Nearshoring vs. Offshoring: Which Model Suits Your Electronics Business?
In today's electronics manufacturing landscape, choosing between nearshoring and offshoring isn't just a business decision – it's a strategic move that can make or break your product's success.
2/17/20254 min read
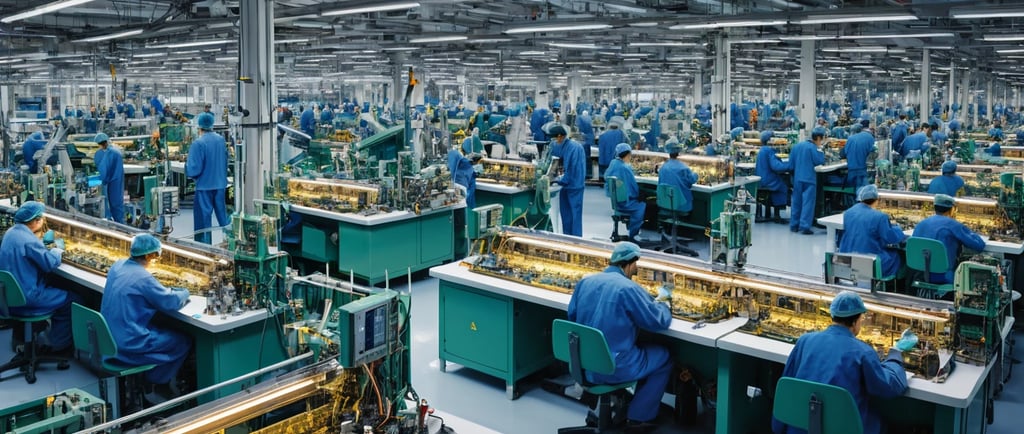
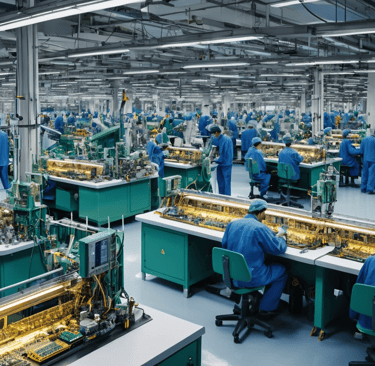
In today's electronics manufacturing landscape, choosing between nearshoring and offshoring isn't just a business decision – it's a strategic move that can make or break your product's success. As someone who's spent years working with electronics manufacturers across different continents, I've seen both triumph and tribulation in these choices. Let's dive into the nuances of both approaches and help you make an informed decision for your electronics business.
Introduction
Remember when "Made in China" was synonymous with electronics manufacturing? While China remains a powerhouse, the manufacturing landscape has evolved dramatically. Global events, from the pandemic to trade tensions, have pushed many electronics companies to reevaluate their manufacturing strategies. Just last month, I spoke with a medical device startup founder who was torn between Mexican nearshoring and Chinese offshoring for their new product line – a dilemma many of you might relate to.
Understanding Nearshoring in Electronics Manufacturing
Nearshoring means moving production to a neighboring country or region. For U.S. companies, this typically means Mexico or Canada. European firms often look to Eastern European countries or North Africa. The appeal? Imagine being able to hop on a two-hour flight to visit your manufacturing facility, rather than enduring a 15-hour journey across multiple time zones.
I recently visited a contract manufacturer in Guadalajara, Mexico – often called the "Silicon Valley of Mexico" – where several American electronics companies have set up shop. The facility manager, Miguel, shared how their U.S. clients can drive down for urgent prototype reviews or production troubleshooting. This proximity has proven invaluable during critical product launches.
Exploring Offshoring in Electronics Production
Despite the anti-globalization sentiment we've witnessed in recent years, the "Made in China" advantage remains compelling. During my recent visit to Shenzhen, I was struck by how the electronics ecosystem has matured. It's not just about lower costs anymore – it's about the concentration of expertise, suppliers, and infrastructure that's been built over decades.
Take the story of a wireless charging startup I advised. They initially balked at Chinese manufacturing due to IP concerns but eventually chose Shenzhen for their production. Why? Because within a one-mile radius of their chosen factory, they found suppliers for every component they needed, from custom magnets to injection-molded parts. This ecosystem efficiency is hard to replicate elsewhere.
Comparative Analysis
Cost Considerations
Let's be real – cost matters. But it's not as straightforward as comparing hourly labor rates. A senior operations manager at a consumer electronics firm shared with me how their apparent savings from lower Chinese labor costs were partially offset by increased shipping costs and inventory carrying charges. However, their overall costs still remained 15-20% lower than nearshore alternatives, even after factoring in recent wage increases in China.
Quality Control and Standards
The old stereotypes about quality issues in offshore manufacturing need updating. Modern Chinese electronics manufacturers often boast state-of-the-art equipment and robust quality management systems. However, nearshoring offers the advantage of easier oversight. As one quality manager told me, "Being able to drive to our Mexican facility for surprise audits gives us peace of mind we never had with our Asian suppliers."
Supply Chain Dynamics
The pandemic taught us all hard lessons about supply chain vulnerability. Nearshoring can offer more resilient supply chains with shorter lead times. However, China's mature supply chain ecosystem remains unmatched. A product manager I know described it best: "In Shenzhen, if a supplier fails us, we can find three alternates before lunch. In other locations, it might take weeks."
Decision Factors for Electronics Businesses
Company Size and Scale
Your company's size significantly influences this decision. I've observed that smaller companies often benefit more from nearshoring's flexibility and personal attention. Larger operations with established processes and higher volumes can better absorb the complexity of offshore operations.
Product Complexity
For highly complex products requiring frequent engineering changes, nearshoring's quick response time can be invaluable. One medical device manufacturer saved months of development time by working with a Mexican partner who could turn around prototype iterations in days rather than weeks.
Industry-Specific Considerations
Consumer electronics often benefit from China's ecosystem, especially for high-volume products. However, industrial electronics manufacturers might find nearshoring more advantageous, particularly when customization and smaller batch sizes are required.
The Future Landscape
The Rise of Automation
Automation is gradually leveling the playing field between regions. A factory owner in Poland showed me how their highly automated PCB assembly line achieves costs competitive with manual assembly in Asia. This trend will continue to reshape the manufacturing landscape.
Geopolitical Factors
The ongoing trade tensions and regulatory changes can't be ignored. However, China's electronics manufacturing infrastructure has shown remarkable resilience. As one Chinese factory owner told me, "We've adapted to every challenge over the past 30 years. This is just another adaptation."
Making Your Decision
Here's a practical framework I've developed from working with numerous electronics companies:
For High-Volume Consumer Products:
Consider Chinese manufacturing if you can manage quarterly orders of 10,000+ units and have stable designs. The ecosystem advantages often outweigh other considerations.
For Complex, Lower-Volume Products:
Nearshoring often makes more sense, especially if you need frequent design iterations or have strict regulatory requirements.
For Startups and New Products:
Consider a hybrid approach – prototype and initial production runs nearshore, then transition to offshore once the design is stable and volumes increase.
Conclusion
The choice between nearshoring and offshoring isn't binary. Many successful electronics companies employ a hybrid approach, leveraging the strengths of both models. The key is understanding your specific needs and constraints.
Think about your product's lifecycle, volume projections, and engineering support requirements. Consider your company's resources for managing distant suppliers and your tolerance for longer lead times. Remember, what works for one product line might not work for another.
Personally, I've seen companies succeed with both models. The most successful ones chose their manufacturing strategy based on a clear-eyed assessment of their specific situation rather than following industry trends.
Looking ahead, we'll likely see continued evolution in both nearshoring and offshoring options. The key is staying flexible and building relationships that can adapt to changing circumstances. Whether you choose to manufacture in Guadalajara or Guangzhou, success lies in understanding and managing the unique challenges and opportunities each option presents.
Have you had experience with either nearshoring or offshoring? I'd love to hear about your experiences in the comments below. Your insights could help others in our community make better decisions for their electronics manufacturing needs.