Top 10 Trends Shaping Electronics Manufacturing in 2025
Electronics manufacturing is evolving faster than ever, driven by technological advancements, supply chain shifts, and increasing demand for sustainable solutions. For designers and decision-makers in electronics product development, keeping up with these changes is not just an option—it’s a necessity.
2/16/20255 min read
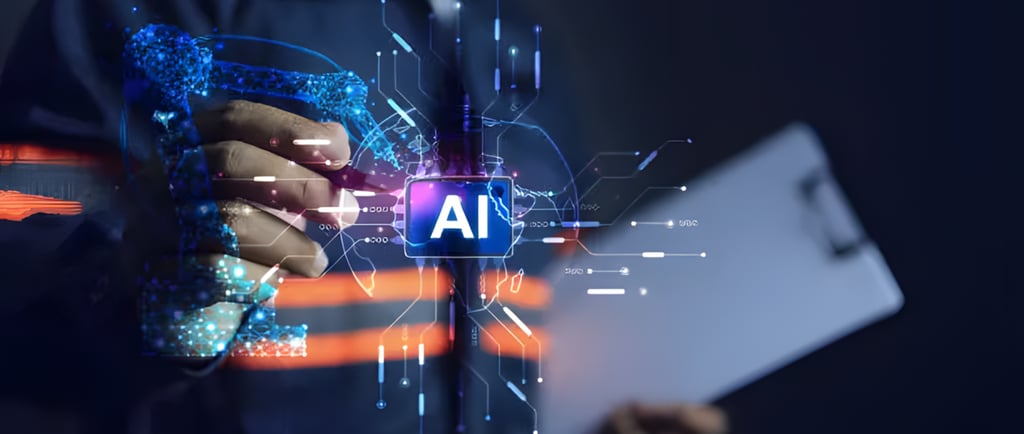
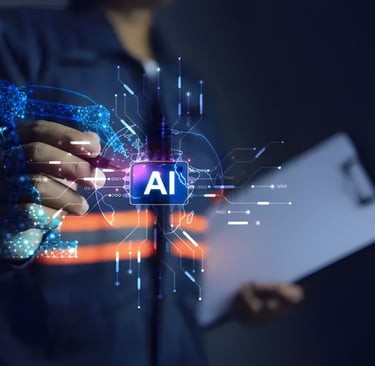
Electronics manufacturing is evolving faster than ever, driven by technological advancements, supply chain shifts, and increasing demand for sustainable solutions. For designers and decision-makers in electronics product development, keeping up with these changes is not just an option—it’s a necessity. Whether you're working on a new consumer gadget, industrial equipment, or medical device, understanding the latest trends will help you make smarter choices and stay ahead of the competition.
Here are the top 10 trends shaping electronics manufacturing in 2025 that you should keep an eye on.
1. AI and Machine Learning in Manufacturing
Artificial intelligence (AI) and machine learning (ML) have moved beyond hype and are now essential in electronics manufacturing. Companies are using AI-driven automation for quality control, predictive maintenance, and process optimization.
Imagine a system that detects microscopic defects in PCBs before they lead to failures or an AI-powered predictive maintenance tool that prevents unexpected machine breakdowns. These innovations improve efficiency, reduce waste, and ultimately lower costs.
One of the most impressive applications of AI in manufacturing is using ChatGPT or DeepSeek to assist engineers in optimizing production workflows. These AI models can analyze vast amounts of manufacturing data, suggest process improvements, and even generate real-time troubleshooting steps for production line anomalies. For instance, if a robotic arm in a factory starts deviating from its expected motion, an AI assistant like ChatGPT can instantly diagnose whether the issue is due to mechanical wear, software glitches, or environmental changes, reducing downtime significantly.
Another example is AI-driven automated optical inspection (AOI), where deep learning models are trained to identify defects in solder joints, traces, and components with higher accuracy than traditional rule-based systems. AI systems like DeepSeek can also help optimize material usage, reducing waste and improving sustainability in the production process.
Moreover, generative AI is revolutionizing PCB design optimization by automatically suggesting layout improvements to enhance thermal performance and signal integrity. Engineers using AI-powered design tools can create more efficient circuits while reducing development cycles, ultimately bringing products to market faster.
If you're designing an electronics product, consider how AI can enhance both the manufacturing process and the end product itself. Integrating AI-driven tools into your workflow can lead to smarter decision-making, increased efficiency, and a competitive edge in the fast-paced electronics industry.
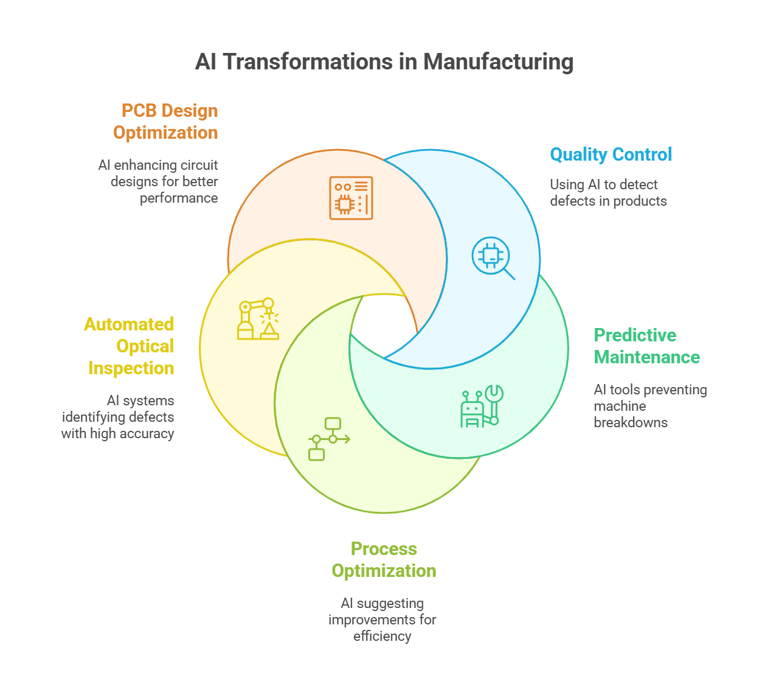
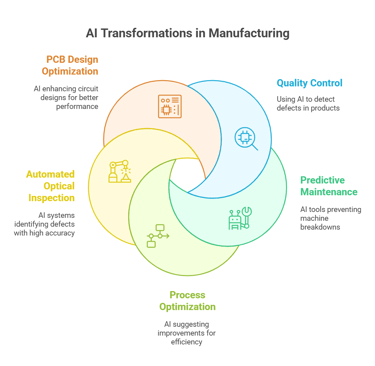
2. Rise of Smart Factories & Industry 4.0
The smart factory revolution, powered by the Internet of Things (IoT), cloud computing, and cyber-physical systems, is transforming how electronics are made.
Factories are becoming more connected than ever, using digital twins—virtual replicas of physical manufacturing environments—to simulate and optimize production in real time. For designers, this means faster prototyping, real-time tracking of production progress, and fewer manufacturing surprises.
If you're leading an electronics project, integrating smart factory solutions into your supply chain can provide greater transparency and agility, helping you meet tight deadlines without compromising on quality.
3. Advanced Robotics and Cobots (Collaborative Robots)
Automation has always played a role in electronics manufacturing, but the new wave of robotics—particularly collaborative robots (cobots)—is changing the game. Unlike traditional industrial robots that require complex programming and safety barriers, cobots work alongside human operators, assisting with tasks like assembly, soldering, and testing.
For designers, this means greater precision and consistency, especially in delicate tasks such as assembling miniaturized components for wearables or medical devices. Companies investing in cobots are not only increasing efficiency but also making manufacturing more flexible and scalable.
4. Sustainability and Green Manufacturing
Sustainability is no longer just a buzzword—it’s a requirement. Consumers and regulators are demanding eco-friendly products, and manufacturers are responding by adopting greener practices.
From energy-efficient production lines to sustainable materials, companies are focusing on reducing their environmental footprint. Some are using biodegradable circuit boards, while others are improving recyclability by designing electronics with modular components.
If your project is targeting environmentally conscious consumers, ensuring sustainability in manufacturing will not only help the planet but also enhance your brand’s reputation.
5. Miniaturization and High-Density Electronics
As electronics become more powerful, they’re also getting smaller. The demand for compact devices in industries like wearables, IoT, and healthcare is pushing manufacturers to develop high-density interconnect (HDI) PCBs, micro-LED displays, and ultra-thin batteries.
However, miniaturization comes with challenges, such as heat dissipation and signal integrity. Designers need to collaborate closely with manufacturers to ensure the product remains functional and reliable despite its reduced size.
If your next project involves miniaturized components, make sure your design and manufacturing teams are aligned from the start to avoid late-stage complications.
6. Advanced Semiconductor Manufacturing & Chip Innovations
The semiconductor industry is undergoing a massive transformation, driven by advancements in 3D semiconductors, new materials like gallium nitride (GaN) and silicon carbide (SiC), and the ongoing global chip shortage.
For product developers, these innovations mean better performance, lower power consumption, and new possibilities for device functionality. However, geopolitical factors affecting semiconductor supply chains mean designers must plan ahead, considering multiple sourcing options to avoid unexpected delays.
7. Additive Manufacturing & 3D Printing for Electronics
3D printing is no longer limited to prototyping—it’s now being used for production-grade electronics. Additive manufacturing allows for rapid iteration, on-demand production, and customization that traditional manufacturing cannot match.
For example, 3D-printed circuit boards (PCBs) enable designers to create complex, multi-layered circuits with embedded components, reducing the need for separate assembly steps. Conductive inks and printed electronics are also opening new possibilities for flexible and wearable devices.
If your project requires unique geometries or rapid iteration, exploring 3D printing technologies could significantly cut development time and costs.
8. Supply Chain Resilience and Regionalization
The past few years have exposed the vulnerabilities of global supply chains. In response, companies are moving towards regionalized manufacturing—also known as onshoring or nearshoring—to reduce reliance on distant suppliers.
For electronics product designers, this shift means better supply chain transparency and shorter lead times. However, it also requires careful planning to balance cost efficiency with supply chain resilience.
Partnering with suppliers that offer localized production capabilities could help you navigate these challenges while keeping your project on schedule.
9. Quantum Computing’s Emerging Influence
While still in its infancy, quantum computing is starting to make waves in materials science and circuit design. Researchers are using quantum simulations to discover new materials with superior electrical properties, which could eventually revolutionize semiconductor manufacturing.
For now, quantum computing remains more of a long-term trend, but staying informed on its progress could give forward-thinking product developers an edge in adopting cutting-edge materials and techniques.
10. Evolution of Flexible & Wearable Electronics
Flexible and wearable electronics are no longer futuristic concepts—they’re becoming mainstream. From stretchable circuits to electronic textiles, these innovations are finding applications in healthcare, sports, and consumer tech.
Designers working on medical wearables, smart clothing, or flexible displays need to consider new materials and manufacturing processes. The rise of printed electronics is also making it easier to integrate flexible components into existing products.
If your next project involves wearables, collaborating with specialized manufacturers in flexible electronics will be key to ensuring durability and performance.
Conclusion
The electronics manufacturing landscape in 2025 is being shaped by AI-driven automation, sustainability, miniaturization, and supply chain shifts. For product designers and decision-makers, staying ahead means embracing these trends and adapting manufacturing strategies accordingly.
Whether you’re developing a new consumer device, industrial solution, or medical innovation, understanding these changes will help you make better design choices, optimize production, and ensure long-term success.
Are you ready for the future of electronics manufacturing? Stay agile, stay informed, and most importantly, stay innovative!