Key Metal Fabrication Techniques for Electronics: Choosing the Right Method for Precision and Efficiency
Metal fabrication plays a crucial role in this process, ensuring that electronic devices maintain durability, performance, and miniaturization while withstanding environmental factors like heat and electromagnetic interference.
2/25/20254 min read
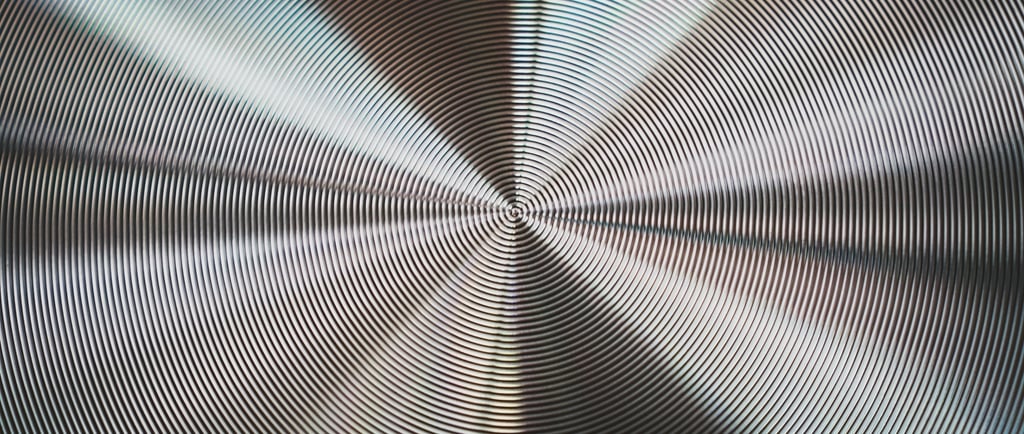
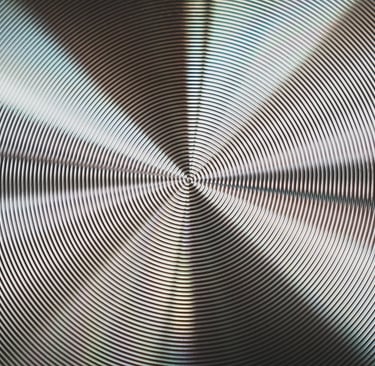
In the world of electronics, precision isn’t just a luxury—it’s a necessity. Whether it’s a microchip, a connector, or a protective casing, every component must meet tight tolerances to function reliably. Metal fabrication plays a crucial role in this process, ensuring that electronic devices maintain durability, performance, and miniaturization while withstanding environmental factors like heat and electromagnetic interference.
For designers and decision-makers in electronics development, understanding the right fabrication techniques can streamline production, optimize costs, and enhance product quality. This article explores three key metal fabrication techniques—laser cutting, CNC machining, and stamping—each offering unique advantages depending on project requirements. By the end, you'll have a clearer understanding of which method suits your needs best.
Laser Cutting: Precision at the Speed of Light
What is Laser Cutting?
Laser cutting is a technology that uses a high-powered laser beam to cut through materials by melting, burning, or vaporizing them. Common laser types used in metal fabrication include:
CO2 Lasers: Ideal for cutting thin metals, plastics, and non-metals.
Fiber Lasers: Best suited for cutting reflective metals like aluminum, copper, and stainless steel.
This process enables manufacturers to create highly intricate designs with exceptional accuracy, making it a favorite for applications where precision is paramount.
Why It’s Great for Electronics
High Precision: Allows for detailed, complex cuts that are difficult to achieve with traditional mechanical methods.
Minimal Material Waste: Since the laser is highly focused, it reduces excess material loss and produces clean edges, eliminating the need for secondary processing.
Works with Thin Metals: Particularly useful for delicate components, such as thin metal shields used in circuit boards.
Real-World Applications in Electronics
Cutting intricate patterns in circuit boards to create pathways for electrical currents.
Fabricating custom enclosures or casings for electronic devices, ensuring protection while maintaining a sleek design.
Creating stencils for solder paste application in PCB assembly, improving efficiency in the production process.
Things to Consider
Not ideal for very thick materials, as the laser beam's penetration depth is limited.
Heat-affected zones (HAZ) can slightly alter the properties of the material, which could be a concern for delicate electronic parts.
Higher costs compared to stamping, making it less suitable for mass production.
CNC Machining: The Art of Subtractive Manufacturing
What is CNC Machining?
CNC (Computer Numerical Control) machining is a subtractive manufacturing process that removes material from a solid block using precision tools like mills, lathes, and drills. This method is computer-controlled, ensuring consistent and repeatable precision, making it an excellent choice for complex and highly detailed electronic components.
Advantages for Electronics
Exceptional Accuracy: CNC machines can achieve tight tolerances, which is critical in electronics manufacturing where even minor deviations can cause malfunctions.
Capability for Complex 3D Shapes: Unlike laser cutting, which is primarily for 2D patterns, CNC machining can produce intricate three-dimensional components.
Great for Prototyping: The ability to create custom parts quickly without the need for expensive tooling makes CNC machining perfect for small batch production and prototyping.
Examples in Electronics
Machining heat sinks for electronic devices to enhance thermal management.
Crafting connectors, sockets, or mounting brackets with precise fits to ensure seamless integration into assemblies.
Producing custom hardware such as screws and fasteners tailored for specific electronic enclosures.
Limitations
Slower production times compared to stamping, especially for intricate or large parts.
Higher costs for small batches, as material waste and machining time contribute to expenses.
More material waste due to its subtractive nature, making it less eco-friendly compared to other methods.
Stamping: Mass Production with Consistency
What is Stamping?
Stamping is a high-speed manufacturing process in which a metal sheet is pressed into a die to create a specific shape. It includes variations such as:
Progressive Stamping: Involves multiple stages, where a strip of metal moves through a series of dies, shaping the part step by step.
Deep Draw Stamping: Used for creating deep, cup-like structures, common in battery casings and enclosures.
Benefits for Electronics Manufacturing
High-speed production, making it the most cost-effective option for high-volume manufacturing.
Uniform and consistent parts, ensuring reliability across thousands or even millions of units.
Cost-effective once the initial tooling is in place, making it ideal for large-scale production.
Common Applications in Electronics
Manufacturing connectors, terminals, and pins used in circuit boards.
Producing electromagnetic interference (EMI) shielding components to prevent signal disruptions.
Creating brackets and clips for structural support within electronic devices.
Considerations
High initial investment for designing and fabricating stamping dies.
Limited flexibility for design changes, as modifying a die can be costly and time-consuming.
Best suited for simpler shapes, as highly intricate designs may require additional machining.
Choosing the Right Technique: A Comparative Look
When to Use Each Technique
Laser Cutting: Ideal for prototypes, small batches, or intricate designs that require quick turnaround times.
CNC Machining: Best for complex, high-precision parts in low-to-medium production volumes.
Stamping: Perfect for high-volume production of consistent, simpler components at a lower per-unit cost.
Factors to Consider
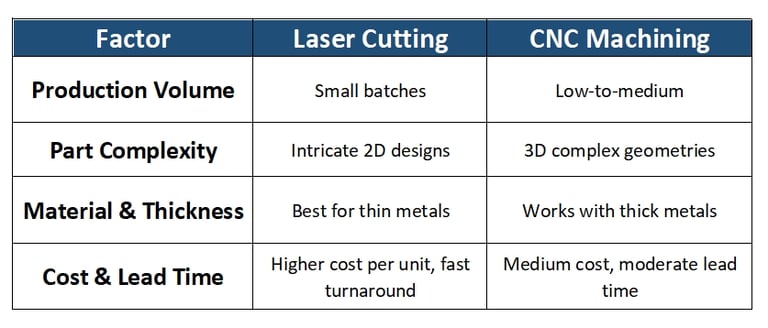
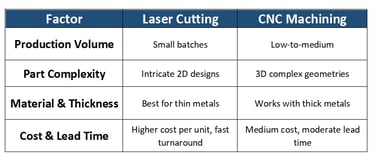
Conclusion
Each of these metal fabrication techniques—laser cutting, CNC machining, and stamping—offers unique strengths for electronics manufacturing. Whether you need high precision, flexibility, or cost-efficient mass production, choosing the right method can significantly impact the success of your product.
As technology continues to advance, so do these fabrication techniques, making electronics manufacturing more precise and efficient than ever before. If you’re designing a new electronic product, carefully evaluate your volume, complexity, and budget to determine which method aligns best with your goals.
Looking to optimize your manufacturing process? Get in touch with fabrication specialists to explore the best options for your next project.