Sustainability in Injection Molding: Eco-Friendly Practices and Materials
njection molding is the unsung hero of electronics manufacturing. It’s how we get those perfectly shaped, durable components that make devices reliable and affordable. But as the push for green manufacturing grows louder—driven by eco-conscious consumers, corporate ESG goals, and tougher regulations—it’s time to rethink how we use this workhorse process.
2/22/20256 min read
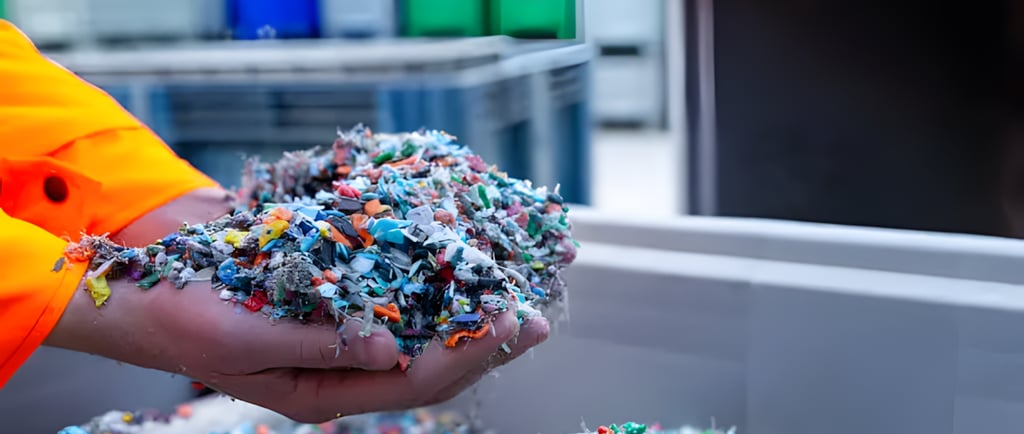
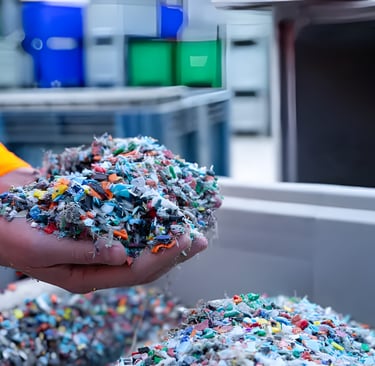
Imagine this: you’re designing the next big thing in electronics—a sleek, lightweight gadget that’ll have customers lining up. You’ve nailed the functionality, the aesthetics are spot-on, and then someone in the boardroom asks, “How sustainable is this?” Suddenly, the room gets quiet. If you’re in electronics development, that question isn’t just a buzzword anymore—it’s a make-or-break moment. The injection molding industry, which churns out everything from phone casings to circuit housings, produces over 55 million tons of plastic parts annually, yet less than 20% of that process prioritizes sustainability. Why should you care? Because your designs—and your decisions—can change that.
Injection molding is the unsung hero of electronics manufacturing. It’s how we get those perfectly shaped, durable components that make devices reliable and affordable. But as the push for green manufacturing grows louder—driven by eco-conscious consumers, corporate ESG goals, and tougher regulations—it’s time to rethink how we use this workhorse process. This isn’t about tree-hugging for the sake of it; it’s about staying ahead of the curve, cutting costs, and building products that don’t just perform but also protect the planet. Let’s dive into how designers and decision-makers like you can make sustainability in injection molding a reality—through smarter practices and eco-friendly materials.
Why Sustainability Matters in Injection Molding
Picture yourself flipping through stats at your desk: traditional injection molding guzzles energy like a teenager downs energy drinks—up to 60% of a facility’s power bill in some cases. Then there’s the waste—those sprues, runners, and defective parts piling up in bins, destined for landfills. And don’t get me started on the emissions from melting virgin plastic. For electronics, where precision and volume are king, this adds up fast. But here’s the kicker: your customers are noticing. A 2023 survey showed 70% of tech buyers prefer brands with green credentials. Your CEO’s probably getting grilled about ESG targets, too.
Then there’s the regulatory hammer looming. The EU’s plastic tax is already hitting manufacturers who don’t recycle, and the U.S. is tightening rules on waste. Ignore this, and you’re not just risking fines—you’re handing your competitors an edge. Sustainability isn’t a feel-good add-on; it’s a lifeline. For electronics designers, it’s a chance to innovate—to prove that the casings and connectors you spec out can be as planet-friendly as they are functional.
Eco-Friendly Practices in Injection Molding
So, how do you make injection molding greener without reinventing the wheel? Let’s start with energy. Those old hydraulic machines humming away in the factory? They’re dinosaurs—reliable, sure, but power-hungry. Switching to electric or hybrid machines can slash energy use by 30-50%. I talked to a buddy who manages a plant in Ohio, and he swears by his new electric setup—says it’s quieter, too, which the crew loves. Pair that with optimizing cycle times—shaving seconds off cooling or injection phases—and you’re not just saving watts, you’re boosting output.
Waste is another biggie. Ever walked past a scrap bin overflowing with rejected parts? That’s money—and opportunity—going to waste. Closed-loop recycling systems can grind up those leftovers and feed them back into the hopper. It’s not perfect—color matching gets tricky—but for non-visible components like internal brackets, it’s a no-brainer. And if you’re designing parts, think thin-wall molding. Slimmer walls mean less material, faster cycles, and lighter electronics that customers adore. I’ve seen teams pull this off with phone bezels, cutting plastic use by 15% without sacrificing strength.
Then there’s the tech angle—smart manufacturing. Picture sensors tracking every machine’s energy draw, or AI tweaking settings on the fly to minimize waste. It’s not sci-fi; it’s happening now. A friend at a mid-sized electronics firm told me they cut their defect rate by 8% just by letting the machines “talk” to each other. For you decision-makers, this isn’t just efficiency—it’s a story to sell to stakeholders. Prove you’re lean and green, and you’ve got a winning pitch.
Take NXP Semiconductors, for instance. They’ve been tweaking their molding process to use less energy, and last year they reported a 12% drop in emissions across their supply chain. That’s the kind of result that gets designers and execs nodding in approval.
Sustainable Materials for Injection Molding
Now, let’s talk materials—because no matter how efficient your process is, if you’re pumping out virgin petroleum-based plastics, you’re still part of the problem. Enter bioplastics. PLA (polylactic acid) and PHA (polyhydroxyalkanoates) come from corn or bacteria, not oil rigs. They’re renewable, and some even biodegrade under the right conditions. I’ve held PLA-molded prototypes—smooth, sturdy, perfect for a non-critical part like a cable clip. The catch? They’re pricier, and heat resistance can be iffy for electronics that run hot. Still, for low-stress components, they’re worth a test run.
Recycled plastics are another game-changer. Post-consumer resins—think soda bottles turned into circuit housings—are flooding the market. They’re cheaper than virgin stuff once you’ve got the supply chain dialed in, and they cut your carbon footprint by up to 70%. The challenge is consistency. I’ve heard horror stories of batches with weird specks or weaker tensile strength. But if you’re spec’ing out a rugged enclosure, partnering with a supplier who certifies their recycled stock can dodge those headaches.
Additives can stretch your sustainability further. Swap out some plastic for natural fibers like hemp or flax—yes, the stuff in your granola bar—and you’ve got a lighter, greener part. Mineral fillers like calcium carbonate work, too. A designer I know used hemp-filled resin for a speaker casing; said it felt premium and shaved 10% off material costs. And keep an eye on the horizon—algae-based plastics and carbon-neutral polymers are bubbling up in R&D labs. They’re not ready for prime time, but when they are, you’ll want to be the first to spec them.
Here’s a tip: start small. Mold a batch of standoffs or spacers with a bioplastic blend, test them in the lab, and see how they hold up. Share the data with your team—it’s how you build buy-in.
Benefits and Challenges of Going Green
Why bother? Beyond the warm fuzzies, going green pays off. Energy-efficient machines and recycled materials can trim your operating costs—sometimes by double digits over a few years. Your brand gets a glow-up, too. Imagine marketing a gadget as “made with 50% recycled materials”—that’s catnip for millennials and Gen Z. And with regulations tightening, you’re not just compliant; you’re ahead of the pack.
But it’s not all rosy. Upfront costs sting—new machines or material trials aren’t cheap. I’ve seen budgets balloon 20% in the first year of a sustainability pivot. Performance can take a hit, too—bioplastics might not handle the heat of a server rack, and recycled resins can throw curveballs in high-precision molds. Plus, good luck finding a steady stream of eco-materials if your supplier’s halfway across the globe.
The fix? Baby steps. Run a pilot project—say, a single production line—and track the ROI. Partner with a local recycler to lock in material quality. And lean on your team—designers can tweak tolerances, engineers can tweak processes. It’s a slog, but the payoff’s worth it.
The Future of Sustainable Injection Molding
Where’s this all heading? Automation’s the big one. Picture a factory where robots optimize every shot, cutting waste to near-zero. AI’s already predicting defects before they happen—my cousin’s startup uses it to save 5% on raw materials monthly. And 3D printing? It’s sneaking into prototyping, letting you test sustainable designs without firing up the big molds.
The circular economy’s the real dream, though. Imagine electronics where every molded part—cases, clips, brackets—gets designed for disassembly, then recycled into the next generation. It’s not far-fetched; companies like Dell are already looping plastics back into their supply chains. For you, that means sketching parts with end-of-life in mind—snap-fits over glue, single-material designs over composites.
This’ll take teamwork. Material scientists need to cook up better resins, policymakers need to fund recycling hubs, and you—designers and deciders—need to push the envelope. Injection molding isn’t just shaping plastic; it’s shaping a greener tomorrow.
Conclusion
Sustainability in injection molding isn’t a pipe dream—it’s a toolbox you can start using today. Energy-efficient machines, recycled resins, and clever design tweaks are all within reach for electronics development. Sure, it takes effort, but the rewards—lower costs, happier customers, a cleaner planet—are too big to ignore. Start small, test a bioplastic spacer, or pitch a hybrid machine to your boss. Share this with your team, kick around some ideas—I’d love to hear what you come up with.
Because here’s the truth: every component you design, every decision you make, ripples out. In a world that’s watching, injection molding can be more than a process—it can be a promise.