Smart Manufacturing Applications in Electronics Metal Fabrication
Electronics development is an industry where precision and efficiency are non-negotiable. Whether you’re designing a new consumer gadget or an industrial control unit, the metal components used in enclosures, heat sinks, and connectors must be fabricated with exacting standards.
2/26/20254 min read
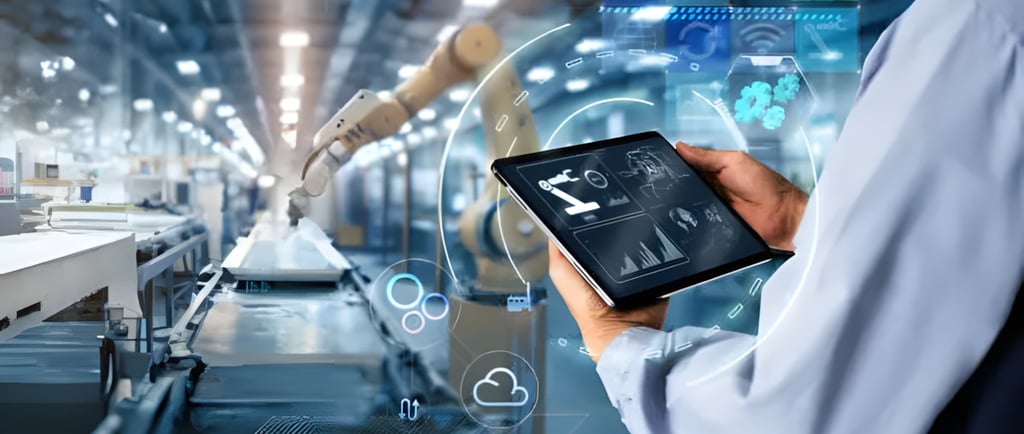
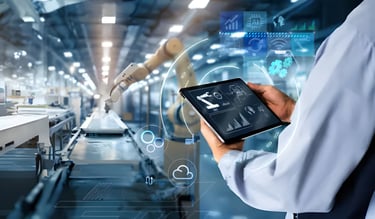
How Data-Driven Techniques and IoT Enhance Efficiency and Precision
Introduction
Electronics development is an industry where precision and efficiency are non-negotiable. Whether you’re designing a new consumer gadget or an industrial control unit, the metal components used in enclosures, heat sinks, and connectors must be fabricated with exacting standards. Yet, traditional metal fabrication methods often involve high material waste, inefficiencies, and production bottlenecks.
Enter smart manufacturing. With data-driven techniques, IoT-enabled monitoring, and AI-powered decision-making, metal fabrication is undergoing a transformation. For designers and decision-makers, understanding these advancements can mean the difference between a sluggish, error-prone supply chain and a streamlined, cost-effective production line.
In this article, we’ll explore how smart manufacturing is enhancing precision, reducing costs, and ensuring higher product reliability in electronics metal fabrication.
The Evolution of Metal Fabrication in Electronics Manufacturing
Traditional vs. Modern Metal Fabrication
Metal fabrication has long been a crucial part of electronics manufacturing, involving processes such as stamping, CNC machining, laser cutting, and welding. Historically, these methods relied heavily on manual operation and human expertise. While skilled craftsmanship played a crucial role, traditional fabrication methods often suffered from:
Inconsistencies in quality due to manual handling
High material waste from inefficient cutting and machining
Extended production times leading to delays in product launches
Unexpected downtimes due to reactive rather than proactive maintenance
With smart manufacturing, these inefficiencies are being addressed using real-time data, automation, and predictive analytics, allowing for seamless and precise metal fabrication.
Key Technologies Driving Smart Manufacturing
Smart manufacturing isn’t a single technology but a combination of multiple innovations that work together to create an interconnected, efficient system. Here are the key drivers:
1. Internet of Things (IoT) for Real-Time Monitoring
IoT sensors embedded in fabrication machines provide real-time data on performance, temperature, pressure, and wear. This enables manufacturers to:
Detect anomalies before they cause defects
Reduce unplanned downtime with predictive maintenance
Track production output to optimize workflows
2. Artificial Intelligence (AI) & Machine Learning
AI is revolutionizing quality control and process optimization in metal fabrication. By analyzing historical data, AI can:
Identify defects early by recognizing patterns that lead to faults
Optimize machining parameters for reduced waste and faster production
Automate decision-making in production scheduling and resource allocation
3. Big Data & Analytics
Data is a powerful tool in manufacturing. With the integration of big data analytics:
Production trends can be analyzed to enhance efficiency
Material usage can be optimized to minimize waste
Costs can be predicted and controlled more accurately
4. Automation & Robotics
CNC machining, robotic welding, and automated laser cutting have significantly improved fabrication speed and consistency. Robots can:
Work with high precision without fatigue
Handle repetitive tasks, reducing human error
Improve workplace safety by reducing exposure to hazardous environments
5. Digital Twin Technology
Digital twins create a virtual model of the physical fabrication process, allowing manufacturers to:
Simulate production runs to detect potential issues
Optimize designs before physical production begins
Enhance predictive maintenance by analyzing virtual models
Smart Manufacturing Applications in Metal Fabrication
The real-world impact of these technologies is already visible in several key applications:
1. Automated CNC Machining
CNC machines equipped with AI can optimize toolpaths dynamically, reducing machining time and extending tool life. This is especially valuable for fabricating aluminum or stainless-steel enclosures, where precision is critical.
2. Smart Laser Cutting & Welding
IoT-enabled laser cutters adjust parameters in real time based on material thickness and environmental conditions, ensuring clean cuts and minimal waste. Similarly, robotic welding systems use AI to adapt to variations in joint alignment, reducing defects in electronic component housings.
3. IoT-Enabled Predictive Maintenance
Rather than waiting for machines to fail, predictive maintenance uses IoT sensors to track machine wear and alert technicians before breakdowns occur. This reduces downtime and extends machine lifespan.
4. Supply Chain Optimization
Data-driven inventory systems ensure materials are stocked efficiently. If a fabrication plant predicts a surge in orders, automated procurement systems adjust inventory levels accordingly, preventing shortages or overstocking.
5. Cloud-Based Manufacturing Execution Systems (MES)
Cloud-based MES solutions provide real-time visibility into production, allowing managers to:
Track work-in-progress fabrication
Monitor machine efficiency remotely
Make data-backed decisions to improve throughput
Benefits of Smart Manufacturing in Electronics Metal Fabrication
For designers and decision-makers in electronics manufacturing, the benefits of smart metal fabrication are game-changing:
✅ Increased Production Efficiency: Automated processes reduce cycle times and eliminate bottlenecks.
✅ Higher Precision & Consistency: AI-driven systems ensure every part meets exact specifications.
✅ Lower Material Waste: Data-driven optimizations cut down on scrap and excess material use.
✅ Improved Quality Control: Sensors and AI detect defects before they reach final assembly.
✅ Faster Time-to-Market: Real-time monitoring and automation accelerate product development.
✅ Flexibility for Customization: Small-batch and on-demand production become more feasible.
Challenges and Considerations in Adopting Smart Manufacturing
Despite its advantages, transitioning to smart manufacturing comes with its own challenges:
High Initial Investment: Smart manufacturing requires investment in IoT sensors, AI software, and automation equipment.
Cybersecurity Risks: With more connected devices, the risk of cyberattacks increases.
Workforce Training Needs: Employees must be trained to operate and maintain smart systems.
Integration with Legacy Systems: Older machinery may require upgrades or retrofitting.
For decision-makers, careful planning and phased implementation can mitigate these challenges and maximize ROI.
Future Trends in Smart Metal Fabrication
As technology evolves, new trends are emerging that will further revolutionize metal fabrication:
🔹 5G for Faster Industrial Connectivity: Enabling real-time data exchange between machines and cloud systems.
🔹 AI-Powered Generative Design: Using AI to optimize material usage and create innovative designs.
🔹 Additive Manufacturing (3D Printing): Expanding the use of metal 3D printing for complex electronics components.
🔹 Blockchain for Supply Chain Transparency: Enhancing security and traceability of materials.
Conclusion
The world of electronics metal fabrication is evolving, and smart manufacturing is at the heart of this transformation. By leveraging IoT, AI, automation, and big data, companies can achieve higher efficiency, better product quality, and faster time-to-market. While challenges exist, the long-term benefits far outweigh the initial hurdles.
For designers and decision-makers, now is the time to explore how smart manufacturing can enhance your production capabilities. Whether it’s reducing material waste, improving precision, or streamlining your supply chain, embracing these technologies will help you stay ahead in the competitive electronics industry.
Are you ready to integrate smart manufacturing into your fabrication processes? The future is here—it's time to take advantage of it!