Made-in-China: Still the Backbone of the Global Electronics Supply Chain
Explore why "Made in China" remains the backbone of global electronics manufacturing despite rising interest in "Make in India." This article breaks down supply chain realities, sourcing trends, and strategic insights for hardware electronics companies navigating today's shifting landscape.
JoeZ
6/3/20254 min read
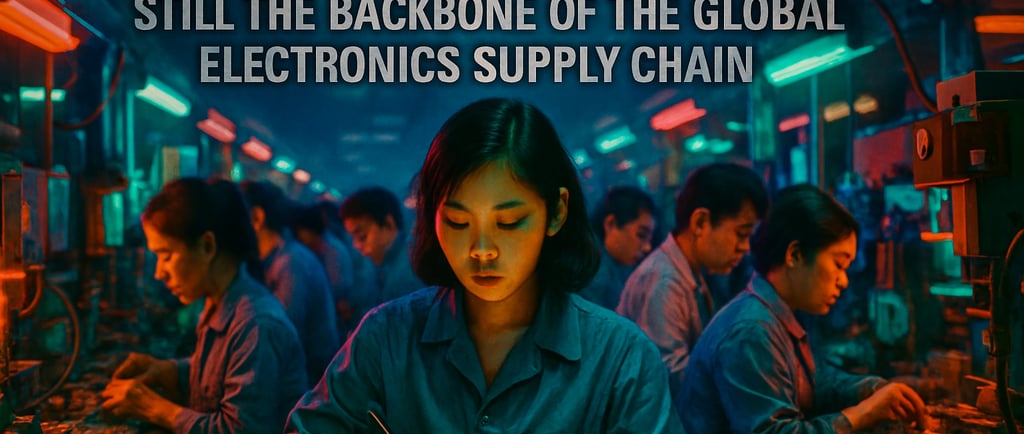
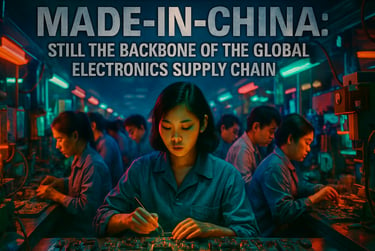
In recent years, the global electronics industry has witnessed mounting pressure to diversify its supply chain away from China. Fueled by geopolitical tensions, trade wars, rising tariffs, and recent policy interventions like India’s Production-Linked Incentive (PLI) scheme, businesses across the world have explored shifting their sourcing strategies. However, despite the narrative of “friend-shoring,” China remains the dominant force in the electronics manufacturing ecosystem. For hardware electronics companies navigating this landscape, it’s crucial to understand why “Made in China” continues to be irreplaceable in many critical aspects.
The Depth of China’s Supply Chain Ecosystem
China’s electronics manufacturing prowess is not a product of mere low-cost labor. Over the past two decades, the country has built a dense, highly integrated ecosystem that includes:
Component Manufacturing: From resistors, capacitors, semiconductors, PCBs to advanced chips and sensors, China produces a significant share of the world's electronic components.
Tooling and Molding: Injection molds, die casting, and stamping tools that power rapid prototyping and high-volume production are deeply concentrated in Southern China.
R&D Infrastructure: Shenzhen, Suzhou, and Chengdu have grown into innovation hubs with robust R&D talent, supplier development, and IP generation.
Logistics and Infrastructure: Deep-sea ports, high-speed rail networks, and bonded zones allow rapid movement of goods, driving just-in-time production models.
This deep integration makes it extraordinarily difficult for other nations to replicate China’s manufacturing capacity within a short timeframe.
The "Assembly in India, Powered by China" Phenomenon
India’s ambition to become a global electronics hub is well-intentioned and timely. The PLI scheme has successfully attracted global players like Apple, Samsung, and Foxconn to establish or expand assembly operations in India. However, these operations often rely heavily on Chinese components and tooling.
The internal supply chain gaps are evident:
Semiconductors: India imports over 90% of its semiconductors, with China and Taiwan as major sources.
Passive Components: India lacks the scale and quality consistency needed for large-scale production of capacitors, inductors, and resistors.
Tooling and Fixtures: Precision tools and jigs continue to be sourced from China due to better cost-performance ratios.
Skilled Labor and Industrial Engineering: China’s workforce has had over two decades of experience in high-volume, high-precision production environments.
While India assembles, China continues to provide the engine that powers the downstream production.
Why Companies Still Prefer China
Speed to Market: In Shenzhen, you can move from concept to production in weeks, thanks to the density of suppliers and prototyping facilities.
Supplier Collaboration: Companies benefit from co-development with local suppliers, reducing product development timelines.
IP and Design Ownership: With China’s recent crackdown on IP theft and the rise of ODMs (Original Design Manufacturers), the fear of losing designs has been significantly mitigated.
Cost Efficiency at Scale: Economies of scale in materials procurement, logistics, and manufacturing drive costs lower.
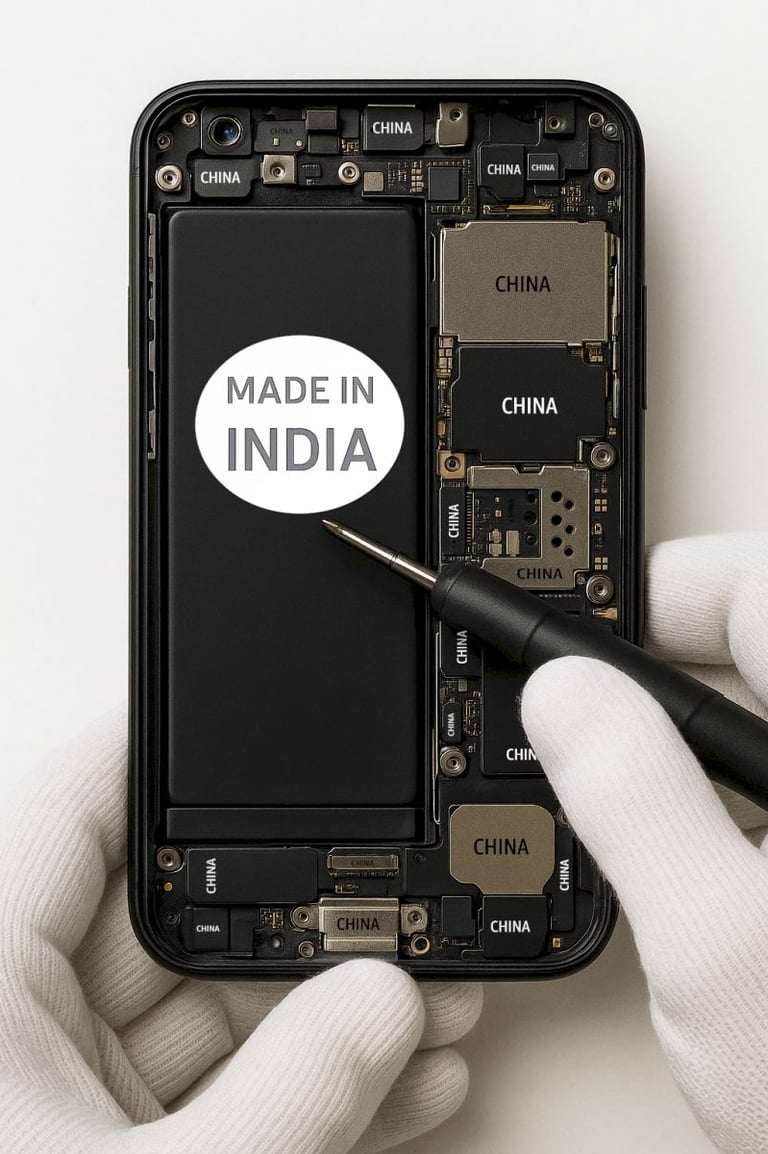
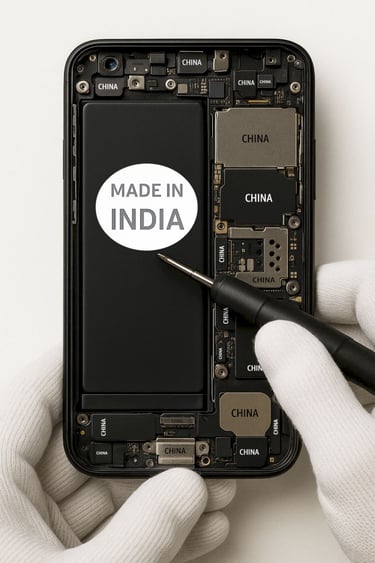
Challenges Facing China's Dominance
Despite its stronghold, China is not without its vulnerabilities:
Rising Labor Costs: Wages in China have steadily increased, pushing low-margin products to Southeast Asia.
Geopolitical Pressures: Trade restrictions, export bans, and the US-China tech war have added layers of complexity.
Regulatory Scrutiny: Environmental and compliance standards have tightened, increasing the cost of doing business.
Yet, these headwinds have not significantly diminished China’s centrality; rather, they have made diversification more strategic than complete decoupling.
Strategies for Hardware Companies Moving Forward
China+1 Strategy: Instead of full relocation, companies are adding capacity in countries like Vietnam, India, and Mexico while keeping R&D and high-value components in China.
Supply Chain Mapping: Conduct thorough audits to understand which components are critical and their country-of-origin risks.
Design for Localization: Develop product architectures that allow flexible sourcing based on regional availability.
Partner with Tier-1 Suppliers: Leading Chinese suppliers often have global footprints and can help ease transition into other geographies.
Invest in India Gradually: Leverage India for final assembly and explore joint ventures to build upstream capabilities over time.
Conclusion: The Future is Hybrid, Not Binary
The idea of overnight reshoring or fully shifting away from China is, as one industry veteran called it, "pure hopium." For now, “Made in China” is less about geographic origin and more about a deeply entrenched value chain that enables rapid innovation, cost efficiency, and scalability.
India, Southeast Asia, and Mexico will grow as complementary hubs, particularly for final assembly, logistics optimization, and diversification against geopolitical risk. But until countries develop full-stack manufacturing capabilities with the same depth and scale as China, the global electronics supply chain will remain China-centric.
For hardware electronics companies, the future lies in leveraging the best of both worlds: the robustness of China and the rising potential of new geographies. It is not about choosing one over the other but building a smart, hybrid strategy that ensures resilience, efficiency, and speed.
Call to Action
If you are a hardware startup, OEM, or supply chain leader evaluating your sourcing roadmap, now is the time to:
Reevaluate your dependency matrix.
Revisit BOM structures.
Engage with China-based ODMs/OEMs who are investing globally.
Explore partnerships with emerging Indian manufacturers for final assembly.
Ultimately, winning in the next decade of electronics innovation will depend not on abandoning China, but on integrating intelligently across the evolving global supply chain landscape.