Streamlining BOM Management: Essential Tips for Startups and Product Developers in Electronics Manufacturing
Discover how to streamline BOM (Bill of Materials) management in electronics manufacturing. This guide offers startups and product developers actionable tips to optimize processes, reduce risks, and achieve efficient production.
1/17/2025
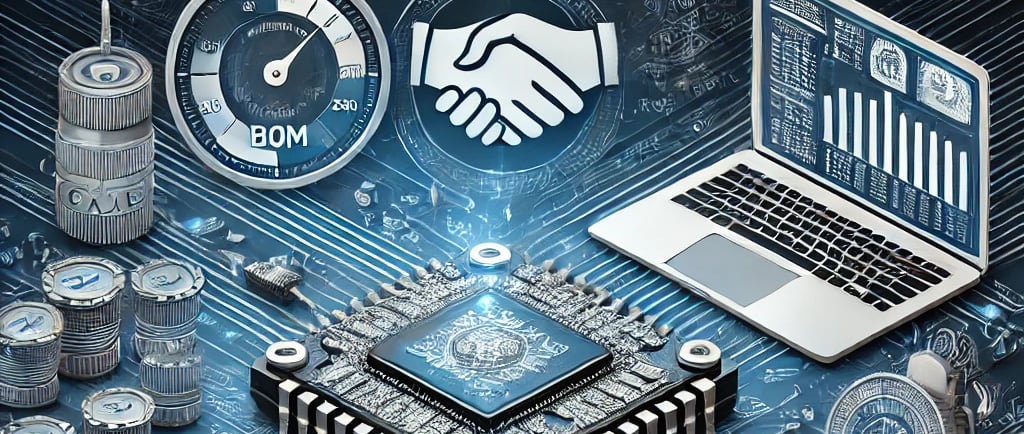
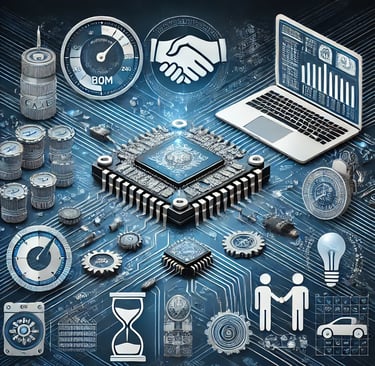
1. Introduction
In the fast-paced world of electronics manufacturing, startups and product developers often grapple with tight budgets, aggressive timelines, and high expectations. At the core of a successful product launch lies the effective management of the Bill of Materials (BOM). The BOM serves as the backbone of any electronics project, detailing every component, material, and assembly required to bring a design to life.
However, poor BOM management can lead to production delays, unexpected costs, and even product failures. In this guide, we’ll explore strategies and best practices for optimizing BOM management to help startups and product developers streamline their processes, reduce risks, and achieve manufacturing success.
2. Understanding the Importance of BOM Management
The BOM is much more than a simple list of parts. It is a detailed document that specifies everything needed to manufacture a product, from individual components and subassemblies to raw materials and hardware.
Why BOM Management Matters:
Production Efficiency: A well-structured BOM ensures that all necessary components are available and correctly assembled, reducing production delays.
Cost Control: Accurate BOMs prevent over-ordering, under-ordering, or sourcing incorrect parts, helping to manage costs effectively.
Time-to-Market: An optimized BOM reduces errors and rework during production, enabling faster product launches.
Real-world example: A startup designing a smart home device overlooked a key resistor in their BOM. This omission led to a delay in production while the team scrambled to source the missing part, ultimately pushing back their launch date by three months.
3. Common Challenges Startups Face with BOM Management
Managing a BOM can be particularly challenging for startups, which often lack the resources and experience of larger organizations. Some common issues include:
Incomplete Data: Missing details like manufacturer part numbers (MPNs), quantities, or material specifications can cause confusion during procurement and assembly.
Inconsistent Formats: Using non-standardized templates leads to miscommunication between design, procurement, and manufacturing teams.
Obsolete Components: Rapidly evolving technology often renders parts obsolete, creating sourcing challenges.
Lack of Revision Control: Failure to track changes in the BOM during development can result in mismatches between design and production.
The impact of these challenges is significant, often leading to increased costs, wasted time, and frustrated stakeholders.
4. Solutions to Improve BOM Management
4.1. Use the Right Tools
Investing in the right tools can transform how startups manage their BOMs. Options include:
BOM Management Software: Tools like Arena PLM or Altium Designer provide features for creating, organizing, and sharing BOMs.
ERP Systems: Platforms like SAP or NetSuite integrate BOM management with procurement and inventory tracking.
For startups on a budget, free or low-cost tools like Google Sheets or Airtable can also be effective, provided they are used with strict guidelines.
4.2. Standardize BOM Formats
A standardized BOM format ensures clarity and consistency across teams. Best practices include:
Using clear column headers such as “Part Number,” “Description,” “Quantity,” and “Supplier.”
Including a “Revision” field to track updates.
Adding a “Notes” column for special instructions or alternatives.
4.3. Ensure Cross-Functional Collaboration
Collaboration between design, procurement, and manufacturing teams is critical. Ways to improve communication include:
Regular BOM review meetings to identify potential issues early.
Shared digital platforms that allow real-time updates and feedback.
Designating a BOM owner responsible for maintaining accuracy.
4.4. Prioritize Component Sourcing
Selecting the right components and suppliers is vital for BOM optimization:
Approved Vendor Lists (AVLs): Create and maintain a list of pre-approved suppliers to ensure quality and reliability.
Second Sourcing: Identify alternative components to mitigate risks like shortages or long lead times.
4.5. Implement Revision Control
Tracking BOM revisions is essential during prototyping and production. A robust revision control process includes:
Assigning unique revision numbers to each version.
Documenting all changes and their rationale.
Communicating updates promptly to all stakeholders.
4.6. Partner with Your EMS Provider
Electronics Manufacturing Service (EMS) providers can offer invaluable support in optimizing BOMs, such as Peakingtech, providing important advantages:
Extensive Components Inventory:
We maintain a comprehensive inventory of commonly used components, enabling faster procurement and reducing lead times. This ensures your production schedules remain on track, even for tight deadlines.
Network of Suppliers for Nonstandard Parts:
Our established relationships with a wide network of trusted suppliers allow us to source hard-to-find or nonstandard components efficiently. Whether it’s a specialized IC or a custom mechanical part, we have the connections to get it.
Experience and Expertise with Various Components:
With years of experience working with diverse components across industries, we understand the nuances of material selection, compatibility, and performance. This expertise enables us to provide reliable advice on component alternatives, ensuring cost-effectiveness without compromising quality.
Design for Manufacturing (DFM) Analysis:
Our team reviews your BOM for potential manufacturing challenges, helping to optimize your design for cost, assembly, and scalability.
Risk Mitigation:
Leveraging our supplier network and industry insights, we proactively identify and mitigate risks like component shortages, long lead times, or obsolescence, safeguarding your supply chain.
5. Cost and Risk Management in BOM
Balancing cost and quality is a constant challenge in BOM management. Tips for achieving this balance include:
Lifecycle Analysis: Choose components with a long lifecycle to avoid obsolescence.
Bulk Purchasing: Take advantage of economies of scale by ordering components in bulk, but ensure you have adequate storage and cash flow.
Forecasting: Use demand forecasts to plan component sourcing, reducing the risk of shortages or excess inventory.
By proactively managing these factors, startups can minimize risks and maintain a competitive edge.
6. Proactive BOM Optimization: Future-Proof Your Product
To stay ahead in the ever-evolving electronics industry, startups must focus on long-term BOM optimization:
Modular BOMs: Design BOMs to accommodate future upgrades or variations, enhancing product flexibility.
Sustainability: Incorporate eco-friendly materials and processes to align with growing consumer and regulatory demands.
Industry Trends: Stay informed about emerging technologies and standards to ensure your BOM remains relevant.
7. Case Study: A Startup’s Journey to BOM Excellence
Imagine a wearable tech startup struggling with frequent production delays due to BOM inaccuracies. By partnering with an EMS provider, they:
Standardized their BOM format, reducing errors during procurement.
Identified cost-effective component alternatives, cutting their material costs by 15%.
Implemented robust revision control, ensuring seamless communication between teams.
As a result, the startup not only launched their product on time but also gained the confidence of investors and customers.
8. Key Takeaways and Actionable Steps
Improving BOM management is a critical step for startups aiming to succeed in electronics manufacturing. To recap:
Use the right tools and standardize your BOM format.
Foster collaboration across design, procurement, and manufacturing teams.
Partner with an EMS provider to optimize your BOM and reduce risks.
Stay proactive by planning for future trends and challenges.
Startups that prioritize these steps can streamline their processes, save costs, and bring their products to market more efficiently.
9. Call-to-Action: Work with a Trusted EMS Partner
Effective BOM management doesn’t have to be overwhelming. By partnering with an experienced EMS provider, startups can gain access to expert guidance, advanced tools, and a reliable supply chain network.
Contact us today to learn how our team can help you optimize your BOM and bring your electronics projects to life. Let us help you turn your vision into reality!