Top Electronics Manufacturing Trends in 2025: What Designers and Decision-Makers Need to Know
We’re diving into the latest trends shaping electronics manufacturing. From smarter automation to greener practices, these shifts aren’t just buzzwords; they’re game-changers that will influence your next project, budget, and timeline.
3/7/20255 min read
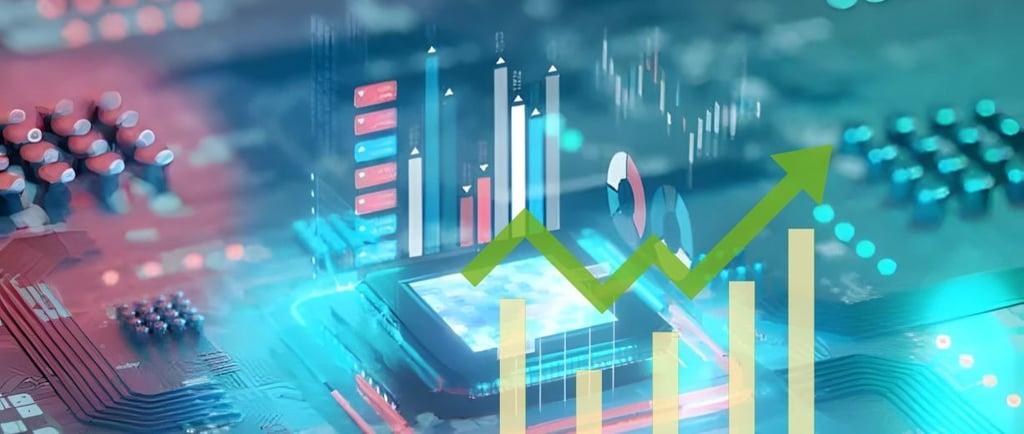
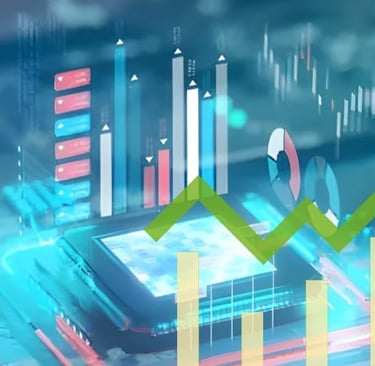
Imagine a world where your smartphone is smaller than ever, your factory runs itself, and every circuit board you design helps save the planet. Sounds like science fiction? It’s not—it’s the reality of electronics manufacturing in 2025. The global industry is hurtling toward a projected valuation of over $1 trillion by the end of this decade, fueled by breakthroughs that are rewriting the rules of production. For designers and decision-makers in electronics development, keeping up isn’t just smart—it’s survival.
In this article, we’re diving into the latest trends shaping electronics manufacturing. From smarter automation to greener practices, these shifts aren’t just buzzwords; they’re game-changers that will influence your next project, budget, and timeline. Let’s explore what’s happening now and how it impacts you.
Trend 1: Adoption of Automation and Industry 4.0
If you’ve walked into a modern electronics factory lately—or even watched a virtual tour—you’ve likely seen the hum of robots and the glow of connected screens. That’s Industry 4.0 in action, the fourth industrial revolution blending automation, IoT (Internet of Things), and data-driven insights. For designers, this means your prototypes can hit production faster; for decision-makers, it’s about slashing costs without sacrificing quality.
Take robotics, for instance. They’re not just assembling parts—they’re inspecting them with AI-powered vision systems that catch defects human eyes might miss. Predictive maintenance is another gem: sensors on machines signal when they’re about to fail, saving millions in downtime. Companies like Foxconn, a giant in contract manufacturing, have leaned hard into this, turning their plants into "smart factories" where efficiency rules.
What it means for you: Designers can iterate faster with real-time feedback from automated systems, while decision-makers can justify the upfront investment with long-term savings. The future? It’s already here—just ask the folks running those humming production lines.
Trend 2: Miniaturization and Advanced Component Design
Remember when a "portable" computer weighed as much as a toddler? Today, we’re cramming more power into chips the size of a fingernail, thanks to miniaturization. In 2025, we’re talking 3-nanometer chips—think of them as the Ferraris of semiconductors, sleek and lightning-fast. TSMC and Intel are leading the charge, pushing boundaries that seemed impossible a decade ago.
But it’s not just chips. Flexible circuits and 3D packaging are letting designers dream up devices that bend, fold, and fit anywhere—think wearables that hug your wrist or medical implants that feel like nothing’s there. For decision-makers, this trend screams opportunity: smaller components mean leaner products, but they also demand precision in supply chains and testing.
What it means for you: Designers, get ready to rethink form factors—your next project might shrink by half. Decision-makers, budget for cutting-edge tools to keep up. The reward? Products that wow customers and dominate markets.
Trend 3: Sustainable and Green Manufacturing Practices
Let’s get real: the planet’s not optional. Consumers and regulators alike are pushing electronics manufacturers to clean up their act, and 2025 is the year sustainability stops being a buzzword and starts being a mandate. From recyclable materials to energy-efficient production lines, "green manufacturing" is reshaping how we build tech.
Apple’s chasing carbon neutrality by 2030, and Samsung’s recycling old phones into new components. These aren’t just PR stunts—they’re proof that sustainable practices can coexist with profit. Designers are now tasked with choosing eco-friendly materials—like biodegradable plastics—while decision-makers weigh the cost of greener tech against long-term gains (and happier customers).
What it means for you: Designers, your next spec sheet might include "low environmental impact" alongside "high performance." Decision-makers, it’s time to pitch sustainability as a competitive edge—because it is.
Trend 4: Rise of Additive Manufacturing (3D Printing)
3D printing isn’t new, but its role in electronics manufacturing is exploding. Picture this: instead of waiting weeks for a custom PCB (printed circuit board) prototype, you print it in-house overnight. That’s additive manufacturing in 2025—fast, flexible, and a little bit magical.
Beyond prototyping, companies are using 3D printers for enclosures, connectors, and even conductive traces. It’s not just about speed; it’s about cutting waste and dodging supply chain headaches. Researchers at MIT have even printed fully functional sensors, hinting at a future where entire devices roll off a printer. For designers, this is a playground—test wild ideas without breaking the bank. For decision-makers, it’s a chance to rethink production timelines.
What it means for you: Designers, experiment freely—your next breakthrough might come from a printer. Decision-makers, consider investing in this tech; it’s a shortcut to agility in a cutthroat market.
Trend 5: Supply Chain Resilience and Localized Production
If the chip shortages of the early 2020s taught us anything, it’s that global supply chains can crumble fast. In 2025, electronics manufacturing is fighting back with resilience. Nearshoring—bringing production closer to home—is picking up steam, fueled by initiatives like the U.S. CHIPS Act, which pumps billions into domestic semiconductor plants. Europe’s doing it too, building regional hubs to cut reliance on Asia.
For designers, this means fewer delays in getting critical components like microcontrollers or sensors. For decision-makers, it’s a strategic pivot—spend more upfront to secure supply, or risk another shortage derailing your launch? The math’s starting to favor local production, and the peace of mind’s hard to beat.
What it means for you: Designers, expect smoother workflows with parts arriving on time. Decision-makers, weigh the cost of local vs. global—it’s a decision that could define your next fiscal year.
Trend 6: Integration of Artificial Intelligence and Machine Learning
AI isn’t just for chatbots—it’s rewriting electronics manufacturing from design to delivery. Imagine software that optimizes your circuit layout before you even sketch it, or machine learning models that spot defects in milliseconds. That’s 2025, and it’s real.
NVIDIA’s using AI to design its next-gen chips, shaving months off development. On the factory floor, ML algorithms predict demand, tweak production schedules, and flag quality issues before they spiral. Designers get a superpower: tools that think alongside you. Decision-makers get data—hard, actionable numbers to justify every move.
What it means for you: Designers, lean on AI to refine your work—it’s like having a genius intern who never sleeps. Decision-makers, use those insights to stay ahead of competitors still crunching spreadsheets.
Conclusion
So, where does this leave us? Electronics manufacturing in 2025 is a whirlwind of automation, tiny tech, green goals, 3D printing, resilient supply chains, and AI smarts. For designers, it’s a chance to push boundaries—create devices that are smaller, smarter, and kinder to the Earth. For decision-makers, it’s a call to act—invest in the right tools, people, and strategies to ride this wave.
The future’s not waiting. It’s unfolding on factory floors and in design labs right now. Whether you’re sketching the next big thing or signing off on a multimillion-dollar production run, these trends are your roadmap. What’s your next move? Drop your thoughts below—I’d love to hear how you’re navigating this wild ride.