Why Customization is the Future of Electronic Enclosure Design
The demand for electronic enclosures that meet specific functional, aesthetic, and environmental requirements is growing rapidly. Businesses and consumers alike are no longer satisfied with one-size-fits-all solutions. Instead, they seek custom enclosures tailored to their unique needs.
2/8/20253 min read
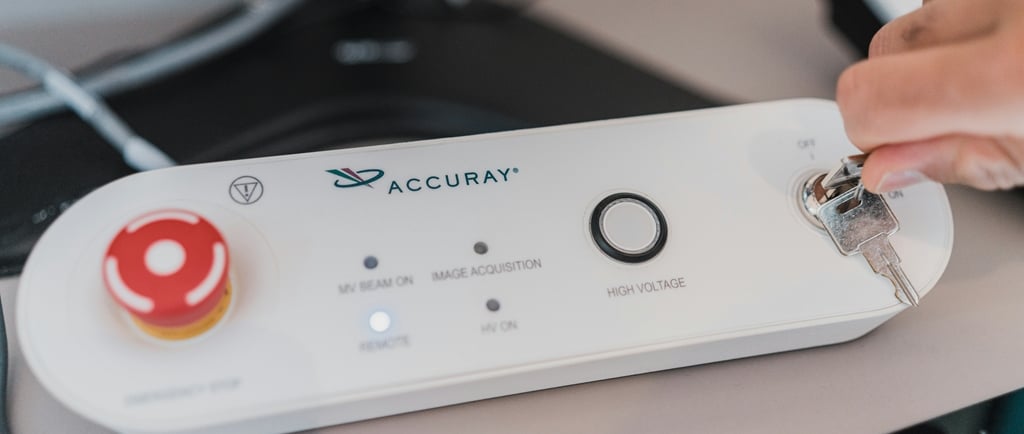
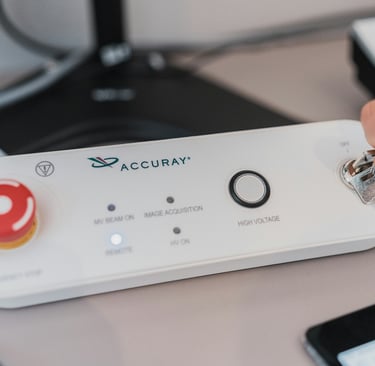
The demand for electronic enclosures that meet specific functional, aesthetic, and environmental requirements is growing rapidly. Businesses and consumers alike are no longer satisfied with one-size-fits-all solutions. Instead, they seek custom enclosures tailored to their unique needs. Advancements in technology and manufacturing have made customization more accessible and cost-effective than ever before.
This article explores why customization is becoming essential in electronic enclosure design and how it benefits various industries.
The Shift Toward Customization in Enclosure Design
Evolving User Expectations
Today’s users expect products that align perfectly with their requirements. From industrial equipment manufacturers to consumer electronics brands, businesses recognize the value of offering personalized solutions rather than generic enclosures.
Industry-Specific Requirements
Different industries demand unique enclosures:
Medical devices require enclosures that are ergonomic and easy to sterilize.
Industrial applications need rugged, durable enclosures that protect electronics from harsh environments.
Aerospace and defense sectors require lightweight yet durable enclosures that comply with stringent safety regulations.
Advances in Manufacturing Technologies
Innovations like CNC machining, 3D printing, and laser cutting make it easier to produce custom enclosures efficiently. These technologies lower the costs of small-batch production, making customization viable even for startups.
Benefits of Customizing Electronic Enclosures
Enhanced Functionality
Custom enclosures ensure that devices meet specific technical requirements:
Tailored cutouts for connectors, displays, or ventilation systems.
Integration of thermal management features like heat sinks or vents to prevent overheating.
Improved Aesthetics and Branding
Custom enclosures enhance product appeal:
Unique colors, logos, and finishes differentiate products in competitive markets.
Premium consumer electronics benefit from sleek anodized aluminum enclosures, while handheld tools may require branded plastic housings.
Better Environmental Protection
Customized designs allow businesses to achieve exact IP ratings, ensuring environmental protection:
Waterproof enclosures safeguard outdoor IoT devices.
UV-resistant materials prevent degradation in sun-exposed applications.
Optimized User Experience
User-centric design enhances device usability:
Contoured grips improve ergonomics for handheld medical scanners.
Easy-access panels simplify maintenance in industrial settings.
Future-Proofing Products
Custom enclosures support modular designs, allowing future upgrades:
Removable panels provide space for additional components or connectivity upgrades.
Industries Driving the Demand for Custom Enclosures
Medical Devices
Medical technology requires ergonomic, sterilizable enclosures:
Example: Handheld diagnostic tools with custom cutouts for screens and buttons.
Industrial Automation
Industrial environments demand rugged enclosures that protect against dust, moisture, and impact:
Example: Control boxes with waterproof seals and shock-resistant materials.
Consumer Electronics
Customization helps brands create aesthetically appealing products that integrate seamlessly into users’ lifestyles:
Example: Smart home devices with sleek finishes and custom mounting options.
Aerospace and Defense
Stringent safety and durability standards drive the need for specialized enclosures:
Example: Avionics housings featuring EMI shielding and modular layouts.
How Technology Enables Customization
Advanced Manufacturing Techniques
CNC Machining: Precision-cut metals or plastics to achieve complex shapes.
3D Printing: Rapid prototyping and small-batch production of intricate designs.
Laser Cutting: High-speed customization of materials with clean edges.
Digital Design Tools
CAD Software: Enables designers to create detailed 3D models for precise enclosure design.
Simulation Tools: Allow performance testing for thermal management, structural integrity, and EMI shielding before manufacturing.
Flexible Production Processes
Small-batch production lets companies test custom designs without large upfront costs.
Modular manufacturing approaches reduce lead times while ensuring high-quality output.
Challenges in Customizing Enclosures (and How to Overcome Them)
Balancing Cost and Complexity
Challenge: Customization can increase costs due to specialized tooling and material choices.
Solution: Partnering with experienced manufacturers helps optimize designs for cost-efficiency.
Ensuring Compliance with Standards
Challenge: Industry regulations (e.g., IP ratings, EMI shielding) must be met.
Solution: Collaborating with manufacturers familiar with regulatory requirements ensures compliance.
Managing Lead Times
Challenge: Custom designs may take longer to produce than off-the-shelf alternatives.
Solution: Using rapid prototyping technologies like 3D printing accelerates the design cycle.
The Future of Custom Electronic Enclosure Design
Personalization at Scale
Mass customization will make tailored enclosures affordable for businesses of all sizes.
Example: Online configuration tools enabling customers to select features before production.
Integration of Smart Features
Future enclosures will incorporate built-in sensors, displays, and connectivity features.
Example: IoT-ready enclosures with integrated antennas or wireless charging.
Sustainability in Customization
Eco-friendly materials such as recycled plastics and biodegradable composites will gain popularity.
Example: Solar-powered outdoor devices housed in sustainable enclosures.
Partnering with Manufacturers for Custom Solutions
Benefits of Working with Experts
Access to advanced tools and materials ensures high-quality customization.
Expertise in balancing aesthetics, functionality, and cost optimizes project outcomes.
Why Choose Peakingtech?
Proven track record in delivering custom enclosure solutions across industries.
State-of-the-art manufacturing capabilities for handling complex projects from concept to production.
Conclusion
Customization is the future of electronic enclosure design, offering enhanced functionality, improved aesthetics, environmental protection, optimized user experience, and future-proofing capabilities. With technological advancements making customization more accessible, businesses can now leverage tailored enclosures to differentiate their products and improve performance.
Call-to-Action (CTA)
Looking for expert guidance on custom enclosures? Contact Peakingtech today to explore tailored solutions for your industry. Browse our portfolio or request a consultation to bring your design ideas to life!
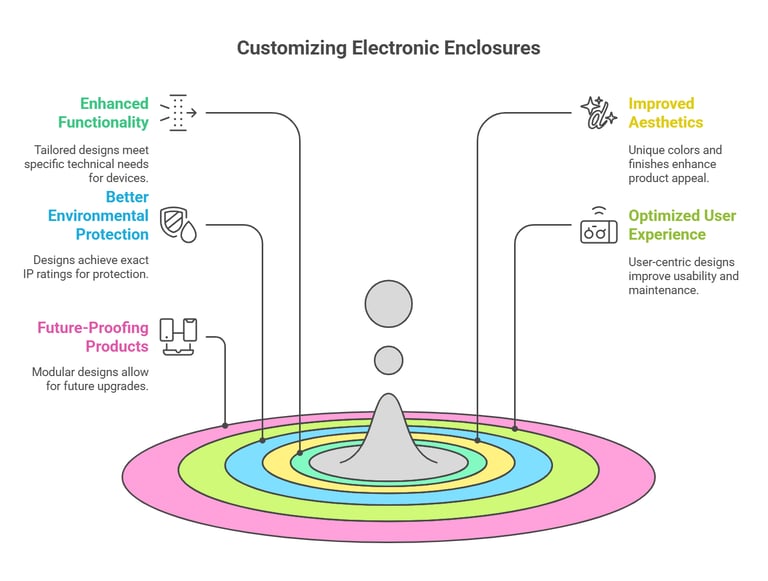
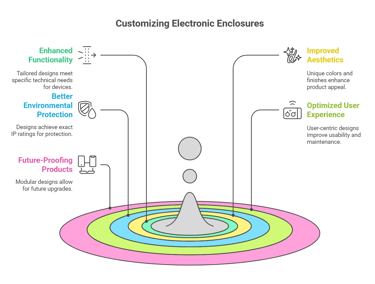