Selecting Materials for Electronics Metal Fabrication: A Designer’s Guide
When designing and manufacturing electronic products, metal selection is often an overlooked aspect—until issues arise. The right metal can make all the difference in terms of performance, durability, and cost-efficiency.
2/25/20254 min read
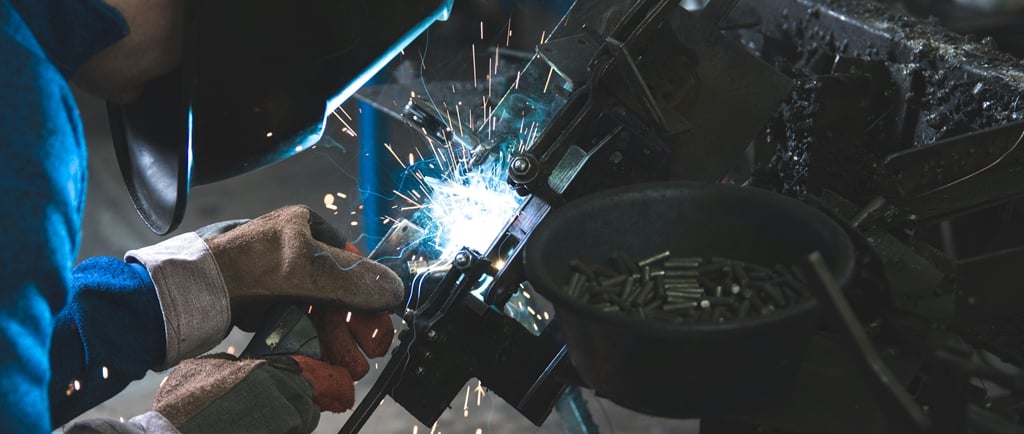
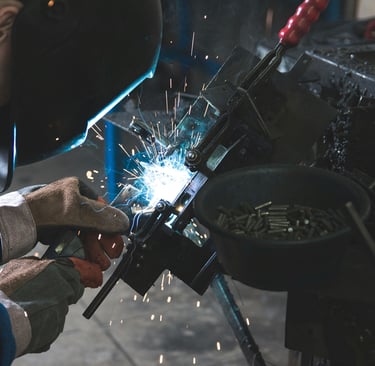
When designing and manufacturing electronic products, metal selection is often an overlooked aspect—until issues arise. The right metal can make all the difference in terms of performance, durability, and cost-efficiency. Whether you're designing enclosures, heat sinks, connectors, or structural components, choosing the best material impacts everything from thermal management to electrical conductivity and corrosion resistance.
For designers and decision-makers, balancing functionality with cost is a constant challenge. Should you go with aluminum for its lightweight properties? Is stainless steel worth considering for durability? And how does copper fit into the equation? In this article, we’ll explore the most commonly used metals in electronics fabrication, their key properties, and how to select the best one for your specific application.
1. Key Considerations for Metal Selection
Before diving into specific materials, let’s break down the main factors you should evaluate when selecting metals for your electronics projects.
Electrical Conductivity
If your application involves electrical components—such as PCBs, shielding, or power distribution—conductivity is a primary concern. Copper, for example, is the gold standard for electrical applications, while aluminum provides a balance of conductivity and affordability.
Thermal Properties
Heat dissipation is critical in electronics. Overheating can lead to reduced performance and early failure. Metals with high thermal conductivity, such as aluminum and copper, are preferred for heat sinks and thermal shielding.
Mechanical Strength & Durability
Structural components, enclosures, and support brackets need to withstand mechanical stress. Stainless steel is one of the strongest metals available, while aluminum offers a balance of strength and weight.
Corrosion Resistance
Electronic devices often face moisture, humidity, and environmental exposure. Metals like stainless steel and anodized aluminum resist corrosion well, making them ideal for enclosures used in outdoor or industrial settings.
Machinability & Fabrication Ease
Your chosen metal should be easy to cut, machine, bend, or weld based on your production process. Aluminum is one of the easiest metals to machine, while stainless steel is more challenging and requires specialized tools.
Cost Considerations
Budget constraints play a role in every project. Copper, while highly conductive, is expensive, whereas aluminum provides a more cost-effective alternative. Stainless steel is pricier but may be justified in applications requiring high durability.
2. Common Metals Used in Electronics Fabrication
Now that we’ve covered key selection criteria, let’s examine the most commonly used metals and their suitability for various applications.
a. Aluminum
Aluminum is widely used in electronics due to its lightweight nature, excellent thermal conductivity, and resistance to corrosion. It’s relatively easy to machine, making it a favorite for fabricating enclosures, heat sinks, and structural frames.
Pros:
Lightweight and strong
Good thermal conductivity (ideal for heat dissipation)
Cost-effective compared to copper and stainless steel
Corrosion-resistant, especially when anodized
Easy to machine and form
Common Applications:
Electronic enclosures and housings
Heat sinks for LEDs, CPUs, and power components
Structural frames for electronic devices
Lightweight brackets and mounts
b. Stainless Steel
If durability is a top priority, stainless steel is an excellent choice. It’s strong, corrosion-resistant, and can withstand harsh environments. However, its electrical and thermal conductivity are lower compared to aluminum and copper.
Pros:
Extremely strong and impact-resistant
Highly resistant to corrosion and rust
Aesthetically appealing (used in high-end consumer electronics)
Cons:
Heavier than aluminum
More challenging to machine
Higher cost compared to aluminum
Common Applications:
Rugged enclosures for industrial and outdoor electronics
High-end consumer electronics (smartphones, laptops)
Connectors and mechanical fasteners
c. Copper
Copper is the best conductor of electricity among commonly used metals, making it the go-to choice for electrical wiring, PCB traces, and EMI shielding. However, it is expensive and prone to oxidation if not properly coated.
Pros:
Highest electrical conductivity of all metals (except silver)
Excellent thermal conductivity for heat dissipation
Naturally antimicrobial (useful in medical electronics)
Cons:
Expensive
Susceptible to oxidation and corrosion if not coated
Heavier than aluminum
Common Applications:
Printed circuit boards (PCBs)
Electrical connectors and bus bars
RF shielding for sensitive electronics
High-performance heat sinks
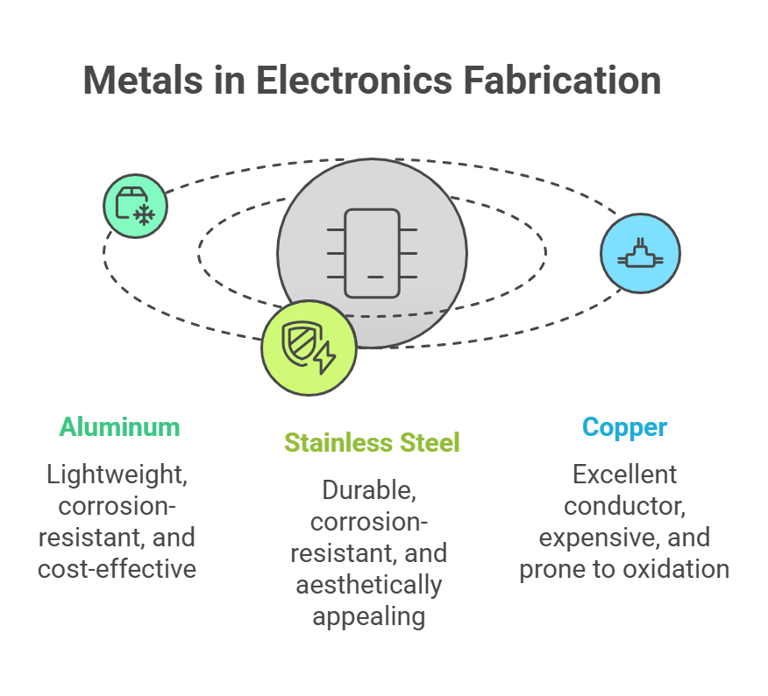
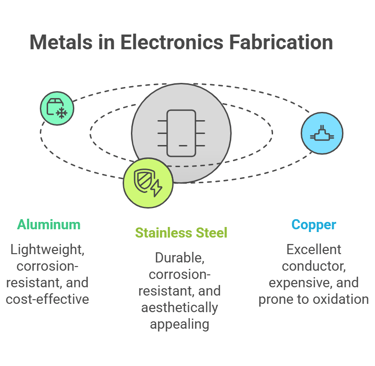
3. Alternative & Specialty Metals
In some cases, specialized metals offer unique advantages that justify their higher cost or specialized handling.
Brass – Offers good conductivity and corrosion resistance; used in connectors and terminal blocks.
Titanium – Extremely strong and lightweight but expensive; used in aerospace and medical electronics.
Nickel Alloys – Used in shielding applications and high-temperature environments.
4. Choosing the Right Metal for Your Application
With so many options, how do you determine the best metal for your electronics project? Here are some practical guidelines:
Define Your Priorities: Identify whether conductivity, strength, corrosion resistance, or cost is your top concern.
Consider Manufacturing Processes: If machining, welding, or bending is required, choose metals that work well with your fabrication methods.
Think About End-Use Environment: Will the product face moisture, chemicals, or extreme temperatures? Stainless steel or anodized aluminum may be better for harsh conditions.
Balance Cost vs. Performance: While copper is ideal for conductivity, aluminum might be a more budget-friendly option for mass production.
Explore Surface Treatments: Anodizing, plating, and coating can enhance corrosion resistance and aesthetics.
Conclusion
Selecting the right metal for electronics fabrication is a crucial step that affects performance, durability, and cost. Aluminum, stainless steel, and copper each have their strengths and trade-offs, and the right choice depends on the specific requirements of your design. Whether you're building an enclosure, heat sink, or electrical component, taking the time to evaluate material properties will help you achieve a reliable and cost-effective final product.
For designers and engineers working on electronics development, the key takeaway is clear: don’t treat material selection as an afterthought. The right metal can enhance efficiency, longevity, and performance, ensuring your product stands out in a competitive market.