The Future of Injection Molding: Trends to Watch in 2025 and Beyond
Injection molding, the unsung hero of electronics manufacturing. For decades, it’s been the go-to for churning out precision parts, from phone casings to tiny connectors. But here’s the kicker: the game’s changing fast, and if you’re a designer or decision-maker in electronics development, you’ll want to keep your eyes peeled for what’s coming in 2025 and beyond.
2/23/20256 min read
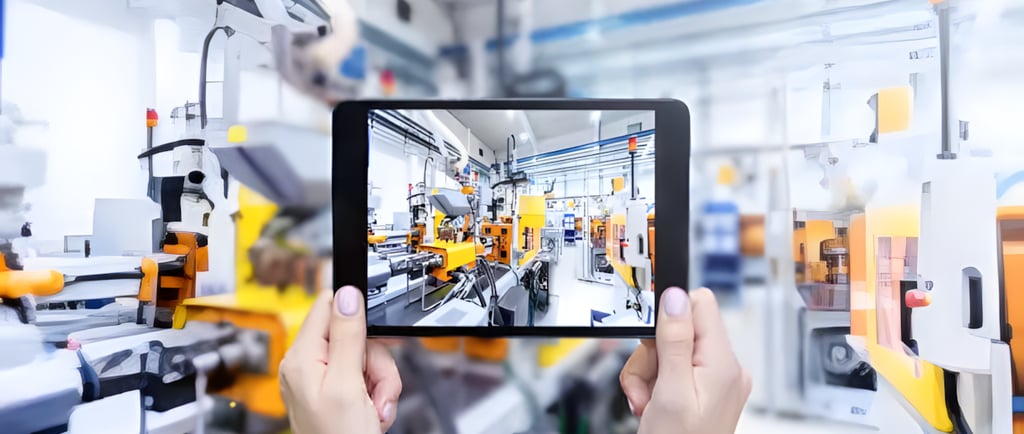
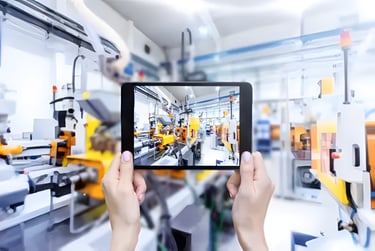
Picture this: you’re sipping your morning coffee, flipping through the latest specs for a sleek new wearable device your team’s been dreaming up. It’s got to be lightweight, durable, and—oh yeah—produced at scale without breaking the bank. Behind that vision? Injection molding, the unsung hero of electronics manufacturing. For decades, it’s been the go-to for churning out precision parts, from phone casings to tiny connectors. But here’s the kicker: the game’s changing fast, and if you’re a designer or decision-maker in electronics development, you’ll want to keep your eyes peeled for what’s coming in 2025 and beyond.
Injection molding isn’t just about melting plastic and hoping for the best anymore—it’s evolving into something smarter, greener, and downright futuristic. Whether you’re sketching the next big thing or signing off on production budgets, these trends will shape how your ideas come to life. Let’s break it down, starting with the buzzword that’s got everyone talking: automation.
The Rise of Automation in Injection Molding
If you’ve ever toured a factory floor, you know the hum of machines and the dance of workers grabbing parts off the line. But by 2025, that scene’s going to look more like a sci-fi movie. Robotics and AI-driven automation are charging in, and they’re not just here to assist—they’re taking the lead. Imagine a setup where robotic arms pluck finished parts with pinpoint accuracy, while AI scans every piece for defects faster than you can blink. That’s not a pipe dream; it’s where we’re headed.
For electronics, this is huge. Think about those tiny, intricate components—like the housing for a smartwatch sensor or the connectors in a circuit board. Precision is everything, and automation delivers. Plus, it slashes labor costs and speeds up production cycles, which means your team can get prototypes to market before the competition’s even laced up their shoes. I spoke to a friend who manages a plant in Ohio, and he’s already seeing 20% faster turnaround times with automated quality checks. By 2025, this could be the norm.
Looking further out, picture fully autonomous factories by 2030. Your design files get uploaded, and the system handles everything—molding, assembly, even packaging—while you focus on dreaming up the next innovation. It’s not just efficiency; it’s a whole new way to think about production.
Smart Molds and IoT Connectivity
Now, let’s talk about something that sounds like it’s straight out of a Tony Stark workshop: smart molds. By 2025, these bad boys will be everywhere, packed with sensors that track temperature, pressure, and cycle times in real time. Why does this matter for electronics? Because consistency is king. A tiny flaw in a molded part—like a hairline crack in a phone case—could mean a failed product launch. Smart molds nip that in the bud by catching issues before they spiral.
Here’s how it works: these molds talk to the machines (and to you) via IoT—yep, the Internet of Things. Say you’re designing a new drone controller. The mold’s sensors flag a pressure spike mid-cycle, tweak the settings on the fly, and save you from scrapping a whole batch. Less downtime, better parts, happier customers. My cousin, an engineer in the Bay Area, swears by this tech already—he says it’s like having a co-worker who never sleeps.
Beyond 2025, we might see self-adjusting molds powered by AI analytics. Imagine a mold that learns from every run, fine-tuning itself to perfection. For electronics designers, that means pushing the limits of complexity—thinner walls, tighter tolerances—without sweating the manufacturing risks.
Sustainability Driving Innovation
Let’s get real: sustainability isn’t just a buzzword—it’s a mandate. Your customers care, regulators care, and if you’re honest, you probably do too. By 2025, injection molding’s going green in a big way, and for electronics, that’s a golden opportunity. Think biodegradable plastics for disposable wearables or recycled resins for speaker housings. These aren’t hippie fantasies—they’re hitting the market now, and they’re only getting better.
The push comes from everywhere. Governments are tightening emissions rules, and consumers are ditching brands that don’t walk the eco-talk. For decision-makers, it’s a chance to future-proof your supply chain. Energy-efficient machines are already cutting power use by 30% in some plants—I saw one in action last year, and the hum was quieter than my old Prius. Pair that with sustainable materials, and you’ve got a win-win: lower costs and a shiny “green” badge for your brand.
Looking ahead, zero-waste molding facilities by the 2030s aren’t out of reach. Imagine every scrap of plastic looped back into production, leaving nothing for the landfill. For electronics, where margins are tight and optics matter, that’s a game-changer.
Advances in Material Science
Materials are the heart of any design, and injection molding’s about to get a serious upgrade. By 2025, expect a flood of high-performance polymers tailored for electronics—lightweight composites for drone frames, heat-resistant plastics for battery casings, you name it. These aren’t just tweaks; they’re breakthroughs that let you shrink parts, boost durability, and tackle tougher specs.
Take medical devices, a cousin to electronics in precision demands. A buddy of mine designs insulin pumps, and he’s buzzing about a new polymer that’s tougher than steel but feather-light. For your next project—say, a foldable tablet—materials like that could mean thinner profiles without sacrificing strength. And the best part? They play nice with injection molding, so scaling up won’t break the bank.
Down the road, pair these materials with 3D-printed molds by 2027, and you’ve got a recipe for custom parts on demand. Designers, this is your playground—start sketching those wild ideas now.
3D Printing and Hybrid Manufacturing
Speaking of 3D printing, it’s not just for prototypes anymore—it’s teaming up with injection molding in a big way. By 2025, hybrid systems will blend the best of both worlds: the flexibility of 3D printing for quick molds and the speed of injection for mass production. For electronics, this is a lifeline. Need a small batch of custom earbud cases to test a new design? Hybrid tech’s got you covered without the hefty tooling costs.
I saw this in action at a trade show last fall—a startup cranked out 500 unique parts in a day, no sweat. For designers, it’s a dream: iterate fast, test in the real world, then scale up seamlessly. Decision-makers, take note: this cuts lead times and keeps budgets in check, especially for niche products like VR accessories or IoT gadgets.
By the late 2020s, hybrid machines could be standard in mid-sized shops. That means your team can pivot from concept to market faster than ever—perfect for staying ahead in the cutthroat electronics game.
Workforce Transformation and Digital Skills
Here’s where it gets personal: the people behind the machines. By 2025, the injection molding workforce is going to look different—not smaller, but smarter. The days of manual tweaks and clipboard checklists are fading. Instead, you’ll need operators who can wrangle IoT dashboards, troubleshoot AI glitches, and interpret data like pros.
For electronics firms, this shift is critical. Your production line’s only as good as the team running it, and as automation and smart tech take over, those roles evolve. I chatted with a plant manager in Texas who’s already training his crew on digital tools—think less “turn the knob” and more “read the analytics.” It’s not about replacing people; it’s about upskilling them to keep pace.
Looking to 2030, expect a leaner, tech-savvy workforce. Designers, you’ll collaborate with these folks more than ever, feeding them specs that lean on automation and smart molds. Decision-makers, budget for training now—it’s an investment that’ll pay off when your competitors are still playing catch-up.
Conclusion
So, where does this leave us? Injection molding’s future is bright—and for electronics designers and decision-makers, it’s a goldmine of opportunity. Automation’s speeding things up, smart molds are nailing precision, and sustainability’s keeping you in the green (literally and figuratively). New materials and hybrid tech are opening doors to wild designs, while a sharper workforce ties it all together.
The takeaway? Start planning now. Invest in these trends, tweak your workflows, and get your team ready—because by 2030, injection molding won’t just be smarter and greener; it’ll redefine how electronics hit the shelves. Your next big idea deserves nothing less.