Overcoming Challenges in Electronics Metal Fabrication: A Guide for Designers and Decision-Makers
Metal fabrication in electronics isn’t just a process; it’s a high-wire act where precision, quality, and speed must balance flawlessly. Yet, challenges like maintaining tolerances, dodging material defects, and keeping production on track can trip up even the best teams.
2/26/20256 min read
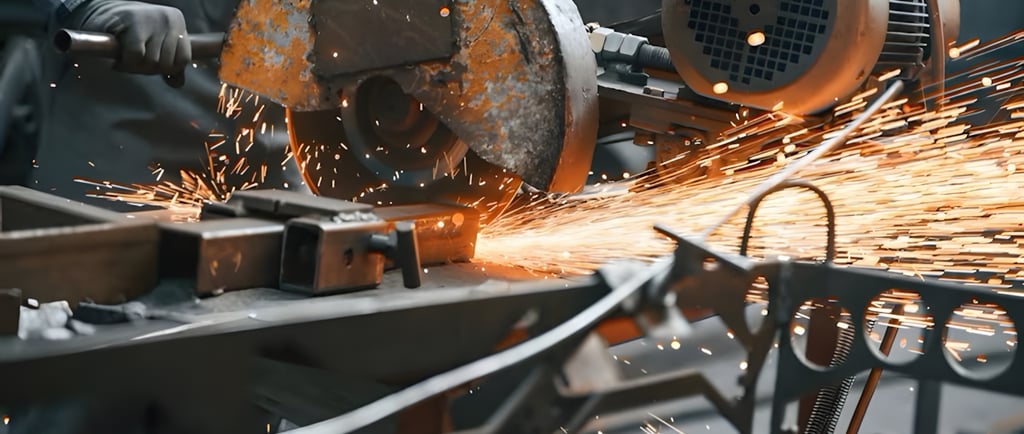
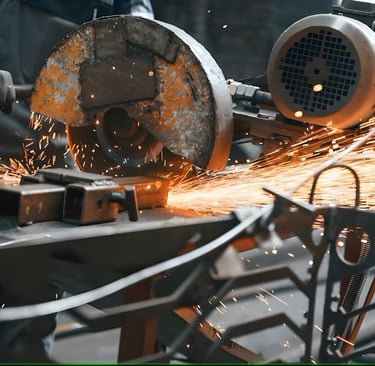
If you’re a designer or decision-maker in electronics development, you know the stakes are high. The components you create—whether they’re tiny connectors in a smartphone or rugged enclosures for industrial sensors—have to be perfect. Not “pretty good,” not “close enough,” but perfect. The tolerances are tighter than a drum, the materials can’t have a single flaw, and heaven forbid a production delay throws your timeline into chaos.
Metal fabrication in electronics isn’t just a process; it’s a high-wire act where precision, quality, and speed must balance flawlessly. Yet, challenges like maintaining tolerances, dodging material defects, and keeping production on track can trip up even the best teams. I’ve seen it firsthand—years in the industry have taught me that these hurdles aren’t just technical; they’re personal. They keep you up at night, wondering how to get it right.
In this article, we’re diving into these common pain points—tight tolerances, material defects, and production delays—and unpacking solutions that work. This isn’t theory from a textbook; it’s practical advice for folks like you who live and breathe electronics development. Let’s roll up our sleeves and tackle these challenges together.
Understanding the Big Three Challenges
Before we fix anything, let’s get real about what we’re up against. These aren’t abstract problems—they’re the headaches you deal with every day.
Tight Tolerances: The Precision Puzzle
Picture this: you’re designing a circuit board connector that needs to fit into a slot thinner than a human hair. One micrometer off, and it’s useless. Tolerances in electronics metal fabrication are brutal because the margins for error are basically nonexistent. Tool wear can throw off your cuts, temperature swings can make metal expand just enough to ruin a batch, and even the steadiest hands (or machines) struggle to keep up. For designers, this is a creativity-killer—you’re dreaming up the next big thing, but the physics of metal keeps slapping you back to reality.
Material Defects: The Hidden Saboteurs
Then there’s the metal itself. You might start with a pristine sheet of aluminum or copper, but tiny flaws—porosity, inclusions, or surface scratches—can sneak in and wreck everything. These defects aren’t just cosmetic; they can weaken a component, mess with conductivity, or cause failures down the line. I once worked with a team that lost weeks tracking down a short circuit, only to find it was a microscopic bubble in the metal. For decision-makers, this is a budget nightmare—rework, scrap, and delays pile up fast.
Production Delays: The Clock That Never Stops
And don’t get me started on delays. You’ve got a deadline—say, a product launch at CES—and suddenly your supplier’s late with raw materials, or a machine goes down, or half a batch needs redoing because of a tolerance slip. In electronics, time isn’t just money; it’s survival. The market moves fast, and if you’re not shipping, someone else is. For both designers and deciders, delays feel personal—like a punch to the gut after months of planning.
These challenges aren’t new, but they’re stubborn. The good news? They’re not unbeatable. Let’s break down how to tackle each one, step by step.
Solutions to Tight Tolerance Challenges
When tolerances are tighter than your last deadline, you need tools and strategies that don’t mess around. Here’s how to keep precision on your side.
Advanced Machining: Your New Best Friend
If you’re not already leaning hard into CNC machining or laser cutting, it’s time to start. These aren’t just buzzwords—they’re game-changers. CNC machines can hit tolerances down to a few microns, and lasers can slice metal like butter without the wear you’d get from traditional tools. Pair that with a solid CAD setup, and you can simulate every move before the first cut. I’ve seen designers tweak a model in software, catch a tolerance issue, and save a whole production run from disaster. It’s like having a crystal ball for your shop floor.
Tooling That Lasts
Speaking of tools, they’re only as good as their upkeep. A worn-out bit or a dull blade can turn your tolerances into a guessing game. Regular calibration isn’t optional—it’s a lifeline. And don’t skimp on quality; invest in tools built for micro-scale work. I once saw a team switch to carbide-tipped bits and cut their rework rate in half. Decision-makers, this is where your budget calls matter—cheap tools cost more in the long run.
Keep It Cool
Heat is a silent killer of precision. Metal expands when it’s hot, and in a game of micrometers, that’s a dealbreaker. Set up a controlled environment—think air-conditioned rooms or cooling systems on your machines. One shop I visited even used heat-resistant alloys for critical parts to keep dimensions stable. It’s a small tweak with big payoffs.
Addressing Material Defects
Defects in your metal are like termites in a house—hard to spot until the damage is done. Here’s how to stop them before they start.
Pick the Right Stuff
It all begins with material selection. Go for high-purity metals from suppliers you trust, and demand certifications. Then test the heck out of it—ultrasonic scans, X-rays, whatever it takes to spot flaws early. I worked with a designer who insisted on pre-checking every batch of copper for a high-end audio project. It added a day upfront but saved weeks of troubleshooting later. Decision-makers, this is your call—quality in equals quality out.
Smarter Processes
Once you’ve got good metal, don’t let your process ruin it. Techniques like vacuum casting can cut down on porosity, and annealing relieves stress that leads to cracks. Surface finishing—polishing, plating, you name it—can smooth out imperfections and boost performance. I’ve seen a rough enclosure turn into a sleek, reliable component with just a little extra care at this stage.
Eyes Everywhere
Quality control isn’t a final step; it’s a constant companion. Inline inspection with AI or machine vision can catch defects mid-run, not after you’ve made 10,000 bad parts. Pair that with statistical process control—tracking trends in your data—and you’ll spot trouble brewing before it blows up. One team I know caught a batch of porous steel early because their system flagged a tiny spike in defect rates. That’s the kind of win that keeps you ahead.
Overcoming Production Delays
Delays are the enemy of every deadline-driven soul in electronics. Here’s how to keep the clock on your side.
Supply Chains That Don’t Snap
A flaky supplier can derail your whole operation. Build relationships with reliable ones, and keep a buffer stock for critical materials. Diversify your sources, too—one late shipment shouldn’t sink you. I once saw a decision-maker negotiate backup contracts with a second supplier just for peace of mind. When a hurricane hit their main vendor, they didn’t even blink.
Machines That Don’t Quit
Equipment downtime is a killer. Schedule preventive maintenance like it’s a sacred ritual—because it is. And if you’re feeling fancy, hook up IoT sensors for predictive maintenance. They’ll tell you a motor’s about to fail before it does. A shop I visited went from monthly breakdowns to near-zero just by listening to their machines. Designers, this keeps your prototypes rolling; deciders, it keeps your budget intact.
Work Smarter, Not Harder
Lean manufacturing isn’t just for car factories—it works here, too. Cut waste, streamline steps, and automate what you can. Robots don’t care about repetitive tasks, and they don’t call in sick. One team I know shaved days off their lead time by letting a bot handle simple cuts while the humans focused on the tricky stuff. It’s not about replacing people; it’s about freeing them up to shine.
Real-World Wins
Need proof this works? Picture a small firm making connectors for medical devices. They struggled with tolerances until they switched to laser cutting and CAD simulations—suddenly, their rejection rate dropped by 80%. Or take a big player in consumer electronics: they tackled defects with AI vision systems and went from scrapping 5% of their enclosures to under 1%. And delays? A startup I know automated their workflow and beat a competitor to market by a month. These aren’t fairy tales—they’re what happens when you fight smart.
Wrapping It Up
Overcoming challenges in electronics metal fabrication isn’t about luck—it’s about grit, smarts, and the right moves. Tight tolerances, material defects, and production delays can feel like unbeatable foes, but they’re not. With advanced machining, quality materials, and streamlined processes, you can turn headaches into victories. For designers, this means your vision comes to life as intended. For decision-makers, it’s a stronger bottom line and a team that delivers.
So, take a hard look at your setup. Where’s the weak spot? Start there—tweak a process, test a tool, talk to your crew. The solutions are in your hands, and the payoff is worth it: better components, happier customers, and a reputation that stands tall in a cutthroat industry. Let’s make it happen.