The Basics of Deep Draw Technology in Enclosure Manufacturing
When it comes to precision manufacturing, deep draw technology stands out as an essential process for creating strong, high-quality enclosures. This metal-forming method allows manufacturers to shape enclosures seamlessly, resulting in durable and versatile solutions that cater to industries like medical, aerospace, and consumer electronics.
2/5/20254 min read


Introduction
When it comes to precision manufacturing, deep draw technology stands out as an essential process for creating strong, high-quality enclosures. This metal-forming method allows manufacturers to shape enclosures seamlessly, resulting in durable and versatile solutions that cater to industries like medical, aerospace, and consumer electronics.
If you’re an engineer, designer, or business owner looking for a reliable enclosure solution, understanding how deep draw technology works can be a game-changer. In this article, we’ll walk you through the basics of deep drawing, its benefits, common applications, potential challenges, and key design tips to help you make informed decisions when working with manufacturers like Peakingtech.
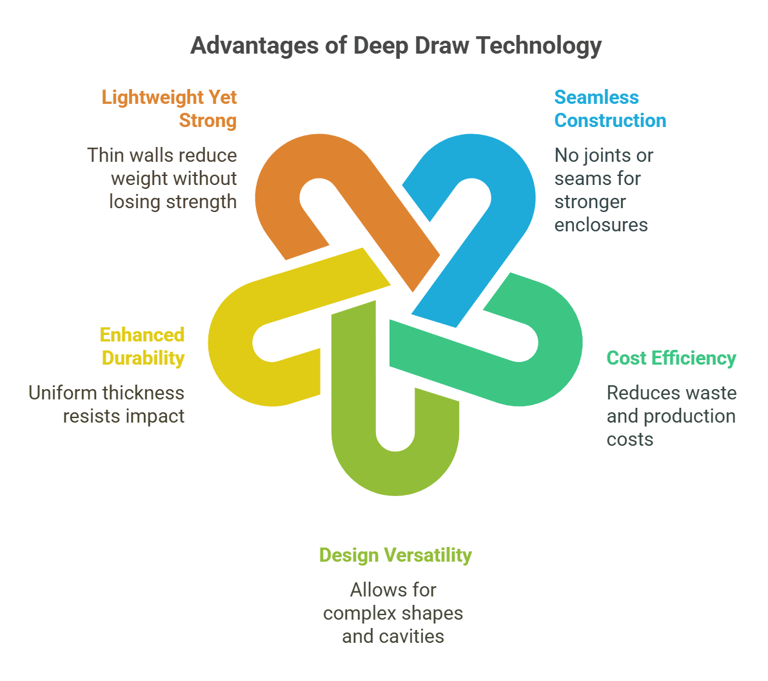
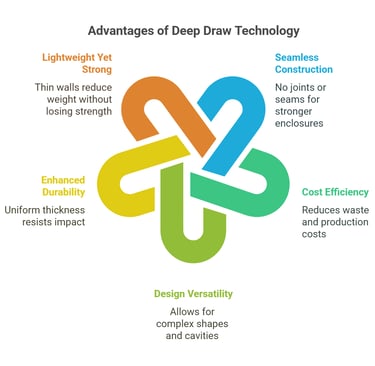
What is Deep Draw Technology?
Understanding the Process
Deep draw technology is a metal-forming technique that takes a flat metal sheet and transforms it into a seamless, hollow structure using a die and punch. Unlike methods such as stamping, machining, or welding, deep drawing creates enclosures without seams or joints, ensuring added strength and durability.
Step-by-Step Overview
Here’s a quick breakdown of how deep draw technology works:
Preparing the Metal Blank – A flat sheet of metal is cut and placed over a die.
Initial Forming – A punch forces the metal into the die cavity, shaping it as required.
Multiple Draw Stages (If Needed) – For deeper or more complex shapes, additional drawing steps refine the enclosure while maintaining strength.
Trimming and Finishing – Excess material is trimmed, and finishing touches like polishing, coating, or anodizing are applied.
Best Metals for Deep Drawing
Some metals work better for deep drawing due to their flexibility and strength, including:
Aluminum – Lightweight, corrosion-resistant, and widely used in aerospace and electronics.
Stainless Steel – Durable and perfect for medical and industrial applications.
Copper & Brass – Known for excellent conductivity and an attractive finish, often used in electrical components.
Why Choose Deep Draw Technology for Enclosures?
1. Seamless & Strong
Since deep-drawn enclosures are made from a single sheet of metal, they don’t have seams or welds that could weaken the structure. This makes them perfect for applications where airtight or watertight properties are essential, such as medical or aerospace uses.
2. Cost-Effective for Large Production Runs
For high-volume manufacturing, deep draw technology reduces waste and speeds up production, making it a more cost-effective solution than machining or welding. The upfront cost of tooling is offset by long-term savings in material and labor.
3. Design Flexibility
Deep draw technology can accommodate intricate shapes and deep cavities that other methods struggle to achieve. Whether you need cylindrical, rectangular, or custom-shaped enclosures, this process makes it possible.
4. Enhanced Durability
Because deep-drawn enclosures maintain a consistent wall thickness, they’re highly resistant to impact and harsh environments. This is crucial for enclosures exposed to extreme conditions.
5. Lightweight Yet Strong
The ability to create thin-walled enclosures without sacrificing durability makes deep drawing an excellent choice for applications where weight matters, such as aerospace and portable electronics.
Where Are Deep Drawn Enclosures Used?
Medical Devices
In the medical field, deep-drawn enclosures are used for surgical instrument housings and diagnostic equipment. Their seamless design helps maintain hygiene and sterility, which is critical in healthcare settings.
Aerospace & Defense
For avionics and military electronics, enclosures need to be rugged yet lightweight. Deep-drawn metal enclosures meet these demands, providing superior protection without unnecessary weight.
Consumer Electronics
Think about the sleek battery housings and handheld device cases you see in the market. Deep draw technology helps manufacturers create these enclosures with both aesthetic appeal and structural integrity.
Industrial Equipment
Industrial environments require enclosures that can withstand heat, moisture, and chemicals. Deep-drawn sensor housings and control panels offer durability and protection against such harsh conditions.
Challenges to Keep in Mind
While deep draw technology is incredibly effective, it does come with some limitations:
Design Restrictions – Very sharp edges or overly complex geometries can be difficult to achieve.
Material Limitations – Only certain metals are flexible enough for the process; brittle materials can crack under pressure.
High Tooling Costs – The initial investment in dies and punches can be expensive, making deep draw more suitable for large production runs rather than small batches.
Tips for Designing Deep-Drawn Enclosures
1. Involve Manufacturers Early
Working closely with experienced manufacturers like Peakingtech from the start ensures your design is optimized for deep drawing. Their expertise can help prevent costly revisions down the line.
2. Choose the Right Material
Selecting a metal that balances strength, flexibility, and cost is crucial. Factors like corrosion resistance and conductivity should be considered based on your product’s needs.
3. Maintain Uniform Wall Thickness
Ensuring even wall thickness helps maintain the enclosure’s structural integrity while minimizing unnecessary material use.
4. Factor in Secondary Processes
Depending on your product’s function, additional treatments like powder coating, anodizing, or drilling holes for assembly may be necessary. Planning for these ahead of time simplifies production.
Why Work with Peakingtech?
Custom Solutions to Fit Your Needs
Peakingtech specializes in crafting deep-drawn enclosures tailored to unique specifications, ensuring each product meets industry demands.
Proven Experience Across Industries
With years of experience serving the medical, industrial, aerospace, and electronics sectors, Peakingtech has a solid track record of delivering reliable, high-quality enclosures.
A Commitment to Quality
By using premium materials and precision-driven manufacturing techniques, Peakingtech guarantees top-notch enclosures that perform under the most demanding conditions.
Final Thoughts
Deep draw technology is a powerful solution for creating durable, seamless metal enclosures that stand up to demanding environments. Its cost efficiency, strength, and design flexibility make it a go-to choice for industries that require high-performance enclosures. While there are some limitations, working with a skilled manufacturer like Peakingtech can help navigate these challenges and optimize your enclosure for success.
Get in Touch
If you’re looking to explore deep draw technology for your next project, reach out to Peakingtech today. Their team of experts is ready to help you design and manufacture the perfect enclosure for your needs. Have thoughts or questions? Drop a comment below—we’d love to hear from you!