The Electronics Manufacturing Process Unveiled: A Designer’s Guide from Concept to Consumer
From smartphones buzzing in pockets to smart TVs lighting up living rooms, electronics are the heartbeat of modern life. For designers and decision-makers like you, understanding the manufacturing process isn’t just trivia—it’s the backbone of bringing your vision to reality.
2/27/20254 min read
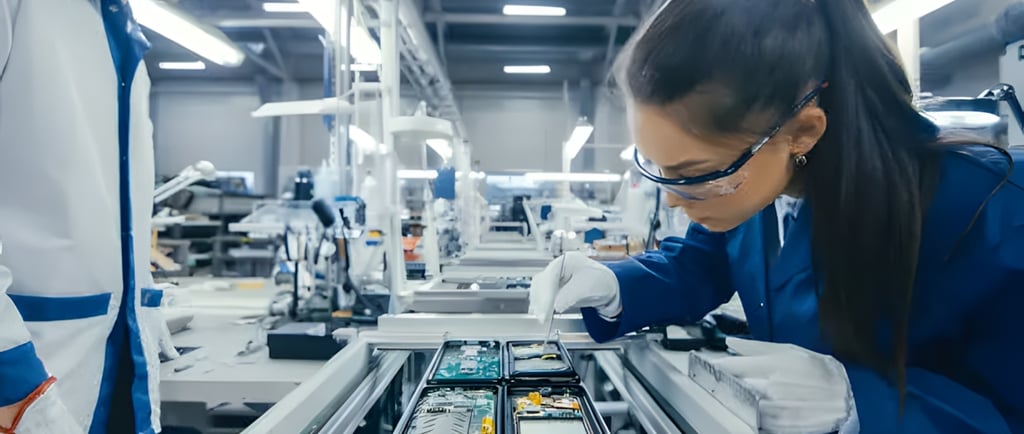
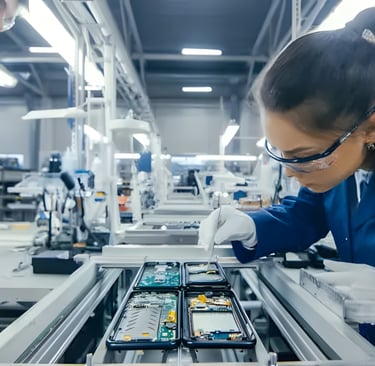
It’s late at night, and I’m tapping away on my laptop, marveling at how this sleek machine connects me to the world. Ever wonder how it—or any electronic device—comes to life? From smartphones buzzing in pockets to smart TVs lighting up living rooms, electronics are the heartbeat of modern life. For designers and decision-makers like you, understanding the manufacturing process isn’t just trivia—it’s the backbone of bringing your vision to reality. In this deep dive, I’ll walk you through the journey from a spark of an idea to a finished product in a consumer’s hands, tailored to those shaping the future of tech. Buckle up—this is where creativity meets precision.
1. Conceptualization and Design: Where It All Begins
Picture this: you’re sitting in a brainstorming session, coffee in hand, sketching out the next big thing. This is the conceptualization phase, where ideas take root. As a designer, you’re dreaming up features—maybe a slimmer profile or a longer battery life—while decision-makers weigh market trends and feasibility. It’s a dance of imagination and pragmatism.
Once the idea solidifies, it’s time to get technical. Engineers draft schematics, mapping out circuits like a city planner designs roads. Tools like CAD (Computer-Aided Design) software and circuit simulators become your best friends, letting you visualize every resistor and capacitor. I’ve seen teams spend weeks tweaking designs, ensuring the layout not only works but sings. For you, this stage is about marrying aesthetics with functionality—because a beautiful device that fails isn’t worth the solder it’s built on.
2. Prototyping: Testing the Dream
Now, let’s get our hands dirty. Prototyping is where your concept steps out of the screen and into the real world. It’s like baking a test cake before the big party—you want to know it’ll rise. Designers often start with breadboards, those cluttered little boards where wires and components tangle like a chaotic first draft. Others might 3D-print a casing to see how it feels in hand.
I remember a friend, an engineer, showing me his first smartwatch prototype. It was clunky, with wires spilling out, but it worked—and that thrill fueled the next iteration. This phase is iterative: build, test, tweak, repeat. Decision-makers, you’re watching timelines and budgets here, deciding when “good enough” becomes “ready.” It’s messy, exhilarating, and absolutely critical.
3. Component Sourcing: Gathering the Building Blocks
Think of components as the ingredients in your tech recipe. Resistors, capacitors, microchips—they’re tiny but mighty. Sourcing them sounds simple, right? It’s not. Designers, you specify what you need, but decision-makers wrestle with the logistics: Where do we get high-quality parts? Can we trust this supplier? Will tariffs jack up costs?
I once chatted with a supply chain manager who likened it to hunting for treasure—except the treasure might be delayed at a port in Shanghai. Sustainability’s a hot topic too; companies are under pressure to use ethically sourced materials. For you, this stage is a reminder that your design’s brilliance rests on a foundation of reliable parts.
4. Printed Circuit Board (PCB) Production: The Heart of the Machine
Here’s where the magic happens. The PCB—Printed Circuit Board—is the skeleton that holds your device together. Designers, you’ve already laid out the blueprint, deciding where each component sits. Now, manufacturers bring it to life.
The process feels like artistry meets science. First, they etch copper onto a board, creating pathways for electricity. Then, they drill tiny holes for components, layering materials with microscopic precision. I’ve toured a PCB factory, and the hum of machines paired with technicians’ focus was mesmerizing. For decision-makers, this is a cost-heavy step—automation cuts labor but demands investment. Get it right, and your device has a rock-solid core.
5. Assembly Process: Piecing It Together
With the PCB ready, it’s assembly time. Imagine a high-tech kitchen: robotic arms whirring, placing components like a chef plating a dish. There are two main methods here—Surface-Mount Technology (SMT) and through-hole assembly. SMT is fast and compact, perfect for sleek gadgets. Through-hole is sturdier, often used in industrial gear.
Soldering locks everything in place, a process that’s evolved from hand-held irons to wave-soldering machines. I once watched a line of SMT machines in action, their speed dizzying yet precise. Designers, you’re ensuring your layout translates here; decision-makers, you’re eyeing efficiency. One misstep, and the whole batch could falter.
6. Testing and Quality Assurance: Making It Foolproof
You’ve built it—now prove it works. Testing is the gatekeeper between factory and consumer. Automated Optical Inspection (AOI) scans for misplaced parts, while In-Circuit Testing (ICT) checks electrical connections. Functional testing simulates real-world use—think pressing buttons or charging ports.
A colleague once told me about a batch of speakers that failed because a single capacitor was off-spec. Hours of rework followed. For designers, this is where your specs are validated; for decision-makers, it’s about risk. Standards like ISO or FCC loom large—fail them, and you’re back to square one. It’s tense, but it’s what separates a product from a paperweight.
7. Packaging and Final Assembly: Dressing It Up
The PCB’s humming, tests are green—time to make it pretty. Final assembly integrates the board into its housing. Screens snap into place, buttons align, and casings click shut. Branding gets added—logos etched or printed with pride.
I’ve held a freshly assembled device, its weight a testament to every step before. Packaging comes next: boxes designed to protect and entice. Designers, you’re ensuring the look matches the function; decision-makers, you’re streamlining for shipping. It’s the last lap before the consumer takes over.
8. Distribution and Market Delivery: Into the Wild
The finish line’s in sight. Distribution moves your creation from factory floors to store shelves—or straight to doorsteps, thanks to e-commerce. Global supply chains kick into gear, navigating customs, carriers, and costs.
I recall a logistics expert explaining how a single storm could delay a shipment by weeks—nerve-wracking for decision-makers watching deadlines. Designers, your work’s done, but you’re hoping retailers showcase it right. Trends like direct-to-consumer sales are shaking things up, putting more power in manufacturers’ hands. Either way, this is where your vision meets its audience.
Conclusion
From that first sketch to a customer unboxing their new gadget, the electronics manufacturing process is a marathon of ingenuity and grit. For designers, it’s a canvas to innovate; for decision-makers, it’s a puzzle of priorities. I’ve seen firsthand how every stage demands collaboration—between dreamers and doers, machines and minds. Next time you power up a device, take a moment to picture the journey behind it. What’s your favorite piece of tech? Drop it in the comments—I’d love to hear your stories.
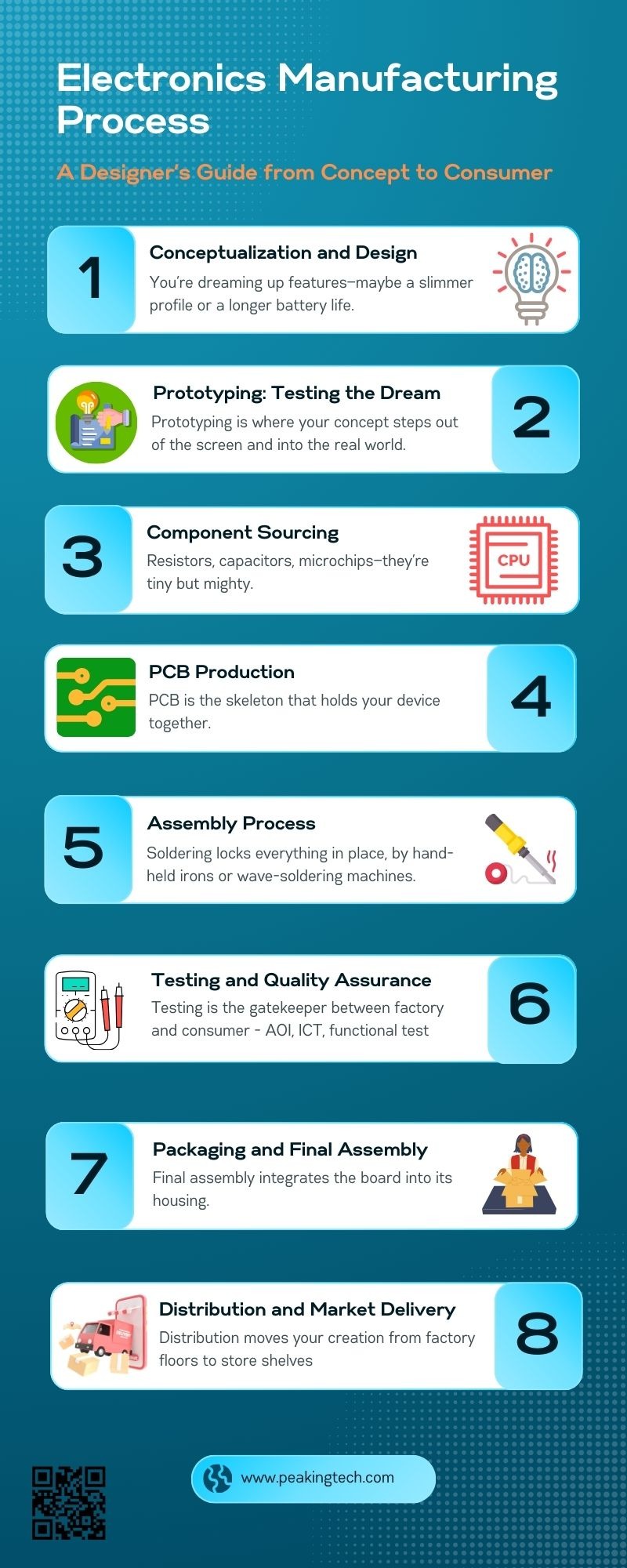
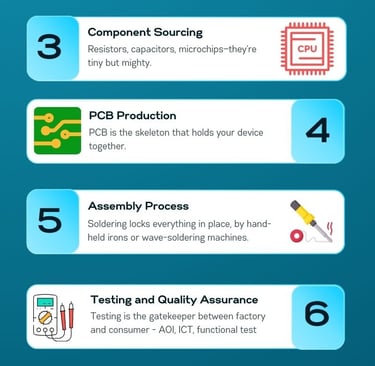