Step-by-Step: The Injection Molding Process Explained for Electronics Innovators
It’s the magic of injection molding, a process that’s been quietly revolutionizing how we bring electronics to life. For designers and decision-makers in electronics development, understanding this process isn’t just a nice-to-have—it’s a superpower. From sketching your vision to cranking out thousands of units, injection molding bridges creativity and production like nothing else.
2/22/20255 min read
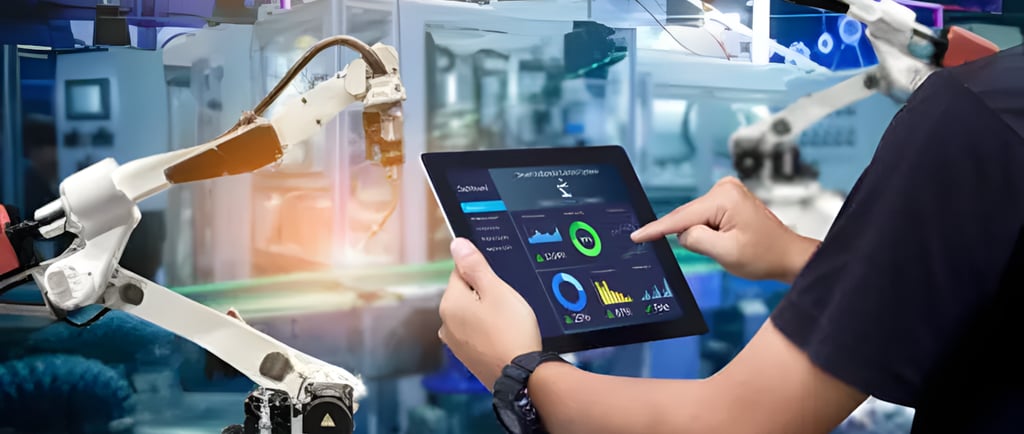
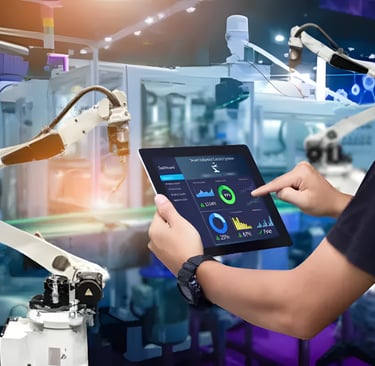
Imagine holding a sleek, perfectly molded plastic housing for the next game-changing electronic gadget—maybe a wearable health monitor or a smart home controller. That satisfying click as components snap into place? It’s no accident. It’s the magic of injection molding, a process that’s been quietly revolutionizing how we bring electronics to life. For designers and decision-makers in electronics development, understanding this process isn’t just a nice-to-have—it’s a superpower. From sketching your vision to cranking out thousands of units, injection molding bridges creativity and production like nothing else.
In this guide, I’ll walk you through the three big stages—design, tooling, and production—with a focus on how they matter to your next electronics project. Whether you’re dreaming up a circuit-hugging enclosure or scaling a product line, here’s the step-by-step breakdown—humanized, practical, and packed with insights.
The Design Stage: Where Your Vision Takes Shape
Every great electronic device starts with a spark—an idea that needs a physical form. In injection molding, the design stage is where you turn that spark into a blueprint, and for electronics folks, it’s a make-or-break moment. You’re not just designing a shell; you’re crafting a home for sensitive circuits, buttons, and ports. Let’s break it down.
Conceptualization and Requirements: The Ground Rules
Picture this: You’re sitting with your team, coffee in hand, hashing out what this gizmo needs to do. Is it a rugged outdoor sensor or a minimalist remote? That decides your material—say, tough polycarbonate for durability or ABS for a smooth finish. You’ll also nail down tolerances—those tiny measurements that ensure your PCB fits snugly without rattling. I’ve seen designers sketch on napkins at this stage, and honestly, that’s where the best ideas start. You’re asking: How thin can the walls be? Where do the screws go? It’s a dance between form, function, and manufacturability.
CAD Modeling: Bringing It to Life
Next, you fire up the CAD software—think of it as your digital sculpting tool. This is where your napkin sketch becomes a 3D model, precise down to the millimeter. For electronics, this means plotting out every detail: the curve of a button, the slot for a USB-C port, even the draft angles (those slight tapers) that’ll let the part pop out of the mold later. I once watched a designer tweak a model for hours just to shave off 0.2mm from a wall—because in electronics, every bit of space counts. This isn’t arts and crafts; it’s engineering with soul.
Simulation and Prototyping: Testing the Waters
Before you commit, you run simulations—mold flow analysis, to be exact. It’s like a crystal ball, showing you where plastic might pool unevenly or cool too fast, leaving ugly sink marks near a screw boss. For electronics, this is clutch—warped parts can throw off alignments for delicate components. Sometimes, you’ll even 3D-print a prototype to hold in your hand. I’ve seen teams cheer when a prototype fits the PCB on the first try—it’s a small win, but it feels huge. This step saves headaches (and cash) down the line.
This stage is your playground, designers. Get it right, and you’ve got a foundation that sings to both your creative side and the production crew.
The Tooling Stage: Building the Heart of the Operation
Now we’re getting serious. The tooling stage is where your design becomes a mold—a steel or aluminum beast that’ll churn out parts like a champ. For electronics decision-makers, this is where you weigh cost, speed, and scale. It’s less about dreaming and more about making it real.
Mold Design: The Blueprint’s Big Brother
Your CAD file hands off the baton to the mold designer, who figures out how to split your part into a core and cavity—the two halves of the mold. They’ll map out gates (where plastic flows in) and cooling channels (to keep things chill). In electronics, precision is everything—think of a mold for a phone case with tiny cutouts for speakers. One misstep, and you’re reprinting boards to match. I’ve heard mold designers grumble about “overly ambitious” part designs—too many undercuts or thin ribs—but a good team makes it work.
Material Selection for the Mold: Steel vs. Aluminum
Here’s where decision-makers lean in. Steel molds are the heavyweights—pricey but built for millions of cycles, perfect for that hot new wearable hitting mass production. Aluminum? It’s lighter on the wallet and faster to machine—great for prototypes or short runs, like a limited-edition controller. I once saw a startup agonize over this choice, crunching numbers late into the night. It’s not sexy, but it’s the kind of call that keeps your project on track.
Mold Fabrication: Craftsmanship Meets Tech
This is the gritty part. CNC machines carve your mold from a solid block, while EDM (electrical discharge machining) zaps away tiny details—like the texture for a grippy surface. Polishing comes next, because in electronics, a flawless finish isn’t just vanity; it’s branding. I’ve toured shops where machinists treat molds like art, wiping sweat as they perfect a mirror shine. It’s slow, meticulous, and totally worth it when you see the first part pop out.
Tooling’s the unsung hero. Designers, you’ll love how it locks in your vision; deciders, you’ll appreciate how it balances budget and ambition.
The Production Stage: Where the Magic Happens
Finally, the payoff—production. This is where your mold meets molten plastic, and your design becomes a tangible product. For electronics, it’s about consistency: every part needs to cradle those circuits just right, batch after batch.
Material Preparation: Setting the Stage
First, you prep the plastic pellets. Ever seen a bag of those colorful little beads? They’re the raw stuff of your enclosure. If it’s a material like nylon, you’ll dry it first—moisture’s the enemy, causing bubbles or weak spots. Then it’s into the hopper of the injection molding machine. I’ve watched operators tweak this step like chefs seasoning a stew—too little care, and the whole batch suffers.
Injection: The Main Event
Here’s the heartbeat: the machine melts the plastic in a heated barrel, then rams it into the mold with a screw at insane pressure—think 20,000 PSI. Temperature’s key—too hot, and it degrades; too cool, and it won’t fill those tiny speaker grilles. Speed matters too—fast for thin walls, slower for chunky parts. I’ve stood by a machine as it hums and hisses, feeling the heat off the barrel. It’s industrial poetry.
Cooling and Solidification: Patience Pays Off
Once injected, the plastic cools inside the mold, hardening into shape. Cooling channels speed this up, but it’s still a waiting game—rush it, and you get warped parts that won’t hold a battery. For electronics, this is where uniformity shines; every unit needs to match. I’ve seen operators tap their feet, itching to open the mold, but timing’s everything.
Ejection and Finishing: The Big Reveal
The mold splits, ejector pins pop the part free, and there it is—your creation. Sometimes there’s flash (excess plastic) to trim, or maybe you paint it for that premium sheen. I once held a freshly molded remote casing, still warm, and felt like a kid unwrapping a gift. Post-processing seals the deal—snap in the electronics, and you’re golden.
Production’s where scale meets reality. Designers, you’ll see your work multiply; deciders, you’ll feel the thrill of efficiency kicking in.
Wrapping It Up: Why This Matters to You
So there you have it—design, tooling, production. The injection molding process is like a three-act play: the creative brainstorm, the gritty setup, and the triumphant rollout. For electronics development, it’s your ticket to turning wild ideas into reliable, mass-produced reality. Designers, you get to flex your ingenuity, crafting enclosures that protect and dazzle. Decision-makers, you steer the ship, balancing cost with quality to hit that sweet spot.
Next time you hold a molded gadget, think of the journey—months of tweaks, a mold carved with love, and a machine humming through the night. Want to dive deeper? Check out CAD tools or chat with a mold maker. Your next big thing’s waiting.