Navigating Compliance and Standards in Electronics Metal Fabrication
For those of us shaping the future of electronics, understanding these regulations isn’t just a chore—it’s a game-changer. Let’s dive into why compliance matters, unpack the key standards you’ll encounter, and explore how they ripple through the fabrication process.
2/26/20256 min read
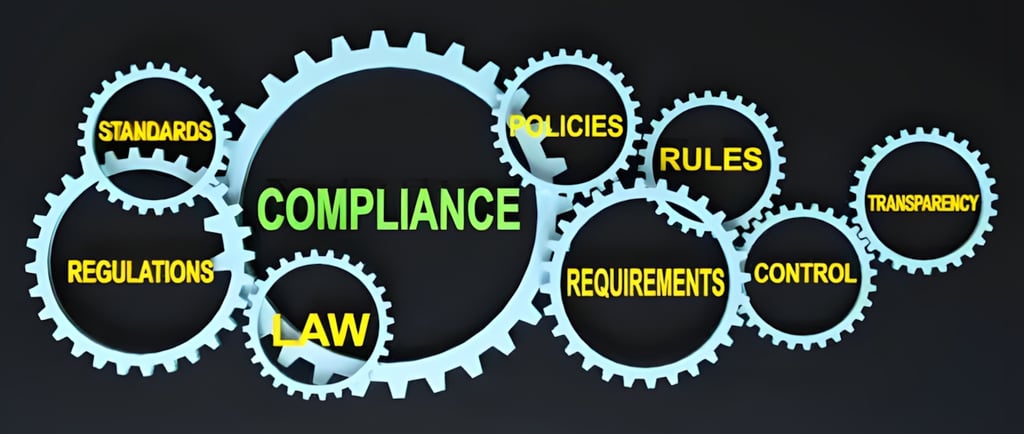
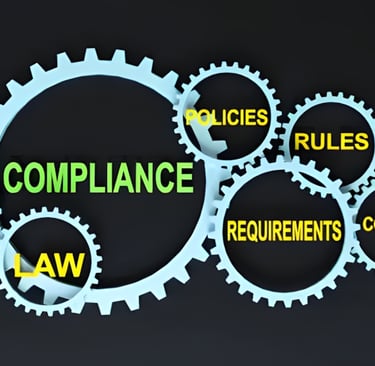
Picture this: You’re a designer sketching out the next big thing in electronics—a sleek, high-performance gadget that’s going to turn heads. Or maybe you’re the decision-maker, crunching numbers and weighing options to get it to market. Either way, there’s a hidden hurdle you can’t ignore: compliance. In the world of electronics metal fabrication, it’s not just about crafting sturdy enclosures or slick connectors—it’s about doing it right. Standards like RoHS and UL certifications aren’t optional checkboxes; they’re the backbone of a product that’s safe, reliable, and legally sound.
For those of us shaping the future of electronics, understanding these regulations isn’t just a chore—it’s a game-changer. Let’s dive into why compliance matters, unpack the key standards you’ll encounter, and explore how they ripple through the fabrication process. By the end, you’ll see why these rules aren’t roadblocks but stepping stones to success.
Why Compliance Matters in Electronics Metal Fabrication
Metal fabrication is the unsung hero of electronics. It’s the chassis that protects your circuit boards, the connectors that keep signals flowing, and the heat sinks that stop your device from turning into a meltdown metaphor. Designers love the flexibility—stainless steel for durability, aluminum for lightweight finesse. Decision-makers appreciate the cost-effectiveness of scalable production. But here’s the catch: if your fabrication process doesn’t meet regulatory standards, all that brilliance could unravel faster than a cheap solder joint.
Non-compliance isn’t just a slap on the wrist. We’re talking hefty fines, product recalls that tank your reputation, and—worst-case scenario—devices that endanger users. I once heard about a small startup that skipped a crucial UL test to save time. Their prototype enclosures sparked during a demo, and poof—there went their funding. Compliance isn’t a buzzkill; it’s your safety net.
For designers, it’s about marrying creativity with responsibility. For deciders, it’s about balancing innovation with the bottom line. Get it right, and you’re golden. Ignore it, and you’re playing with fire—sometimes literally.
Key Regulatory Requirements in Electronics Metal Fabrication
So, what are the big players in this compliance game? Let’s break down the heavy hitters: RoHS, UL certifications, and a few others you’ll want on your radar.
RoHS (Restriction of Hazardous Substances)
First up, RoHS. If you’ve ever wondered why lead solder is harder to come by these days, this is why. RoHS—short for Restriction of Hazardous Substances—is a European directive that limits the use of nasty stuff like lead, mercury, cadmium, and a handful of other chemicals in electronics. It’s all about keeping toxins out of landfills and, frankly, out of our lives.
For designers, RoHS reshapes how you think about materials. That shiny metal coating? Better make sure it’s lead-free. Those solder joints? Time to switch to alternatives like tin-silver-copper alloys. It’s not just the metals themselves—finishes, platings, and even adhesives need scrutiny. I remember chatting with a fabricator who groaned about retooling his shop for RoHS-compliant processes. “The upfront cost stung,” he said, “but losing EU clients would’ve hurt more.”
Decision-makers, take note: RoHS compliance can pinch your budget. Testing raw materials, retraining staff, and sourcing certified suppliers aren’t cheap. But the EU market is massive, and non-compliance locks you out. Plus, customers love eco-friendly brands—it’s a win worth chasing.
UL Certifications (Underwriters Laboratories)
Next, let’s talk UL certifications. Underwriters Laboratories isn’t a government body; it’s an independent organization that’s been setting safety benchmarks for over a century. In electronics, UL standards ensure your fabricated metal parts won’t catch fire, zap someone, or fall apart under stress. Think of it as the Good Housekeeping Seal for your enclosures and connectors.
For metal fabrication, standards like UL 50 (for electrical enclosures) and UL 94 (for flammability of materials) often come into play. Designers, this means your sleek chassis design needs to pass muster—think about thickness, grounding, and how it handles heat. I once worked with a team tweaking an aluminum enclosure to meet UL 50. We had to ditch a flashy open-vent design for something sturdier, but the peace of mind was worth it.
Decision-makers, UL certification isn’t a one-and-done deal. It’s a process: submit your design, test prototypes, document everything, and pay for the stamp of approval. It’s an investment, sure, but it’s also a ticket to credibility. Retailers and clients—especially in the U.S.—often won’t touch a product without that UL logo.
Other Notable Standards
RoHS and UL aren’t the only players. There’s REACH, another EU regulation that digs deeper into chemical safety, overlapping with RoHS but broader in scope. Then there are IPC standards, which focus on manufacturing quality—like how tight your tolerances need to be. And don’t forget: regulations shift depending on where you’re selling. The EU might demand RoHS, but the U.S. might lean harder on UL or FCC rules for electromagnetic interference.
Keeping up can feel like herding cats, but it’s part of the gig. Designers and deciders need to sync up—your brilliant idea won’t fly if it’s illegal in half your markets.
Impact of Compliance on the Fabrication Process
Compliance doesn’t just sit on a shelf; it seeps into every step of metal fabrication. Let’s walk through how it shakes things up.
Start with materials. RoHS might nix your favorite leaded alloy, forcing you to hunt for alternatives. Suppliers get pickier too—decision-makers will notice longer lead times and higher costs as vendors scramble to certify their stock. I once saw a project stall because a batch of steel had trace cadmium levels. The fix? A new supplier and a three-week delay.
Manufacturing tweaks come next. Precision cutting and forming stay the same, but finishing processes—like plating or painting—get a compliance makeover. Lead-free coatings mean new equipment or retraining, and UL might demand tighter tolerances to pass safety tests. Quality control ramps up too. Every batch gets tested—sometimes destructively—to prove it meets spec. It’s tedious, but it beats a recall.
Here’s a real-world nugget: A mid-sized fabricator I know shifted to RoHS-compliant soldering for a client’s server racks. They overhauled their line, audited suppliers, and ran trial batches. Six months later, they landed a contract with a green-tech giant. Compliance opened doors they didn’t even know existed.
Benefits of Adhering to Standards
Sure, compliance is a hassle, but the payoff is real. For designers, it’s about peace of mind—your creation won’t fry someone’s desk or poison a landfill. For decision-makers, it’s a market edge. Certified products sell better in regulated regions, and customers trust brands that prioritize safety and sustainability.
Take UL certification. A stamped enclosure screams reliability—think of it as a badge of honor that sets you apart from the fly-by-night crowd. RoHS, meanwhile, aligns you with the eco-conscious wave. I’ve seen companies plaster “RoHS-compliant” on their packaging like it’s a medal—it’s catnip for environmentally savvy buyers.
Then there’s the bigger picture. Less lead and mercury mean cleaner soil and water. It’s not just business; it’s leaving the planet a little better than we found it. Who doesn’t want that on their resume?
Challenges and Future Trends
Let’s be real—compliance isn’t all sunshine. Costs creep up with every new test or supplier switch. Training staff to spot RoHS violations or nail UL specs takes time. And standards evolve—yesterday’s “good enough” might be tomorrow’s lawsuit.
I talked to a designer who vented about this. “We nail one reg, and then bam—some new rule drops,” he said. “It’s like chasing a moving target.” Decision-makers feel it too—budgets stretch thin when you’re retrofitting for the latest mandate.
Looking ahead, things are shifting. Environmental laws are tightening—think stricter RoHS updates or carbon footprint rules. Automation’s creeping in, with smart systems tracking compliance in real time. Green fabrication—recycled metals, low-energy processes—is gaining traction too. And as 5G and IoT explode, expect standards to adapt. Thinner, lighter enclosures might need new UL tests for heat or interference.
The trick? Stay nimble. Watch the trends, lean on certified partners, and build compliance into your workflow from day one.
Conclusion
Compliance in electronics metal fabrication isn’t glamorous, but it’s non-negotiable. For designers, it’s the guardrail that keeps your genius grounded. For decision-makers, it’s the key to unlocking markets and trust. RoHS, UL, and their regulatory cousins aren’t here to stifle you—they’re here to elevate you.
So, embrace it. See standards as a chance to shine, not a chore to dread. Stay curious, team up with suppliers who get it, and bake compliance into your DNA. In a world where safety, reliability, and sustainability matter more than ever, that’s how you don’t just survive—you thrive.