The Role of 3D Printing in Modern Electronics Manufacturing
Electronics manufacturing has always been at the forefront of innovation, evolving from manual circuit assembly to highly automated production lines. Today, another transformative technology is making waves—3D printing, or additive manufacturing.
2/15/20254 min read
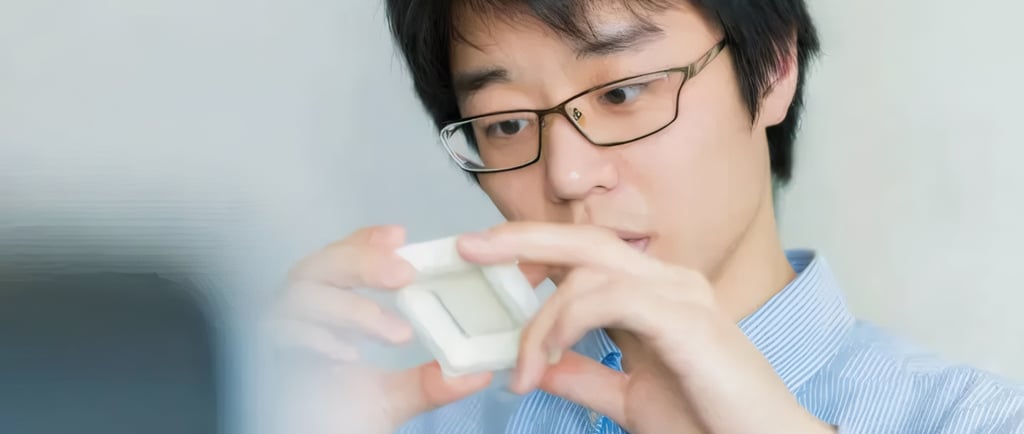
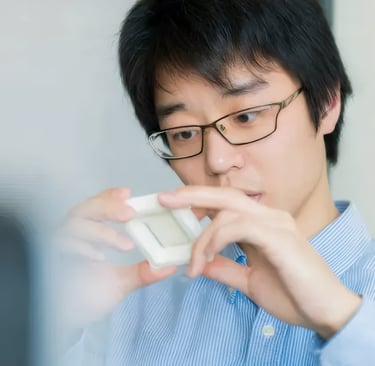
Electronics manufacturing has always been at the forefront of innovation, evolving from manual circuit assembly to highly automated production lines. Today, another transformative technology is making waves—3D printing, or additive manufacturing. While initially popularized for prototyping, 3D printing is now making inroads into end-use electronics manufacturing, offering designers and decision-makers an agile, cost-efficient, and highly customizable approach.
For electronics product designers, engineers, and project managers, 3D printing presents an opportunity to rethink product development, speed up iterations, and even create entirely new types of components. This article explores how 3D printing is shaping the electronics industry, from rapid prototyping to fully functional electronic components.
Understanding 3D Printing in Electronics
Before diving into its applications, let's briefly understand how 3D printing works in the context of electronics.
Unlike traditional subtractive manufacturing, which carves parts out of raw material, 3D printing builds objects layer by layer. Various printing technologies are now used in electronics, including:
Stereolithography (SLA) and Digital Light Processing (DLP): Excellent for microfabrication, used in precise component housings.
Fused Deposition Modeling (FDM): Ideal for prototyping enclosures and fixtures.
Selective Laser Sintering (SLS): Used for functional, durable plastic parts.
Direct Ink Writing (DIW) and Aerosol Jet Printing: Enable the direct printing of conductive materials, creating electronic circuits and flexible PCBs.
Each of these methods serves different purposes, from housing designs to embedded circuit fabrication, making 3D printing a versatile tool in the hands of electronics designers.
Key Applications of 3D Printing in Electronics Manufacturing
1. Prototyping and Rapid Design Iteration
One of the biggest advantages of 3D printing in electronics is the ability to iterate quickly. Traditional prototype manufacturing involves long lead times, costly tooling, and significant setup investments. With 3D printing, engineers can:
Print and test multiple design variations within days instead of weeks.
Reduce costs by eliminating the need for expensive molds.
Get functional prototypes that closely resemble final production units.
For designers, this means more room for innovation, enabling quick adjustments based on performance testing and user feedback.
2. 3D Printed Circuit Boards (PCBs)
Traditionally, PCB fabrication involves photolithography, etching, and multiple chemical processes. 3D printing introduces a new paradigm:
Printed conductive inks allow circuit traces to be directly printed onto substrates.
Multi-layered 3D-printed PCBs can integrate complex wiring without the need for separate layers.
Flexible PCBs can be printed on substrates that conform to different shapes, ideal for wearables and IoT devices.
These advancements offer designers a new level of freedom, allowing for unconventional form factors and embedded electronics within mechanical structures.
3. Customized Enclosures and Housings
Electronics product aesthetics and ergonomics are just as important as their functionality. 3D printing enables the creation of:
Unique, highly customized casings tailored for specific applications.
Lightweight, complex enclosures that would be impossible or costly with traditional manufacturing.
Integrated enclosures with embedded features, such as clips or venting, reducing assembly steps.
For startups and companies looking to differentiate their products, 3D printing offers an easy way to produce striking, functional enclosures without committing to mass production tooling.
4. Embedded Electronics and Structural Integration
One of the more futuristic applications of 3D printing in electronics is printing structural components that have electronics built into them. This means:
Sensors, circuits, and antennas can be embedded directly within a product’s structure.
Fewer connectors and assembly steps are needed, reducing product complexity and failure points.
Printed batteries and energy storage components can be integrated seamlessly.
This approach not only enhances product durability but also opens up possibilities for ultra-thin, lightweight electronics in aerospace, medical, and consumer applications.
5. Microelectronics and Miniaturization
Electronics are shrinking, and 3D printing is helping to drive that trend. Micro 3D printing technologies allow the creation of:
Ultra-small electronic components, ideal for hearing aids, medical implants, and smart wearables.
Microfluidic devices that integrate electronic and mechanical functions for biotech applications.
For engineers working on cutting-edge, space-constrained designs, 3D printing provides a way to prototype and manufacture intricate microstructures that would be challenging with traditional methods.
6. Sustainable and Eco-friendly Electronics Manufacturing
With the increasing emphasis on sustainability, companies are seeking ways to reduce waste and improve resource efficiency. 3D printing contributes by:
Minimizing material waste—only the required material is used.
Reducing carbon footprints—localized manufacturing eliminates the need for long supply chains.
Enabling repair and replacement parts—instead of discarding entire products, companies can 3D print spare parts on demand.
This sustainable approach aligns well with modern consumer expectations and regulatory pressures for greener electronics production.
Advantages of 3D Printing in Electronics Manufacturing
Cost Efficiency: Lower development costs by reducing tooling, labor, and material waste.
Speed and Agility: Faster iterations and quicker time to market.
Design Freedom: Enables more innovative and complex geometries.
Supply Chain Optimization: Reduces dependence on external suppliers, enhancing production resilience.
Sustainability: Supports circular economy models and eco-friendly manufacturing.
For decision-makers, these advantages translate to better margins, faster turnaround times, and enhanced product differentiation.
Challenges and Limitations
Despite its potential, 3D printing in electronics is not without challenges:
Material Limitations: Not all conductive materials are printable yet.
Scalability Issues: Mass production with 3D printing remains expensive and slow compared to injection molding or PCB mass fabrication.
Regulatory Compliance: 3D-printed electronics must meet industry standards, which can be a hurdle in safety-critical applications.
Technological Maturity: While progress is rapid, many applications are still in the R&D phase.
However, ongoing research and advancements in materials and print speeds are gradually overcoming these hurdles, making 3D printing more viable for a wider range of applications.
Future Trends and Innovations
Looking ahead, we can expect:
More flexible, stretchable, and biocompatible printed electronics for wearables and medical applications.
Integration of AI and automation to optimize 3D printing processes.
New printable materials that improve conductivity, strength, and durability.
Hybrid manufacturing approaches that combine traditional methods with 3D printing.
Scalability improvements as faster and more cost-effective 3D printing technologies emerge.
Conclusion
For electronics designers and decision-makers, 3D printing is no longer just a prototyping tool—it is an enabler of innovation. From customized enclosures to printed PCBs and embedded electronics, this technology is transforming how products are designed and manufactured.
While challenges remain, the trajectory is clear: 3D printing is set to play a significant role in the future of electronics manufacturing. Companies that embrace this shift will gain a competitive edge, enabling faster innovation, cost efficiency, and sustainability in their product development cycles.
For those looking to integrate 3D printing into their electronics projects, now is the time to explore its possibilities. The future of electronics is being printed—layer by layer.