Metal Fabrication Solutions for Wearable Electronics: Crafting the Future of Wearable Tech
Wearable electronics—smartwatches, fitness trackers, augmented reality glasses, you name it—are booming. Consumers want devices that are light enough to forget they’re wearing, tough enough to survive their chaotic lives, and sleek enough to turn heads.
2/26/20255 min read
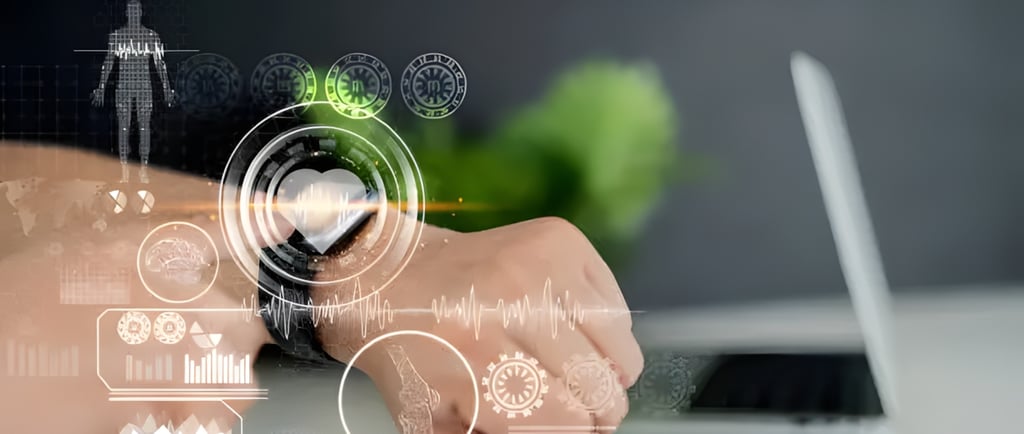
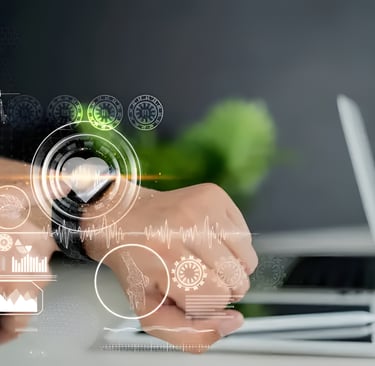
Imagine slipping on a smartwatch that feels like a feather on your wrist yet shrugs off the sweat of a 5K run or the accidental knock against a desk corner. Or picture a medical wearable that tracks your vitals 24/7 without ever cracking under pressure. For designers and decision-makers in the electronics world, these aren’t just dreams—they’re the benchmarks you’re chasing. And here’s the thing: metal fabrication is stepping up to make them real.
Wearable electronics—smartwatches, fitness trackers, augmented reality glasses, you name it—are booming. Consumers want devices that are light enough to forget they’re wearing, tough enough to survive their chaotic lives, and sleek enough to turn heads. That’s a tall order, and it’s why metal fabrication has become the unsung hero behind the scenes. In this article, I’ll walk you through how this craft meets the unique demands of wearable tech, from material choices to cutting-edge techniques, and why it’s a game-changer for your next project.
The Unique Demands of Wearable Electronics
Let’s start with the basics: wearables aren’t your average gadgets. They’ve got to live on us—on our wrists, ears, or even clipped to our clothes—so they face a different set of rules. As a designer, you know the struggle: every gram counts. A clunky fitness tracker? No one’s wearing that to yoga class. It’s got to be lightweight, or it’s a non-starter.
But lightweight isn’t enough. These devices take a beating—splashed with rain, drenched in sweat, or accidentally slammed into a gym locker. Durability isn’t optional; it’s mandatory. Corrosion from salty skin or a cracked casing from a drop can kill a product’s reputation faster than a bad review. And then there’s the size issue. Wearables are tiny. You’re cramming sensors, batteries, and displays into spaces smaller than a postage stamp. Precision is everything.
Oh, and let’s not forget—they’ve got to look good. Your users aren’t just tech geeks; they’re fashion-conscious too. A smartwatch that looks like a brick isn’t winning any style points. So, you’re juggling weight, toughness, size, and aesthetics. Sound familiar? Metal fabrication gets it—and it’s got answers.
How Metal Fabrication Meets These Challenges
So, how does metal fabrication pull off this magic trick? It’s all about the right materials, the right techniques, and a little ingenuity. Let’s break it down.
Advanced Materials: The Lightweight Heavyweights
First up, the metals themselves. You’re not stuck with bulky steel anymore. Today’s fabrication pros are working with aluminum, titanium, and magnesium alloys—materials that pack a punch without the pounds. Aluminum’s a favorite for smartwatch casings because it’s super light and resists rust like a champ. Titanium? It’s the go-to for premium wearables—stronger than steel but half the weight. And magnesium alloys? They’re popping up in fitness trackers because they’re ridiculously light yet tough.
Why does this matter to you? These metals give you a high strength-to-weight ratio. That means your wearable can handle a tumble without feeling like a dumbbell on the user’s wrist. Plus, they’re naturally corrosion-resistant—perfect for devices that live next to sweaty skin or humid air. It’s like giving your design a built-in shield.
Precision Techniques: Small Parts, Big Impact
Now, let’s talk about how these metals turn into wearable components. Wearables demand precision—think tiny screws, intricate housings, or wafer-thin bands. That’s where techniques like CNC machining, laser cutting, and microfabrication shine. CNC machining carves out parts with tolerances tighter than a hair’s breadth, so your sensor housing fits perfectly every time. Laser cutting slices through metal with pinpoint accuracy, letting you craft delicate patterns or ultra-slim frames. And microfabrication? It’s the secret sauce for those microscopic parts—like the connectors in a hearing aid.
For you, the decision-maker, this means flexibility. Need a prototype with a funky new shape? Done. Want to scale up production without losing consistency? These tools have your back. They’re fast, reliable, and let you push the boundaries of what “small” can do.
Durability Enhancements: Built to Last
Lightweight and precise is great, but what about durability? Metal fabrication doesn’t stop at shaping—it toughens things up too. Take anodizing: it’s a process that thickens the natural oxide layer on aluminum or titanium, making it harder and more scratch-resistant. Ever wonder why some smartwatches still look pristine after months of wear? That’s anodizing at work. Or consider powder coating—it adds a protective skin that laughs off corrosion and dings.
This isn’t just about longevity; it’s about trust. Your users expect a device that doesn’t flake or fade. These finishes deliver that promise, and as a designer, they give you peace of mind knowing your creation won’t let anyone down.
Customization: Your Vision, Made Real
Here’s where it gets fun: customization. Metal fabrication isn’t a one-size-fits-all deal. Want a smartwatch with a brushed finish that screams luxury? You got it. Need a flexible band with metal accents for a fitness tracker? No problem. Techniques like stamping, bending, and even etching let you tailor every piece to your design specs. It’s like handing you a blank canvas with all the tools to paint your masterpiece.
For decision-makers, this is gold. You can differentiate your product in a crowded market—think unique textures or signature shapes—without reinventing the wheel. Metal fabrication bends (literally) to your vision.
Real-World Applications
Still not convinced? Let’s look at some wearables that owe their success to metal fabrication.
Take the Apple Watch. Its aluminum or stainless steel casing isn’t just pretty—it’s a lightweight fortress. The aluminum version weighs next to nothing, while the stainless steel option adds durability for those who want a premium feel. CNC machining and anodizing make it happen, giving designers a palette to play with and users a device that lasts.
Or consider medical wearables, like continuous glucose monitors. These gadgets need housings that protect sensitive electronics while staying comfy against skin. Titanium’s strength and biocompatibility make it a star here, machined into tiny, durable shells that patients rely on daily.
Fitness trackers, like Fitbit’s sleek clips, lean on magnesium or aluminum too. They’re light enough to wear all day, tough enough for a marathon, and styled to blend into any outfit. Laser-cut frames and coated finishes keep them functional and fresh.
What’s the takeaway? These aren’t hypothetical wins—they’re proof metal fabrication delivers. Your next wearable could be the next big thing, and this is how you get there.
The Future of Metal Fabrication in Wearables
So, where’s this all heading? The future’s looking bright—and a little wild. Let’s peek ahead.
3D Printing: Prototyping on Steroids
Metal 3D printing is shaking things up. Imagine designing a complex, hollowed-out smartwatch frame that’s lighter than ever—and printing it in hours. It’s already happening. Titanium and aluminum powders are being fused layer by layer to create shapes that traditional machining can’t touch. For you, this means faster prototyping and bolder designs. Got a crazy idea? Test it tomorrow.
Sustainability: Green Vibes Only
Sustainability’s not just a buzzword—it’s a demand. Metal fabrication’s stepping up with recyclable alloys. Aluminum and magnesium can be melted down and reused without losing their mojo. Decision-makers, this is your chance to pitch eco-friendly wearables that win over the planet-conscious crowd. Less waste, same performance—why not?
Flexible Futures: Metal Meets Soft
Wearables are getting bendy—think smart fabrics or stretchy bands. Metal fabrication’s adapting by pairing with flexible materials. Picture a metal mesh woven into a soft wristband, combining durability with comfort. It’s early days, but the potential’s huge. Designers, this could be your next frontier.
Conclusion
Here’s the bottom line: wearable electronics need to be light, tough, tiny, and gorgeous. Metal fabrication checks every box. With lightweight alloys, precision tools, durability boosts, and endless customization, it’s the backbone of devices people love to wear—and keep wearing. From today’s smartwatches to tomorrow’s flexible hybrids, it’s paving the way for what’s next.
For you designers and decision-makers, this isn’t just tech talk—it’s opportunity. Metal fabrication hands you the keys to innovate, differentiate, and deliver. So, what’s your next move? Dive into these solutions, sketch that wild idea, or drop a comment below—I’d love to hear how you’re shaping the wearable future.