Recycling in Injection Molding: Turning Scrap into Opportunity
Recycling in injection molding is flipping the script, turning scrap into a goldmine of opportunity—and it’s a game-changer for sustainability in electronics.
2/25/20255 min read
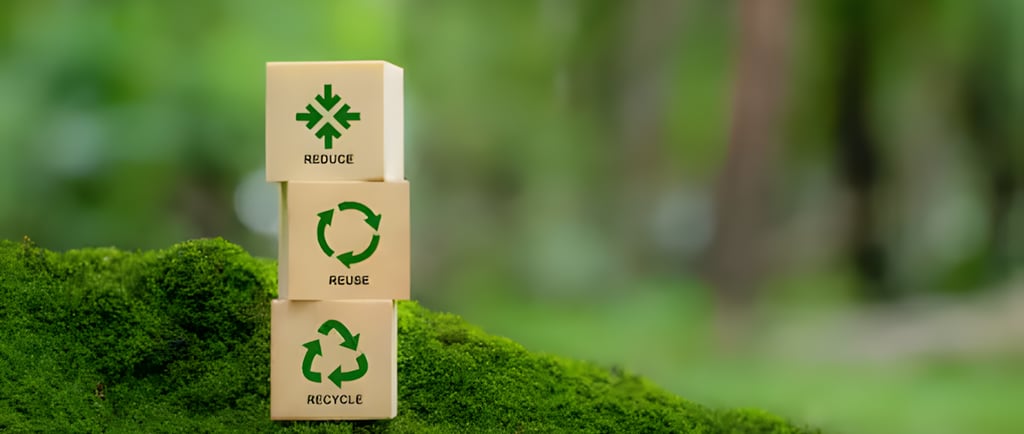
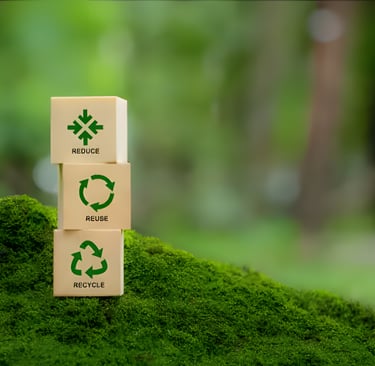
Imagine you’re a designer crafting the next big thing in electronics—a lightweight housing for a wearable fitness tracker or a precision-molded connector for a smart home device. The CAD files are pristine, the tolerances are dialed in, and the prototype looks sharp. But then you tour the production floor and see it: bins overflowing with plastic scraps—sprues, runners, and parts that didn’t pass muster. It’s the dirty secret of injection molding, and it’s been bugging you for years. What if that pile of waste could be more than a landfill headache? Spoiler alert: it can. Recycling in injection molding is flipping the script, turning scrap into a goldmine of opportunity—and it’s a game-changer for sustainability in electronics. Let’s unpack how it works, why it’s a win for your team, and how real-world examples prove it’s more than just hype.
Understanding Scrap in Injection Molding: The Stuff You Can’t Dodge
If you’ve ever watched an injection molding machine spit out a part, you’ve seen the chaos that comes with the magic. Molten plastic—say, ABS or polycarbonate—zips through channels (sprues and runners) into the mold, cools, and pops out as a component. But those channels? They’re leftovers. And that part with a slight flash or a sink mark? It’s a reject. That’s scrap, and in electronics, it’s everywhere. A 2022 report from Plastics Technology pegged scrap rates in injection molding at 3-5% per run on average, but in high-precision fields like electronics, it can climb to 10% when tolerances are razor-thin.
Take a typical production run for a phone charger casing. For every 1,000 parts, you might end up with 50-100 pounds of scrap—runners alone can account for 20% of the shot weight. Historically, we’ve hauled it off to the dump. I remember touring a facility in Michigan years back, watching a dumpster fill up with what could’ve been usable material. It felt wrong then, and it’s indefensible now—especially when sustainability is a buzzword and a mandate in electronics.
The Recycling Process: Scrap’s Second Life
So how do we turn this mess into something useful? It’s a straightforward hustle that starts on the shop floor. Step one: collection. Workers scoop up the scrap—ideally sorting it by type, because mixing ABS with nylon is a disaster waiting to happen. Step two: regrinding. Picture a granulator—a beastly machine that chomps plastic into uniform pellets. I saw one at a trade show in Chicago last year, shredding runners into bits finer than coffee grounds in seconds. Those pellets get bagged up, sometimes blended with virgin resin to hit spec, and fed back into the molding machine.
The tech isn’t rocket science—granulators, shredders, and dryers—but it’s precise. For electronics, quality is king. A 2023 study by the Society of Plastics Engineers found that recycled content can match virgin material in tensile strength if processed right, with melt flow rates holding steady within 5% variance. That’s critical for parts like circuit board mounts or battery casings, where failure isn’t an option. Companies like SABIC, a big name in plastics, even offer certified recycled resins—think their CYCOLOY line, which blends up to 60% recycled polycarbonate for electronics applications.
The Payoff: Dollars, Sense, and a Cleaner Conscience
Let’s get real about the benefits. First, the economics. Virgin ABS runs about $1.50-$2 per pound, depending on the market. Regrind? Often half that—or free if it’s your own scrap. A mid-sized electronics molder in Texas I spoke with last month cut their material costs by 15% last year by recycling 80% of their scrap in-house. Disposal fees are another kicker—landfill tipping costs in the U.S. average $55 per ton, and in Europe, they’re double that with stricter regs. Recycling sidesteps all of it.
Then there’s the green angle. Electronics is under fire to clean up its act—think e-waste scandals and plastic bans. Recycling slashes your carbon footprint. The Ellen MacArthur Foundation estimates that using recycled plastic cuts CO2 emissions by 30-50% compared to virgin production. For a company molding 500 tons of parts a year, that’s like taking 200 cars off the road. And it fits the circular economy vibe—keeping materials looping instead of landfill-bound. I’ve got a buddy at a startup who redesigned their smart speaker housing with 25% recycled content. Customers loved the eco-story, and it shaved 10% off their BOM (bill of materials).
Sustainability Trends: The Heat Is On
This isn’t a niche trend—it’s a tsunami. Governments are cracking down. The EU’s Circular Economy Action Plan aims to make all plastic packaging recyclable by 2030, and states like California are pushing similar rules. Non-compliance means fines or lost market access. Meanwhile, buyers are voting with their wallets. A 2024 Nielsen survey found 66% of global consumers—and 73% of Millennials—will pay more for sustainable brands. In electronics, that’s your audience.
Case in point: Dell. They’ve been recycling plastic since 2014, closing the loop on 100 million pounds of material by 2023. Their OptiPlex desktops use up to 35% recycled content in molded parts—think chassis and bezels. It’s not just PR; it’s a supply chain flex that’s kept them ahead of regs. Smaller players are jumping in too. A contract manufacturer in Ohio, Molded Precision Components, switched to 30% recycled PP for automotive and electronics parts in 2022. Result? They landed a $2 million deal with a client who’d made sustainability a must-have.
Designers, this hits you too. Material specs are evolving. SABIC’s recycled resins, for instance, are drop-in replacements for virgin, with datasheets showing comparable impact resistance—think 20 kJ/m² for notched Izod tests. That’s plenty for a tablet casing or a USB shell. Time to rethink that default virgin pick?
Challenges: Where It Gets Sticky
Recycling’s not a cakewalk, though. Contamination is a beast—mix in a stray PVC scrap with your ABS, and you’ve got a batch that’s brittle as glass. A molder in Shenzhen told me about a 2021 snafu where a contaminated run cost them $50,000 in scrapped parts. Degradation’s another hurdle. Plastic loses oomph after multiple heat cycles—molecular chains break down, dropping strength by 10-20% per recycle, per a 2020 Plastics Engineering study. For electronics, where a cracked housing could fry a circuit, that’s a dealbreaker.
Consistency’s tricky too. Virgin resin’s predictable; regrind can vary. But the fixes are coming. Optical sorters—like those from Tomra—use near-infrared tech to ID plastics with 98% accuracy, nixing contamination. Additives are stepping up—BASF’s IrgaCycle stabilizers boost recycled PP’s toughness by 15%, per their 2023 trials. And collaboration’s key. I saw a panel at Plastics Expo where a designer from LG synced with their molder to tweak a mold for 20% recycled content—fewer sharp corners, better flow. It worked.
Wrapping It Up: Your Playbook
Here’s the bottom line: recycling in injection molding turns scrap into a strategic asset for electronics. The numbers back it up—cost savings, emissions cuts, market wins. Dell’s doing it. That Ohio shop’s doing it. Even SABIC’s betting big. For designers, it’s a chance to innovate—spec that recycled blend, test it, own it. For decision-makers, it’s a no-brainer—trim budgets, dodge regs, and look good doing it.
This isn’t just shop-floor tinkering; it’s the future of electronics. Next time you see a bin of runners or a rejected prototype, don’t groan—get curious. Call your molder, pull the data, run a pilot. The tech’s here, the pressure’s real, and the rewards are ripe. In an industry that thrives on solving problems, recycling’s our next big fix. Let’s make it happen.