Leveraging Metal Fabrication for Customization and Prototyping in Electronics Innovation
Metal fabrication is the backbone of customization and rapid prototyping, two elements that are absolutely vital for pushing the envelope in electronics innovation. Whether you’re dreaming up tailored designs that fit like a glove or racing to test a prototype before the next funding pitch, this craft has your back.
2/26/20255 min read
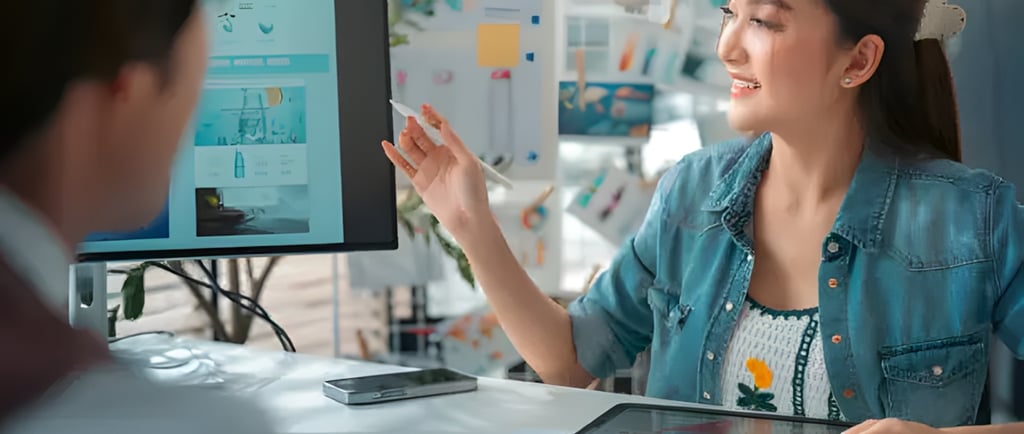
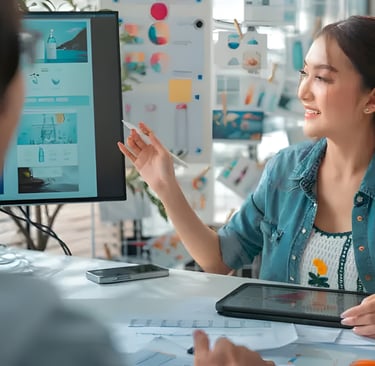
Picture this: You’re a designer hunched over your desk, sketching out the next big thing in electronics—a sleek, lightweight wearable that tracks health metrics in real time. Or maybe you’re a decision-maker, pacing the office, weighing options to get a groundbreaking IoT device from concept to market before the competition beats you to it. In either case, there’s one unsung hero that can make or break your project: metal fabrication. It’s not just about bending steel or cutting sheets—it’s about turning your wildest ideas into reality, fast.
Metal fabrication is the backbone of customization and rapid prototyping, two elements that are absolutely vital for pushing the envelope in electronics innovation. Whether you’re dreaming up tailored designs that fit like a glove or racing to test a prototype before the next funding pitch, this craft has your back. Let’s dive into how it works, why it matters, and how it’s shaping the future of electronics—one custom part at a time.
The Power of Customization Through Metal Fabrication
So, what exactly is metal fabrication? At its core, it’s the art of shaping metal into something useful—think cutting, bending, welding, and assembling. But for you, the designers and deciders in electronics, it’s so much more than that. It’s your ticket to creating parts that don’t just fit the specs but define them. Need a custom enclosure for that delicate circuit board? Done. How about a one-of-a-kind chassis for a wearable that’s as stylish as it is functional? Metal fabrication delivers.
I’ve seen this firsthand talking to a friend who designs audio gear. He once told me about a project where off-the-shelf enclosures just wouldn’t cut it—the sound quality dipped because of poor fit and interference. So, he turned to a local fabricator who used laser cutting and precision bending to whip up a custom aluminum housing. The result? Crystal-clear audio and a product that stood out on the shelf. That’s the kind of flexibility metal fabrication brings to the table—it lets you tailor every detail to your vision.
For electronics, where every millimeter and every ounce matters, this is a game-changer. Imagine crafting a heat sink that’s perfectly contoured to your high-performance chip, or a lightweight frame for a drone that balances strength and agility. With techniques like CNC machining or sheet metal forming, you’re not stuck with generic parts—you’re building exactly what your project demands. It’s like having a bespoke suit made for your tech, and who doesn’t love a perfect fit?
Rapid Prototyping Enabled by Metal Fabrication
Now, let’s talk speed. In the electronics world, time is everything. You’ve got a brilliant idea, but if it takes six months to test it, someone else might beat you to the punch. That’s where rapid prototyping comes in—and metal fabrication is the secret sauce that makes it happen.
Prototyping is all about taking your concept and turning it into something you can hold, test, and tweak. Metal fabrication turbocharges this process with tools like CNC machining, laser cutting, and even 3D metal printing. These aren’t just buzzwords—they’re your fast track to a working model. Say you’re designing a new component for a drone—a lightweight motor mount that needs to withstand serious vibration. With CNC machining, you can go from a digital sketch to a metal prototype in a matter of days, not weeks. Test it, tweak it, repeat. That’s the beauty of rapid iteration.
I once chatted with an engineer at a startup who was racing to pitch a new IoT sensor to investors. They had a tight deadline—two weeks to show something tangible. Using laser-cut steel and a quick weld job, they mocked up a rugged housing that not only worked but looked the part. The investors were sold, and that prototype became the foundation for a full product line. Without metal fabrication’s speed, they’d still be waiting on plastic molds or overseas shipments.
The payoff? You get to fail fast, learn faster, and refine your design before the stakes get too high. In electronics, where innovation moves at warp speed, that’s not just an advantage—it’s a necessity.
Why Metal Fabrication is Vital for Electronics Innovation
Let’s zoom out for a sec. Why does metal fabrication matter so much for electronics specifically? It’s all about the synergy. Metal isn’t just strong—it’s conductive, durable, and a champ at managing heat. These are the building blocks of modern tech, from smartphones to electric vehicles. And as designers and deciders, you know the pressure’s on to make devices smaller, smarter, and more sustainable. Metal fabrication rises to that challenge.
Take miniaturization, for instance. As gadgets shrink, every component has to pull double duty. A tiny metal bracket might need to hold a circuit in place and dissipate heat. With precision fabrication, you can craft parts that do both, no compromise required. Or think about IoT devices—those little sensors popping up everywhere. They need enclosures that are tough enough for the real world but light enough to keep costs down. Metal fabrication nails that balance.
Then there’s the sustainability angle. I was reading about a company making electric vehicle battery casings—super lightweight aluminum, fabricated to exact specs. Not only did it cut the car’s weight (hello, better range!), but the metal was recyclable too. That’s the kind of forward-thinking design metal fabrication enables. Whether it’s a next-gen smartphone or a solar-powered gadget, this craft helps you innovate without breaking the planet.
For you, the folks steering the ship, it’s about staying ahead. Metal fabrication doesn’t just keep up with trends—it drives them. It’s the tool that lets you push boundaries while keeping performance rock-solid.
Practical Applications and Success Stories
Okay, let’s get real—where’s this actually happening? The applications are everywhere, and the success stories are inspiring. Take aerospace, for example. Companies like Boeing use metal fabrication to prototype custom brackets and housings for avionics systems. These parts have to be featherlight yet tough as nails, and fabrication delivers every time. One designer I know swears by titanium CNC milling for these jobs—pricey, but worth it for the precision.
Medical tech is another hot spot. Think about a surgical robot—those intricate metal arms need to be custom-fitted to the tiniest tolerances. A fabricator friend once showed me a prototype for a robotic scalpel holder, cut from stainless steel in under 48 hours. That kind of speed and accuracy is saving lives, not just impressing clients.
And don’t sleep on consumer tech. Ever wonder how startups crank out slick prototypes for crowdfunding campaigns? Metal fabrication is often the answer. I saw a Kickstarter for a modular smart speaker—the team used laser-cut aluminum panels to build a prototype that looked production-ready. Backers ate it up, and they hit their goal in a week.
The best part? This isn’t just for the big players anymore. Tools like desktop CNC machines and affordable 3D metal printers are bringing fabrication to small shops and startups. You don’t need a massive budget to get started—just a solid design and a fabricator who gets it. And once you’ve got that prototype dialed in, scaling up is a breeze. The same process that built your one-off can churn out a thousand units when you’re ready.
Conclusion
So, where does this leave us? Metal fabrication isn’t some dusty old trade—it’s a powerhouse for customization and rapid prototyping, especially in electronics. For you designers, it’s the freedom to craft exactly what you envision, no settling required. For you deciders, it’s the speed and scalability to turn bold ideas into market wins. Together, it’s the engine driving innovation in an industry that never slows down.
Next time you’re sketching a new device or pitching a game-changer, think about metal fabrication. It’s not just about making parts—it’s about making possibilities. Whether you’re tinkering in a garage or leading a corporate R&D team, this is your chance to build something extraordinary. So, grab that concept, call up a fabricator, and let’s see what you can create. The future of electronics is waiting—and it’s got your name on it.