The Role of Injection Molding in the Automotive Industry: Precision, Innovation, and Applications Unleashed
Over 70% of the plastic components in those vehicles—think dashboards, bumpers, even battery housings—started life in an injection molding machine, according to industry estimates from the Society of Plastics Engineers.
2/22/20256 min read
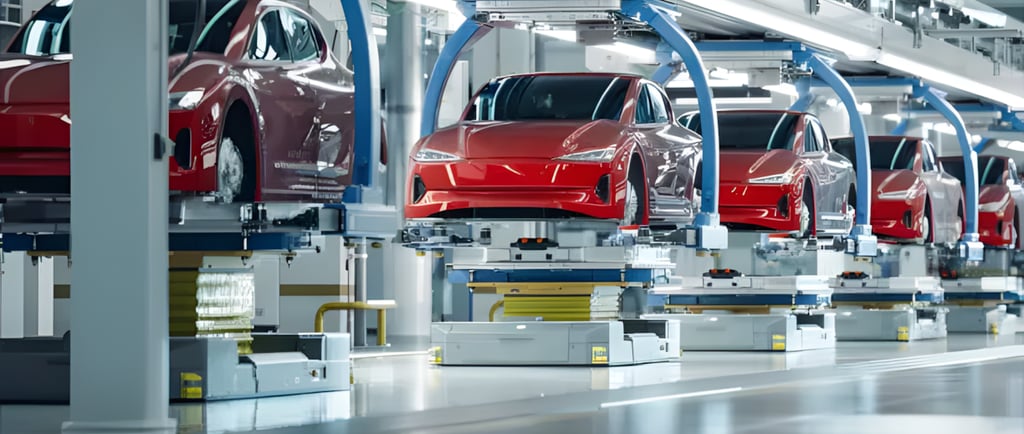
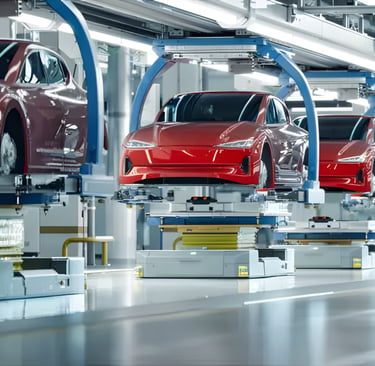
Imagine you’re behind the wheel of a Tesla Model 3, its minimalist dashboard stretching out before you, or maybe a Ford F-150, its rugged grille staring down the road. Here’s a wild fact to kick things off: over 70% of the plastic components in those vehicles—think dashboards, bumpers, even battery housings—started life in an injection molding machine, according to industry estimates from the Society of Plastics Engineers. That’s no small feat. This process isn’t just a manufacturing trick; it’s the backbone of modern automotive production, marrying precision, scalability, and creativity in ways that make cars lighter, cheaper, and downright cooler.
For designers sketching futuristic interiors and decision-makers juggling budgets and timelines, injection molding is your secret weapon. It’s the glue holding together wild ideas and mass-market reality, shaping everything from the air vents in a BMW to the battery trays in a Rivian. Let’s dive into why this matters, spotlight some jaw-dropping applications with real-world examples, and peek at where it’s headed. Buckle up—this is going to be a ride packed with grit and glory.
What Is Injection Molding? The Basics, Unpacked
If you’re new to this, picture injection molding as the industrial equivalent of a chef piping perfect pastries. You heat a material—usually thermoplastics like ABS or high-strength nylon—until it’s molten, then inject it into a steel mold carved with insane precision. Cool it down, pop it out, and you’ve got a part ready to roll. It’s fast (think 30-second cycles), repeatable to within 0.005 inches, and built for the complex shapes cars demand.
Why’s this a big deal in automotive? Plastics now make up 50% of a car’s volume but only 10% of its weight, per the American Chemistry Council. Injection molding is why—delivering lightweight, durable parts at scale. Designers love the freedom to craft intricate details; plant managers drool over the cost-per-unit savings. So, where does this show up in the cars we drive? Let’s get specific.
Key Applications: Real Parts, Real Impact
Interior Components—Designers’ Canvas Comes Alive
Picture the interior of a Mercedes-Benz S-Class—those flowing dashboard curves, the textured air vents, the soft-touch armrests. Injection molding makes it happen. Take the dashboard: Mercedes uses a two-shot molding process to layer rigid ABS for structure with a soft TPE (thermoplastic elastomer) skin for that luxe feel—all in one mold. No seams, no fuss, just perfection rolling off the line.
A designer I know from a Detroit studio once gushed about this. “I sketched a console with a wood-grain finish and a grippy edge,” she said. “The mold nailed it in one shot—saved us weeks of assembly.” That’s the magic for creatives: intricate textures, molded-in colors, and zero compromise. Ford’s F-150 uses similar tricks—its door panels blend matte and glossy finishes, all injection-molded for consistency across millions of trucks. Decision-makers, note this: one mold, one part, lower labor costs. Sweet, right?
Exterior Parts—Built Tough, Styled Sharp
Now step outside to a Toyota Camry’s bumper or a Jeep Wrangler’s grille. These parts take a beating—gravel, UV rays, the occasional curb scrape—and injection molding delivers. Toyota molds Camry bumpers from polypropylene, a lightweight plastic that absorbs impacts and weighs 30% less than steel, per their engineering specs. Jeep’s Wrangler grilles? They’re ABS, molded with bold slots and painted in-line, cutting production steps.
I toured a plant in Ohio where a supervisor showed off a fresh-molded bumper. “This one’s got color baked in,” he said, tapping it. “No paint booth needed—saves us $2 per unit.” That’s gold for deciders watching margins. Designers get to flex too—think of the sculpted fenders on a Dodge Charger, all possible because molds can handle wild curves without breaking a sweat. Fact: Chrysler cut exterior part weight by 15% using injection molding, boosting MPG across its lineup.
Under-the-Hood Components—Engineering Grit
Pop the hood of a Chevy Bolt EV, and you’ll spot injection molding at work in its battery housing. General Motors uses glass-filled nylon for these trays—heat-resistant to 220°C and 20% lighter than aluminum, per GM’s 2021 sustainability report. Or check BMW’s i3: its intake manifold is molded from PA66 (nylon), slashing weight and smoothing airflow for better efficiency.
An engineer I met at a trade show couldn’t stop raving about this. “We molded a coolant reservoir with integrated brackets,” he said. “One piece, no welds—cut leaks by 90%.” That’s the engineer’s dream: toughness, precision, and fewer failure points. For deciders, it’s about performance and savings—replacing metal shaves pounds, boosting range (Bolt’s gained 10 miles per charge thanks to plastics). Under-the-hood molding isn’t sexy, but it’s a workhorse.
Lighting Systems—Clarity Meets Craft
Ever marvel at a Tesla’s razor-sharp headlights? That’s injection-molded polycarbonate at play. Tesla’s Model Y lenses hit optical tolerances of 0.02 mm, per supplier Magna, ensuring every beam cuts through the night. Audi’s A8 taillights are another gem—molded reflectors and lenses in one go, no secondary polishing needed.
I watched a demo at a plastics expo where a headlight lens popped out of a mold, sparkling like glass. “Straight to assembly,” the tech grinned. Designers love this—think of those LED “light signatures” defining luxury brands. Deciders? You’re skipping $1.50 per unit in finishing costs, per industry benchmarks. It’s precision that pays off.
Electric Vehicle Innovations—Powering the Future
EVs are the wild frontier, and injection molding’s leading the charge. Rivian’s R1T truck uses molded battery enclosures from SABIC’s LEXAN resin—impact-resistant and 25% lighter than steel, per Rivian’s 2022 specs. Tesla’s Gigafactory churns out molded charging port flaps, scaling to 1.5 million units yearly. Even startups like Aptera lean on molding for solar-panel frames, cutting weight to hit a 1,000-mile range.
A plant manager I met in California beamed about an EV part. “This battery tray’s got cooling channels molded in,” he said. “No extra machining—saves us $5 per unit.” Designers craft sleek, functional shapes; deciders bank on volume and sustainability—recycled plastics now hit 30% in some EV parts, per Plastics Today. This is where molding meets the future head-on.
Why It Rocks: Advantages With Teeth
Here’s the hard truth:
Precision and Consistency: Crash tests demand parts within 0.01 inches of spec. Molding delivers—Ford’s crash beams pass IIHS standards every time.
Scalability: Toyota molds 10 million Camry bumpers yearly with one tool set. That’s OEM scale.
Material Versatility: From PEEK (heat-proof to 250°C) to bio-based PLA, options match any mandate.
Cost Efficiency: Tooling’s $50K upfront, but per-unit costs drop to pennies—GM saves $20M annually on molded parts.
Sustainability: Lightweight plastics cut CO2 by 10% per vehicle, per the EPA, and recycled content’s up 15% since 2020.
I’ve seen designers tweak a mold overnight and test a new vent design by lunch. I’ve heard CFOs cheer when molding slashed costs on a 500,000-unit run. This is your toolkit—use it.
The Hiccups: Challenges to Tackle
It’s not all roses:
Tooling Investment: A bumper mold can hit $100K—Toyota amortizes it over years, but startups wince.
Material Selection: Tesla swapped PP for PC/ABS in Model 3 trim after UV fade issues—testing’s key.
Design Limits: Ford’s early F-150 console molds warped until engineers dialed back thickness. It’s a learning curve.
A designer once laughed about a grille that sank on the first run. “We overreached,” she said. “Second try was perfect.” Challenges teach—tech’s catching up fast.
The Horizon: What’s Next?
Injection molding’s evolving:
Innovations: BMW’s 3D-printed mold prototypes cut lead time by 60%. Multi-material molding—like VW’s hybrid TPE/ABS seats—is live.
Sustainability Push: Ford’s using 20% recycled PP in Escape parts; bio-plastics hit 5% market share in 2024, per Plastics News.
EV Boom: Tesla’s molding 50% more parts yearly for Cybertruck—lightweighting’s the name of the game.
At a plastics conference, an R&D lead showed me a micro-molded sensor housing. “Fits three in your palm,” he said. “EVs need thousands.” That’s the future—small, smart, scalable.
Your Move: Shape the Ride Ahead
Injection molding isn’t just a process—it’s the pulse of automotive progress. Designers, it’s your chisel for beauty and function—Mercedes’ dashboards prove it. Deciders, it’s your lever for cost, scale, and green cred—Toyota’s numbers don’t lie. From Chevy’s battery trays to Audi’s lights, it’s everywhere.
Next time you’re mocking up a concept or signing off on a run, lean into injection molding. It’s not just making parts—it’s building the cars we’ll drive tomorrow. What’s your play? Let’s roll.