What Is Electronics Manufacturing? A Deep Dive into the Process Powering Your Devices
At its core, electronics manufacturing is the art and science of designing, building, testing, and producing the electronic components and devices we rely on. For those of you steering the ship—whether you’re sketching circuit boards or calling the shots on production lines—this process is your playground.
2/27/20255 min read
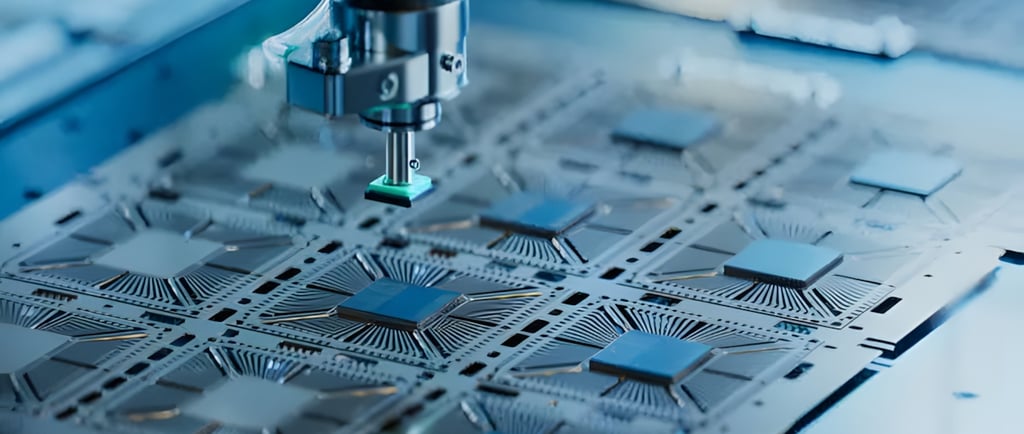
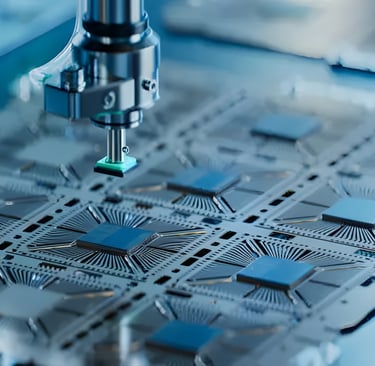
Imagine this: you’re holding your smartphone, scrolling through this article, maybe sipping coffee. That sleek little gadget in your hand? It didn’t just appear out of thin air. It’s the result of a fascinating, intricate journey called electronics manufacturing. From the tiny chip buzzing inside to the screen lighting up your words, every piece has a story—one that designers and decision-makers like you shape every day.
So, what is electronics manufacturing? At its core, it’s the art and science of designing, building, testing, and producing the electronic components and devices we rely on. For those of you steering the ship—whether you’re sketching circuit boards or calling the shots on production lines—this process is your playground. Let’s peel back the curtain and explore what makes it tick, why it matters, and how it’s evolving. Ready? Let’s dive in.
The Basics of Electronics Manufacturing
Picture a bustling workshop where ideas turn into reality. That’s electronics manufacturing in a nutshell. It’s the backbone of every gadget, from the laptop I’m typing on to the MRI machine saving lives in a hospital. At its simplest, it’s about taking raw materials—think silicon, copper, and a dash of ingenuity—and transforming them into finished products.
For designers, this is where your blueprints come to life. For decision-makers, it’s where budgets, timelines, and quality standards collide. The endgame? Devices like smartphones, wearables, or even the control systems in your car. Without this process, our tech-driven world would grind to a halt. It’s not just nuts and bolts—it’s the pulse of innovation, and you’re the ones keeping it beating.
Key Stages in Electronics Manufacturing
Let’s break it down. Electronics manufacturing isn’t a single step; it’s a relay race with distinct legs. Here’s how it unfolds—and where your expertise comes into play.
Design and Prototyping
It all starts with a spark. You, the designer, sit down with tools like CAD software, sketching out circuits and dreaming up the next big thing. Maybe it’s a slimmer smartwatch or a more efficient power supply. This is the phase where creativity meets precision. You tweak, test, and prototype—sometimes failing spectacularly (we’ve all been there)—until it’s just right. For decision-makers, this is where you greenlight the vision, balancing innovation with feasibility. Ever had that “aha” moment when a prototype finally works? That’s the magic of this stage.
Component Production
Once the design’s locked in, it’s time to make the pieces. Think of this as the kitchen of electronics—where raw ingredients like semiconductors and resistors get cooked up. Factories churn out printed circuit boards (PCBs), microchips, and capacitors with tolerances tighter than a drum. As a designer, you’re ensuring every spec aligns with your vision. As a decider, you’re watching costs and sourcing—because a single delay in chip supply can derail everything. It’s gritty, detailed work, but it’s the foundation of every device.
Assembly
Here’s where the puzzle comes together. Components hit the production line, and suddenly, your design is taking shape. Surface-mount technology (SMT) robots place parts with pinpoint accuracy, while soldering locks them in place. I’ve watched these lines in action—there’s something mesmerizing about the rhythm, like a dance of machines and human oversight. Designers, you’re double-checking tolerances here. Decision-makers, you’re ensuring the line hums without hiccups. It’s chaos turned into order, and it’s beautiful.
Testing and Quality Control
No one wants a phone that fries on day two. That’s why testing is the unsung hero of this process. Stress tests, burn-ins, and defect scans make sure every unit meets the mark. I once talked to an engineer who swore by the “drop test”—literally tossing prototypes to see what broke. Designers, this is your reality check. Decision-makers, it’s your safety net—because a recall is every exec’s nightmare. Quality isn’t optional; it’s the line between success and scrap.
Packaging and Distribution
The finish line! Devices get boxed up, branded, and shipped out to stores or straight to doorsteps. It sounds simple, but designers tweak packaging for durability, while decision-makers optimize logistics to hit deadlines. Ever unboxed a gadget and felt that thrill? That’s the payoff of this stage—and your work made it happen.
Technologies and Tools Used
Now, let’s talk tools. Electronics manufacturing isn’t some dusty assembly line from the ‘50s—it’s a high-tech symphony. Automation rules the day, with robots placing components faster than any human could. I’ve seen these machines up close; they’re like something out of a sci-fi flick, whirring away with uncanny precision. For designers, software like Altium or Eagle turns your ideas into actionable plans. Decision-makers lean on ERP systems to keep the chaos in check.
Then there’s the cutting edge: 3D printing for rapid prototypes, AI predicting production snags, and miniaturization shrinking devices without losing power. Ever marvel at how your smartwatch packs so much punch? That’s the tech at work—and you’re the ones pushing it forward.
The Global Impact of Electronics Manufacturing
Zoom out for a second. This isn’t just a factory floor—it’s a global engine. Economically, it’s massive, creating millions of jobs and driving trade. Designers, your work fuels innovation hubs from Silicon Valley to Shenzhen. Decision-makers, you’re navigating a supply chain that spans continents, juggling raw materials like rare earths and finished goods like OLED screens.
But it’s not all rosy. E-waste piles up—those old phones don’t just vanish. Labor conditions in some regions spark debates, and supply chain hiccups (remember the chip shortage?) keep execs up at night. I’ve talked to folks in the industry who wrestle with these issues daily. It’s a balancing act—profit, planet, and people—and your decisions tip the scales.
Why It Matters to You
Let’s bring it home. As a designer, electronics manufacturing is your canvas—every line you draw shapes the future. For decision-makers, it’s your chessboard—strategy here determines wins or losses. You’re not just building gadgets; you’re crafting the tools we live by. That fitness tracker nudging you to walk? The telemedicine device checking a patient’s heart? That’s your legacy.
Looking ahead, the stakes are only getting higher. Wearable tech, smart homes, autonomous cars—they’re all on the horizon, and you’re the ones steering us there. I’ve got a friend who’s obsessed with his smart thermostat; he doesn’t know it, but he’s cheering for your work. So next time you’re tweaking a design or crunching numbers, remember: you’re not just making stuff—you’re making the world tick.
Conclusion
So, what is electronics manufacturing? It’s a blend of grit, genius, and gears—a process that turns dreams into devices. For designers and decision-makers, it’s your proving ground, where every choice echoes from the drafting table to the end user’s hands. I’ve always been amazed by how much goes into the tech we take for granted—how a late-night sketch becomes a lifesaving tool or a morning ritual.
Next time you pick up your phone or tweak a prototype, take a second to appreciate the journey. You’re not just part of it—you’re driving it. What’s your favorite gadget? Drop it in the comments—I’d love to hear what keeps you inspired.