The Future Landscape of Metal Fabrication in Electronics: A Glimpse into Tomorrow
Metal fabrication has always been the unsung hero of electronics—think enclosures that shield delicate circuits, connectors that keep signals flowing, or heat sinks that stop your latest prototype from turning into a meltdown metaphor.
2/26/20256 min read
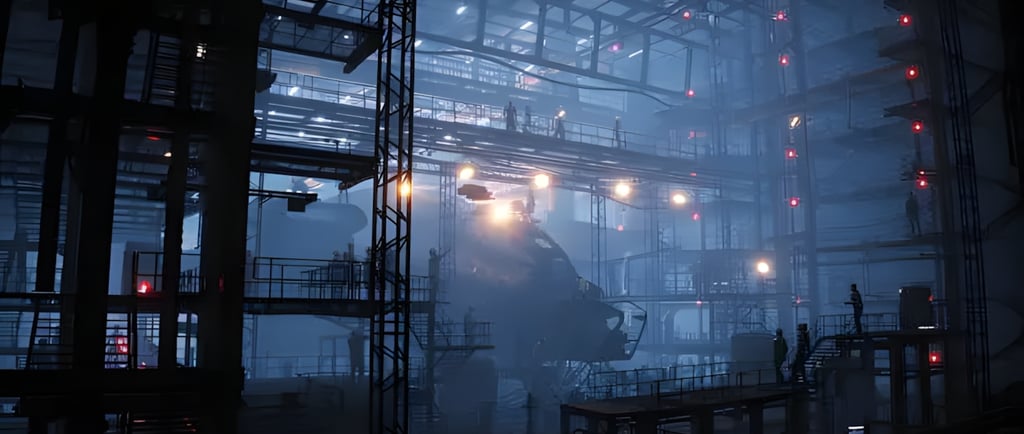
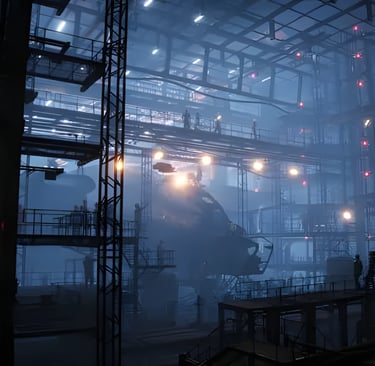
Picture this: you’re holding the next big thing in electronics—a device so sleek it feels like it’s from a sci-fi movie, with components that don’t just endure but adapt to the chaos of daily use. Now imagine that the secret sauce behind it isn’t some exotic chip, but the metal itself—crafted with materials and methods we’re only beginning to dream up. That’s where metal fabrication in electronics is headed, and if you’re a designer or decision-maker in this space, you’re standing at the edge of a revolution.
Metal fabrication has always been the unsung hero of electronics—think enclosures that shield delicate circuits, connectors that keep signals flowing, or heat sinks that stop your latest prototype from turning into a meltdown metaphor. But the game’s changing fast. New materials, cutting-edge tech, and bold process tweaks are poised to redefine how we shape metal for the gadgets of tomorrow. Let’s dive into what’s coming—because whether you’re sketching the next wearable or greenlighting a production run, this future’s got your name on it.
Next-Gen Metals and Alloys: The Building Blocks of Tomorrow
Let’s start with the raw stuff: the metals we bend, cut, and weld into shape. Today, it’s all about aluminum for lightweight casings, copper for conductivity, and stainless steel for durability. Solid choices, right? But what if I told you the metals of the future might do more than just sit there looking pretty?
Imagine self-healing alloys. Yeah, you heard that right—metals that patch themselves up like a scraped knee. Researchers are already tinkering with alloys that can recrystallize under heat or stress, sealing tiny cracks before they become big problems. For electronics, that could mean connectors that don’t wear out after a thousand plug-ins or heat sinks that stay flawless under thermal strain. Less downtime, fewer replacements—your reliability engineers will thank you.
Then there’s the lightweight dream. Picture superalloys—think titanium kissed with graphene—that are stronger than steel but light enough to make your next wearable feel like a feather. Designers, this is your chance to slim down devices without sacrificing toughness. Decision-makers, it’s a cost-benefit puzzle: these materials might sting the budget upfront, but the payoff in performance and customer wow-factor could be huge.
And don’t sleep on conductive nanomaterials. Mixing metals with carbon-based structures like nanotubes could give us circuits that pack more punch in less space. Miniaturization’s been the name of the game forever, but this could take it to a new level—think denser, faster chips that don’t overheat. It’s the kind of edge that turns a good product into a market leader.
The catch? These materials aren’t cheap or easy to mass-produce yet. But as a designer, you can start experimenting now—prototype with them, feel their potential. As a decider, keep an eye on the R&D pipeline. The day these hit scale, they’ll redefine what’s possible.
Tools of Tomorrow: Tech That’ll Make You Rethink Fabrication
Now, let’s talk tools. If you’ve been in the trenches of electronics design, you know the drill: laser cutters slicing with surgical precision, CNC machines churning out parts like clockwork, and 3D printers spitting out metal prototypes. It’s a solid toolkit. But the future? It’s like upgrading from a flip phone to a smartphone—same job, whole new game.
First up, AI-driven precision. Imagine an AI that doesn’t just follow your CAD file but tweaks it on the fly—shaving a micron here, reinforcing a stress point there. It’s like having a master craftsman who never sleeps, optimizing every cut for strength, efficiency, and zero waste. For designers, this means less trial-and-error; for decision-makers, it’s a leaner production line that keeps costs in check.
Then there’s the wild card: atomic-level fabrication. Think of it as sculpting metal one atom at a time. Tools like molecular assemblers—still sci-fi for now—could build components with zero defects, perfect crystal structures, and insane precision. Your next circuit board might not just be smaller; it could be flawless, boosting performance in ways we can barely measure today. It’s a long shot, sure, but if it lands, it’s a game-changer.
And let’s not forget 3D printing. Metal printers are already cool, but picture this: a printer that layers multiple metals in one go—say, a copper core for conductivity wrapped in a titanium shell for strength. One machine, one pass, done. Designers, you could dream up parts that fuse form and function like never before. Deciders, you’d cut production steps, slashing time-to-market. It’s not here yet, but the tech’s inching closer every year.
The upside? Faster, smarter fabrication that keeps you ahead of the curve. The downside? These tools need big investments—both in cash and training. Start small, though—test an AI plugin or a next-gen printer on a pilot project. The future favors the bold.
Rethinking How Metal Meets Circuitry: Process Innovation
Materials and tech are only half the story. The way we put it all together—the processes—might be where the real magic happens. Today, we’re stamping casings, welding joints, and etching traces like it’s 1999. It works, but it’s not exactly screaming “future.” Let’s dream bigger.
How about sustainable fabrication? Imagine a factory where every scrap of metal gets melted down and reused on the spot—no landfill, no waste. Closed-loop systems could turn your offcuts into tomorrow’s enclosures, shrinking your environmental footprint and your material costs. Designers, you’d have more room to experiment without guilt; deciders, you’d have a green credential to flaunt to eco-conscious customers.
Then there’s hybrid manufacturing. Picture this: a machine that 3D-prints a rough metal shape, then switches to CNC mode to polish it to perfection—all in one workflow. It’s like baking and decorating a cake in the same oven. You’d get the speed of additive manufacturing and the precision of subtractive, opening doors to complex parts that’d be a nightmare to make otherwise. Think integrated heat pipes or multi-metal connectors—stuff that makes your product stand out.
And let’s get wild with smart assembly. Imagine robotic arms with sensors that “feel” the metal as they work, adjusting pressure or speed based on humidity, temperature, whatever. It’s like a chef tweaking a recipe mid-cook because the kitchen’s too hot. This could mean fewer defects, tighter tolerances, and even custom runs that adapt to each batch’s quirks. Designers, you’d have flexibility to push boundaries; deciders, you’d have consistency without babysitting the line.
The payoff’s clear: efficiency, sustainability, customization. But scaling these ideas takes guts—and cash. Start with a proof-of-concept. A sustainable scrap system or a hybrid prototype could show you the ROI before you bet the farm.
Navigating the Road Ahead: Challenges and Solutions
Okay, let’s get real for a sec. This future sounds amazing, but it’s not all smooth sailing. New materials like self-healing alloys or nanomaterials? They’re pricey, and we don’t fully know how they’ll behave at scale—or if regulators will freak out over, say, nanoparticle risks. Cutting-edge tools like atomic assemblers? They’re years away from your shop floor, and even AI upgrades need serious upfront investment. Processes like closed-loop fabrication? Great in theory, but retrofitting a factory ain’t cheap.
So, what do you do? As a designer, don’t wait—play with what’s available now. Test a graphene composite, mock up an AI-optimized part. Get a feel for where this is going. As a decision-maker, think partnerships—team up with universities or tech startups to split the R&D load. Push for industry standards on new materials to ease regulatory headaches. And start small—pilot a sustainable process or a hybrid machine. Prove it works, then scale it.
The stakes are high, but so’s the reward. Nail this, and you’re not just keeping up—you’re setting the pace.
The Big Picture: Where We’re Headed
So, where does this leave us? Metal fabrication in electronics is about to leap from reliable workhorse to innovative powerhouse. Materials that heal and conduct like champs, tools that think and build with atomic finesse, processes that waste nothing and adapt on the fly—it’s a trifecta that could make your next device lighter, smarter, and greener than ever.
Designers, this is your playground. Dream up parts that push limits, knowing the tools and materials are catching up. Decision-makers, this is your chessboard. Move early, invest wisely, and you’ll own the board when the future lands. Either way, stay curious—watch the trends, talk to your teams, maybe even drop a comment below with your take. Because the next big thing in electronics? It’s going to start with the metal.