Understanding IPC Standards for PCB Quality and Reliability
Whether you're developing a consumer gadget, medical device, or military-grade technology, the performance of your PCB can make or break the product. The PCB serves as the backbone of your device, interconnecting components and enabling critical functions. However, a poor-quality PCB can lead to malfunction, costly recalls, and damaged reputations.
2/18/20256 min read
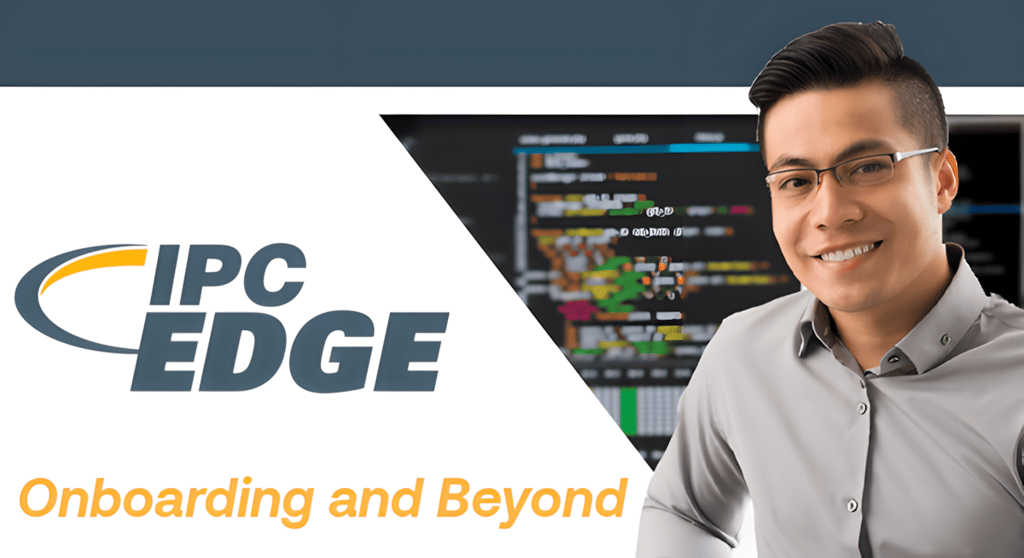
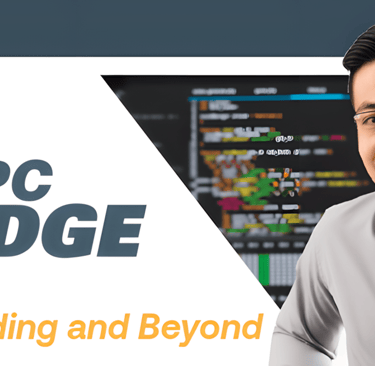
When designing an electronics product, one of the most important—and often overlooked—components is the printed circuit board (PCB). Whether you're developing a consumer gadget, medical device, or military-grade technology, the performance of your PCB can make or break the product. The PCB serves as the backbone of your device, interconnecting components and enabling critical functions. However, a poor-quality PCB can lead to malfunction, costly recalls, and damaged reputations.
This is where IPC standards come in. Developed by the Institute for Printed Circuits (IPC), these internationally recognized guidelines help ensure that every PCB meets a set of predefined quality and reliability criteria. In this article, we'll explore the importance of IPC standards in PCB design and manufacturing, dive into some key standards, and share real-world examples to illustrate their impact.
1. What Are IPC Standards?
IPC, originally known as the Institute for Printed Circuits, is a global association that sets industry standards for electronics design, assembly, and testing. Founded in 1957, IPC now collaborates with manufacturers, engineers, and quality specialists to develop best practices for PCB production.
The core purpose of IPC standards is to eliminate variability in PCB manufacturing, ensuring that products are consistent, reliable, and meet the necessary industry specifications. Without these standards, manufacturers would face unpredictable quality, delays in production, and potentially disastrous product failures in the field.
For instance, the automotive industry, where PCB failure can result in safety hazards or production stoppages, relies heavily on IPC standards to ensure the reliability of in-car electronics. Car manufacturers like Toyota, Ford, and GM require their suppliers to adhere to IPC guidelines to meet stringent quality control measures, ensuring the components in their vehicles last for years and operate safely.
2. Key IPC Standards for PCB Quality and Reliability
IPC has developed numerous standards, but several are particularly critical in maintaining the quality and reliability of PCBs. Let’s explore some of the key ones:
2.1 IPC-A-600: Acceptability of Printed Boards
IPC-A-600 is a comprehensive guide that outlines the visual inspection criteria for bare PCBs. It provides a clear set of guidelines that help manufacturers and quality control teams assess whether a PCB meets the acceptable quality level for various types of products.
Real-World Example:
Let’s say you’re working on a PCB for a medical device that requires Class 3 quality, the highest level of reliability. IPC-A-600 outlines the acceptance criteria that your PCB must meet, including no visible damage to the copper traces or solder pads and no delamination of the laminate material. Any deviation from these criteria would render the PCB unsuitable for medical use, potentially compromising the safety of the device.
In industries like medical devices, aerospace, and military, a Class 3 PCB is non-negotiable. Products in these fields require maximum reliability, and failure to comply with IPC-A-600 standards could lead to catastrophic results, such as malfunctioning medical equipment or faulty military electronics.
2.2 IPC-6012: Qualification and Performance for Rigid PCBs
IPC-6012 outlines the performance requirements for rigid PCBs. This standard addresses important aspects such as material selection, plating thickness, conductive pattern integrity, and the PCB's ability to withstand stress over time.
Real-World Example:
For a smartphone manufacturer like Apple, ensuring that a PCB meets IPC-6012 standards is critical. A failure in the PCB could lead to issues like overheating or, in extreme cases, the device catching fire. The thermal management properties required by IPC-6012 are critical for high-performance electronics. Apple works with suppliers who are IPC-certified to ensure their PCBs are capable of dissipating heat effectively, preventing costly issues such as device failure or customer dissatisfaction.
2.3 IPC-2221: Generic Standard on PCB Design
Designing a PCB isn’t just about creating a layout; it's about ensuring that the layout is manufacturable. IPC-2221 defines the rules for designing PCBs that are not only functional but also manufacturable at scale. This includes guidelines for trace widths, hole sizes, and signal integrity.
Real-World Example:
Consider an IoT company that is designing a PCB for a sensor that will be deployed in remote environments. Adhering to IPC-2221’s design guidelines ensures that the PCB is not only reliable but cost-effective to produce in high volumes. For example, if traces are too narrow or too close together, the PCB may experience interference or even short circuits. By following IPC-2221, designers can ensure that the PCB layout will pass manufacturing tolerances and meet performance expectations.
2.4 IPC-A-610: Acceptability of Electronic Assemblies
While IPC-A-600 defines the criteria for bare PCB acceptability, IPC-A-610 is focused on assembled PCBs. It provides guidelines for assessing the quality of the solder joints, component placement, and general assembly.
Real-World Example:
In the consumer electronics industry, companies like Samsung must adhere to IPC-A-610 when assembling their smartphones and tablets. A poor solder joint or misaligned component can lead to performance issues, such as malfunctioning touchscreens or connectivity problems. For instance, a failure in the PCB of a Samsung Galaxy phone might cause the device to overheat or fail to charge. By applying IPC-A-610 standards, manufacturers ensure that all assembled components are correctly placed and soldered, minimizing the risk of post-assembly failures.
2.5 IPC-5725: Guidelines for Resin Coated Copper (RCC) in PCBs
For high-frequency applications, such as in telecommunications or automotive radar systems, IPC-5725 provides guidelines on using Resin Coated Copper (RCC) to enhance PCB performance. RCC materials help minimize signal loss, making them essential for high-speed or high-frequency applications.
Real-World Example:
In autonomous vehicles, radar and LiDAR systems are crucial for detecting objects in the environment. These systems rely on PCBs with high-frequency capabilities to process data in real time. Manufacturers of these systems use RCC materials as outlined in IPC-5725 to ensure the PCB can handle high-frequency signals without degrading signal quality, thus enhancing the reliability of the entire system.
3. Why IPC Standards Matter for PCB Manufacturing
IPC standards are essential for several reasons.
3.1 Ensuring Consistent Quality
When working with multiple suppliers across different regions, having a uniform set of standards ensures that the PCBs produced will meet the same level of quality, no matter where they’re made. For instance, a global tech company like Intel can expect consistent results across its suppliers, thanks to IPC standards.
3.2 Reducing Defects and Failures
Defects like poor solder joints or faulty vias can lead to product malfunctions or even recalls. For example, in 2010, Toyota faced a massive recall for millions of vehicles due to faulty PCBs in their electronic control units, causing safety and operational issues. Ensuring IPC compliance significantly reduces these types of risks.
3.3 Meeting Industry and Regulatory Requirements
In industries like aerospace and medical devices, the consequences of PCB failure are far-reaching. Failure to meet IPC standards in these fields can lead to regulatory fines or, worse, product recalls. For example, the FDA mandates strict quality control over medical devices, and any company failing to comply with standards like IPC-A-610 could face regulatory penalties or legal consequences.
4. How to Implement IPC Standards in PCB Production
Adhering to IPC standards requires a proactive approach. Here’s how to make sure you implement these guidelines effectively:
4.1 Work with IPC-Certified Manufacturers
Choose manufacturers that are IPC-certified or have a proven track record in adhering to IPC standards. A supplier’s certification should be verified regularly through audits and inspections to ensure compliance.
4.2 Conduct Regular Inspections
Use the IPC standards as part of your inspection process. In the automotive industry, for instance, manufacturers like Tesla perform rigorous visual inspections based on IPC-A-600 and IPC-A-610 to ensure their PCBs meet the highest standards before being assembled into vehicles.
4.3 Train Your Team on IPC Compliance
Offer IPC training for your design, engineering, and quality control teams. This ensures everyone involved in the PCB development process is familiar with the standards and can spot potential issues early.
4.4 Stay Updated on IPC Revisions
IPC standards are updated regularly to reflect technological advances and industry trends. For example, the transition to higher-frequency applications has made IPC-5725 increasingly relevant in the telecom and automotive sectors. Stay ahead of revisions by subscribing to IPC updates and attending relevant workshops.
5. Common Challenges in Meeting IPC Standards
Despite the clear benefits, meeting IPC standards can present challenges:
5.1 Balancing Cost vs. Quality
High-performance PCBs that meet stricter IPC standards come at a cost. In consumer electronics, like smartphones, manufacturers often face the challenge of balancing quality and cost. Apple, for instance, spends considerable resources ensuring its PCBs meet Class 3 standards, which comes at a higher cost but ensures product reliability.
5.2 Supplier Compliance Issues
Not all manufacturers follow IPC standards to the letter. In 2018, a well-known European automotive supplier faced issues when it was discovered that some of their PCB suppliers were not IPC-certified. This led to quality control issues and delays in production, forcing the supplier to overhaul their vendor selection process.
5.3 Keeping Up with Standard Updates
The fast pace of technology means that IPC standards are continually evolving. Staying updated with these changes can be challenging. However, neglecting to incorporate the latest standards can result in subpar product performance. For example, automotive manufacturers need to adapt to newer, more stringent standards as they incorporate more advanced PCB technologies for autonomous driving systems.
Conclusion
IPC standards aren’t just guidelines—they are essential tools for ensuring the quality and reliability of your PCBs. By following these standards, you can:
✔ Improve product durability and lifespan
✔ Minimize defects and costly recalls
✔ Meet regulatory requirements in highly regulated industries
✔ Build a trusted reputation with customers and partners
In short, whether you're developing a next-gen consumer product, an automotive component, or a critical medical device, adherence to IPC standards will significantly increase your chances of success. With the right knowledge, resources, and partners, your PCBs will perform reliably—every time.
Are your PCBs up to IPC standards? If not, it’s time to make compliance a top priority.