Unveiling the Costs of Electronics Manufacturing: A Deep Dive for Designers and Decision-Makers
We’re peeling back the layers of electronics manufacturing costs with hard numbers, real-world examples, and lessons from the trenches.
3/7/20255 min read
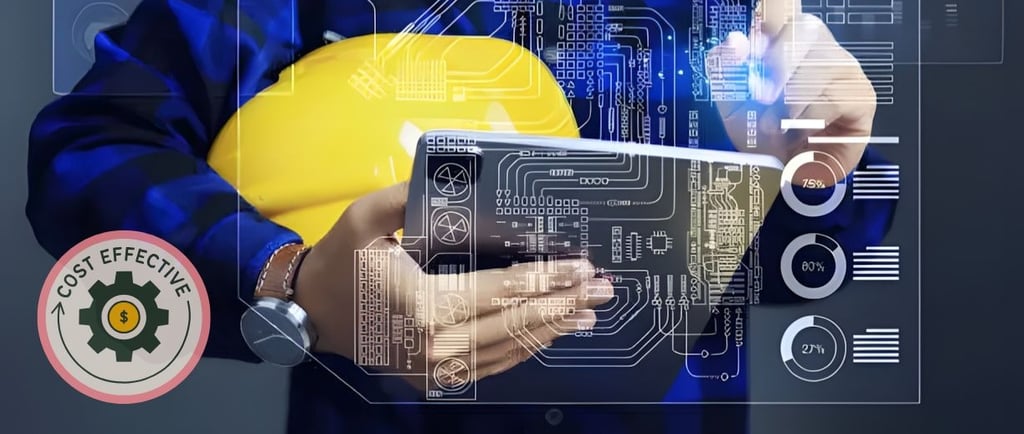
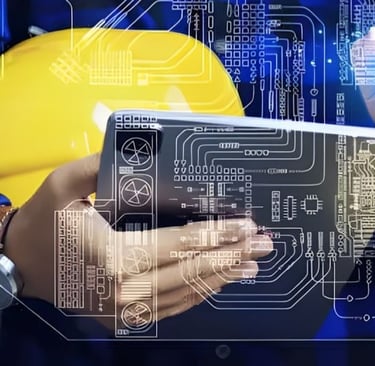
Imagine you’re a designer sketching the blueprint for a sleek fitness tracker, or perhaps a decision-maker weighing the budget for a smart thermostat that could dominate the market. The buzz of innovation fills the air—until the inevitable question hits: “How much will this cost to make?” Suddenly, the excitement shifts to scrutiny. In electronics manufacturing, costs aren’t just line items; they’re the difference between a prototype that gathers dust and a product that changes lives.
In this detailed guide, we’re dissecting the costs of electronics manufacturing with real-world examples, hard numbers, and lessons from the trenches. From sourcing chips to scaling production, we’ll equip you—designers and decision-makers—with the insights to navigate this complex landscape. By March 2025, the industry’s still reeling from supply chain scars and tech booms, making this knowledge more critical than ever. Let’s dig in.
1. The Foundation: Raw Materials and Component Costs
Every gadget begins with its guts—think microchips, resistors, capacitors, and the trusty printed circuit board (PCB). But these essentials come with a volatile price tag. Take semiconductors: the 2021-2022 chip shortage pushed costs up by 20-40%, according to Deloitte. Even now, a mid-range microcontroller like the STM32 series might range from $5 to $15, while a high-end NVIDIA Jetson Nano for AI applications can hit $50 per unit. For a 10,000-unit run, that’s $50,000 to $500,000 just on chips.
PCBs tell a similar story. A basic single-layer board for a simple LED device might cost $2-$5 each in small batches, per PCBShopper data. But a multi-layer board for a 5G router? You’re looking at $50-$100 per unit for prototypes, dropping to $20 with volume. Add in connectors ($1-$5 each), OLED displays ($10-$30), and lithium-ion batteries ($5-$20), and your bill climbs fast. In 2023, Apple reportedly spent $150 per iPhone 14 on components alone, per Counterpoint Research—a benchmark for premium devices.
Case Study: Fitbit’s Versa line leaned on off-the-shelf components to keep costs down, avoiding custom chips that could’ve doubled their material spend. Designer Tip: Spec widely available parts—think Texas Instruments over boutique brands. Decision-Maker Move: Negotiate bulk deals with suppliers like DigiKey or Mouser to hedge against price swings.
2. Prototyping: Where Dreams Meet Dollars
Prototyping is your sandbox—soldering, testing, tweaking—but it’s not cheap. A single PCB run from a service like JLCPCB might cost $100 for five boards, jumping to $500 with expedited shipping. Assembly’s another beast: hand-soldering a complex prototype with 50 components could take a technician 5 hours at $30/hour—$150 right there. Outsource it to a firm like Seeed Studio, and you’re at $300-$1,000 per unit, per industry quotes.
Revisions amplify the pain. Take the Raspberry Pi Pico: its initial design reportedly went through three iterations before launch in 2021, costing thousands in rework, per Hackaday estimates. For a startup making a smart lock, I’ve seen prototyping budgets hit $10,000 after four rounds of fixes—new sensors, better antennas, you name it.
Real Example: The Pebble smartwatch team famously burned through $50,000 in prototyping before their 2012 Kickstarter, iterating on display and battery issues. Designer Hack: Use simulation tools like Altium to catch flaws early. Decision-Maker Call: Approve a $5,000-$10,000 prototyping fund upfront—penny-pinching here delays launches.
3. Labor Costs: People Power in a Tech World
Even with automation, humans assemble, inspect, and troubleshoot your electronics. Labor rates vary wildly by region. In Silicon Valley, a technician earns $25-$40/hour, per Glassdoor 2025 data. In Shenzhen, China—a manufacturing hub—it’s $3-$8/hour, per Statista. For a device needing 30 minutes of assembly per unit, that’s $12.50-$20 in the U.S. versus $1.50-$4 overseas for 1,000 units.
Design choices matter here. Tesla’s Model 3 battery packs, with their intricate wiring, reportedly require 20% more labor time than simpler packs, per Bloomberg—a cost passed to production. Contrast that with IKEA’s flat-pack philosophy applied to electronics: modular designs cut assembly time by 15-30%, per industry studies.
Case Study: Dyson’s Singapore plant shaved millions off labor costs for its cordless vacuums by automating 70% of assembly, but smaller firms without that capital lean on human hands. Designer Tip: Minimize hand-soldered parts. Decision-Maker Strategy: Weigh onshore quality control against offshore savings—delays from miscommunication can erase the gap.
4. Equipment and Tooling: Precision’s Price Tag
Mass production demands heavy gear—SMT machines, reflow ovens, wave solderers. A contract manufacturer (CM) like Foxconn bundles this into their fees, but custom tooling isn’t free. A stencil for PCB assembly might cost $500, while an injection mold for a plastic enclosure runs $5,000-$25,000, per Protolabs pricing. For Samsung’s Galaxy line, tooling investments reportedly top $100 million per model, per Reuters.
Smaller runs can lean on 3D printing—$200-$500 for a batch of enclosures—but scaling to 10,000 units demands molds. Take the Nest Thermostat: its sleek shell required a $15,000 mold, amortized over millions of units, per Forbes estimates.
Real-World Lesson: A drone startup I advised budgeted $10,000 for tooling but faced a $40,000 bill after underestimating mold complexity. Designer Move: Embrace design-for-manufacturability (DFM) principles—fewer parts, simpler assembly. Decision-Maker Play: Match tooling spend to volume; 1,000 units might not justify a $20,000 mold.
5. Testing and Quality Assurance: The Safety Net
Testing ensures your product doesn’t flop—or explode. Basic functional tests might cost $1,000-$3,000 in-house, using oscilloscopes and multimeters. Third-party certifications—like UL for safety or FCC for emissions—add $5,000-$15,000, per Intertek rates. Tesla spent millions certifying its Cybertruck, but even a small IoT device faces $10,000 in compliance costs.
QA during production varies. Inspecting 1% of a 10,000-unit run at $1/unit adds $100; full inspection jumps to $10,000. GoPro’s early cameras faced recalls in 2015 due to battery flaws, costing millions—proof that skimping on QA backfires.
Example: Sonos tests every speaker for audio fidelity, adding $2-$3 per unit but ensuring brand trust. Designer Tip: Build in diagnostics—like LED indicators—to speed testing. Decision-Maker Move: Budget 5-10% of production costs for QA and compliance—fines dwarf this.
6. Scaling Up: Volume’s Double-Edged Sword
Economies of scale kick in with volume. A 100-unit run of a Bluetooth speaker might cost $50 each; 10,000 units drop to $20, per McKinsey manufacturing benchmarks. But scaling requires cash—$50,000 in components for that jump, plus warehouse space at $1-$2 per square foot monthly.
Fitbit scaled its Charge line from 100,000 to 1 million units annually by 2016, cutting per-unit costs by 25%, per Forbes. But a misstep—like over-ordering chips—can sink you. In 2022, a VR startup I consulted overstocked $100,000 in GPUs, only to see demand tank.
LSI Boost: “Electronics production scaling costs” fits here. Designer Tip: Design modularly for easy upgrades. Decision-Maker Call: Forecast demand conservatively—break-even at 5,000 units beats a warehouse of unsold stock.
7. Logistics and Distribution: The Final Mile
Shipping a 1-pound gadget costs $2-$5 domestically via UPS, $10-$20 internationally, per 2025 rates. Packaging—foam inserts, boxes—adds $0.50-$2 per unit. Tariffs? Importing PCBs from China faces a 2-5% duty, per U.S. Customs data. For a $1 million shipment, that’s $20,000-$50,000.
Case Study: Oculus Rift’s 2016 launch stumbled when shipping delays left backers fuming—extra air freight cost millions. Lesson: A friend’s startup lost $15,000 to damaged goods from skimpy packaging. Tip: Invest in logistics planning—$1 upfront saves $10 later.
8. Hidden Costs: The Curveballs
Supply chain hiccups, like the 2024 Taiwan port strike, can delay parts by weeks, forcing $10,000 in expedited shipping. A component’s end-of-life—like Intel’s Atom chips in 2023—might demand a $20,000 redesign. New EU regs in 2025 added $5,000 in compliance costs for a client’s smart bulb.
Advice: Pad your budget by 15-20%. Designers, stay adaptable; decision-makers, track industry news.
Conclusion: Turning Costs into Wins
The costs of electronics manufacturing—materials ($5-$150/unit), prototyping ($1,000-$10,000), labor ($1-$20/unit), and beyond—are a maze. But with examples like Fitbit’s thrift and Tesla’s scale, you’ve got a roadmap. Designers, optimize early; decision-makers, fund smartly. Your next big idea’s price tag is steep—but master it, and the payoff’s priceless. Share your cost challenges below—I’m all ears.
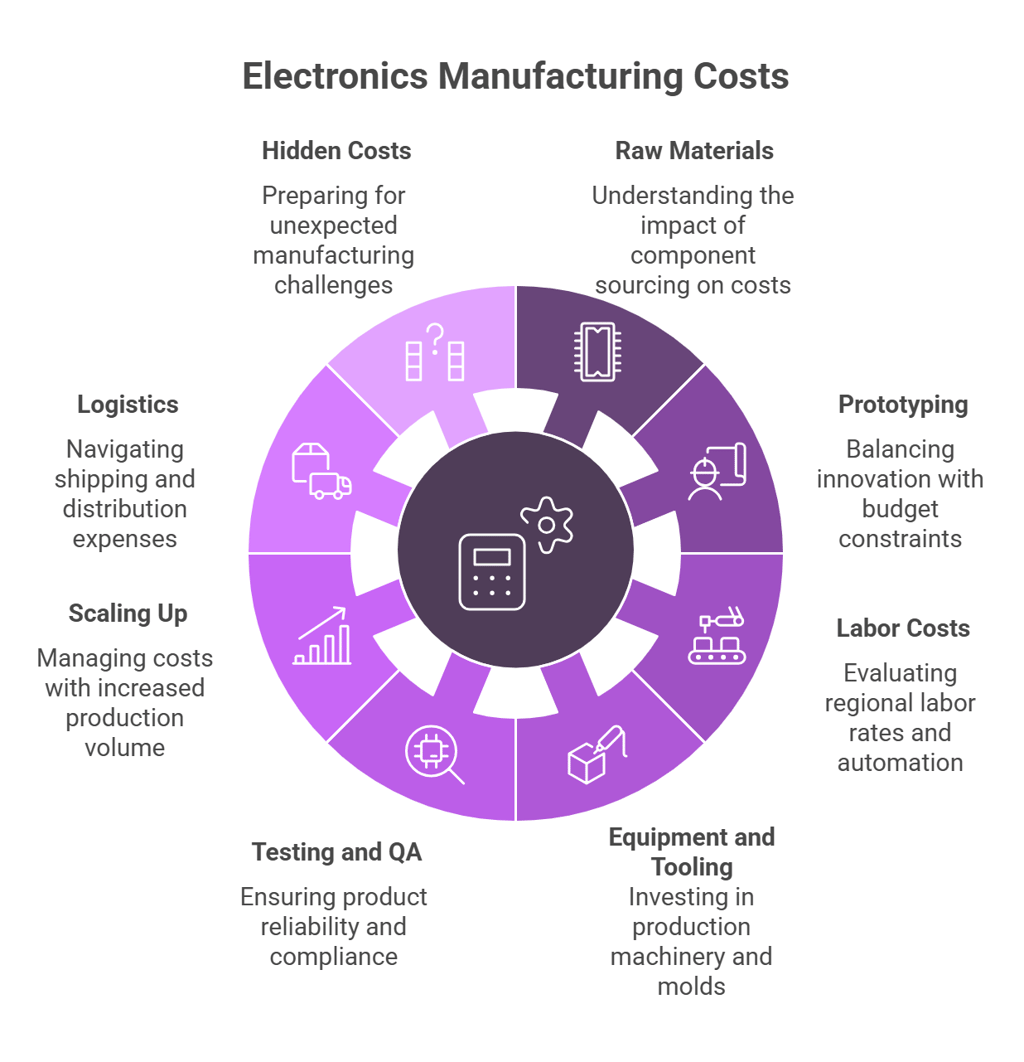
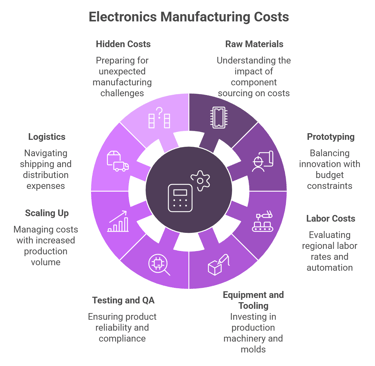