ourselves apart by delivering exceptional plastic injection molding services tailored to your needs. Partner with Peakingtech and experience our decades of expertise, cutting-edge equipment, and a customer-first approach for your project.
Unmatched Precision
Fast Turnaround Times
Cost-Effective Solutions
Cutting-Edge Technology
Wide Material Selection
Scalable Production
With streamlined processes and a dedicated team, we deliver projects quickly—whether it’s a prototype in days or high-volume production in weeks—keeping you ahead of deadlines
Our advanced machinery and skilled engineers achieve tolerances as low as ±0.001 inches, ensuring every part meets your exact specifications with zero compromise on quality.
By optimizing material use and minimizing waste, we offer competitive pricing without sacrificing durability or performance, maximizing your return on investment.
Our state-of-the-art injection molding machines and 3D modeling tools ensure consistent results, even for the most complex geometries and challenging materials.
Choose from an extensive range of high-performance plastics—ABS, polypropylene, PEEK, and more—plus sustainable options to meet both functional and environmental goals.
Whether you need a small batch for testing or millions of units for market rollout, our flexible capacity adapts seamlessly to your project scale.
What Factors Affect the Cost of Plastic Injection Molding?
Understanding the cost of plastic injection molding is key to planning your project effectively. We optimize these factors to deliver cost-effective injection moulding solutions without compromising quality.
Part Complexity: Simple designs with basic shapes cost less to mold, while intricate geometries or features like undercuts and threads require advanced tooling, increasing expenses.
Mold Design and Fabrication: Custom molds, especially those made from high-grade steel for durability, represent a significant upfront investment—typically $1,000 to $50,000+ depending on complexity.
Material Selection: Standard plastics like ABS or polypropylene are affordable, whereas specialty resins (e.g., PEEK or reinforced composites) drive up costs due to their higher price per pound.
Production Volume: Low-volume runs (e.g., prototypes) have a higher cost per part due to mold setup, while high-volume production spreads the tooling cost, lowering the unit price.
Cycle Time: Faster cycles reduce labor and machine time, cutting costs, but complex parts with longer cooling or injection phases may increase production time and price.
Tolerances and Finishing: Tight tolerances (±0.001 inches) or secondary processes like painting, polishing, or assembly add to labor and equipment costs.
Tooling Lifespan: Aluminum molds are cheaper but wear out faster (e.g., 10,000 cycles), while steel molds cost more upfront but last longer (e.g., 1M+ cycles), affecting long-term pricing.
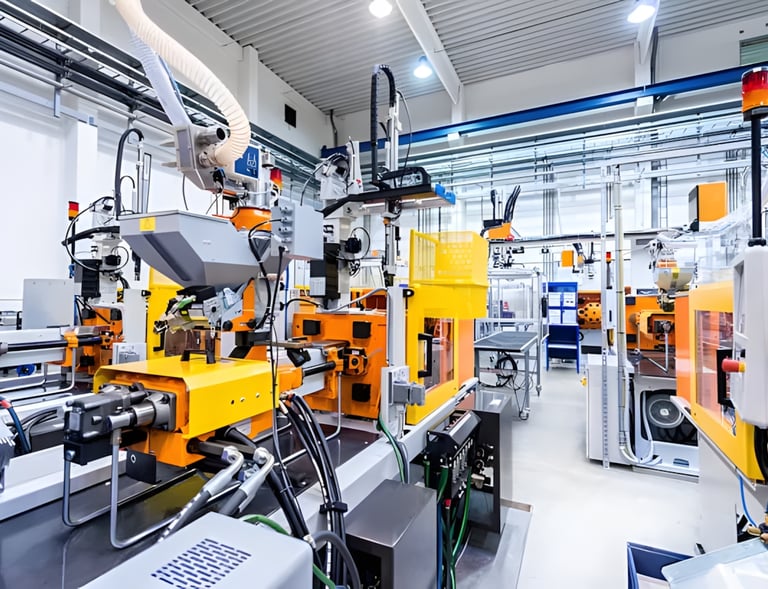
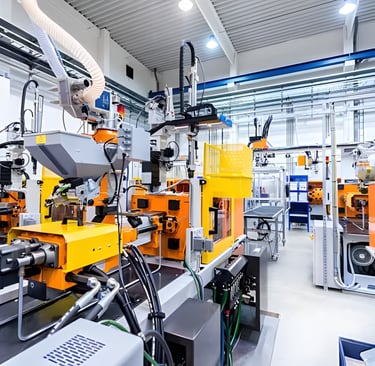
When it comes to injection molding for plastic parts or enclosures, the cost advantage of Made-in-China manufacturing is undeniable—just ask Tim Cook, who has long endorsed China’s precision and efficiency in production. With lower labor costs, cutting-edge facilities, and a robust supply chain, Chinese mold manufacturing delivers high-quality molds at a fraction of Western prices, slashing your tooling expenses by up to 50%.
Missing out on this could become your unaffordable competitive disadvantage as rivals optimize their budgets and accelerate production. Don’t let costs hold you back—request quotes now for your molds and discover how Peakingtech leverages China’s expertise to help you cut prices without compromising quality.
Watch: How Plastic Injection Molding Powers Your Products
Dive into the world of plastic injection molding with our exclusive video! Discover how this precision manufacturing process transforms raw materials into the high-quality parts that power your everyday products—from automotive components to medical devices. See our cutting-edge technology in action and learn why Peakingtech is your go-to partner for innovative, cost-effective solutions. Watch now and unlock the potential of plastic injection molding for your next project!

Peakingtech was a game-changer for my product development journey! At the initial stage, they expertly crafted a steel injection mold that not only halved the cost but also delivered excellent results for low-volume injection molding. Their ability to balance cost-efficiency with high-quality output was truly impressive. Thanks to their expertise, I was able to move forward with my project without compromising on quality. Highly recommend Peakingtech for anyone looking for smart, cost-effective manufacturing solutions!
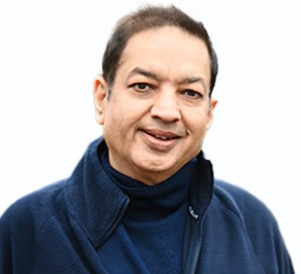
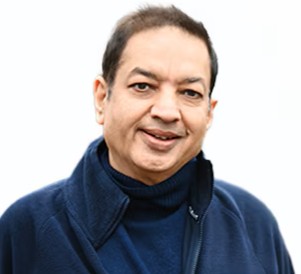
★ ★ ★ ★ ★