Metal Fabrication vs. Alternative Methods: Choosing the Best Approach for Electronics Applications
Whether you’re crafting rugged industrial enclosures, sleek consumer gadgets, or high-performance components, the choice between metal fabrication and alternative methods like plastic injection molding can make or break your product’s success.
2/26/20257 min read
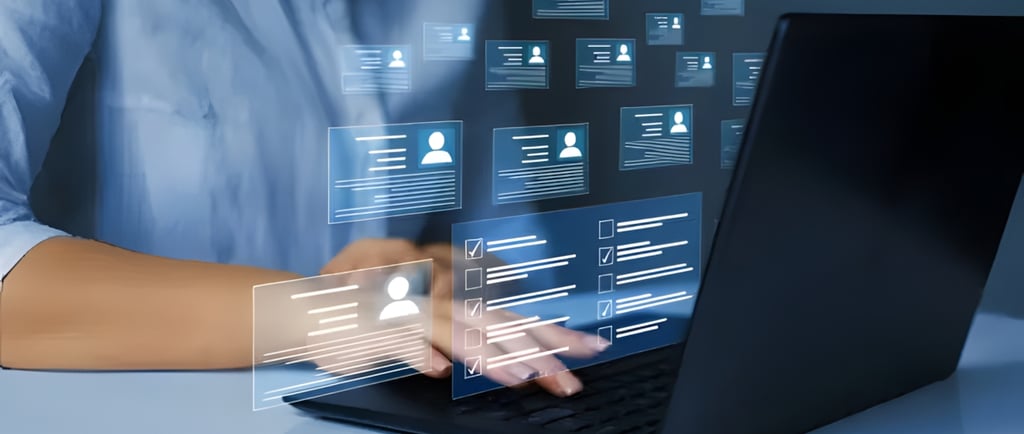
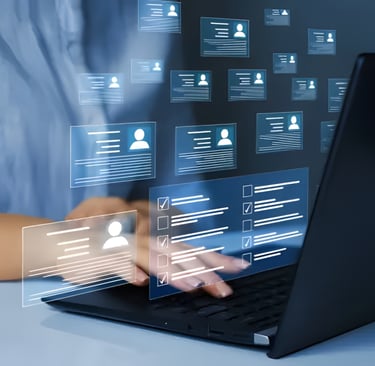
As a designer or decision-maker in electronics development, you’re no stranger to the challenges of selecting the right materials and manufacturing methods for your projects. Whether you’re crafting rugged industrial enclosures, sleek consumer gadgets, or high-performance components, the choice between metal fabrication and alternative methods like plastic injection molding can make or break your product’s success. I’ve been in the trenches of electronics design for years, and I’ve seen firsthand how these decisions impact everything from functionality and cost to aesthetics and longevity. Let’s dive into a detailed comparison of metal fabrication and its alternatives, exploring the pros, cons, and real-world considerations to help you make informed choices for your next project.
Why Material Choice Matters in Electronics Design
Picture this: you’re designing a new IoT device for a factory floor, where it’ll face extreme heat, vibrations, and potential corrosion. Or maybe you’re working on a sleek wearable gadget that needs to be lightweight, durable, and visually appealing. In both cases, the materials you choose—and how they’re shaped into components—define not just the product’s performance but also its manufacturability and market appeal. Metal fabrication has long been a go-to for electronics, offering strength and reliability, but alternatives like plastic injection molding are gaining traction for their versatility and cost-effectiveness. This article will walk you through the nitty-gritty of both approaches, so you can weigh your options with confidence.
What Is Metal Fabrication, and Why Does It Matter for Electronics?
Metal fabrication is the art and science of shaping raw metal into finished products through processes like cutting, bending, welding, and machining. For electronics, it’s often used to create enclosures, heat sinks, brackets, and other critical components. Think aluminum for its lightweight strength, steel for its toughness, or copper for its unbeatable electrical conductivity. I’ve seen engineers rely on these metals to build everything from server racks to smartphone frames, leveraging their ability to handle harsh environments and dissipate heat effectively.
The process starts with raw metal sheets or bars, which are then transformed using tools like laser cutters, presses, or CNC machines. It’s a hands-on, industrial approach that’s been refined over decades, but it’s not without its challenges—like higher costs and weight compared to other methods. Still, for electronics that need to last in demanding conditions, metal fabrication is often the gold standard.
Exploring Alternatives: Plastic Injection Molding and Beyond
Now, let’s talk about the competition—particularly plastic injection molding, which has become a powerhouse in electronics manufacturing. This method involves melting plastic pellets, injecting them into a mold, and letting them cool into the desired shape. Materials like ABS, polycarbonate, or nylon are popular choices, prized for their lightweight nature, insulation properties, and ability to create complex designs. I’ve worked on projects where plastic enclosures were perfect for consumer devices like smartwatches or remote controls, thanks to their affordability and design flexibility.
But plastic isn’t the only alternative. 3D printing and composite materials are also making waves, especially for prototypes or niche applications. However, for large-scale production, plastic injection molding tends to dominate due to its efficiency and scalability. It’s a game-changer for lightweight, portable electronics, but it’s not always the best fit—especially when heat, durability, or shielding are concerns.
The Upsides of Metal Fabrication for Electronics
Let’s start with why metal fabrication remains a favorite in electronics design. First, its strength and durability are unmatched. I once designed an enclosure for a medical device that needed to withstand drops, spills, and constant use in a hospital setting. Aluminum fabrication gave us the ruggedness we needed, ensuring the device could handle the rigors of real-world use without cracking or deforming.
Second, metals excel at heat dissipation. Electronics generate heat, and components like heat sinks or enclosures made from aluminum or copper can channel that heat away, keeping sensitive parts cool. I’ve seen this make a huge difference in high-performance servers or power amplifiers, where overheating could spell disaster.
Third, metals offer excellent electrical conductivity and shielding. Copper, for instance, is a go-to for grounding or shielding against electromagnetic interference (EMI)—a must for devices like radios or medical equipment. And don’t overlook the aesthetic appeal: a brushed aluminum enclosure can give your product a premium, industrial look that customers love.
Finally, metals are incredibly long-lasting. With proper coatings or treatments, they resist corrosion and wear, making them ideal for outdoor or industrial electronics. It’s no wonder metal fabrication is a staple in the field—but it’s not perfect.
The Downsides of Metal Fabrication for Electronics
Of course, metal fabrication isn’t without its drawbacks, especially when budget and weight are concerns. For starters, it’s often more expensive than plastic alternatives. The raw materials, specialized equipment, and labor involved can drive up costs, particularly for low-volume production runs. I’ve had to justify these costs to stakeholders on projects where budget constraints were tight, and it’s not always an easy sell.
Weight is another issue. Metals like steel can add significant bulk, which might not be ideal for portable devices like smartphones or wearables. I’ve seen designers struggle to balance functionality with portability, sometimes opting for lighter materials or hybrid designs.
Then there’s the challenge of complexity. While metal fabrication can handle intricate designs, it’s not as flexible as plastic molding for creating thin walls, fine details, or integrated features like snap-fits. And without proper treatment—like galvanizing or anodizing—metals can corrode in humid or salty environments, which is a concern for outdoor electronics.
The Advantages of Plastic Injection Molding for Electronics
Now, let’s flip the script and explore why plastic injection molding is so appealing for electronics. First and foremost, it’s cost-effective for large-scale production. Once you’ve invested in the mold (which can be pricey upfront), churning out thousands of plastic parts becomes remarkably efficient. I’ve worked on consumer electronics projects—like smart home devices—where plastic enclosures saved us money without sacrificing quality.
Lightweight is another big win. Plastics are ideal for portable electronics, where every gram counts. Imagine designing a fitness tracker: a plastic case keeps it comfortable to wear while maintaining durability for everyday use.
Design flexibility is a major perk, too. Plastic injection molding lets you create complex shapes, incorporate features like threads or hinges, and achieve a wide range of finishes and colors—all without extra steps. I’ve seen designers use this to their advantage, crafting sleek, modern looks for products that stand out on store shelves.
Finally, plastics are naturally insulating, which can be a plus for components that need to avoid conducting electricity. They’re also resistant to certain chemicals, though this depends on the specific plastic used.
The Drawbacks of Plastic Injection Molding for Electronics
But plastic isn’t a silver bullet. Its durability pales in comparison to metal, especially under physical stress or high temperatures. I’ve seen plastic enclosures crack or deform in industrial settings where metal would have held up better. Heat dissipation is another weak spot—plastics don’t conduct heat as well as metals, so you might need additional cooling solutions for heat-sensitive electronics.
Plastics can also scratch easily, fade under UV light, or degrade when exposed to harsh chemicals. And while they’re non-conductive, they’re lousy at shielding against EMI unless you add costly coatings or inserts. For high-performance electronics, this can be a deal-breaker.
Head-to-Head: When to Choose Metal Fabrication or Plastic Injection Molding
So, how do you decide? It depends on your project’s specific needs. Let’s break it down.
If durability, heat management, and shielding are top priorities—like for industrial equipment or medical devices—metal fabrication is likely your best bet. I’ve used aluminum enclosures for factory automation systems, where they withstood extreme conditions while dissipating heat effectively. The trade-off? Higher costs and weight, which might not work for budget-conscious or portable designs.
On the other hand, if you’re building consumer electronics like smartwatches or remote controls, plastic injection molding shines. It’s lightweight, affordable for mass production, and allows for intricate, eye-catching designs. But you’ll need to address heat and durability concerns, possibly with hybrid solutions or additional components.
Consider factors like production volume, budget, design complexity, and environmental conditions. For example, a high-volume run of plastic parts might offset the initial mold cost, while a low-volume metal project could become prohibitively expensive. I’ve also seen designers blend metals and plastics—using a metal frame with plastic panels—to strike the perfect balance.
Real-World Examples
Take industrial electronics: a rugged enclosure for a factory sensor might use stainless steel fabrication for its strength and corrosion resistance, even if it adds weight and cost. Meanwhile, a consumer smart speaker might opt for a plastic molded case to keep it lightweight and affordable, with a metal heat sink inside for thermal management. These hybrid approaches are becoming more common as designers get creative with material combinations.
Looking Ahead: Trends and Innovations
The future of electronics materials is exciting. Metal fabrication is evolving with techniques like laser cutting and additive manufacturing, making it faster and more precise. I’ve seen 3D-printed metal parts used for prototypes, offering new possibilities for complex designs.
Plastics, too, are advancing. Reinforced plastics, biodegradable options, and smart materials are hitting the market, driven by sustainability demands. As electronics designers, we’re increasingly pressured to consider recycling and environmental impact, which could tilt the scales toward greener materials in the coming years.
Wrapping It Up: Making the Right Choice for Your Electronics Project
Choosing between metal fabrication and plastic injection molding—or a hybrid approach—boils down to your project’s unique needs. Metals offer unmatched durability, heat dissipation, and shielding, but they come with higher costs and weight. Plastics are lightweight, cost-effective, and design-friendly, but they struggle with heat and toughness.
As someone who’s navigated these decisions countless times, I’d encourage you to evaluate your application requirements, production goals, and budget. Ask yourself: Does this device need to survive harsh conditions? Is weight a concern? Can we afford the upfront investment in molds or metalworking? By weighing these factors, you’ll find the sweet spot for your electronics design.
And don’t forget sustainability—both metals and plastics have environmental trade-offs, but innovations like recycling and eco-friendly materials are opening new doors. Whether you’re crafting the next big industrial tool or a trendy consumer gadget, the right material choice can set your project up for success.
What’s your experience been like with these materials? Have you found a killer combination for your electronics projects? Drop a comment below—I’d love to hear your stories and insights!