Metal vs. Plastic Enclosures: Which One Should You Choose?
Selecting the right material for electronic enclosures is a critical decision that impacts durability, cost, functionality, and aesthetics. Whether designing consumer electronics, industrial equipment, or IoT devices, the choice between metal and plastic enclosures plays a significant role in performance and longevity.
2/4/20254 min read
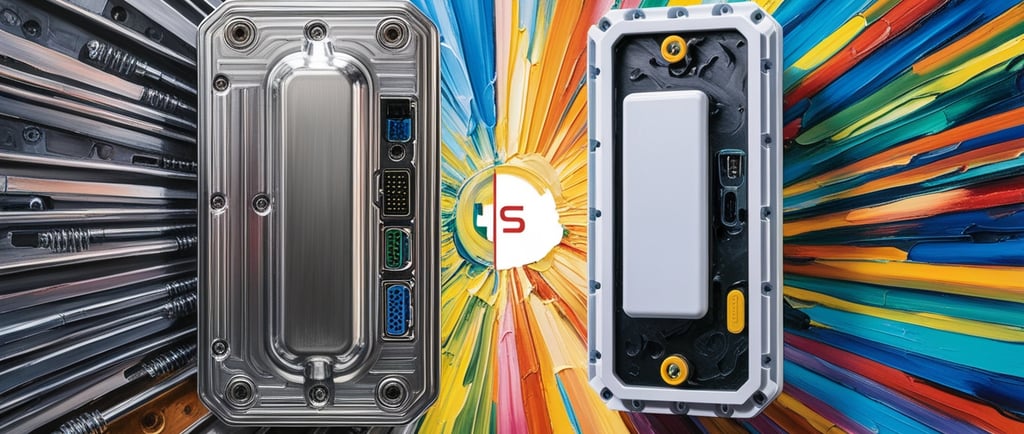
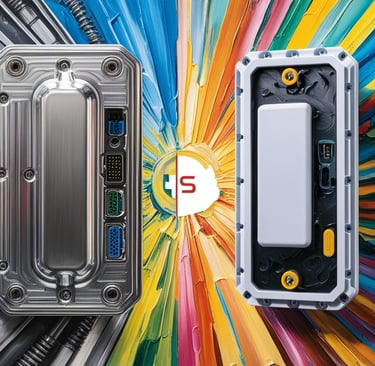
Introduction
Selecting the right material for electronic enclosures is a critical decision that impacts durability, cost, functionality, and aesthetics. Whether designing consumer electronics, industrial equipment, or IoT devices, the choice between metal and plastic enclosures plays a significant role in performance and longevity. This article explores the advantages and limitations of each material to help you make an informed decision based on your specific needs.

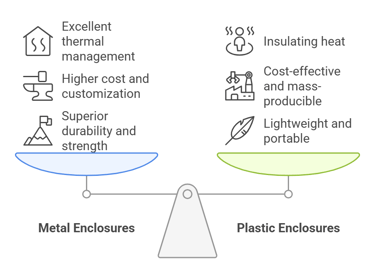
1. Overview of Metal and Plastic Enclosures
Metal Enclosures
Metal enclosures are commonly made from materials such as aluminum, steel, and stainless steel. Aluminum is a lightweight yet strong option that is corrosion-resistant and excels in heat dissipation. Steel, on the other hand, is heavy-duty and robust but requires proper coating to prevent rust. Stainless steel is the most durable and corrosion-resistant, making it ideal for use in harsh environments.
Metal enclosures are known for their strength and durability, allowing them to withstand harsh conditions, impacts, and general wear. Their natural conductivity makes them an excellent choice for applications requiring EMI shielding. Additionally, metal enclosures provide superior heat dissipation, making them ideal for high-power electronics. However, their heavier weight can be a drawback for portable applications.
Plastic Enclosures
Plastic enclosures are typically made from materials such as ABS (Acrylonitrile Butadiene Styrene), polycarbonate, and acrylic. ABS is a cost-effective option that is impact-resistant and easy to mold. Polycarbonate offers high strength, UV resistance, and flame-retardant properties, making it a versatile choice. Acrylic, while providing a glossy and transparent finish, is more brittle compared to other plastics.
Plastic enclosures are lightweight, making them easier to handle and transport. They are also highly versatile, available in various shapes, colors, and textures to meet different design requirements. Their cost-effectiveness is another advantage, especially in high-volume manufacturing. However, since plastic is non-conductive, additional coatings or metal liners may be required for EMI shielding in sensitive applications.
When to Choose Each
Metal enclosures are best suited for rugged environments, industrial applications, and devices that require EMI shielding and effective heat dissipation. They offer excellent durability and protection but may add weight and cost to the final product. On the other hand, plastic enclosures are a great choice for consumer electronics, lightweight applications, and budget-conscious projects. Their ease of manufacturing and design flexibility make them a popular option for many electronic devices.
2. Key Factors to Consider When Choosing Between Metal and Plastic
A. Durability and Strength
Metal: Offers superior strength, making it ideal for industrial control systems, military-grade electronics, and outdoor enclosures exposed to mechanical stress.
Plastic: Durable for everyday use but less resistant to extreme impacts or harsh environmental conditions. Commonly used in remote controls, routers, and IoT devices.
B. Weight
Metal: Heavier, which can be beneficial for stationary applications requiring stability but may not be ideal for handheld or portable devices.
Plastic: Lightweight, making it the preferred choice for wearables and mobile gadgets.
C. Cost
Metal: Generally more expensive due to material costs and machining requirements. Additional customization, such as anodizing or powder coating, increases the cost further.
Plastic: More budget-friendly, with injection molding making mass production significantly more economical.
D. Thermal Management
Metal: Superior heat dissipation properties, making it the best choice for high-power electronics that generate substantial heat.
Plastic: Acts as an insulator, requiring additional cooling mechanisms such as vents or heat sinks.
E. EMI Shielding
Metal: Naturally conductive, providing excellent EMI shielding for sensitive electronics in high-interference environments.
Plastic: Requires additional conductive coatings or metal liners to achieve EMI protection, adding to the cost.
F. Environmental Resistance
Metal: Resistant to UV rays and extreme temperatures but can corrode if not treated properly.
Plastic: Corrosion-proof but susceptible to UV degradation unless UV-stabilized.
G. Aesthetics and Customization
Metal: Offers a premium, professional finish and can be customized through anodizing, powder coating, or engraving.
Plastic: Highly versatile, allowing for complex designs, custom colors, and textures with ease.
3. Use Cases for Metal Enclosures
Industrial Control Systems: Require durability, EMI shielding, and heat dissipation.
Outdoor Equipment: Must withstand harsh weather conditions and temperature extremes.
High-Power Electronics: Need effective heat management to prevent overheating.
4. Use Cases for Plastic Enclosures
Consumer Electronics: Common in remote controls, gaming accessories, and home automation devices.
Wearable Technology: Lightweight design makes it suitable for smartwatches and fitness trackers.
Budget-Sensitive Projects: Mass production is more affordable with plastic enclosures.
5. Hybrid Solutions: When to Combine Metal and Plastic
In some cases, a hybrid approach that combines both materials can provide the best of both worlds. Examples include:
Metal Frames with Plastic Covers: Ensures strength while keeping weight minimal.
Plastic Housing with Metal Inserts: Adds reinforcement in critical areas for durability.
EMI Shielding Coated Plastic: Provides protection without the need for a full-metal enclosure.
6. Tips for Making the Right Choice
When selecting an enclosure material, ask yourself the following questions:
What environment will the device operate in?
Harsh conditions may require metal enclosures.
Indoor consumer electronics can use plastic.
Is EMI shielding a priority?
Metal is preferable, but coated plastic can work for less critical applications.
How important are weight and portability?
Handheld and wearable devices benefit from plastic’s lightweight nature.
What is your budget?
Plastic is cost-effective, while metal offers higher durability at a premium price.
Does the enclosure need a specific aesthetic appeal?
Metal provides a sleek, professional look, whereas plastic allows for vibrant customization.
Collaborating with Manufacturers
To ensure the best solution for your project, it is essential to consult experienced manufacturers like Peakingtech. Their expertise in custom enclosures can help tailor solutions to your specific requirements, balancing cost, functionality, and aesthetics.
Conclusion
Choosing between metal and plastic enclosures depends on several factors, including durability, weight, cost, thermal management, and EMI shielding. While metal excels in strength and conductivity, plastic offers affordability and design flexibility. In some cases, hybrid solutions may provide the ideal balance.
Call-to-Action (CTA)
If you’re looking for expert guidance in selecting or customizing enclosures for your projects, Peakingtech is here to help. Contact us today for tailored solutions that meet your exact needs. Have experience with metal or plastic enclosures? Share your insights in the comments below!