Metal Fabrication’s Role in the Miniaturization of Electronics
Electronics are getting smaller, yet more powerful. The evolution of consumer electronics, medical devices, wearables, and industrial sensors has been largely driven by the demand for compactness without compromising performance. As devices shrink, so do their internal components, pushing manufacturers to explore innovative fabrication methods to keep up with the trend.
2/26/20255 min read
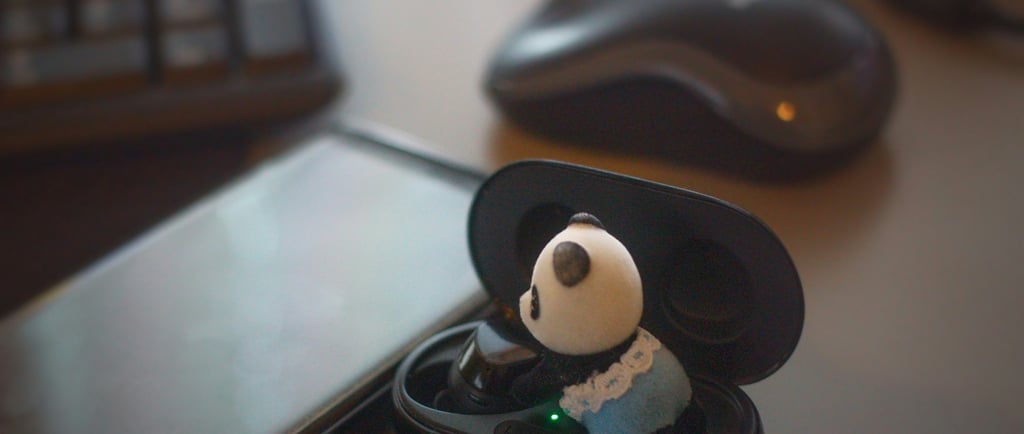
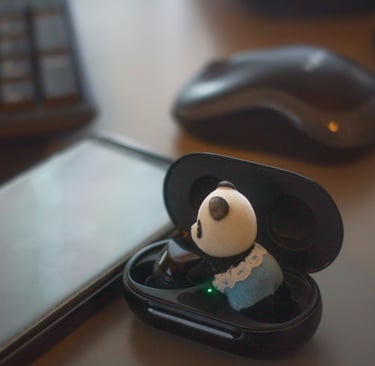
Electronics are getting smaller, yet more powerful. The evolution of consumer electronics, medical devices, wearables, and industrial sensors has been largely driven by the demand for compactness without compromising performance. As devices shrink, so do their internal components, pushing manufacturers to explore innovative fabrication methods to keep up with the trend. Metal fabrication plays a critical role in making miniaturization possible by enabling precise, durable, and thermally efficient components.
For designers and decision-makers in electronics development, understanding how metal fabrication supports miniaturization is crucial. Whether you're developing the next breakthrough in IoT devices or refining an existing product, leveraging the right metalworking techniques can give you a competitive edge. In this article, we’ll explore how metal fabrication is shaping the future of miniaturized electronics, the key processes involved, and what challenges and opportunities lie ahead.
1. The Push for Miniaturization in Electronics
The trend toward smaller, more powerful electronics is driven by both consumer expectations and technological advancements.
Consumer Demand for Compact Devices
The modern consumer expects slim, lightweight, and portable devices. Smartphones have evolved from bulky handsets into sleek, powerful computing tools. Wearable technology, from fitness trackers to smart glasses, relies on miniaturized components to maintain comfort and usability. Similarly, hearing aids and implantable medical devices must be discreet and efficient.
Industry Needs for Smaller Components
Beyond consumer electronics, industries such as aerospace, automotive, and industrial automation demand compact electronics for space efficiency. IoT devices, which require embedded sensors in tight spaces, have further fueled the miniaturization movement. The challenge is achieving this reduction in size without sacrificing functionality, durability, or manufacturability.
2. Metal Fabrication Techniques Enabling Miniaturization
To meet the need for smaller and more intricate electronic components, metal fabrication has evolved significantly. Several key techniques are pushing the boundaries of what’s possible in electronics miniaturization.
CNC Machining: Precision at a Microscopic Level
Computer Numerical Control (CNC) machining has become indispensable for fabricating ultra-precise metal parts. With modern CNC machines capable of working at micron-level accuracy, manufacturers can produce intricate enclosures, connectors, and heat sinks essential for miniaturized electronics. CNC machining allows for customization and high repeatability, ensuring that each component fits perfectly into the overall design.
Sheet Metal Stamping & Forming: Efficient and Scalable
For mass production of small metal parts, stamping and forming provide cost-effective solutions. These processes allow manufacturers to produce thin, lightweight metal casings, brackets, and shielding components at scale. With advancements in die technology, metal stamping can now achieve tighter tolerances and more complex geometries than ever before.
Laser Cutting & Etching: Ultra-Fine Detailing
Laser technology has revolutionized metal fabrication by enabling micro-cutting and micro-etching with extreme precision. For applications such as semiconductor components, RF shielding, and intricate circuit board parts, laser cutting ensures clean edges and detailed patterns that traditional mechanical methods cannot achieve.
Micro Welding & Soldering: Connecting Tiny Components
As electronics continue to shrink, traditional welding and soldering methods struggle to meet the precision requirements. Micro welding techniques, such as laser welding and resistance welding, allow manufacturers to join ultra-small components with minimal heat impact. This is particularly important for medical implants, sensors, and aerospace electronics, where even slight misalignment can lead to failure.
Metal Injection Molding (MIM): Cost-Effective Miniature Components
Metal Injection Molding combines the precision of CNC machining with the scalability of plastic injection molding. MIM allows for the mass production of complex metal parts with high precision, making it ideal for small electronic enclosures, connectors, and internal structural components. The ability to create intricate shapes without extensive machining reduces waste and cost.
3. Advanced Materials for Miniature Electronics
The choice of materials plays a significant role in supporting miniaturization while maintaining performance. Not all metals are suitable for compact electronics, but certain high-performance materials have proven to be game-changers.
High-Performance Alloys for Strength and Conductivity
Miniaturized devices require materials that offer both strength and electrical conductivity. Alloys such as beryllium copper and phosphor bronze provide excellent mechanical properties while ensuring reliable electrical performance in connectors and shielding applications.
Ultra-Thin Metal Foils for Shielding and Circuitry
EMI (Electromagnetic Interference) shielding is critical in small electronic devices to prevent signal interference. Ultra-thin metal foils, such as aluminum and copper, provide effective shielding without adding bulk. These materials are widely used in smartphones, medical devices, and aerospace electronics.
Lightweight Metals for Durability Without Bulk
Aluminum and titanium are often used in miniaturized devices due to their lightweight and high-strength properties. Titanium, in particular, is favored for medical implants and aerospace electronics due to its biocompatibility and corrosion resistance.
4. Role of Metal Fabrication in Thermal Management
As electronics get smaller, heat dissipation becomes a major challenge. Efficient thermal management is essential to maintain performance and prevent overheating. Metal fabrication plays a vital role in addressing this issue.
Custom Heat Sinks and Thermal Shielding
Miniaturized devices still generate heat, and without proper dissipation, they can fail prematurely. Custom-designed heat sinks, often made of aluminum or copper, help to draw heat away from critical components. Advanced fabrication techniques, such as CNC machining and metal forming, enable the production of micro heat sinks tailored to compact spaces.
Advanced Metal Coatings to Improve Heat Dissipation
Metal coatings, such as nano-ceramic or graphite-infused layers, improve thermal conductivity without increasing weight. These coatings enhance heat dissipation in confined electronic spaces and are increasingly used in mobile devices, wearables, and high-performance computing applications.
Integration of Metal Cooling Components in Compact Designs
Metal fabrication enables the integration of cooling features directly into the structural design of a device. For example, metal enclosures can double as heat spreaders, reducing the need for additional cooling elements. This approach not only optimizes thermal performance but also enhances space efficiency.
5. Challenges & Future Trends in Metal Fabrication for Miniaturization
While metal fabrication has come a long way in supporting miniaturization, challenges remain. However, new trends and innovations are addressing these challenges head-on.
Precision Limitations and Cost Challenges
Achieving extreme precision at a microscopic scale requires advanced machinery and skilled labor, leading to higher costs. However, automation and AI-driven manufacturing are making high-precision metal fabrication more accessible and cost-effective.
AI and Automation in Precision Manufacturing
AI-driven design and manufacturing software now allow engineers to optimize metal fabrication processes with predictive modeling. Automated quality control ensures that every component meets strict tolerances, reducing errors and waste.
3D Printing of Metal Components
Metal additive manufacturing (3D printing) is opening new possibilities for creating highly complex, lightweight components. This technology allows for rapid prototyping and production of intricate designs that would be impossible with traditional fabrication methods.
Future Materials Driving Miniaturization
New materials, such as graphene-infused metals and nano-engineered alloys, promise to further revolutionize miniaturized electronics. These materials offer superior strength, conductivity, and thermal performance, paving the way for the next generation of ultra-compact devices.
Conclusion
The miniaturization of electronics is not just a trend—it’s the future. Metal fabrication plays an essential role in making smaller, more powerful devices possible. From advanced CNC machining to micro welding and innovative materials, metalworking techniques are evolving to meet the demands of compact electronics.
For designers and decision-makers, understanding these fabrication methods can help in selecting the right processes and materials for their next innovation. As new technologies continue to emerge, the future of miniaturized electronics will be shaped by the ongoing advancements in precision metal fabrication.
Are you ready to push the boundaries of miniaturization in your next product? The right fabrication strategy could be the key to making it happen.