Understanding the Cost of Plastic Injection Molds: A Comprehensive Guide
Plastic injection molding is a cornerstone of modern manufacturing, enabling the mass production of everything from medical devices to consumer goods. However, one of the most common questions from businesses and innovators is: “What does a plastic injection mold cost?”
2/7/20253 min read
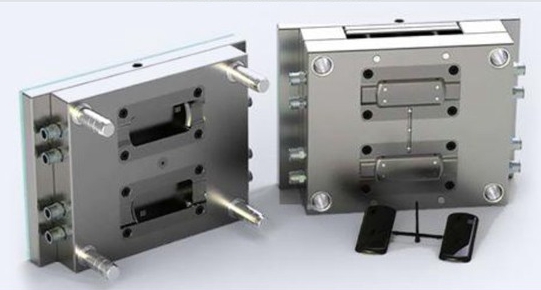
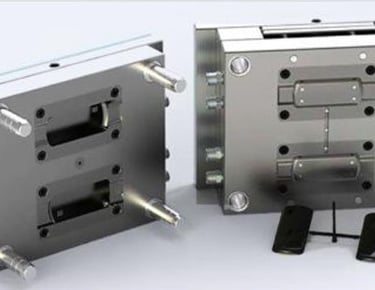
Plastic injection molding is a cornerstone of modern manufacturing, enabling the mass production of everything from medical devices to consumer goods. However, one of the most common questions from businesses and innovators is: “What does a plastic injection mold cost?” The answer isn’t straightforward, as mold pricing depends on a variety of factors. In this guide, we’ll break down the key elements that influence mold costs and provide actionable insights for budgeting your project effectively.
Key Factors That Determine Injection Mold Costs
Mold Complexity
The design intricacy of your part directly impacts mold cost. Simple molds for flat or low-detail components require less machining and engineering, keeping costs lower. Conversely, complex geometries, undercuts, tight tolerances, or textured finishes demand advanced tooling techniques (like multi-slide actions or EDM machining), which drive up expenses.Material Selection
Molds are typically made from aluminum or steel:Aluminum Molds: Cost-effective and faster to produce, these are ideal for prototypes or short production runs (10–1,000 parts). However, aluminum wears faster under high-pressure cycles.
Steel Molds: More durable and capable of producing millions of parts, steel molds are pricier upfront but offer long-term value for high-volume production. Variants like P20 or hardened tool steel further affect cost and lifespan.
Size and Number of Cavities
Larger molds require more material and machining time, increasing costs. Additionally, multi-cavity molds (which produce multiple parts per cycle) are more expensive to design but boost production efficiency. For example, a 4-cavity mold may cost 50% more than a single-cavity version but quadruple output.Lead Time
Expedited tooling schedules often come with a premium. Planning ahead allows manufacturers to optimize workflows, while rushed timelines may incur additional fees for overtime or priority machining.
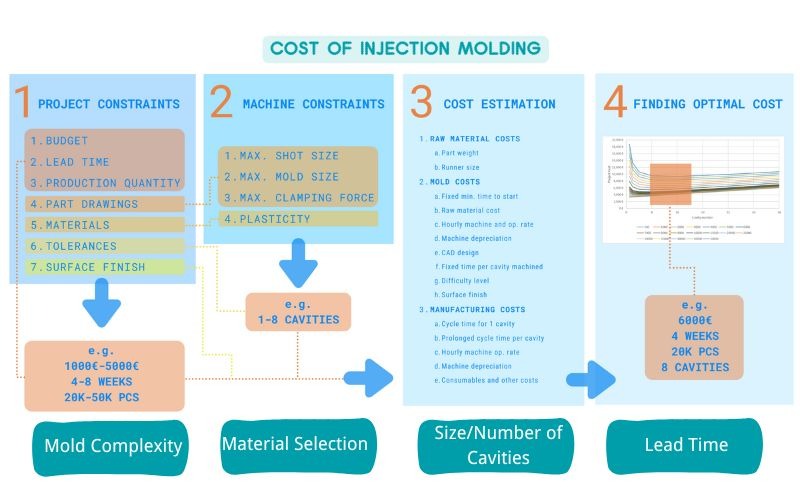
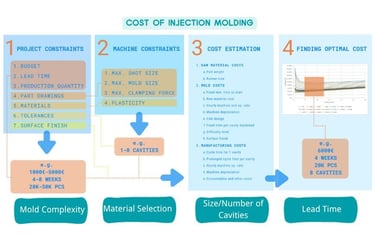
Typical Cost Ranges for Injection Molds
Prototype Molds (1,000–1,000–10,000):
Made from aluminum, these are designed for small batches or testing. While affordable, they lack the durability for long-term use.Mid-Range Molds (10,000–10,000–50,000):
Steel molds in this range suit medium-volume production (10,000–100,000 parts). They balance durability and cost, often with basic features like 2–4 cavities.High-End Molds (50,000–50,000–200,000+):
Built for mass production (millions of parts), these molds use premium steel, intricate cooling systems, and multi-cavity designs. They’re common in industries like automotive or aerospace, where precision and longevity are critical.
How to Reduce Injection Mold Costs
Simplify Your Design
Minimize undercuts, thin walls, and complex textures. Collaborate with your mold designer early to identify cost-saving opportunities without compromising functionality.Choose the Right Material
Opt for aluminum if you’re testing a concept or producing small batches. Reserve steel for high-volume needs where durability justifies the investment.Optimize Cavity Count
Start with a single cavity for prototyping, then scale up as demand grows. Over-investing in cavities upfront can inflate costs unnecessarily.Partner with Experienced Manufacturers
A reputable mold maker can identify inefficiencies, suggest design improvements, and leverage economies of scale. Offshore manufacturers may offer lower rates, but weigh potential trade-offs in communication and quality control.
Conclusion: Balancing Cost and Quality
While plastic injection molds represent a significant upfront investment, understanding the factors that drive costs empowers you to make informed decisions. By prioritizing design simplicity, material suitability, and production volume needs, you can optimize your budget without sacrificing quality. Remember: a well-built mold not only reduces per-part costs over time but also ensures consistent product quality—key to staying competitive in today’s market.
Whether you’re launching a new product or scaling production, partnering with a trusted manufacturer and investing in the right tooling strategy will pay dividends in the long run.