Surface Mount Technology (SMT) vs. Through-Hole: Which is Right for Your Project?
Two of the most common assembly techniques are Surface Mount Technology (SMT) and Through-Hole Technology (THT). Understanding the strengths and weaknesses of each method is key to making the right choice for your product’s design, production process, and long-term performance.
2/15/20256 min read
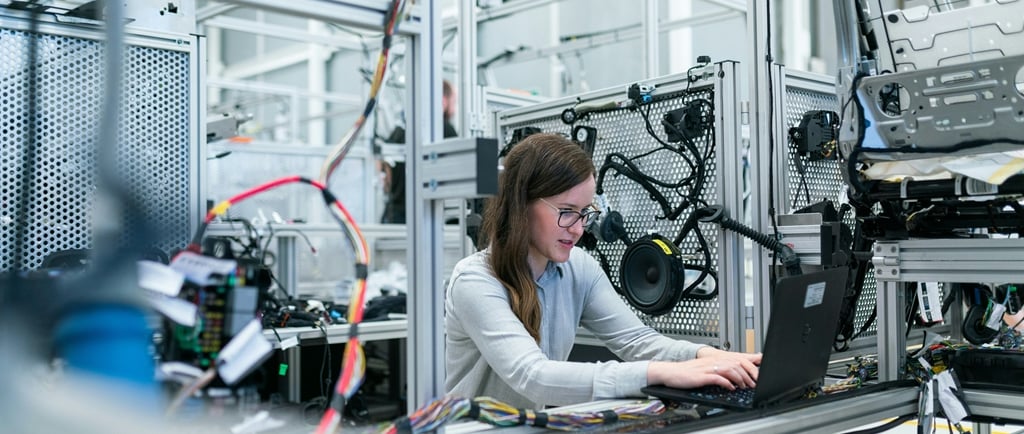
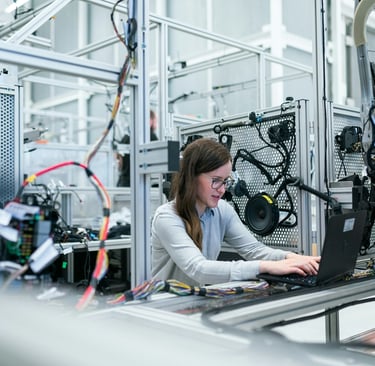
If you're working on an electronics project, whether it’s designing a sleek consumer gadget or developing something for industrial use, you’re likely facing the decision of how to assemble your printed circuit boards (PCBs). Two of the most common assembly techniques are Surface Mount Technology (SMT) and Through-Hole Technology (THT). Understanding the strengths and weaknesses of each method is key to making the right choice for your product’s design, production process, and long-term performance.
In this post, we’ll walk through the essentials of SMT and THT, explain when and why to use each, and help you figure out which one is best for your next project. Let’s dive in.
What is Surface Mount Technology (SMT)?
Surface Mount Technology, or SMT, is a method where electronic components are mounted directly onto the surface of the PCB. Instead of leads going through the board, SMT components have flat contacts that are soldered onto the surface during the assembly process. It’s a common method for modern electronics because it’s fast and efficient—especially when you’re working with compact, high-density designs.
What You Need to Know About SMT:
Component Types: SMT is used primarily for small, lightweight components like resistors, capacitors, integrated circuits (ICs), and microchips.
Speed & Automation: Because SMT can be fully automated, it’s perfect for high-volume manufacturing. Machines can place and solder thousands of components in a fraction of the time it would take by hand.
Space-Saving: SMT allows for very small components that take up less space, making it ideal for designing sleek, compact devices like smartphones and wearable tech.
What is Through-Hole Technology (THT)?
Through-Hole Technology, or THT, is an older method where components have leads (the pins or wires) that pass through holes drilled into the PCB. The leads are soldered on the opposite side of the board, creating a mechanical bond that’s both physically strong and electrically secure. While THT is less commonly used in consumer devices these days, it’s still the go-to option for certain types of designs.
What You Need to Know About THT:
Component Types: THT is often used for larger, more durable components like connectors, transformers, high-power resistors, and switches—parts that need to be robust or exposed to high currents.
Manual & Labor-Intensive: While some THT processes can be automated, they often require manual insertion of components and soldering, making them a bit more labor-intensive compared to SMT.
Durability: THT components are generally more robust, with better mechanical strength, making them ideal for environments where the PCB will experience vibrations, shocks, or heavy use.
Key Differences Between SMT and THT
Now that we’ve outlined the basics of each method, let’s take a closer look at how SMT and THT stack up against each other in several important areas.
1. Manufacturing Process
One of the biggest differences between SMT and THT is the manufacturing process. SMT is much more automated. Machines place and solder components in high-speed sequences, making it ideal for mass production. For instance, in smartphone manufacturing, automated machines can place hundreds of tiny components per minute, which would be nearly impossible by hand.
THT, on the other hand, usually requires more manual labor. While machines can assist with inserting components, it’s still common to see assembly workers physically placing and soldering parts—especially when you’re dealing with low-volume production or prototypes.
2. Component Size and Density
If your design requires small, densely packed components, SMT is the clear winner. Because SMT components are much smaller than THT parts, you can fit more of them in the same space, allowing for more compact, space-efficient designs. This is crucial for modern consumer electronics like laptops, tablets, and wearables, where space is at a premium.
THT components, due to their larger size, require more space on the board. While they are perfect for larger, heavier components that need mechanical strength, they’re not ideal for tiny, intricate designs.
3. Reliability and Durability
Reliability is always a top concern in electronics, but the kind of reliability you need depends on your application. THT has a stronger mechanical bond between the component and the PCB, thanks to the leads passing through the holes. This makes THT a better option for high-stress environments like automotive, industrial machinery, and military electronics, where the boards will be exposed to vibrations, shocks, and extreme conditions.
SMT, while generally reliable in most scenarios, doesn’t have the same kind of physical support as THT. It’s better suited for devices where the focus is on small size and high performance rather than rugged durability. That being said, advancements in soldering techniques and board design have made SMT increasingly resilient to mechanical stress.
4. Cost Considerations
Cost is always a major factor in deciding which technology to use. When it comes to mass production, SMT wins hands down because of its automated processes. Automation drives down labor costs, and the speed at which machines can assemble boards helps keep production costs low. For high-volume products like smartphones or consumer electronics, SMT is usually the more cost-effective choice.
However, if you’re working on low-volume production or a prototype, THT may be more economical, as it doesn’t require expensive automated equipment. The manual assembly process can be more time-consuming and labor-intensive, but for smaller batches or specialized parts, it may make more sense from a cost perspective.
5. Ease of Assembly
Because of the high level of automation in SMT, the process tends to be faster and more efficient for large runs. Once you’ve set up the initial equipment, machines can handle the bulk of the assembly, allowing you to ramp up production quickly.
On the other hand, THT requires more manual intervention, which can make the process slower and more prone to human error. While this makes THT less ideal for high-volume production, it can be advantageous in smaller runs or custom projects where more flexibility and hands-on work are required.
6. Repair and Modification
What happens when you need to fix something? THT is easier to repair or modify because the leads are larger and more accessible. If a component fails, you can easily replace it by desoldering the leads and swapping out the part. This is especially helpful in prototypes or low-volume production runs where modifications may be frequent.
SMT, while still repairable, can be more challenging to work with. The small components are harder to handle, and if you need to replace a faulty part, you’ll likely need specialized tools and equipment. This makes SMT less ideal for projects that require frequent repairs or modifications.
When Should You Use SMT?
If your product is a high-volume consumer electronic device (think smartphones, laptops, wearables), SMT is the way to go. It allows for faster production, smaller components, and a compact design. SMT is also great for low-power devices, where space-saving and performance are top priorities.
When Should You Use THT?
THT is better suited for industrial, military, or aerospace applications, where the boards will be exposed to harsh conditions. If your components need more mechanical strength and stability (e.g., connectors, large capacitors, and high-power components), THT is the better choice.
It’s also a good option for low-volume production or prototyping, especially if you need more flexibility and customizability in your assembly process.
Hybrid Approaches: Combining SMT and THT
Sometimes, the best solution is a hybrid. You might use SMT for most of the components, but THT for the larger or more rugged parts that require extra durability. This approach can be especially useful when you're designing a complex product that needs both compactness and toughness.
How to Choose the Right Technology for Your Project
The choice between SMT and THT boils down to a few key factors:
Production volume: High-volume? Go for SMT. Small batch or prototype? THT might work better.
Size and design complexity: If you need to minimize size, SMT is your friend. For larger, more robust components, go with THT.
Reliability needs: Harsh environments? THT is the stronger option. For most commercial applications, SMT will be fine.
Budget and timeline: Consider both short-term and long-term costs. High-volume runs will benefit from the cost efficiency of SMT, but low-volume or custom projects might be cheaper with THT.
Conclusion
Choosing between SMT and THT depends on the unique requirements of your project. There’s no one-size-fits-all answer, but understanding the pros and cons of each technology will help you make an informed decision. Whether you go with SMT for its speed and compact design or THT for its rugged reliability, the right choice will ensure your product performs at its best.
Ultimately, your decision will hinge on factors like production volume, component size, durability, and cost. By keeping these elements in mind, you can choose the method that aligns with your project’s needs and sets your product up for success.
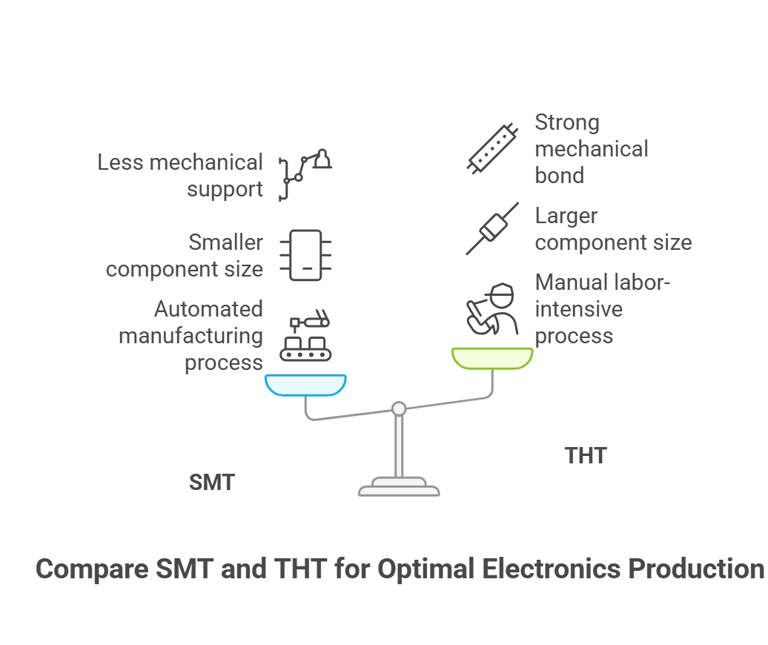
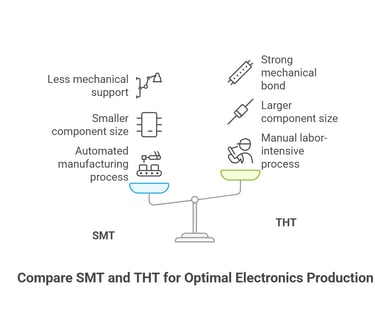