Unlocking Innovation with Flexible Printed Circuit Board Prototyping Services: A Guide for Electronics Designers and Decision-Makers
Are you an electronics designer tasked with creating a sleek, lightweight wearable device—or perhaps you’re a decision-maker overseeing a groundbreaking project in automotive electronics.
4/6/20255 min read
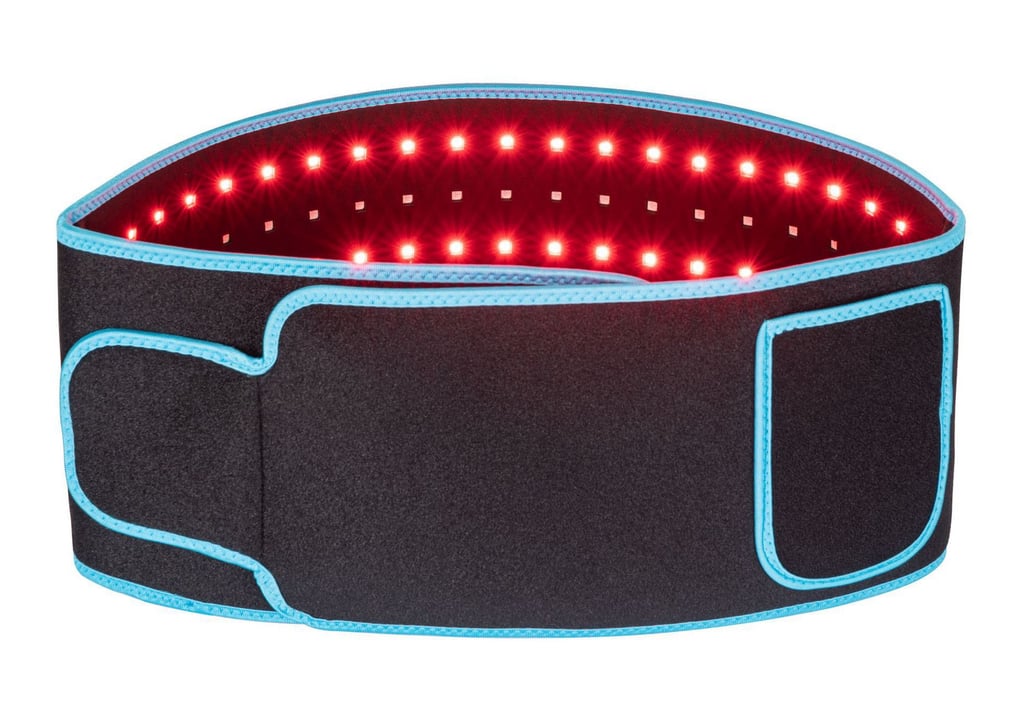
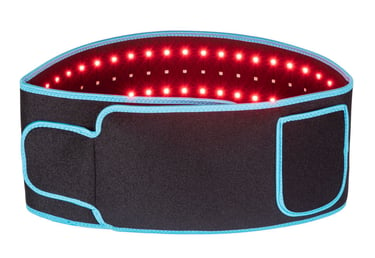
I. Introduction
Imagine you’re an electronics designer tasked with creating a sleek, lightweight wearable device—or perhaps you’re a decision-maker overseeing a groundbreaking project in automotive electronics. In either case, you’ve likely encountered the magic of flexible printed circuit boards (FPCBs). These bendable, adaptable circuits are revolutionizing how we design and build electronics. But before you can bring your vision to life, there’s a critical step: prototyping. That’s where flexible printed circuit board prototyping services come in, offering a bridge between your ideas and a market-ready product.
Prototyping isn’t just a checkbox—it’s the heartbeat of innovation in electronics development. It’s where concepts are tested, flaws are ironed out, and brilliance takes shape. In this article, we’ll dive deep into the world of FPCB prototyping services, exploring why they matter, how they work, and how they can empower designers and decision-makers like you to push the boundaries of what’s possible.
II. Understanding Flexible Printed Circuit Boards
Let’s start with the basics. A flexible printed circuit board is exactly what it sounds like: a circuit board that bends, twists, and conforms to unique shapes without breaking. Unlike their rigid counterparts, FPCBs are made from flexible substrates like polyimide or polyester, layered with conductive traces. This flexibility makes them lightweight, durable, and perfect for tight spaces.
So, why choose FPCBs over traditional rigid PCBs? For one, they save space and weight—crucial for wearables, medical devices, and aerospace applications. They also handle dynamic flexing (think foldable smartphones) and offer better heat dissipation. From consumer gadgets to industrial sensors, FPCBs are everywhere—powering LED strips, automotive dashboards, and even satellite systems.
As a designer, you might already be dreaming up ways to use FPCBs. As a decision-maker, you’re likely weighing their cost-effectiveness and scalability. Prototyping is where these dreams and decisions meet reality.
III. The Prototyping Process for FPCBs
Prototyping an FPCB isn’t like slapping together a quick mockup—it’s a deliberate, multi-step journey. It starts with design, where you map out the circuit layout, considering factors like bend radius, layer stacking, and component placement. Unlike rigid boards, FPCBs demand extra attention to flexibility and stress points. One wrong move, and your circuit could crack under pressure—literally.
Next comes material selection. Polyimide is a go-to for its heat resistance, but thinner substrates might suit low-profile designs. Then, the fabrication phase kicks in: etching traces, laminating layers, and adding stiffeners where needed. Finally, assembly and testing ensure your prototype works as intended, whether it’s powering an LED strip or a medical sensor.
This process can feel daunting, especially if your team lacks the tools or expertise. That’s why partnering with a prototyping service can be a game-changer.
IV. Benefits of Using a Flexible Printed Circuit Board Prototyping Service
Picture this: You’re racing against a deadline to get your FPCB design into production. Your in-house team is stretched thin, and your equipment can’t handle the precision required. Enter a flexible printed circuit board prototyping service. Here’s why it’s a lifeline for designers and decision-makers:
Specialized Expertise and Equipment: Prototyping services bring years of experience and cutting-edge tools to the table. They’ve seen it all—complex multilayer FPCBs, ultra-thin circuits, you name it. This means fewer headaches for you and a smoother path to success.
Speedy Turnaround: Time is money, right? These services streamline the process, delivering prototypes faster than most in-house setups. Need a quick iteration? They’ve got you covered.
Cost Savings: Setting up an FPCB prototyping line in-house is expensive—think specialized machinery, materials, and training. Outsourcing lets you skip the upfront investment and focus on what matters: your design.
Test and Refine: A good prototype isn’t just a proof of concept—it’s a chance to tweak and perfect. Prototyping services often include testing, so you can catch issues before mass production.
Take Peakingtech, for example. With experience crafting FPC boards up to 1220mm in length, they’re a standout in the field. Plus, they’ve cracked the code on continuous FPC production—think 100-meter rolls for LED strips. That’s the kind of innovation that can transform your project.
V. Choosing the Right FPCB Prototyping Service
Not all prototyping services are created equal, so how do you pick the right one? As a designer, you need a partner who gets your vision. As a decision-maker, you want reliability and ROI. Here’s what to look for:
Experience and Technical Capabilities: Can they handle your project’s complexity? A provider like Peakingtech, with its track record on long FPCBs (up to 1220mm), proves they’ve got the chops.
Service Range: Look for end-to-end solutions—design support, fabrication, assembly, and testing. The more they offer, the less you juggle.
Quality Control: Ask about their testing protocols. Do they check for bend durability, signal integrity, and thermal performance? Quality matters.
Turnaround and Support: Tight deadlines call for fast delivery and responsive communication. A good provider keeps you in the loop.
Collaboration is key. Share your specs, ask questions, and build a relationship. The best services act like an extension of your team, not just a vendor.
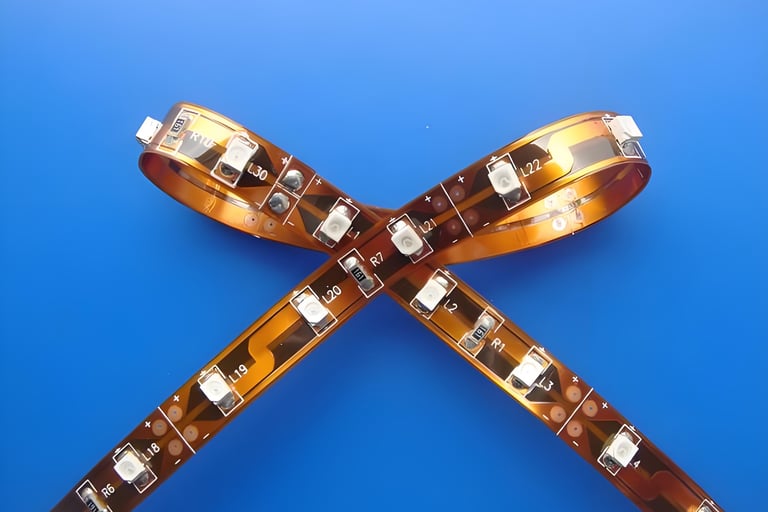
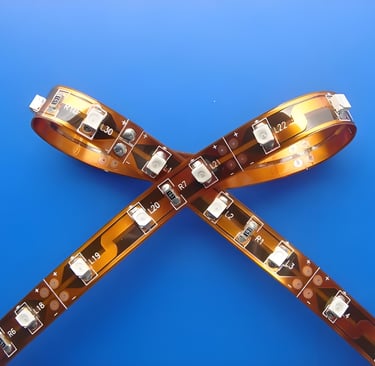
VI. Case Studies: Successful FPCB Prototyping Projects
Let’s ground this in real-world examples—stories that might spark your next big idea.
Case Study 1: Wearable Fitness Tracker
A startup wanted a compact FPCB for a wrist-worn fitness tracker. Their prototyping service helped refine a multilayer design, shaving weeks off development. The result? A sleek, flexible circuit that fit perfectly and hit the market ahead of schedule.
Case Study 2: LED Strip Lighting
A lighting company needed a continuous FPCB for a 100-meter LED strip. Peakingtech stepped in with their continuous FPC production solution, including equipment modification and supplier sourcing, delivering a seamless, cost-effective prototype. The client scaled up production and lit up the competition.
What’s the takeaway? Whether you’re designing a tiny wearable or a massive lighting array, the right prototyping partner can make or break your project.
VII. Future Trends in FPCB Prototyping
The FPCB world isn’t standing still, and neither should you. Here’s what’s on the horizon:
Emerging Tech and Materials: Think stretchable circuits and eco-friendly substrates. These innovations could open doors to new applications, from smart textiles to biodegradable electronics.
Industry 4.0 Impact: Automation and AI are speeding up prototyping. Imagine real-time design adjustments or predictive quality checks—efficiency is skyrocketing.
Evolution Ahead: As devices get smaller and smarter, FPCB prototyping will lean toward miniaturization and integration. Services that adapt will lead the pack.
Staying ahead means keeping an eye on these trends—and choosing a forward-thinking partner like Peakingtech, whose long-board and continuous production expertise already hints at what’s next.
VIII. Conclusion
Flexible printed circuit boards are more than a trend—they’re a cornerstone of modern electronics. For designers, they’re a canvas for creativity. For decision-makers, they’re a strategic asset. And at the heart of it all lies flexible printed circuit board prototyping services, turning your ideas into tangible, testable realities.
Why go it alone when you can tap into expertise, save time, and cut costs? Companies like Peakingtech, with their mastery of 1220mm FPCBs and 100-meter continuous production for LED strips, show what’s possible when you partner with the right team.
So, what’s your next project? A bendable sensor? A sprawling LED array? Whatever it is, a prototyping service could be your secret weapon. Reach out, explore your options, and let’s bring your vision to life—one flexible circuit at a time.