Step-by-Step Guide: How to Partner with a Manufacturer for Custom Enclosure Design
In today's competitive market, custom enclosures play a crucial role in meeting unique project requirements. Whether it's functionality, durability, or branding, custom enclosures can make or break the success of your product.
2/10/20253 min read
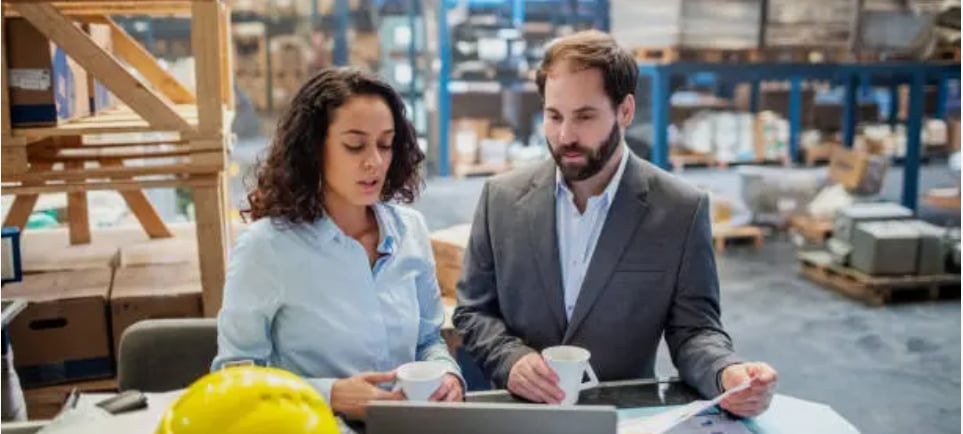
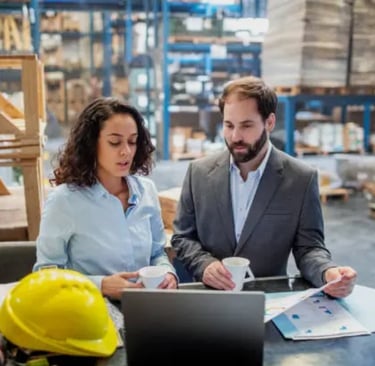
In today's competitive market, custom enclosures play a crucial role in meeting unique project requirements. Whether it's functionality, durability, or branding, custom enclosures can make or break the success of your product. Partnering with an experienced manufacturer simplifies the process and ensures high-quality results. This guide will walk you through the essential steps to collaborate effectively with a manufacturer on custom enclosure design.
Why Partnering with a Manufacturer is Essential
Expertise in Customization
Manufacturers bring specialized knowledge in materials, processes, and design optimization. Their expertise can help you navigate the complexities of custom enclosure design, ensuring that your product meets all functional and aesthetic requirements.
Access to Advanced Technology
Manufacturers have access to advanced technologies like CNC machining, 3D printing, and deep draw technology. These capabilities are often difficult to replicate in-house, making a partnership with a manufacturer invaluable.
Cost and Time Efficiency
Manufacturers streamline production while minimizing waste and reducing costs. Their efficient processes ensure that your project stays within budget and meets deadlines.
Step 1: Define Your Project Requirements
Identify Key Needs
Functional Requirements:
Size, Shape, and Internal Layout: Determine the dimensions and internal configuration of your enclosure.
Cutouts: Specify the need for cutouts for connectors, displays, or buttons.
Environmental Considerations:
Waterproofing (IP Ratings): Ensure your enclosure can withstand moisture.
Heat Dissipation: Consider thermal management requirements.
Impact Resistance: Ensure durability against physical impacts.
Consider Aesthetic Goals
Branding Elements: Incorporate logos or custom colors to enhance brand recognition.
Surface Finishes: Choose finishes like anodizing or powder coating for durability and aesthetics.
Set a Budget and Timeline
Determine your budget constraints and project deadlines to guide the design process. This will help you make informed decisions throughout the project.
Step 2: Research and Select the Right Manufacturer
Evaluate Experience and Expertise
Industry Experience: Look for manufacturers with a proven track record in your industry, whether it's medical devices, IoT, or consumer electronics.
Case Studies: Review past projects to assess their capabilities and success stories.
Assess Capabilities
Customization Options: Ensure they offer the necessary customization options, such as material selection and advanced manufacturing techniques.
Project Scale: Confirm their ability to handle your project’s scale, whether it's small-batch or large-scale production.
Check Certifications and Standards
Industry Standards: Ensure compliance with relevant industry standards, such as ISO certifications and RoHS compliance.
Regulatory Requirements: Verify their ability to meet regulatory requirements for your product.
Step 3: Collaborate on Design Development
Share Detailed Specifications
CAD Files or Sketches: Provide detailed drawings of your desired enclosure design.
Detailed Notes: Include notes on dimensions, materials, and functional features.
Leverage Manufacturer Expertise
Refine Your Concept: Work with their design team to refine your initial concept.
Improve Durability and Cost-Efficiency: Discuss options for enhancing durability, reducing costs, and improving manufacturability.
Plan for Prototyping
Request Prototypes: Use prototypes to test fit, functionality, and aesthetics.
Iterative Improvements: Use feedback from prototypes to make necessary adjustments.
Step 4: Understand Manufacturing Processes
Material Selection
Work with the manufacturer to choose materials that balance performance, cost, and sustainability. For example, consider aluminum for durability or plastic for cost-efficiency.
Manufacturing Techniques
CNC Machining: Ideal for precision designs.
Deep Draw Technology: Suitable for seamless metal enclosures.
Injection Molding: Perfect for complex plastic designs.
Surface Finishes and Post-Processing
Discuss options like powder coating, anodizing, or engraving to enhance durability and branding.
Step 5: Test and Approve the Final Design
Perform Functional Testing
Real-World Conditions: Test prototypes under real-world conditions, such as temperature extremes or moisture exposure.
Component Fit: Verify that all components fit properly within the enclosure.
Ensure Compliance with Standards
Confirm that the enclosure meets industry regulations, such as IP ratings and EMI shielding.
Provide Final Approval
Review all design elements before moving into full-scale production.
Step 6: Move into Production
Small-Batch vs Full Production Runs
Decide whether to start with a small batch for additional testing or proceed directly to full production.
Quality Control Measures
Quality Assurance: Ensure the manufacturer has robust quality assurance processes in place.
Documentation: Request documentation or certifications verifying product quality.
Tips for Building a Strong Partnership with Your Manufacturer
Communicate Clearly and Frequently
Open Lines of Communication: Maintain open communication throughout the design and production process.
Share Updates: Share updates or changes promptly to avoid delays.
Be Open to Feedback
Leverage the manufacturer’s expertise to improve your design or address potential issues early.
Establish Long-Term Collaboration
Build a relationship for future projects by demonstrating trust and reliability on both sides.
Why Choose Peakingtech as Your Manufacturing Partner?
Expertise in Custom Enclosure Design
Decades of Experience: Serving industries like medical devices, industrial automation, consumer electronics, and IoT.
Tailored Solutions: Proven ability to deliver custom solutions that meet complex requirements.
Advanced Capabilities
Cutting-Edge Techniques: Access to deep draw technology, CNC machining, and rapid prototyping services.
Rapid Prototyping: Quickly refine designs with rapid prototyping.
Commitment to Quality and Collaboration
ISO-Certified Processes: Ensure high-quality results.
Dedicated Team: Works closely with clients from concept to production.
Conclusion
Partnering with a manufacturer for custom enclosure design involves defining requirements, selecting the right partner, collaborating on design development, understanding manufacturing processes, testing prototypes, and moving into production. Working with an experienced manufacturer ensures high-quality custom enclosures that meet unique project needs.
Call-to-Action (CTA)
Ready to bring your custom enclosure design to life? Contact Peakingtech for expert guidance and schedule a consultation or request a quote for your next project. Let's create something extraordinary together!