The Science Behind Injection Molding: Understanding Pressure, Heat, and Flow
Behind every precision-engineered component in electronics lies a process that’s equal parts science and artistry: injection molding.
2/23/20256 min read
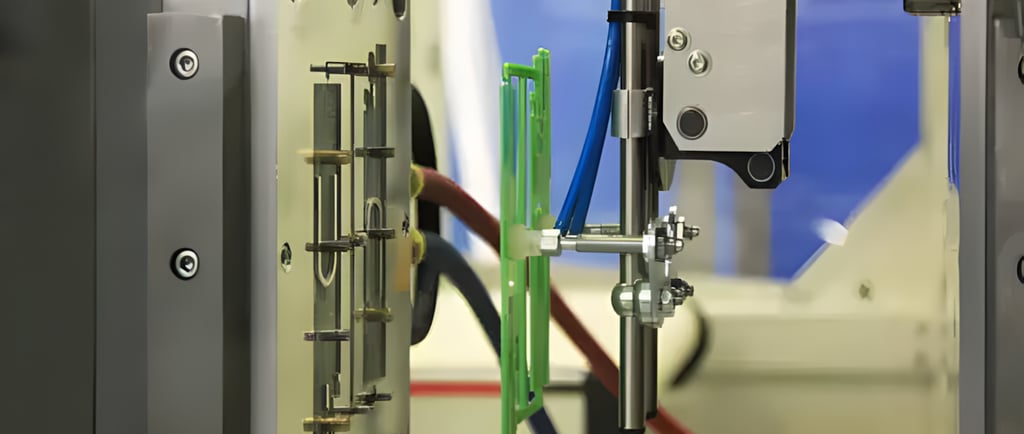
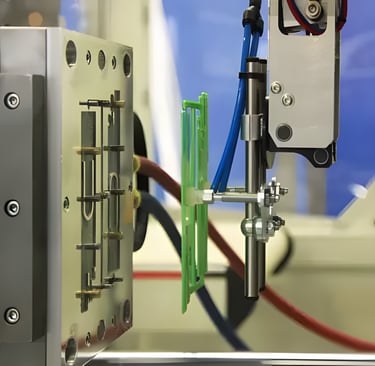
Imagine picking up your latest smartphone or plugging in a sleek charger. That satisfying click of a perfectly molded plastic casing? It’s no accident. Behind every precision-engineered component in electronics lies a process that’s equal parts science and artistry: injection molding. For designers and decision-makers in electronics development, understanding this process—specifically the interplay of pressure, heat, and flow—can mean the difference between a product that wows and one that flops. Let’s dive into the nitty-gritty of how these forces shape the plastic parts powering your next big innovation.
What Is Injection Molding, Anyway?
If you’re in electronics, you’ve likely seen injection molding at work—those tiny connectors, housings, or buttons that make your designs functional and beautiful. At its core, it’s a manufacturing method where molten plastic is shot into a mold, cooled, and popped out as a solid part. Simple, right? Not quite. It’s the go-to for mass production because it’s fast, repeatable, and can churn out parts with tolerances tighter than a gnat’s eyelash.
But here’s the kicker: getting it right isn’t just about having a fancy machine. It’s about mastering three key players—pressure, heat, and flow. Think of them as the trio jamming together in a rock band. If one’s out of tune, the whole performance falls apart. So, let’s break it down for the designers sketching the next big thing and the decision-makers signing off on production runs.
The Role of Pressure: The Muscle of the Operation
Pressure is the brute force that gets the job done. Picture this: you’ve got a vat of molten plastic—gooey, hot, and ready to roll. Pressure is what shoves it into every nook and cranny of your mold, ensuring that USB-C port or battery casing comes out crisp and detailed.
There are a few flavors of pressure in this game. First up is injection pressure, the initial push that forces the plastic through the machine’s nozzle into the mold—think of it as the sprinter bursting off the starting line. For electronics parts, this can hit 10,000 to 20,000 psi, depending on the design’s complexity. Then there’s packing pressure, which kicks in after the mold’s filled. It’s like a coach yelling, “Hold the line!” as the plastic cools and shrinks, preventing gaps or sink marks that could ruin a sleek finish. Finally, clamping pressure keeps the mold halves locked tight against all that force—crucial for those thin-walled enclosures you’re designing to keep weight down.
The science? It’s basic physics: Pressure = Force divided by Area. Too much pressure, and you get “flash”—those annoying plastic burrs that scream sloppy QC. Too little, and you’re stuck with “short shots,” where the plastic doesn’t fill the mold, leaving your connector DOA. For you designers, this means your intricate geometries need to play nice with the pressure limits of the machine. And for decision-makers, it’s a heads-up: skimping on a robust press could cost you downstream.
Heat: The Alchemist Turning Plastic into Gold
Now, let’s talk heat—the unsung hero that gets plastic from stiff pellets to a flowing liquid. Without it, your polycarbonate or ABS (you know, the stuff your rugged device casings are made of) wouldn’t budge. Heat’s job starts in the barrel of the injection molding machine, where temperatures climb from a cozy 200°F at the hopper to a blistering 500°F or more near the nozzle, depending on the material.
Here’s where it gets fun for the nerds among us. Plastics like ABS have a glass transition temperature (Tg)—say, around 221°F—where they go from rigid to rubbery. Push past that to their melting point, and they’re ready to flow. The barrel’s zoned heating system is like a chef simmering a sauce: too hot, and you burn it (thermal degradation, hello brittle parts); too cool, and it’s a clumpy mess that won’t fill your mold.
Once injected, the mold itself needs some thermal love—typically kept at 100–200°F for electronics parts. Why? It controls how fast the plastic cools. Too quick, and you get warpage; too slow, and cycle times drag, driving up costs. Heat lowers the plastic’s viscosity—its resistance to flow—making it glide like honey instead of slogging like molasses. For designers, this means material choice and wall thickness matter. Decision-makers, take note: investing in precise temperature controls pays off in consistency.
Flow: The Dance of Molten Plastic
Flow is where the magic happens—it’s how that molten plastic navigates your mold’s twists, turns, and tiny features. Think of it as choreography. The material’s got to waltz through runners, pirouette past gates, and fill every cavity without tripping over itself. For electronics, where parts like chip housings or lens covers demand precision, flow is make-or-break.
What drives it? Shear rate—how fast the plastic moves—plays a starring role. Most plastics are “shear-thinning,” meaning they flow easier under pressure (a bit like ketchup when you shake the bottle). The mold’s design—those narrow channels or sharp corners you sketched—dictates the flow path. Get it wrong, and you’ll see weld lines (where flows meet imperfectly) or air traps that wreck aesthetics and strength.
The science here dips into fluid dynamics. Molten plastic isn’t your average liquid—it’s “non-Newtonian,” so its behavior shifts with force and speed. Ever hear of the Hagen-Poiseuille equation? Simplified, it ties flow rate to pressure and viscosity, but in practice, it’s a juggling act. Cooling kicks in mid-dance, slowing the flow as heat escapes into the mold. For designers, this means simulating flow early—tools like Moldflow can save your bacon. Decision-makers, this is your cue: better mold design upfront cuts rework later.
Pressure, Heat, and Flow: The Three Amigos
Here’s where it gets real: these three don’t work solo. They’re a team. Heat softens the plastic and cuts viscosity, pressure powers the flow, and flow dictates how cooling shapes the final part. Mess up one, and the others stumble.
Take a thin-walled electronics housing—say, a smartwatch backplate. You need high injection pressure (15,000 psi, maybe) to zip the plastic through tight spaces before it cools. The heat has to be spot-on—too low, and it won’t flow; too high, and it degrades, leaving your part brittle. Flow must be optimized with gate placement to avoid weak spots where streams collide. Tweak one variable—like bumping mold temp 20°F—and the others shift too.
I’ve seen this in action. A buddy of mine, an engineer at a wearables startup, fought warpage on a prototype. Turned out their mold was too cold, stiffening the plastic mid-flow. A quick adjustment, and boom—perfect parts. For you designers, this interplay is why collaboration with moldmakers matters. Decision-makers, it’s a reminder: cutting corners on simulation or equipment risks delays.
Real-World Wins and Cool Innovations
So, why should you care? Because this science powers your world. That tiny HDMI connector? Injection molding nailed its pin alignment. The matte finish on your laptop chassis? Heat and flow dialed in just right. It’s not just about making stuff—it’s about making it well, at scale, without breaking the bank.
And the field’s evolving. Smart sensors now track pressure and heat in real time, catching hiccups before they scrap a run—perfect for tight-margin electronics. Simulation software like Moldflow lets designers test ideas virtually, slashing trial-and-error costs. Even sustainable materials—think bio-based plastics—are shaking things up, demanding new heat and flow tweaks.
I chatted with a product lead at an audio tech firm last month. They switched to a recycled polymer for earbud casings. Sounded great until flow issues caused sink marks. A bit of mold redesign and temp tuning, and they were back on track—greener and still profitable. For designers, this is your playground: innovate, but know the physics. Decision-makers, it’s your budget on the line—fund the tools to stay ahead.
Wrapping It Up: The Unsung Heroes of Your Next Product
Pressure, heat, and flow aren’t just technical buzzwords—they’re the heartbeat of injection molding. Master them, and you’ve got precision parts that fit like a glove, look sharp, and hold up under use. For electronics designers, it’s about turning your vision into reality without hiccups. For decision-makers, it’s the key to hitting deadlines, keeping costs down, and staying competitive.
Next time you hold a perfectly molded gadget, give a nod to the unseen forces that shaped it. Want to dig deeper? Chat with your molding team, run a simulation, or just marvel at how science and engineering collide to make the everyday extraordinary.
Sidebar: Quick Reference for the Pros
Pressure Ranges: 10,000–20,000 psi (injection), varies by part size/material.
Typical Temps: ABS (~450°F barrel, 150°F mold); PC (~550°F barrel, 200°F mold).
Flow Tip: Gate size matters—too small chokes flow, too big slows cooling.