Space Electronics: Manufacturing Challenges for Satellites and Spacecraft
Space electronics aren’t just a job; they’re a frontier that tests every ounce of ingenuity and grit. Let’s unpack the real challenges, spotlight some hard-earned wins, and see what’s cooking for the future, all with a lens on the nitty-gritty details that matter to your work.
2/20/20256 min read
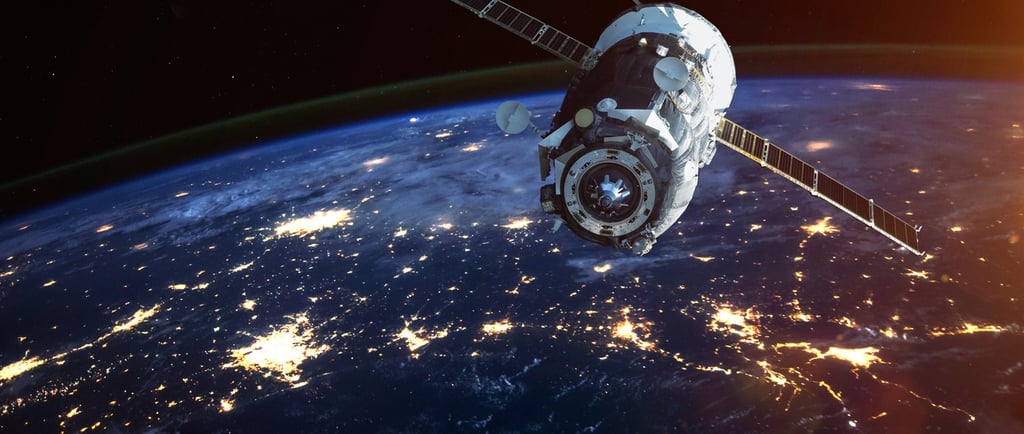
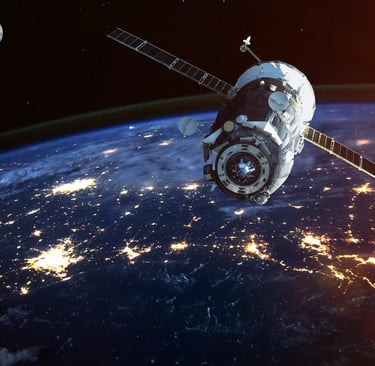
Picture this: a microchip no bigger than your thumbnail, zooming 36,000 kilometers above Earth, shrugging off radiation bursts that’d fry your laptop in seconds, all while sipping power from a solar panel thinner than a credit card. That’s the everyday magic of space electronics—the guts of satellites and spacecraft that keep our world connected and our curiosity about the cosmos alive. But designing and building these marvels? It’s a high-stakes game where the rules are brutal, and the penalties for failure are cosmic.
For you—designers crafting circuits and decision-makers steering budgets and timelines—space electronics aren’t just a job; they’re a frontier that tests every ounce of ingenuity and grit. Let’s unpack the real challenges, spotlight some hard-earned wins, and see what’s cooking for the future, all with a lens on the nitty-gritty details that matter to your work.
What Are Space Electronics, Really?
Space electronics are the lifeblood of every orbiting satellite and far-flung spacecraft. Think radiation-resistant microprocessors in the Hubble Space Telescope, gyroscopic sensors guiding SpaceX’s Starlink constellation, or power regulators keeping the Mars Perseverance rover chugging along. These components handle navigation, data crunching, and communication—tasks we take for granted until you realize they’re happening in a void where a single hiccup can cost billions.
Unlike the chips in your smartwatch, which might konk out if you drop it in the sink, space electronics face a gauntlet of cosmic chaos. They’re custom-built warriors, and the stakes couldn’t be higher—whether it’s delivering GPS signals or snapping photos of Jupiter’s moons.
The Big Challenges: Where Space Pushes Electronics to the Brink
Building electronics for space is like designing a Formula 1 car that has to race through a hurricane, on a budget, with no pit stops. The challenges are relentless, and the examples below show just how wild it gets.
1. The Harsh Space Gauntlet
Space is a hostile beast. Take radiation: a single solar flare can blast electronics with 1,000 rads of energy—equivalent to 100,000 chest X-rays, according to NASA’s radiation studies. The Hubble’s Wide Field Camera 3 has seen its fair share of bit-flips from cosmic rays, requiring error-correction software to keep images crisp.
Then there’s the thermal nightmare. The International Space Station (ISS) swings between -120°C in shadow and 120°C in sunlight every 90 minutes. Most commercial chips would crack under that strain, but space-grade ones—like those in the ISS’s avionics—use ceramic packaging and thermal coatings to endure. And the vacuum? No air means heat only escapes through radiation or conduction, a problem that famously overheated early satellites like Telstar 1 in 1962 until engineers redesigned cooling systems.
Designers, this means your circuits need to be radiation-hardened gladiators, not just functional—they’ve got to thrive where earthly tech dies.
2. Reliability: When Failure Isn’t an Option
Space missions don’t get do-overs. When Voyager 1 launched in 1977, its electronics—built with 1970s tech—had to last decades. They’re still ticking 24 billion kilometers away, sending faint signals back to Earth. That’s not luck; it’s obsessive redundancy. Voyager’s computers have triple backups, cross-checking every command to avoid a single-point failure.
Contrast that with the Mars Climate Orbiter, lost in 1999 because a software glitch (a unit conversion error) sent it crashing into the planet. A $327 million lesson that reliability isn’t negotiable. For you, this means designing with triple-checks and planning for the long haul—some CubeSats now aim for 10-year lifespans with no maintenance.
3. Miniaturization: Small Size, Big Stakes
Launch costs are a brutal reality check—SpaceX’s Falcon 9 charges about $2,700 per kilogram to orbit. The Starlink satellites, each weighing around 260 kg, cram cutting-edge phased-array antennas and processors into a flat-panel design thinner than a laptop. Every gram shaved off saves thousands, but the electronics still need to perform like heavyweights.
Take the PhoneSat project: NASA stuffed smartphone guts into a 10cm CubeSat in 2013, proving you could orbit a $7,500 satellite. It worked, but scaling that simplicity to complex missions—like powering a lunar lander—is a designer’s puzzle. Decision-makers, you’re juggling lightweight materials like aluminum-lithium alloys against the cost of exotic composites. Every choice is a trade-off.
4. Supply Chain Headaches
Sourcing space-grade parts is a logistical circus. Radiation-hardened chips, like Intersil’s HS-6664RH SRAM, cost $1,000 apiece and come from a tiny pool of suppliers. Compare that to a consumer chip at $5. Then there’s obsolescence: the BAE Systems RAD750 processor, a space staple since 2001, powers over 150 missions (think Curiosity rover), but its PowerPC architecture is ancient by Earth standards. Engineers scour stockpiles or redesign mid-project when parts vanish.
The 2021 chip shortage hit space hard—delaying NASA’s Artemis program as suppliers prioritized consumer tech. For you, this means locking in suppliers early or betting on adaptable designs that don’t collapse when a part goes extinct.
5. Testing: Torture Chambers for Tech
Testing space electronics is a budget-busting marathon. Simulating radiation takes particle accelerators—NASA’s Goddard Space Flight Center spends millions annually blasting chips with protons. Thermal-vacuum chambers, like those at JPL, mimic space’s extremes, costing $50,000 per run. The James Webb Space Telescope’s electronics endured 100+ days of testing to prove they’d survive -233°C deep-space cold.
A real-world flop? The 1990 Intelsat VI satellite failed post-launch because a wiring fault slipped through rushed tests, stranding it in low orbit. For decision-makers, it’s a stark reminder: cut testing corners, and you’re rolling dice with a $200 million payload.
Solutions and Successes: How We’re Winning the Fight
The challenges are brutal, but the industry’s fighting back with brilliance. Here’s how, with cases that prove it works.
Radiation-Hardened Ingenuity
Rad-hard chips are the MVPs. The RAD750, mentioned earlier, shrugs off 1 million rads—100 times more than a typical chip—using triple-modular redundancy (TMR). It’s in Curiosity, Juno, and more, keeping missions alive. Newer tricks, like Xilinx’s radiation-tolerant FPGAs in SpaceX’s Starlink, let engineers reprogram chips mid-flight, adapting to unexpected cosmic hits.
Materials That Shine
Gallium nitride (GaN) is a rockstar—50% lighter than silicon and 10 times more radiation-resistant. It powers the European Space Agency’s Solar Orbiter, launched in 2020, which stares down the Sun’s fury at 42 million kilometers. Silicon carbide (SiC) is another gem, handling 600°C in NASA’s Venus rover prototypes. These materials cost a fortune—GaN wafers hit $500 each—but they’re game-changers.
Modular Smarts
Modularity saved the day for the ISS. When its Data Management System crashed in 2017, swappable electronics boxes got it back online fast. Now, companies like Planet Labs use modular CubeSats—300+ in orbit—swapping parts between launches to keep costs under $500,000 per bird. It’s Lego for space, and it’s brilliant.
AI and Automation Power-Up
AI’s no gimmick here. Lockheed Martin uses it to optimize F-35 avionics layouts, a trick now bleeding into space. xAI’s own tech helps simulate radiation effects, cutting test times by 30%. Automation? JPL’s cleanrooms assemble chips with robotic precision, slashing human error. It’s like having a genius robot sidekick.
Case Studies That Inspire
The James Webb Space Telescope, launched 2021, is a masterclass—its Near-Infrared Camera’s electronics survived 1.5 million kilometers of radiation to snap the universe’s oldest galaxies. Or look at SpaceX’s Starlink: 4,000+ satellites by 2025, each with electronics mass-produced for under $1 million a pop. These wins show what’s possible when innovation meets necessity.
The Future: What’s Next for Space Electronics
The horizon’s buzzing. Quantum computing could shrink processors 100-fold—DARPA’s already testing quantum chips for orbit by 2030. 3D printing’s real: NASA printed a copper antenna in 2022, hinting at on-demand spacecraft parts. And with SpaceX aiming for 12,000 Starlink birds, commercial demand’s forcing costs down—rad-hard chips might drop 20% in price by 2030, per industry forecasts.
Sustainability’s on the radar too. The European Space Agency’s Clean Space initiative pushes biodegradable circuits to cut debris—imagine electronics that dissolve after a mission. It’s sci-fi turning real.
Your Turn: Shaping the Cosmic Future
Space electronics are a wild ride—radiation, budgets, and all. From Voyager’s 47-year marathon to Starlink’s orbit swarm, every challenge spawns a breakthrough. Designers, you’re crafting the DNA of tomorrow’s missions. Decision-makers, your calls on testing and materials decide what flies or flops.
Dig into NASA’s rad-hard specs, track SpaceX’s next launch, or brainstorm with peers on X. The cosmos is calling, and your work’s the key. Where will you take it next?