Technique Showdown: Laser Cutting vs. Waterjet Cutting for Electronics
Two of the most widely used cutting techniques in electronics manufacturing are laser cutting and waterjet cutting. Both methods offer unique advantages, but they also come with limitations that can affect your production efficiency, cost, and overall product quality.
2/26/20254 min read
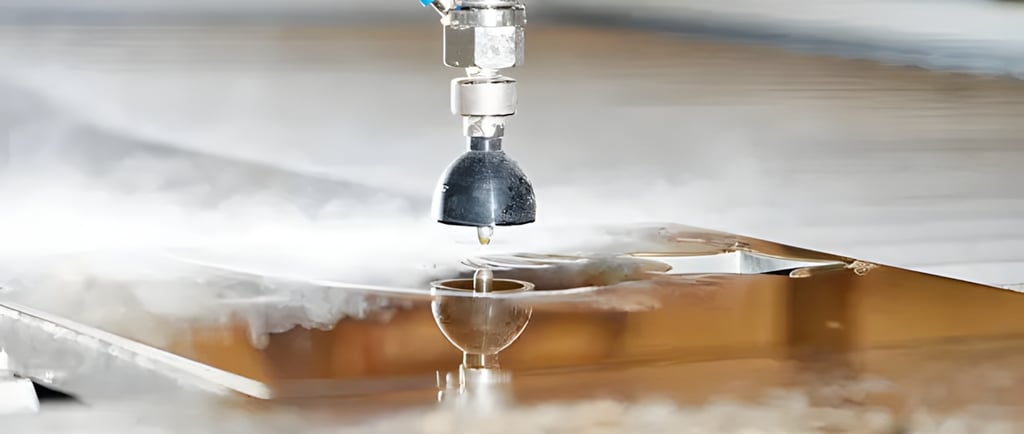
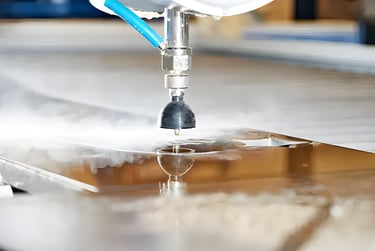
In electronics development, precision is everything. Whether you’re designing enclosures for your latest circuit board or cutting intricate patterns for flexible circuits, the fabrication method you choose can make or break your project. But with so many cutting technologies available, how do you decide which one is best suited for your application?
Two of the most widely used cutting techniques in electronics manufacturing are laser cutting and waterjet cutting. Both methods offer unique advantages, but they also come with limitations that can affect your production efficiency, cost, and overall product quality. In this article, we’ll break down these two fabrication techniques, explore their strengths and weaknesses, and help you make an informed decision on which method suits your electronics development needs.
1. Understanding Laser Cutting
How It Works
Laser cutting operates by directing a high-powered laser beam onto a material, which then melts, burns, or vaporizes the surface to create precise cuts. Depending on the material being processed, different types of lasers can be used:
CO₂ lasers – Ideal for cutting plastics, acrylics, and wood-based materials.
Fiber lasers – Best suited for cutting thin metals like stainless steel and aluminum.
UV lasers – Used for ultra-fine cutting of PCBs and delicate components.
Laser cutting is a non-contact process, meaning there’s minimal physical stress on the material. It’s also an incredibly fast and accurate method, making it a popular choice in electronics manufacturing.
Applications in Electronics Manufacturing
Laser cutting has found its way into multiple applications within the electronics industry, including:
Cutting PCB substrates – Materials like FR4, ceramics, and polyimide films can be cut with high precision.
Microfabrication of semiconductor components – Laser cutting enables the production of tiny, intricate designs used in microelectronics.
Creating enclosures and panels – Precise cutting of metal and acrylic panels for electronic device casings.
Flexible circuit cutting – Lasers provide an effective way to cut flexible circuits without causing mechanical stress.
Advantages of Laser Cutting
High Precision – Achieves tolerances within microns, making it ideal for small components.
Fast Cutting Speed – Particularly for thin materials, laser cutting is much faster than traditional methods.
Minimal Waste – Optimized laser paths ensure reduced material wastage.
Non-Contact Process – No risk of tool wear or mechanical deformation.
Limitations of Laser Cutting
Heat-Affected Zone (HAZ) – High temperatures can cause thermal damage, affecting material properties.
Limited Material Compatibility – Struggles with reflective metals like copper and aluminum.
Thickness Constraints – Less effective on thick materials due to the beam’s penetration limits.
2. Understanding Waterjet Cutting
How It Works
Waterjet cutting is a cold-cutting process that utilizes a high-pressure stream of water mixed with abrasive particles to slice through materials. Unlike laser cutting, waterjet cutting doesn’t generate heat, making it an excellent choice for materials that are sensitive to temperature changes.
Applications in Electronics Manufacturing
Waterjet cutting is widely used for:
Metal enclosures and heat sinks – Thick metals can be precisely cut without warping.
Processing non-conductive materials – Ceramics, plastics, and rubber-based materials are ideal candidates.
Structural components – Cutting complex shapes for brackets, frames, and mounts used in electronic devices.
Advantages of Waterjet Cutting
No Heat-Affected Zone (HAZ) – Ensures that heat-sensitive materials retain their structural integrity.
Wide Material Compatibility – Can cut almost any material, including thick metals, ceramics, and composites.
Excellent Edge Quality – Smooth, burr-free edges reduce the need for post-processing.
Environmentally Friendly – Produces minimal waste and doesn’t release harmful fumes.
Limitations of Waterjet Cutting
Slower than Laser Cutting – While effective for thick materials, it’s less efficient for thin materials.
Lower Precision for Fine Details – Cannot achieve the micro-level precision of laser cutting.
Higher Operating Costs – Requires water, abrasive materials, and extensive maintenance.
3. Laser Cutting vs. Waterjet Cutting: A Side-by-Side Comparison
To make it easier to compare, let’s break down the key differences between laser cutting and waterjet cutting:
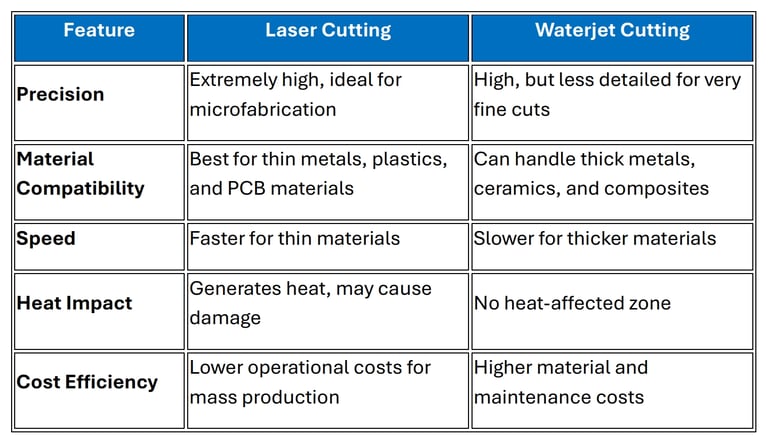
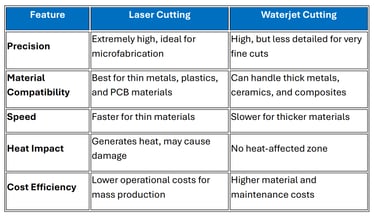
From the table above, you can see that laser cutting excels in speed and precision, while waterjet cutting offers superior material compatibility and prevents heat damage.
4. Choosing the Right Method for Your Electronics Project
So, which method should you choose? It depends on the specific needs of your electronics development. Here are some key factors to consider:
Choose Laser Cutting if:
You need high precision and intricate details.
Your materials are thin (e.g., PCB substrates, plastic films).
Speed and efficiency are priorities for mass production.
Choose Waterjet Cutting if:
You’re working with thick metals or brittle materials.
You need a process that doesn’t introduce heat damage.
Environmental sustainability is a key consideration.
Hybrid Approaches
In some cases, a hybrid approach may be the best solution. For example, you might use laser cutting for precision detail work and waterjet cutting for structural components. By understanding the strengths and weaknesses of each method, you can optimize your fabrication workflow and get the best of both worlds.
Conclusion
Choosing between laser cutting and waterjet cutting is not a one-size-fits-all decision. If precision, speed, and intricate details matter most, laser cutting is likely your best bet. However, if you need to cut thick, heat-sensitive materials, waterjet cutting will be the superior choice.
For electronics designers and decision-makers, selecting the right fabrication method can significantly impact production efficiency, costs, and end-product quality. By weighing the pros and cons of each technique, you can ensure that your electronics development process is optimized for success.
Got a project in mind? Carefully consider your cutting method, and you’ll be one step closer to bringing your next great electronics innovation to life!