The Role of Simulation Software in Injection Molding Design
Before a single mold is cut, you’ve already “seen” how the molten plastic will flow, where it might cool unevenly, and whether that tricky corner will hold up under stress—all on your computer screen. That’s the magic of simulation software in injection molding design.
2/24/20256 min read
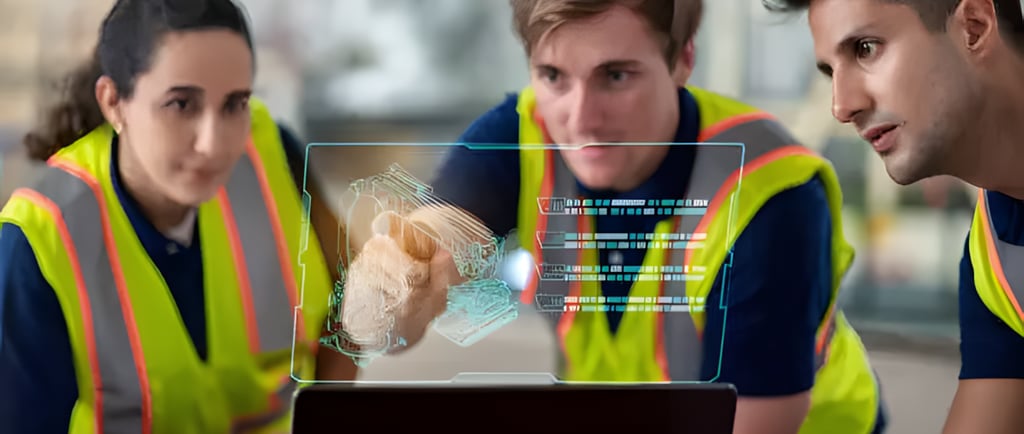
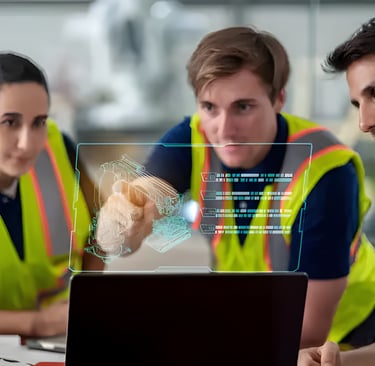
Imagine you’re tasked with designing a sleek, lightweight casing for the next big thing in consumer electronics—a smartwatch, perhaps, or a cutting-edge wireless earbud. The stakes are high: the part needs to be durable, precise down to the micrometer, and, of course, cost-effective to produce at scale. In the old days, you’d build a mold, run a few test shots, and cross your fingers that the plastic wouldn’t warp or leave unsightly sink marks. If it didn’t work, back to the drawing board—wasting time, money, and a little bit of your sanity.
Now, picture this: before a single mold is cut, you’ve already “seen” how the molten plastic will flow, where it might cool unevenly, and whether that tricky corner will hold up under stress—all on your computer screen. That’s the magic of simulation software in injection molding design. Tools like Autodesk Moldflow are transforming the way designers and decision-makers in electronics development approach manufacturing, bringing precision and confidence to a process that used to feel like a roll of the dice. Let’s dive into how this technology works, why it’s a game-changer for precision, and what it means for you and your team.
What is Simulation Software in Injection Molding?
Injection molding is the backbone of electronics manufacturing. From tiny connectors to full device housings, it’s how we turn raw plastic into the polished components that power our gadgets. But getting it right isn’t easy—molten plastic is finicky, molds are expensive, and deadlines are tight. Enter simulation software: a virtual sandbox where you can test your designs without touching a pellet of resin.
At its core, simulation software mimics the injection molding process. You input your part geometry, material choice, and mold setup, and the program calculates how the plastic will behave as it’s injected, cooled, and ejected. Think of it as a crystal ball for manufacturing. Tools like Moldflow—a favorite among engineers—take this a step further with advanced algorithms that predict everything from flow patterns to potential defects. For electronics designers, where tolerances are razor-thin and aesthetics matter as much as function, this is a lifeline.
I remember chatting with a colleague who’d spent years tweaking molds the old-fashioned way. “It was like playing whack-a-mole,” he said. “Fix one issue, and another pops up—warpage here, short shots there.” Simulation software flips that script, letting you see the whole picture before you commit.
Key Features of Tools Like Moldflow
So, what makes Moldflow and its ilk so powerful? It’s all about the details. These tools don’t just guess—they simulate the physics of injection molding with uncanny accuracy. Let’s break it down.
First, there’s material flow. In electronics, where parts often have intricate geometries—think of the delicate ribs inside a phone case or the thin walls of a battery compartment—knowing how plastic will fill every nook and cranny is critical. Moldflow maps this out, showing you where the material might hesitate or leave voids.
Then there’s cooling. Uneven cooling can spell disaster, especially for precision parts. Ever cracked open a cheap gadget and seen a warped plastic piece? That’s what happens when heat doesn’t dissipate properly. Simulation software analyzes temperature gradients across your design, helping you tweak cooling channels in the mold for uniformity.
Pressure and fill time are next. Too much pressure, and you risk flash (those annoying plastic whiskers); too little, and the mold won’t fill. Moldflow optimizes these variables, ensuring your part comes out clean and strong. And let’s not forget defect visualization—warpage, sink marks, air traps—the software flags these headaches early, so you’re not scrambling to fix them later.
For designers in electronics, this is gold. You’re not just designing a part; you’re designing how it’s made. Moldflow puts that control in your hands.
Benefits for Precision in Design
Precision isn’t a buzzword in electronics—it’s a necessity. A misaligned connector or a warped enclosure can tank a product launch. Simulation software delivers precision in ways traditional methods can’t touch. Here’s how.
First, it nails part design and mold creation. By simulating the process upfront, you can adjust wall thicknesses, gate locations (where the plastic enters the mold), and runner systems to hit your tolerances spot-on. I’ve seen teams shave days off their design cycles because they didn’t have to guess where to put the gate—they knew.
Second, it cuts down on physical prototyping. In the past, you’d build a mold, run a test, tweak it, and repeat—each iteration costing thousands and pushing deadlines. With simulation, you’re iterating digitally. One designer I know likened it to “getting 90% of the way there before the steel’s even cut.” That’s time and money back in your pocket.
Third, it optimizes material use. Electronics often demand high-performance plastics—think polycarbonates or ABS blends. Simulation lets you test how these materials behave under your specific conditions, so you’re not over-engineering (and overspending) or risking failure with something too brittle.
Finally, it catches flaws early. A sink mark on a visible surface? Warpage that misaligns a snap-fit? These aren’t surprises you discover in production—they’re problems you solve at your desk. For decision-makers, this means fewer late-stage headaches and happier customers.
I’ll never forget a story from a friend at a mid-sized electronics firm. They were designing a housing for a new IoT device, and the first physical run showed warpage that threw off the PCB alignment. Weeks of rework later, they adopted Moldflow. The next project? Spot-on from the first shot. That’s the kind of precision that keeps projects—and careers—on track.
Real-World Impact
The proof’s in the pudding, right? Companies across the electronics space are reaping the rewards of simulation software. Take a major player like Foxconn, a giant in contract manufacturing. They’ve leaned on tools like Moldflow to streamline production of everything from phone cases to laptop chassis, cutting lead times and boosting quality. Smaller firms, too—like a startup I consulted with last year—use it to punch above their weight, delivering flawless parts without a massive R&D budget.
The numbers back this up. Studies show simulation can slash production timelines by 20-30% and reduce material waste by double digits. That’s not just efficiency; it’s sustainability. In an industry under pressure to go green, minimizing scrap is a win for both the planet and the bottom line.
Then there’s cost. Yes, the software and training aren’t cheap upfront—I’ll get to that—but the savings pile up fast. Fewer mold revisions, less downtime, and happier clients mean ROI that’s hard to argue with. For decision-makers, that’s the kind of math that gets a green light in the boardroom.
Challenges and Considerations
Of course, it’s not all sunshine and perfectly molded parts. Simulation software has its hurdles, and being honest about them helps you make smarter choices.
For one, there’s a learning curve. Moldflow isn’t plug-and-play—it takes training to master the inputs and interpret the outputs. I’ve seen newbies get frustrated when their results don’t match reality, only to realize they’d skimped on material data or overlooked a variable. It’s a tool, not a miracle worker, and it rewards expertise.
Cost is another sticking point. Licensing fees can sting, especially for smaller teams, and you might need to upgrade your hardware to run it smoothly. But weigh that against the price of a failed mold ($10,000? $50,000?) and it starts looking like a bargain.
And here’s the kicker: simulation is only as good as your data. Garbage in, garbage out. If your material specs are off or your mold design’s incomplete, the software can’t save you. It’s a partner, not a replacement for solid engineering.
Still, these aren’t dealbreakers—they’re trade-offs. I’ve watched teams wrestle with the learning curve only to come out the other side faster and sharper. The key is commitment: invest in the skills, and the payoff follows.
Conclusion
Simulation software like Moldflow isn’t just a tool—it’s a revolution in how we design for injection molding. For electronics designers and decision-makers, it’s the difference between guessing and knowing, between scrambling and succeeding. It brings precision to your parts, speed to your timelines, and confidence to your decisions. In a field where margins are slim and expectations are sky-high, that’s invaluable.
The future’s only getting brighter. As these tools evolve—think AI-driven insights or real-time collaboration features—they’ll keep pushing the boundaries of what’s possible. But you don’t have to wait. Whether you’re a designer sketching the next must-have gadget or a leader steering your team through a product launch, simulation software is ready to help you nail it.
So, take a look. Kick the tires on Moldflow or its cousins. Talk to your team about what precision could mean for your next project. Because in electronics development, good enough doesn’t cut it—great does. And this is how you get there.