The Future of Manufacturing Careers: Challenges, Opportunities, and Strategies for Workforce Growth
The manufacturing industry has always been a backbone of economic growth, providing stable jobs and driving innovation. However, as technology evolves and workforce expectations shift, manufacturers face new challenges in attracting and retaining skilled workers.
3/17/20254 min read
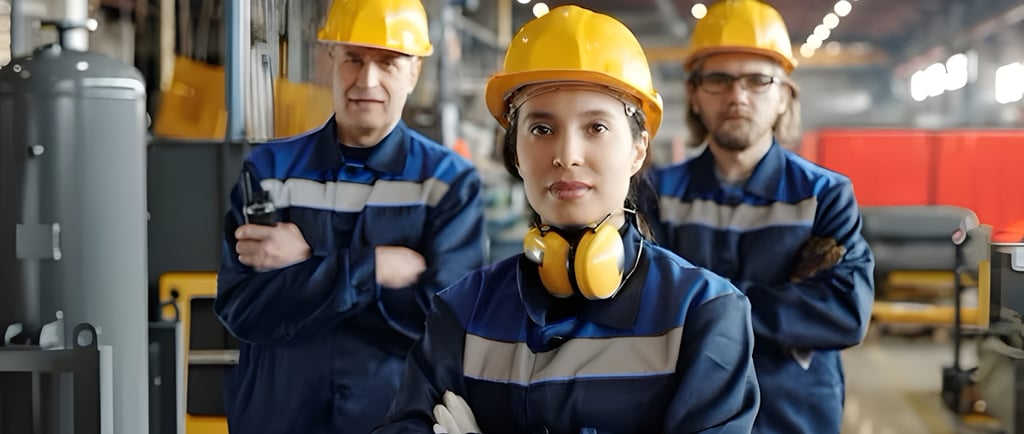
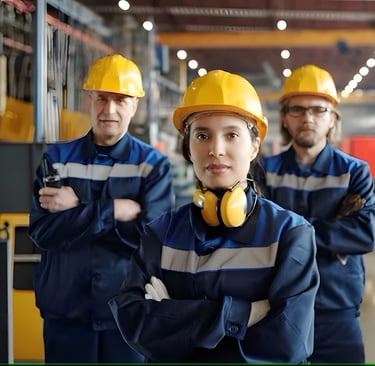
The manufacturing industry has always been a backbone of economic growth, providing stable jobs and driving innovation. However, as technology evolves and workforce expectations shift, manufacturers face new challenges in attracting and retaining skilled workers. Despite these hurdles, there are exciting opportunities ahead for both employers and employees in the industry.
The Current State of Manufacturing Careers
According to a recent survey on career advancement in manufacturing, the industry is seen in a positive light, with 80% of respondents recommending it as a career choice. Interestingly, more women are recognizing progress in the field, with 78% acknowledging significant improvements for women in manufacturing over the last five years.
That said, there’s still a major issue with labor shortages. Nearly 79% of manufacturers report struggling to find and retain workers. What’s even more telling is that many people in the industry never planned on entering manufacturing—74% of women and 49% of men say they “fell into” their careers.
This shows that manufacturers need to do a better job of attracting young talent and making manufacturing careers more intentional rather than accidental. Additionally, 87% of women and 56% of men agree that diversity in the workplace leads to better business outcomes, meaning that inclusive hiring and development strategies can play a key role in shaping the future workforce.
Major Challenges Facing Manufacturers
1. Automation and AI Integration
While automation increases efficiency, it also raises concerns about job displacement. Some factories, particularly in China, are exploring fully automated “dark factories” that require no human workers. However, rather than eliminating jobs, automation often shifts the types of roles needed, creating demand for skilled workers who can operate and maintain advanced machinery.
2. Skilled Labor Shortages
Even as technology advances, manufacturers still need skilled workers to operate, troubleshoot, and optimize production lines. The demand for experienced workers remains high, yet many factories struggle to fill critical roles.
3. Perception Problems
The outdated stereotype that manufacturing jobs are low-skill, low-tech, and physically demanding still lingers. In reality, modern manufacturing involves cutting-edge technology, automation, and problem-solving—elements that could attract younger generations if presented correctly.
4. Economic Uncertainty
Fluctuations in global trade, rising material costs, and shifting tax policies can all impact job stability in the manufacturing sector. To stay competitive, businesses must remain adaptable and forward-thinking.
Opportunities for Growth in the Industry
Despite these challenges, manufacturers have plenty of opportunities to create a strong, resilient workforce:
1. Embracing Technological Advancements
Rather than fearing automation, manufacturers can use it to their advantage by training employees in high-tech skills. This not only improves efficiency but also creates career growth opportunities in areas like robotics, AI-driven production, and data analysis.
2. Investing in Workforce Development
Apprenticeships and training programs, such as those run by the FAME USA initiative, are equipping workers with hands-on experience and relevant technical knowledge. Companies that invest in employee growth see higher retention rates and a more skilled workforce.
3. Promoting Diversity and Inclusion
A diverse workforce brings fresh perspectives and innovative problem-solving skills. Programs that support women, minorities, and underrepresented groups in manufacturing can help close the talent gap and create a more dynamic industry.
4. Improving the Industry’s Image
Manufacturers must actively work on changing outdated perceptions by showcasing modern facilities, high-tech machinery, and the meaningful career paths available in the industry. Engaging with schools, universities, and online platforms can help attract new talent.
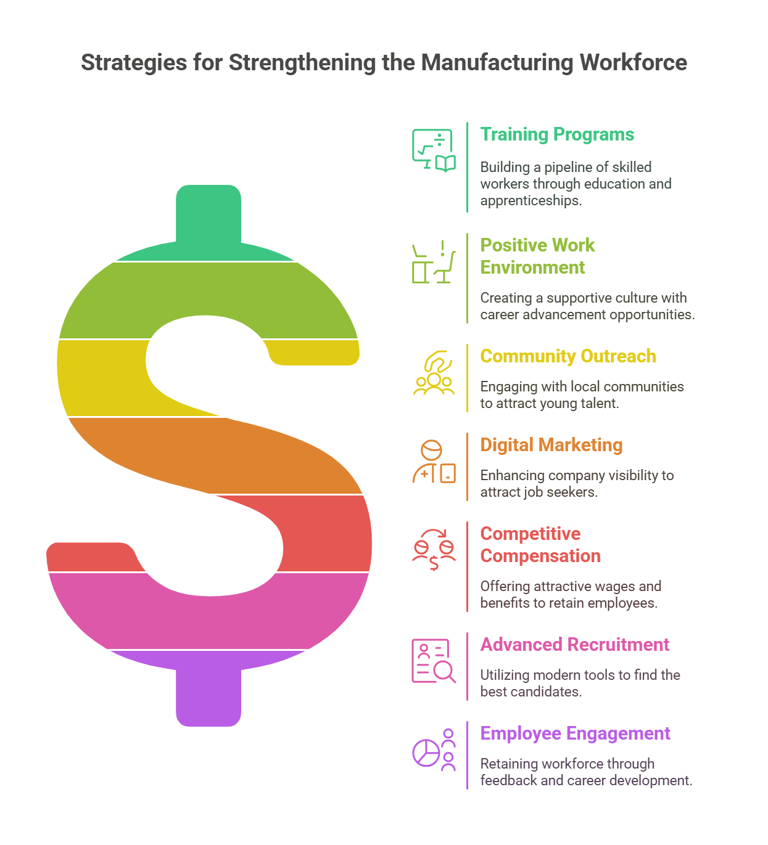
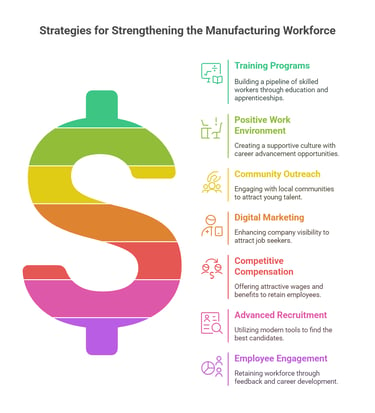
Practical Strategies for Manufacturers
If you’re a manufacturer looking to strengthen your workforce, here are some actionable steps:
Develop Strong Training Programs – Partner with technical schools and offer on-the-job training programs to build a pipeline of skilled workers. Hands-on apprenticeships, vocational training, and industry certifications can help new hires adapt to the complexities of modern manufacturing.
Foster a Positive Work Environment – Employees are more likely to stay in a company that values their contributions and offers clear career advancement opportunities. Implement mentorship programs, provide regular performance feedback, and ensure that workers have access to leadership training. Encouraging a culture of innovation and problem-solving can also boost job satisfaction.
Engage in Community Outreach – Many young people are unaware of the diverse career options available in manufacturing. Companies can bridge this gap by collaborating with high schools, colleges, and community organizations to showcase career pathways. Hosting facility tours, offering summer internships, and participating in job fairs can help attract fresh talent to the industry.
Leverage Digital Marketing – Use social media, job boards, and content marketing to enhance your company’s visibility. Sharing behind-the-scenes videos of production lines, employee success stories, and thought leadership articles can help shape a modern and attractive image of manufacturing careers. Consider launching a company blog or YouTube channel to engage with potential job seekers and demonstrate what sets your company apart.
Offer Competitive Compensation and Benefits – Manufacturing roles must compete with other industries when it comes to wages, benefits, and work-life balance. Providing health insurance, retirement plans, paid time off, and flexible work arrangements can make a significant difference in attracting and retaining employees. Additionally, performance-based incentives, tuition reimbursement programs, and career development grants can encourage employees to stay long-term and grow within the company.
Adopt Advanced Recruitment Strategies – Traditional hiring methods may not be enough to fill the talent gap. Utilize AI-driven recruitment tools, employee referral programs, and data-driven hiring strategies to identify the best candidates. Expanding recruitment efforts beyond local job boards to include global talent pools can also help manufacturers find specialized skills that are in high demand.
Encourage Employee Engagement and Retention – Workforce retention is just as important as hiring. Regularly seek employee feedback through surveys and open forums to address concerns and improve job satisfaction. Offering cross-training opportunities can also keep employees engaged by allowing them to learn different roles within the company and advance their careers
Conclusion
The future of manufacturing careers is bright for those willing to adapt and innovate. While labor shortages and automation challenges persist, forward-thinking manufacturers can overcome these obstacles by investing in workforce development, promoting diversity, and modernizing the industry’s image. By taking these steps, manufacturers can ensure they attract top talent and remain competitive in an ever-changing landscape.