Navigating Global Supply Chain Disruptions in Electronics Manufacturing
Whether it’s a semiconductor shortage delaying production or skyrocketing shipping costs eating into margins, the challenges seem endless. Electronics manufacturing has always been a complex puzzle, but recent global events—pandemics, trade wars, and geopolitical instability—have made it even trickier to piece together.
2/17/20254 min read
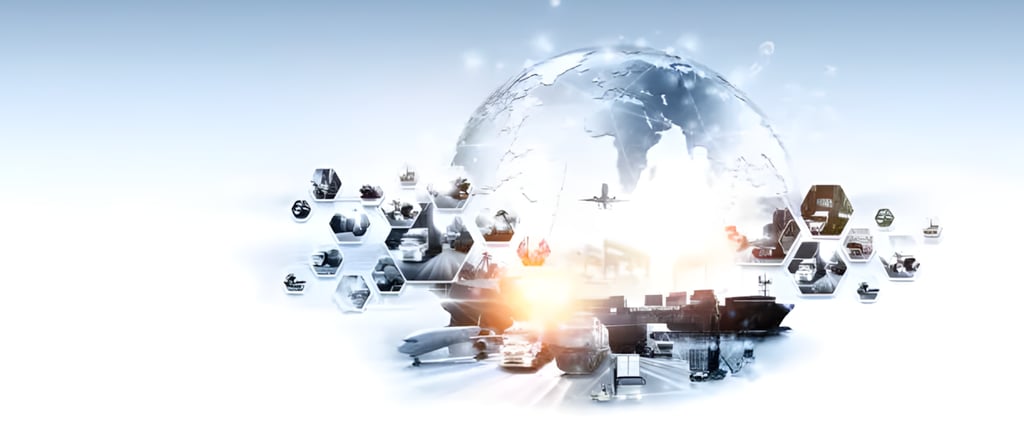
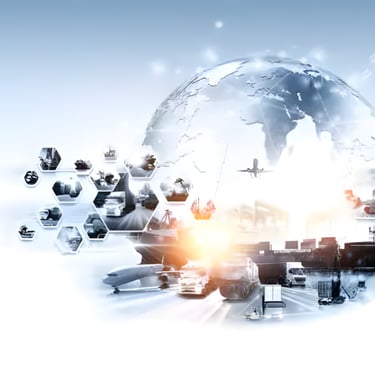
If you’re designing and developing electronic products, you’ve likely felt the impact of supply chain disruptions firsthand. Whether it’s a semiconductor shortage delaying production or skyrocketing shipping costs eating into margins, the challenges seem endless. Electronics manufacturing has always been a complex puzzle, but recent global events—pandemics, trade wars, and geopolitical instability—have made it even trickier to piece together.
However, challenges also present opportunities. Companies that adapt quickly and rethink their supply chain strategies can gain a competitive edge. In this article, we’ll explore the biggest disruptions in the global electronics supply chain and actionable strategies to navigate them.
1. Key Challenges in the Global Electronics Supply Chain
Component Shortages: The Chip Crisis and Beyond
The global semiconductor shortage has been one of the most severe supply chain disruptions in recent history. The demand for chips surged due to the digital transformation of various industries, but supply couldn’t keep up. Foundries were stretched thin, and lead times for microcontrollers, GPUs, and power management ICs jumped from weeks to months.
Beyond semiconductors, passive components, PCBs, and even basic connectors have faced shortages, affecting industries from automotive to consumer electronics.
Logistics Bottlenecks: Freight Costs and Shipping Delays
Even if you manage to source components, getting them delivered is another hurdle. The pandemic disrupted global shipping routes, leading to port congestion, container shortages, and unprecedented freight costs. A container that once cost $2,000 to ship from China to the U.S. surged to over $15,000 at its peak.
Companies relying on just-in-time (JIT) inventory management found themselves in a crisis when shipments were delayed, and production lines ground to a halt.
Geopolitical Tensions and Trade Policies
If you’re sourcing components from China, you’ve likely encountered rising tariffs and export restrictions. The U.S.-China trade war, combined with new regulations targeting technology exports, has made sourcing certain electronic components a legal and financial challenge. Additionally, shifts in manufacturing policies in the EU and India are pushing companies to rethink their global supply chains.
Environmental and Compliance Regulations
Governments worldwide are enforcing stricter sustainability and compliance regulations. The European Union’s Restriction of Hazardous Substances (RoHS) and China’s environmental policies have forced manufacturers to rethink their material choices. E-waste regulations are also pushing companies toward more sustainable designs, which sometimes require switching to new suppliers with compliant materials.
Supplier Dependence: The Danger of a Single Source
Many electronics companies have relied on a handful of key suppliers for critical components. But when those suppliers face factory shutdowns, labor strikes, or raw material shortages, the ripple effects can be devastating. The inability to pivot quickly leads to production halts and missed market opportunities.
2. Strategies to Mitigate Supply Chain Risks
Diversifying Suppliers and Manufacturing Hubs
Relying solely on Chinese manufacturers may no longer be the best strategy. Companies are shifting production to Southeast Asia, Mexico, and even bringing some manufacturing back to the U.S. and Europe.
Nearshoring vs. Offshoring: While offshoring to lower-cost regions reduces expenses, nearshoring to countries closer to your end market can reduce lead times and geopolitical risks.
Multi-supplier Strategy: Establishing relationships with multiple suppliers across different regions helps mitigate risks from localized disruptions.
Strengthening Inventory Management
The traditional just-in-time (JIT) model, which minimizes inventory to reduce costs, has proven risky in an era of supply chain disruptions. Many companies are now adopting a Just-in-Case (JIC) approach, maintaining buffer stocks for critical components.
Predictive Demand Forecasting: Leveraging AI-driven analytics can help forecast supply and demand more accurately, ensuring you don’t overstock or understock key components.
Strategic Stockpiling: Keeping a reserve of high-risk components (like semiconductors) can protect against sudden shortages.
Enhancing Supply Chain Visibility and Collaboration
Real-time data is critical to navigating supply chain risks. Companies are increasingly investing in IoT, blockchain, and ERP systems to enhance visibility.
IoT-enabled Tracking: Sensors provide real-time shipment tracking, ensuring you can react quickly to delays.
Blockchain for Transparency: Some manufacturers are using blockchain to verify supplier authenticity and track component origins, reducing risks of counterfeit parts.
Designing for Flexibility: Alternative Components and Manufacturing Processes
One way to reduce supply chain risks is by designing products with interchangeable components. For example:
Choosing alternative microcontrollers that can be sourced from multiple suppliers.
Using modular PCB designs that allow for alternative layouts with different components.
Selecting materials that comply with multiple environmental regulations to avoid last-minute redesigns.
Leveraging Government Policies and Incentives
Many governments are offering incentives to boost domestic semiconductor production and electronics manufacturing.
The U.S. CHIPS Act aims to reduce reliance on foreign semiconductors.
India’s PLI (Production-Linked Incentive) scheme is attracting major electronics manufacturers.
The EU is investing in semiconductor independence.
Keeping up with these incentives and policy changes can help you strategically position your supply chain.
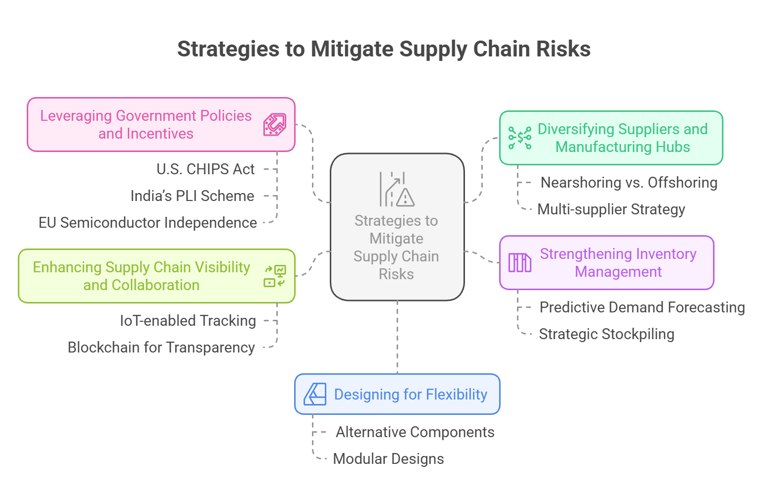
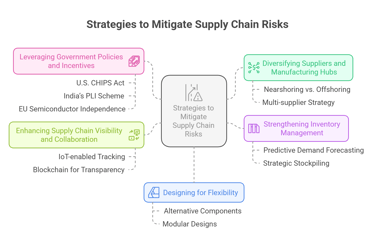
3. Case Studies: Lessons from Leading Electronics Manufacturers
Case 1: Apple’s Supply Chain Resilience
Apple has mastered the art of supply chain diversification. When faced with chip shortages, the company secured exclusive deals with suppliers and diversified production across multiple countries, reducing reliance on any single factory.
Case 2: Tesla’s Agile Approach to Component Shortages
Tesla faced semiconductor shortages but quickly pivoted by rewriting firmware to use alternative chips, allowing them to maintain production while competitors struggled.
Case 3: A Startup’s Success in Securing Alternative Supply Routes
One European electronics startup overcame supply chain disruptions by using a combination of local PCB suppliers and offshore component distributors, balancing cost and resilience.
4. The Future of Supply Chain Resilience in Electronics Manufacturing
Regionalized Supply Chains and Micro-Factories
Instead of relying on massive centralized factories, more companies are considering localized production. Micro-factories that can rapidly adapt to demand are emerging as a viable alternative to traditional mass production.
AI and Predictive Analytics in Supply Chain Management
AI is revolutionizing supply chain planning by predicting component shortages, optimizing inventory, and even suggesting alternative suppliers in real time.
Sustainability and Circular Supply Chains
As regulations tighten, the shift towards circular supply chains—where materials are recycled and reused—will gain traction. Companies investing in sustainable electronics design today will be ahead of regulatory pressures in the future.
Conclusion
Supply chain disruptions in electronics manufacturing aren’t going away, but companies that embrace agility, visibility, and strategic sourcing can thrive despite the challenges. By diversifying suppliers, leveraging technology, and designing with flexibility in mind, you can build a more resilient operation.
If you’re involved in electronics product development, now is the time to rethink your supply chain strategy. Don’t wait for the next disruption—start building resilience today.