Material Showdown: Aluminum vs. Stainless Steel for Electronics Enclosures
For those of us working in electronics design and development, material selection for enclosures isn't just about aesthetics—it's a critical decision that affects everything from product lifespan to manufacturing costs, from user experience to thermal management.
2/26/202510 min read
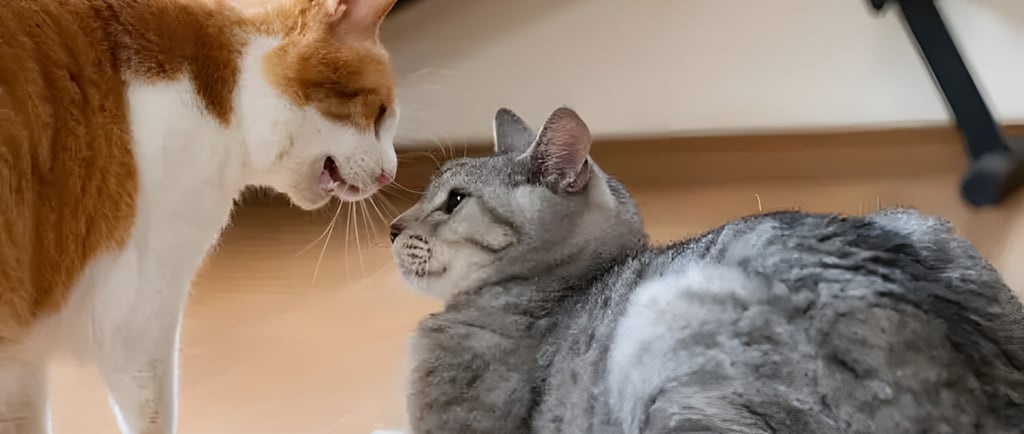
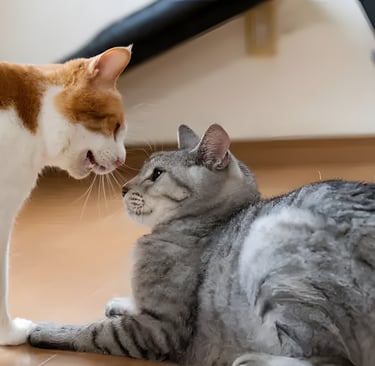
Remember that moment when you picked up the latest MacBook Air and thought, "How can something so thin and light feel so solid?" The answer lies in the careful selection of materials—specifically aluminum—that balances weight, strength, and thermal properties in a way that transformed how we think about portable electronics.
For those of us working in electronics design and development, material selection for enclosures isn't just about aesthetics—it's a critical decision that affects everything from product lifespan to manufacturing costs, from user experience to thermal management. Two materials often find themselves competing for attention in our design meetings: aluminum and stainless steel.
In this article, I'll dive into the nitty-gritty of these popular metals, comparing them across factors that matter most to electronics professionals. Having spent fifteen years watching material trends evolve across consumer and industrial electronics, I've seen firsthand how the right (or wrong) enclosure material can make or break a product's success. Whether you're developing the next revolutionary wearable or designing ruggedized equipment for industrial applications, understanding these materials' strengths and limitations will help you make more informed decisions.
Overview of Aluminum in Electronics
Aluminum has become ubiquitous in modern electronics—from Apple's unibody laptops to Samsung's smartphone frames, from drone bodies to portable hard drives. This isn't by accident. As the third most abundant element in Earth's crust, aluminum offers a compelling combination of properties that make it ideal for consumer electronics in particular.
What exactly is aluminum as used in electronics? While pure aluminum exists, what we typically work with are aluminum alloys—mixtures containing small amounts of other elements like magnesium, silicon, or zinc that enhance specific properties. The 6000-series alloys (particularly 6061) are favorites in the electronics industry due to their excellent balance of strength, workability, and corrosion resistance.
The magic of aluminum lies in its density—just one-third that of steel. This lightweight nature allows designers to create larger enclosures without making devices uncomfortably heavy. Beyond weight considerations, aluminum naturally conducts heat efficiently, making it a natural choice for devices that generate significant thermal output during operation.
We see aluminum everywhere: the sleek bodies of ultrabooks, the frames of high-end smartphones, the chassis of gaming consoles, the housings of external SSDs, and perhaps most importantly, in heat sinks and thermal management systems where its conductivity shines brightest.
Overview of Stainless Steel in Electronics
In contrast to aluminum's lightweight ubiquity, stainless steel carries a different kind of presence in the electronics world—one of premium durability and industrial reliability. Stainless steel isn't just steel; it's an alloy containing at least 10.5% chromium, which creates an invisible protective chromium oxide layer that provides its signature corrosion resistance.
The stainless steel varieties most commonly used in electronics are 304 and 316 grades. The former offers good all-around performance, while 316 provides enhanced corrosion resistance, particularly against chlorides (making it ideal for marine environments or medical applications).
When a product needs to convey uncompromising durability or survive harsh conditions, stainless steel often gets the call. Its substantial weight—three times heavier than aluminum—translates to a perception of quality and solidity that premium brands sometimes leverage intentionally. The cool touch of stainless steel, its resistance to scratches, and its ability to maintain structural integrity under extreme stress make it invaluable in specific applications.
You'll find stainless steel in professional kitchen tablets designed to withstand food splatter and sanitization, premium smartwatches like certain Apple Watch models, industrial control panels exposed to harsh conditions, medical device enclosures that require rigorous sterilization, and server racks where structural integrity trumps weight concerns.
Head-to-Head Comparison
Cost
In the perpetual battle between budget constraints and design aspirations, cost often becomes the deciding factor. Here's how our materials stack up:
Aluminum: The cost advantage clearly belongs to aluminum. Raw material costs typically run 50-60% lower than stainless steel for comparable volumes. The pricing delta widens further when considering manufacturing expenses—aluminum's softer nature means faster machining times, reduced tool wear, and lower energy consumption during production. For projects with tight margins or high-volume consumer products, this difference can significantly impact overall profitability.
Stainless Steel: There's no getting around it—stainless steel commands a premium. Beyond higher raw material costs, its hardness extends production timelines and increases tool replacement frequency. One client of mine switched from stainless to aluminum for a consumer product line and reported approximately 22% manufacturing cost reduction overall. However, the calculus changes when considering product lifespan—premium industrial equipment often justifies higher upfront costs through extended service life and reduced replacement frequency.
Weight
The density difference between these materials creates significant design implications:
Aluminum: At approximately 2.7 g/cm³, aluminum weighs roughly one-third as much as stainless steel. This weight advantage becomes exponentially important as device size increases. For portable electronics like laptops or tablets, the weight savings directly impacts user comfort and usability. I once worked with a team developing a handheld industrial scanner—switching from a steel housing to aluminum reduced weight by 273 grams, dramatically improving user satisfaction in field tests where operators used the device for 8+ hours daily.
Stainless Steel: With density around 8.0 g/cm³, stainless steel creates significantly heavier products. While this can be prohibitive for portable applications, the heft sometimes serves a purpose. In stationary equipment, the added weight provides stability. For certain consumer products, particularly in the premium segment, weight paradoxically becomes a selling point—communicating quality and substance. Weight also provides vibration dampening properties beneficial in certain precision equipment.
Corrosion Resistance
Environmental durability determines where and how devices can be deployed:
Aluminum: In its natural state, aluminum actually forms a thin oxide layer that provides some corrosion resistance. However, this passive protection has limitations, particularly against certain chemicals or saltwater exposure. This is where surface treatments become crucial. Anodizing—electrochemically increasing the thickness of the natural oxide layer—significantly enhances corrosion resistance while opening possibilities for coloration. Type III (hard) anodizing provides even greater protection for extreme environments. Without such treatments, aluminum remains vulnerable, particularly to galvanic corrosion when in contact with dissimilar metals.
Stainless Steel: The corrosion resistance of stainless steel is legendary—and built into the material itself thanks to its chromium content. This inherent protection makes it ideal for harsh environments: outdoors, marine applications, medical settings, or industrial facilities with exposure to chemicals. I've examined 5-year-old stainless steel equipment from food processing plants that looked nearly new despite constant exposure to cleaning agents and moisture. This resistance comes without requiring additional treatments, though passivation processes can enhance performance further.
Strength and Durability
How these materials withstand stress, impacts, and deformation affects both design parameters and product longevity:
Aluminum: With yield strength typically between 35-90 MPa (depending on alloy and treatment), aluminum offers good strength for its weight. However, it's more prone to denting and deformation from impacts. This necessitates design compensations—thicker walls or internal reinforcement—when durability is paramount. Aluminum's excellent strength-to-weight ratio still makes it appropriate for most consumer applications, but designers must account for its limitations.
Stainless Steel: With yield strength ranging from 170-310 MPa for common grades, stainless steel provides superior resistance to physical abuse. Its hardness resists scratching, and its structural integrity holds up under impacts that would dent or deform aluminum. This makes it ideal for ruggedized applications or environments where physical abuse is expected. During product testing for a client's industrial controller, stainless enclosures survived drop tests that consistently damaged aluminum alternatives, despite design reinforcements.
Thermal Conductivity
How materials handle heat transfer directly impacts electronic component performance and lifespan:
Aluminum: With thermal conductivity around 205-250 W/m·K (depending on alloy), aluminum excels at dissipating heat—a critical advantage in electronics design. This property allows enclosures to function as passive heat sinks, drawing thermal energy away from sensitive components. Devices with aluminum exteriors often achieve better sustained performance under load with less throttling. This property has made aluminum the go-to choice for actively cooled devices, from gaming laptops to high-performance tablets.
Stainless Steel: The thermal conductivity of stainless steel (approximately 14-16 W/m·K) presents significant challenges for electronics that generate substantial heat. This poor conductivity can create hotspots and potentially reduce component lifespan without appropriate design accommodations. Successful designs using stainless typically incorporate separate thermal management systems rather than relying on the enclosure for heat dissipation. This limitation explains why you rarely see stainless steel smartphones or laptops—the thermal management challenges would be substantial.
Aesthetics and Finish
The visual and tactile qualities of materials contribute significantly to brand perception and user experience:
Aluminum: The versatility of aluminum's appearance gives designers tremendous flexibility. Natural aluminum provides a modern, technical look, while anodizing opens up virtually unlimited color possibilities without the need for paint. Texture options from glass bead blasting to brushed finishes further expand design choices. Additionally, anodized finishes resist fingerprints better than many alternatives. The material's lightweight nature also allows for more expansive design gestures that might be structurally challenging with heavier materials.
Stainless Steel: The distinctive appearance of stainless steel communicates premium quality and industrial reliability. While color options are more limited, various finish techniques—from mirror polishing to hairline texturing—create distinctive aesthetics. The fingerprint resistance varies by finish, with brushed finishes generally performing better than mirror polishes. The cool-to-touch sensation and substantial weight create a tactile experience that consumers often associate with luxury products, which explains its prevalence in premium wearables.
Manufacturability
Production considerations significantly impact timelines, costs, and design possibilities:
Aluminum: The machinability of aluminum (rating around 100-300% of standard steel benchmarks) means faster production cycles and lower tool replacement costs. Complex shapes can be achieved through various methods: CNC machining, extrusion for consistent profiles, or die casting for intricate designs at scale. Finishing operations are generally straightforward, with anodizing being well-established in manufacturing pipelines. This processing flexibility contributes significantly to aluminum's popularity in mass-produced electronics.
Stainless Steel: Working with stainless steel presents greater manufacturing challenges. Its hardness (50-80 on the Rockwell B scale) increases machining time and tool wear significantly. Cutting speeds often need to be reduced by 50% or more compared to aluminum, with cooling methods carefully controlled to prevent work hardening. Forming operations require greater force, and springback compensation becomes an important consideration. These factors extend production timelines and increase costs, particularly for complex geometries or high-volume production.
Pros and Cons Summary
Aluminum Pros:
Significantly lighter weight (critical for portable devices)
Excellent thermal conductivity for managing component heat
Lower material and manufacturing costs
Greater design flexibility through various forming methods
Wide range of aesthetic finishes and colors through anodizing
Faster and less expensive manufacturing processes
Aluminum Cons:
Less durable and more prone to denting/deformation
Requires surface treatment for optimal corrosion resistance
Potential galvanic corrosion issues when contacting dissimilar metals
Less premium perceived value compared to stainless steel
Less resistance to extreme environments without additional treatments
Stainless Steel Pros:
Exceptional durability and impact resistance
Superior natural corrosion resistance without treatments
Premium look and feel with high perceived value
Excellent performance in harsh environments
Better electromagnetic shielding capabilities
Greater resistance to extreme temperatures
Stainless Steel Cons:
Significantly heavier weight limits portability
Poor thermal conductivity complicates heat management
Higher material and manufacturing costs
More challenging and time-consuming to machine
Limited color options compared to aluminum
Requires more energy during production (environmental consideration)
Real-World Applications
When Aluminum Shines
Aluminum finds its sweet spot in applications where weight, thermal management, and cost efficiency take priority:
Consumer Electronics: The dominance of aluminum in laptops, tablets, and smartphones stems from its perfect balance of weight, strength, and thermal properties. Apple's shift to aluminum unibody designs revolutionized portable computing, demonstrating how the material enables thinner, lighter devices without sacrificing structural integrity.
Cooling-Critical Devices: Gaming hardware, high-performance computing equipment, and multimedia devices leverage aluminum's thermal conductivity. I recently consulted on a project where simply switching the enclosure from plastic to aluminum improved CPU sustained performance by 22% without any other thermal management changes.
Cost-Sensitive Products: For products where margins matter greatly, aluminum's lower processing costs provide advantages. A consumer electronics startup I advised was able to maintain premium build quality despite tight budget constraints by optimizing their aluminum enclosure design, where stainless would have been prohibitively expensive at their production volume.
Colorful or Design-Forward Products: When distinctive aesthetics or color matching to brand standards is crucial, aluminum's anodizing capability provides unmatched versatility.
When Stainless Steel Dominates
Stainless steel becomes the clear choice in scenarios where durability, environmental resistance, and premium positioning are paramount:
Industrial and Medical Equipment: Devices deployed in factories, healthcare settings, or outdoor installations benefit from stainless steel's ability to withstand harsh conditions, chemical exposure, and frequent cleaning with aggressive agents. One medical device manufacturer I worked with exclusively uses 316 stainless for equipment destined for surgical settings due to its ability to withstand repeated sterilization cycles.
Premium Consumer Products: In the luxury segment, the substantial feel of stainless steel helps justify higher price points. The tactile experience of a stainless steel product communicates quality in a way aluminum rarely achieves—explaining why high-end smartwatches frequently feature the material despite its weight penalty.
Extreme Environment Deployment: Equipment destined for marine environments, outdoor installation, or chemical exposure naturally gravitates toward stainless solutions. A control system installed on offshore oil platforms demonstrated zero corrosion issues after three years in salt spray conditions—performance that would be challenging to achieve with aluminum without significant additional protection.
EMI-Sensitive Applications: When electromagnetic interference shielding is crucial, stainless steel's superior performance sometimes outweighs its drawbacks.
Hybrid Approaches
Increasingly, manufacturers are exploring combined approaches to leverage the strengths of both materials:
Aluminum Frame with Steel Reinforcement: Computer server chassis often utilize this approach—aluminum provides the lightweight structure and thermal management while strategic stainless steel components reinforce high-stress areas.
Composite Designs: Some high-end smartphones use stainless steel structural elements combined with aluminum thermal components under glass or ceramic exteriors.
Material-Appropriate Zoning: Designing products where each section uses the ideal material—aluminum where weight and thermal performance matter most, stainless where durability is critical.
Conclusion
The choice between aluminum and stainless steel ultimately comes down to understanding your specific product requirements and prioritizing accordingly. Neither material represents an absolute "best choice"—each offers distinct advantages that align with different design goals.
For portable consumer electronics where weight, thermal management, and cost efficiency drive decisions, aluminum typically provides the optimal balance. Its versatility in manufacturing and finishing further cements its position as the go-to material in this space.
Conversely, when developing products for harsh environments, industrial applications, or premium market positioning where durability and longevity justify higher costs, stainless steel delivers compelling benefits that often outweigh its weight and manufacturing challenges.
The most successful product teams I've worked with approach material selection methodically—weighing functional requirements, user expectations, manufacturing constraints, and cost targets rather than defaulting to what's familiar or trendy. Sometimes this analysis leads to unexpected choices or innovative hybrid approaches that deliver competitive advantages.
As electronics continue evolving—becoming simultaneously more powerful and more portable—material selection remains a crucial element in successful product development. Understanding these materials deeply allows designers and decision-makers to make choices that balance performance, user experience, and business requirements effectively.
What's your experience with these materials? Have you found creative ways to leverage the strengths of each while minimizing their limitations? Share your insights and questions in the comments—I'm always interested in hearing how other teams navigate these fundamental design decisions.