What is Injection Molding? A Beginner’s Guide to the Process
If you’re a designer sketching the next big thing in electronics or a decision-maker crunching numbers for production, injection molding is likely on your mind—or it should be.
2/21/20256 min read
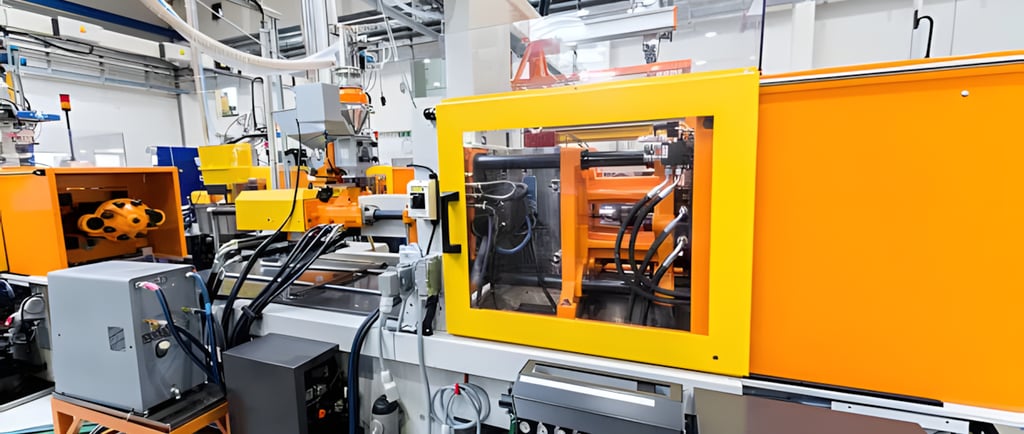
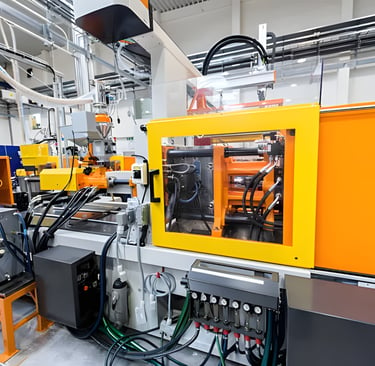
Imagine cracking open your latest gadget—say, a Logitech wireless mouse or the casing of a Nest thermostat. Ever stopped to think how those smooth, perfectly shaped plastic parts came to life? If you’re a designer sketching the next big thing in electronics or a decision-maker crunching numbers for production, injection molding is likely on your mind—or it should be.
Here’s the deal: injection molding is the backbone of modern electronics manufacturing. It’s how companies churn out millions of durable, precise plastic components, from tiny circuit spacers to sleek device housings, with jaw-dropping efficiency. I’ve seen it in action—rows of machines humming away, spitting out parts faster than you can blink. This beginner’s guide is your crash course in how it works, why it’s a lifesaver for electronics, and what it can do for your projects. Ready to get the scoop? Let’s jump in!
What is Injection Molding?
Injection molding is essentially high-tech sculpting. Picture this: molten plastic gets shot into a custom metal mold under pressure, cools into shape, and pops out as a finished part. It’s the process behind everything from the buttons on your TV remote to the casing of a medical wearable. For electronics pros, it’s a goldmine—think precision molding that nails tolerances down to 0.005 inches (about 0.13 mm), per industry standards from the Society of Plastics Engineers.
The setup? An injection machine—some as big as a car—melts plastic pellets, pushes them into a mold cavity, and repeats the cycle thousands of times. Why’s it a big deal? It’s fast (cycles as short as 10 seconds), versatile, and built for mass production. Companies like Apple and Samsung rely on it to crank out phone parts by the millions. For you, it’s the key to turning a sketch into a shelf-ready product without losing sleep over quality.
How Does Injection Molding Work? A Step-by-Step Breakdown
Let’s walk through the process like we’re touring a factory floor. I’ll break it down with examples from electronics to show you why this matters for your designs and decisions.
Step 1: Mold Design—Your Blueprint Comes to Life
It all starts with the mold—a steel or aluminum masterpiece that dictates your part’s shape. For electronics, this is make-or-break. Take the Fitbit Versa’s casing: its mold had to account for curves that hug the wrist, slots for sensors, and a flawless finish. A single mold can cost $5,000 to $50,000, depending on complexity (data from Protolabs), but it’s a one-time hit for thousands of parts.
Designers, you’ll tweak this with CAD software—maybe adding a 2-degree draft angle to ensure ejection, a tip I picked up from a mentor years ago. Decision-makers, this is your tooling cost line item—pricey upfront, but it amortizes over a run of 10,000 units to pennies per part.
Step 2: Material Selection—Choosing Your Plastic Soulmate
Next, you pick your plastic. Thermoplastics rule here—ABS for toughness (used in Logitech mice), polycarbonate for clarity (think GoPro housings), or nylon for flexibility (common in cable ties). Fact: over 32 million tons of thermoplastics were molded globally in 2022, per Plastics Insight, and electronics gobbled up a huge chunk.
I once worked with a team on a Bluetooth speaker—ABS gave it a matte finish users loved, while staying under $1 per pound. Designers, your choice shapes the feel and function; decision-makers, it’s a cost-performance dance—polycarbonate might cost $2 per pound but resists shattering in a drop test.
Step 3: Melting and Injection—The Heat Is On
Here’s the fun part: the injection machine melts those pellets at 400–500°F (204–260°C) and blasts them into the mold at pressures up to 20,000 psi. For a USB-C port cover, this step nails tiny details like pin slots in seconds. A real case? Dyson’s Airwrap uses injection molding to craft its intricate attachments—each one a testament to injection pressure precision.
I’ve stood by these machines, mesmerized as they whir and hiss. Designers, your tolerances better be spot-on—0.1 mm off, and that port won’t fit. Decision-makers, this speed (up to 100 parts per hour on a mid-size mold) is your production lifeline.
Step 4: Cooling and Solidification—Where Patience Pays
Once injected, the plastic cools in the mold—think 20–60 seconds, depending on thickness. Mold cooling is an art; channels in the mold circulate water to speed it up. For a thin-walled phone case, Apple’s suppliers might hit a 15-second cycle time, churning out 240 units hourly per machine (industry benchmarks). Rush it, though, and you get warping—ask me about the warped prototype I once tossed!
In electronics, thin parts are king, so this step ensures durability—like the crack-free shell of a Roku remote. Decision-makers, balancing speed and quality here is your ROI sweet spot.
Step 5: Ejection and Finishing—The Big Reveal
The mold splits, pins push out the part, and voilà—your creation’s born. Sometimes there’s flash (extra plastic) to trim, like on a cheap plastic toy, but for electronics, it’s minimal—think Samsung Galaxy buds, polished to perfection. Post-processing might mean painting or laser-etching a logo.
I’ve held a freshly molded circuit bracket—still warm—and marveled at its detail. Designers, this is your proof of concept; decision-makers, it’s where part consistency (99.9% identical, per SPI stats) seals the deal. (Want a diagram of this flow? Hit me up—I’d love to sketch it!)
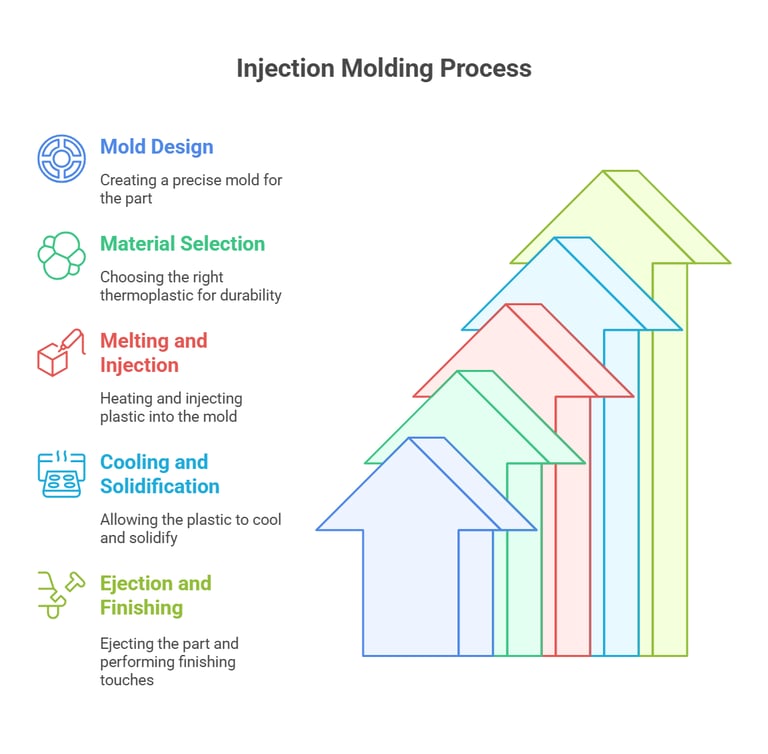
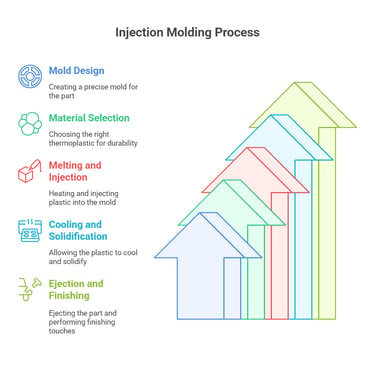
Common Applications in Electronics Development
Injection molding’s fingerprints are all over electronics. Here’s proof:
Consumer Tech: The iPhone’s backplate—once plastic—came from this process, as do Kindle shells. Foxconn, Apple’s partner, molds millions yearly.
Internal Bits: Circuit spacers in a Dell laptop or battery clips in a Tesla Powerwall—small, precise, and molded.
Industrial Wins: Server casings for IBM’s data centers, built to last with industrial molding.
A buddy of mine designed a smart lock—its molded housing survived 10,000 lock cycles in testing. For you, this means reliable parts that scale from prototype to production.
Advantages of Injection Molding for Electronics
Why bet on this process? Here’s the payoff:
Precision and Consistency: Tolerances tighter than 0.005 inches mean your PCB mounts fit every time—crucial for a Raspberry Pi enclosure.
Scalability: From 100 prototypes to 1 million units, it’s seamless. Xiaomi molds 60 million phone parts annually this way.
Cost Efficiency: A $10,000 mold for a speaker grille drops to $0.10 per part over 100,000 units (Protolabs data). Compare that to $1 per 3D-printed piece!
Material Options: Pick ABS for a $50 controller or polycarbonate for a $500 drone—your call.
Designers, this is your playground—dream up intricate shapes without compromise. Decision-makers, it’s budget-friendly scale—my old boss once slashed costs 30% switching to molding mid-project.
Challenges and Considerations
It’s not flawless, though. Here’s the real talk:
Upfront Costs: A complex mold for a VR headset might hit $20,000. But over 50,000 units? Just $0.40 each. Math checks out.
Design Limits: Sharp corners caused sink marks on a prototype I once oversaw—fixed with a redesign. Design optimization is non-negotiable.
Learning Curve: First-timers might stumble. A client of mine lost $5,000 on a bad mold before nailing it with expert help.
The fix? Partner with pros and test early—I’ve seen it turn flops into wins every time.
Why Injection Molding Matters in Electronics Today
Injection molding isn’t static—it’s evolving. In 2025, automation molding cuts labor costs 20% (McKinsey stats), while sustainable manufacturing uses recycled plastics—Canon’s molded printer parts are 70% recycled now. Designers, this means faster prototypes; my team once molded a smartwatch band in two weeks flat. Decision-makers, it’s your edge—launch a hit product before competitors blink.
Take Logitech: its G502 mouse, a molded marvel, hit shelves with precision and speed that 3D printing couldn’t match. That’s your power here—turning ideas into reality, profitably.
Wrapping It Up
So, what’s injection molding? It’s the wizardry that transforms plastic into the electronics we love—from mold design to ejection, a five-step masterpiece. For designers, it’s precision at your fingertips; for decision-makers, it’s scale without sacrifice. Whether you’re crafting a new earbud or greenlighting a factory run, this process delivers.
Digging this? Check our posts on molding materials or cost breakdowns next. Got a question? I’m here—shoot me a note. And hey—what’s one molded gadget you use daily? Bet it’s closer than you think!