Why NPI Is Critical for Hardware Startup Success
A Startup's Guide to New Product Introduction: Manufacturing Success with PeakingTech - Discover why a robust NPI process is essential for hardware startup success. Learn how integrated manufacturing services in plastic molding, metal fabrication, and electronics can streamline your journey from prototype to production. This comprehensive guide explores cost benefits, common challenges, and proven strategies for efficient product launches, featuring real-world insights from PeakingTech's decade-plus experience in helping startups scale their hardware products.
1/17/20254 min read
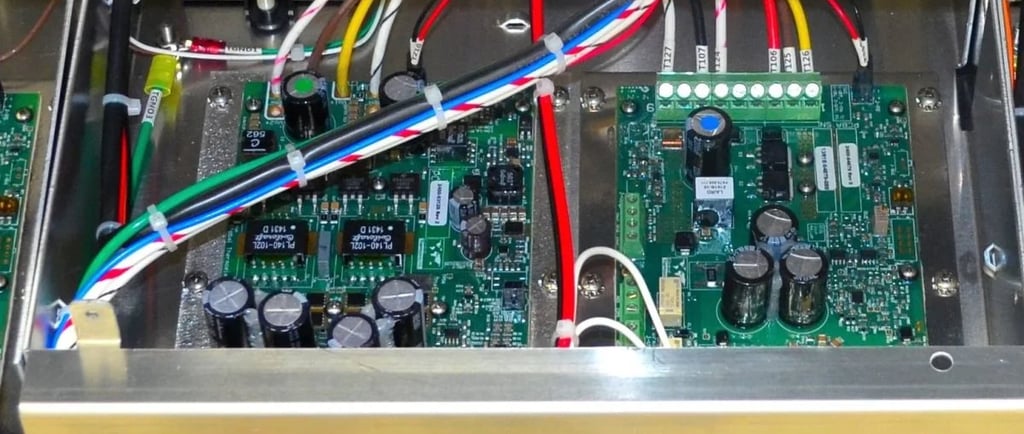
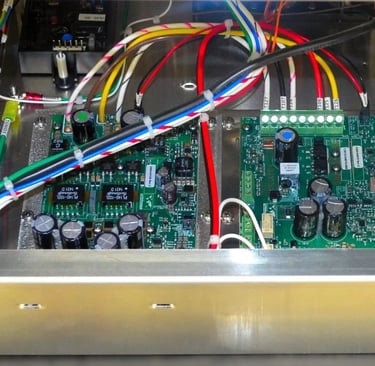
In today's fast-paced technology landscape, hardware startups face unique challenges in bringing their innovative ideas to market. New Product Introduction (NPI) stands as a crucial process that can make or break a startup's success. While many startups focus primarily on product design and market strategy, understanding and implementing a robust NPI process is equally vital for successful product launches and sustainable growth.
Understanding NPI and Its Significance
New Product Introduction is a comprehensive methodology that bridges the gap between product design and mass production. It encompasses everything from initial concept validation to manufacturing readiness, ensuring that products can be produced efficiently, consistently, and at the right cost point. For startups, particularly in the hardware sector, NPI isn't just a manufacturing process—it's a strategic advantage that can significantly impact time-to-market, product quality, and overall business success.
The Real Cost of Overlooking NPI
Many startups learn the hard way that skipping or rushing through proper NPI processes can lead to devastating consequences. The immediate drive to get products to market quickly often overshadows the importance of thorough NPI planning. However, this shortsightedness typically results in:
Extended development cycles due to unforeseen manufacturing challenges
Quality issues that damage brand reputation and customer trust
Unexpected cost overruns from manufacturing inefficiencies
Compliance issues that delay market entry
Supply chain disruptions and component shortages
Comprehensive NPI Services: A Strategic Partnership Approach
This is where experienced manufacturing partners like Peakingtech become invaluable. By offering integrated NPI services across plastic molding, metal fabrication, and electronics manufacturing, they provide startups with a one-stop solution for their manufacturing needs. Let's explore how these integrated services address critical aspects of the NPI process:
Design for Manufacturing (DFM)
PeakingTech's approach to DFM combines expertise across multiple manufacturing disciplines:
Plastic Molding: Early involvement in material selection, wall thickness optimization, and draft angle analysis ensures parts are designed for optimal manufacturability
Metal Fabrication: Assessment of fabrication methods, material choices, and finishing requirements to balance cost and quality
Electronics Manufacturing: Component selection, PCB layout optimization, and assembly process planning for reliable production
Product Validation Process
A robust validation process includes:
Engineering Verification Testing (EVT)
Prototype development using production-intent materials
Functional testing of mechanical and electronic components
Initial assembly process verification
Design Verification Testing (DVT)
Comprehensive testing under various environmental conditions
Integration testing of all subsystems
Regulatory compliance verification
Production Verification Testing (PVT)
Full-scale production run simulation
Quality control process validation
Yield optimization
Supply Chain Integration
PeakingTech's established supplier network offers several advantages:
Direct relationships with material suppliers and component manufacturers
Alternative sourcing strategies for critical components
Inventory management systems to prevent production delays
Quality assurance processes for all incoming materials
Timeline and Implementation
A well-executed NPI process typically follows this timeline:
Pre-Production Phase (4-6 weeks)
Design review and optimization
Material and component sourcing strategy
Manufacturing process planning
Engineering Verification (6-8 weeks)
Prototype development
Initial testing and refinement
Process documentation
Design Verification (8-10 weeks)
Production tool development
Quality control implementation
Regulatory testing
Production Verification (4-6 weeks)
Pilot production run
Process optimization
Final documentation
Cost Benefits of Professional NPI Services
Partnering with an experienced manufacturer like Peakingtech for NPI services offers significant cost advantages:
Reduced Development Costs
Early identification of design issues
Optimized material selection
Efficient tooling development
Manufacturing Efficiency
Streamlined production processes
Reduced scrap rates
Optimized assembly procedures
Long-term Savings
Scalable manufacturing solutions
Reduced warranty claims
Lower maintenance requirements
Common Challenges and Solutions
Startups often face several challenges during the NPI process:
1.Resource Constraints
Challenge: Most startups operate with limited engineering teams and manufacturing expertise.
Solution: Peakingtech offers comprehensive technical support through dedicated project managers and specialized engineers. Our team seamlessly integrates with your development process, providing:
DFM expertise across plastics, metals, and electronics
Tooling design and optimization
Process development and validation
Quality control implementation
2.Time-to-Market Pressure
Challenge: Aggressive launch schedules often clash with proper NPI procedures.
Solution: Our parallel development approach accelerates the timeline by:
Concurrent engineering for tooling and fixtures
Early supplier engagement for long-lead items
Rapid prototyping capabilities
Pre-production optimization during DVT phase
3.Budget Management
Challenge: Unexpected costs and revisions can quickly deplete development budgets.
Solution: Strategic cost control through:
Early identification of design optimization opportunities
Material and component cost analysis
Efficient tooling design to minimize modifications
Volume pricing strategies for production scaling
4.Supply Chain Complexity
Challenge: Managing multiple vendors and ensuring component availability.
Solution: PeakingTech's integrated manufacturing approach provides:
Single-source responsibility for plastic, metal, and electronic components
Established supplier network for critical components
Inventory management strategies
Alternative sourcing options for risk mitigation
5.Quality Control
Challenge: Maintaining consistent quality across different manufacturing processes.
Solution: Comprehensive quality management system including:
In-house testing capabilities
Statistical process control
Documented quality procedures
Real-time production monitoring
Best Practices for Successful NPI
Documentation
Detailed design specifications
Process control plans
Quality assurance procedures
Traceability systems
Communication
Regular project status updates
Clear escalation procedures
Cross-functional team coordination
Quality Control
In-process inspection protocols
Final product testing
Continuous improvement processes
Success Story
A recent collaboration between PeakingTech and a smart home device startup illustrates the benefits of comprehensive NPI services. The startup needed to manufacture a complex product involving plastic housing, metal components, and electronic assemblies. Through PeakingTech's integrated approach:
Design optimization reduced material costs by 15%
Manufacturing cycle time was reduced by 25%
First-pass yield exceeded 98%
Time-to-market was shortened by two months
Looking Forward: The Impact of Proper NPI
The importance of NPI for hardware startups cannot be overstated. In an increasingly competitive market, the ability to efficiently transition from design to production can determine a startup's success. Working with an experienced manufacturing partner like PeakingTech, who offers integrated services across plastic molding, metal fabrication, and electronics manufacturing, provides startups with:
Reduced technical risks
Faster time-to-market
Optimized production costs
Scalable manufacturing solutions
Enhanced product quality
Conclusion
For hardware startups, implementing a thorough NPI process through partnership with an experienced manufacturer like PeakingTech is not just about avoiding problems—it's about creating a foundation for sustainable growth. The investment in proper NPI processes, supported by comprehensive manufacturing capabilities in plastic molding, metal fabrication, and electronics manufacturing, pays dividends throughout the product lifecycle. As the hardware startup ecosystem continues to evolve, those who prioritize robust NPI processes will be better positioned for long-term success.