Troubleshooting Injection Molding Defects: Solutions for Common Issues
From sleek smartphone housings to intricate connectors, this process delivers precision parts at scale. But anyone who’s spent time in the trenches of product development knows it’s not always smooth sailing. Defects like warping or sink marks can derail timelines, inflate costs, and leave you scrambling to explain why that perfectly designed enclosure doesn’t fit the PCB anymore.
2/23/20256 min read
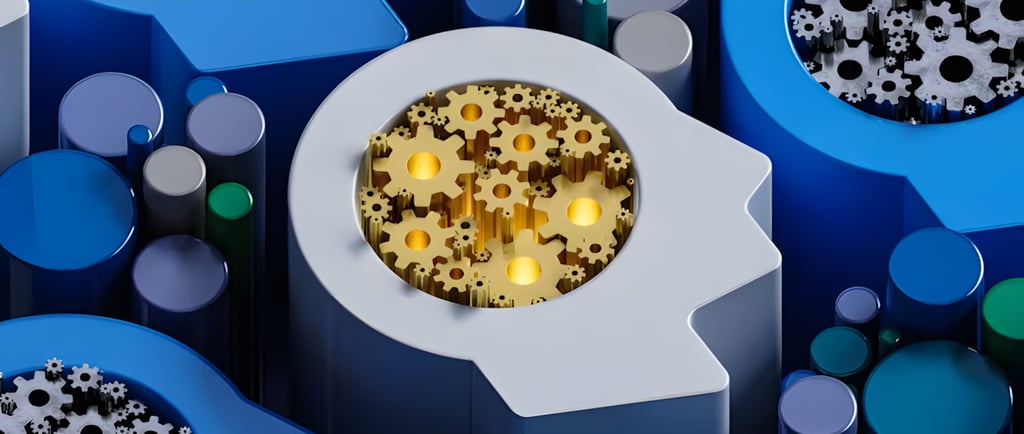
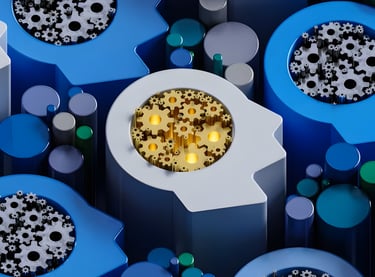
Injection molding is the backbone of modern electronics manufacturing. From sleek smartphone housings to intricate connectors, this process delivers precision parts at scale. But anyone who’s spent time in the trenches of product development knows it’s not always smooth sailing. Defects like warping or sink marks can derail timelines, inflate costs, and leave you scrambling to explain why that perfectly designed enclosure doesn’t fit the PCB anymore. I’ve been there—staring at a warped prototype, coffee in hand, wondering where it all went wrong. If you’re a designer or decision-maker in electronics development, this article is for you. We’ll unpack the most common injection molding headaches—warping and sink marks especially—and arm you with practical, actionable solutions to keep your projects on track.
Understanding Injection Molding Defects
Let’s start with the basics. Injection molding defects aren’t random gremlins; they’re symptoms of something off-kilter—be it the material, the mold, or the machine settings. In electronics, where tolerances are tight and aesthetics matter, these flaws can be dealbreakers. Warped casings won’t align with circuit boards, and sink marks on a glossy finish scream “cheap” to customers. The culprits? Uneven cooling, poor mold design, or pushing a material beyond its limits. For designers, spotting these issues early is key; for decision-makers, it’s about knowing when to tweak the process or invest in a fix.
The good news? Most defects are solvable with a systematic approach. Think of it like debugging code—identify the glitch, trace its source, and test a solution. Except here, you’re working with molten plastic, not lines of Python. Let’s dive into two of the biggest offenders—warping and sink marks—then touch on a few others you’re likely to encounter.
Warping – Causes and Solutions
Picture this: You’ve designed a slim, lightweight enclosure for a wearable device. The CAD looks flawless, but the first batch comes back twisted like a pretzel. That’s warping—uneven shrinkage that bends your part out of shape. It’s maddening because it often doesn’t show up until the part cools, leaving you with a stack of rejects and a looming deadline.
What’s Happening?
Warping happens when different areas of the part cool and shrink at different rates. Thick sections contract more than thin ones, or one side of the mold cools faster than the other. Maybe the walls vary too much in thickness—an easy trap in electronics where you’re balancing strength with sleekness. Or perhaps the packing pressure was cranked too high, forcing extra stress into the part. I’ve seen this with ABS enclosures—great for impact resistance, but prone to warping if you’re not careful.
How to Fix It:
First, tackle cooling. If the mold’s cooling channels aren’t evenly placed, you’re asking for trouble. Adjust their layout or extend cooling time so the part solidifies uniformly. I once worked on a project where a quick tweak to the coolant flow turned a 20% reject rate into single digits. Next, check your design. Uneven wall thickness is a silent killer—aim for consistency, even if it means rethinking rib placement or adding a slight taper.
Process tweaks help too. Dial back the packing pressure to reduce internal stress, and play with injection speed to avoid overpacking one area. If the material’s the issue—say, a high-shrinkage resin like unfilled nylon—consider switching to a filled version (glass-filled works wonders) or a low-shrinkage alternative like polycarbonate.
A Designer’s Secret Weapon: Mold flow simulation. It’s like a crystal ball for predicting warpage before you cut steel. Run a simulation, spot the hot zones, and adjust your design or parameters. It’s an upfront cost, but it beats scrapping a mold later. For decision-makers, this is where you weigh the ROI—spend now to save later.
Sink Marks – Causes and Solutions
Now imagine a different headache: You’ve got a polished remote control housing, but there’s a tiny dent right where the logo goes. That’s a sink mark—another shrinkage issue, but this time it’s localized. In electronics, sink marks are a double whammy: They ruin the look and hint at structural weak spots. Customers notice, and so do quality inspectors.
What’s Happening?
Sink marks pop up when thick sections cool slower than the surface. The outer skin hardens, but the core keeps shrinking, pulling the surface inward. Think about those chunky bosses or ribs you added for screw mounts—they’re prime suspects. Or maybe the packing pressure wasn’t enough to fill out the part as it cooled. High melt temperatures can make it worse, too—more heat, more shrinkage.
How to Fix It:
Start with the process. Boost packing pressure and hold it longer to force material into those thick spots as they cool. I’ve seen this work miracles on a chunky battery cover—just a few extra seconds of hold time smoothed out the dents. Temperature matters too—lower the melt temp a bit to reduce shrinkage, but don’t go so low you get short shots (more on those later).
Design tweaks can save the day here. If you’ve got a thick section, thin it out or add ribs to spread the load without bulking up. Gate placement counts too—make sure material flows evenly to problem areas. I once shifted a gate on a mold for a sensor housing, and the sink marks vanished overnight.
Pro Tip for Decision-Makers: Invest in pressure sensors for your molds. They give real-time feedback on how well you’re packing out the part. It’s a small upgrade that pays off in consistent quality—perfect for high-stakes electronics where every unit counts.
Other Common Defects and Quick Fixes
Warping and sink marks aren’t the only gremlins in injection molding. Here’s a quick rundown of other issues you might face, plus fixes to keep your production humming.
Short Shots:
You’ve got a half-filled part—material didn’t reach the corners. Maybe the injection pressure was too low, or air got trapped and blocked the flow. Crank up the pressure, add vents to the mold, or increase the shot volume. I’ve seen this with thin-walled connectors—better venting turned it around fast.
Flash:
Excess plastic oozes out at the mold’s parting line, leaving a messy edge. It’s usually too much pressure or a worn-out mold. Ease off the injection force, check the clamping tonnage, and inspect the mold for damage. A quick repair can stop this cold—don’t let it become a recurring cost.
Burn Marks:
Brown or black streaks on your part? That’s overheated air getting trapped and scorching the plastic. Add vents, slow the injection speed, or drop the melt temp. I once fixed this on a clear acrylic lens by tweaking the vent size—no more ugly marks, just crystal-clear parts.
Systematic Troubleshooting Approach
So, how do you tackle these issues without losing your mind? Treat it like a detective game. Step one: Spot the defect. Grab a caliper or a 3D scanner and measure it—know exactly what you’re dealing with. Step two: Dig into the data. Check the machine logs—temperature, pressure, cycle time. Was something off? Step three: Look at the mold and material. Is the gate in the right spot? Is the resin a mismatch?
Step four is where the rubber meets the road—test fixes one at a time. Adjust cooling, then pressure, then temp, and log what works. I’ve burned through weekends tweaking settings, but documenting each change saved me from repeating mistakes. Finally, step five: Run a small batch to confirm your fix before going full tilt. It’s methodical, but it beats guessing and hoping.
Preventative Measures for Long-Term Success
Fixing defects is great, but preventing them is better—especially in electronics, where margins are slim and deadlines are brutal. Start with mold flow simulation. It’s not just for warping—it catches sink marks, short shots, you name it. Next, keep your molds in top shape. A little maintenance goes a long way—worn seals or clogged channels can sneak defects into every cycle.
Training matters too. Equip your team to spot issues early and adjust on the fly. I’ve seen operators catch warping mid-run because they knew the signs—saved us a fortune. And don’t sleep on material selection. Match the resin to your part’s geometry and demands—PC/ABS blends are my go-to for electronics enclosures; tough, stable, and mold-friendly.
Conclusion
Injection molding defects like warping and sink marks can feel like personal attacks when you’re knee-deep in an electronics project. But they’re not unbeatable. With the right tweaks—cooling for warping, packing for sink marks—and a sharp eye on design and process, you can churn out flawless parts. Designers, this is your chance to refine your CAD and dodge pitfalls. Decision-makers, it’s your call to greenlight tools like sensors or simulations that keep quality high and costs low.
Got a tricky defect you’ve cracked? Drop it in the comments—I’d love to hear your war stories. Or if you’re stumped, reach out to an expert. We’re all in this plastic-molding game together, chasing that perfect part.