ISO 9001 Certification for Electronics Manufacturers: A Complete Guide
ISO 9001 certification isn't just a box to check—it’s a strategic move that can elevate your business, streamline operations, and open doors to new markets. But what does it really take to get certified? How does it impact your design and production processes?
2/18/20254 min read
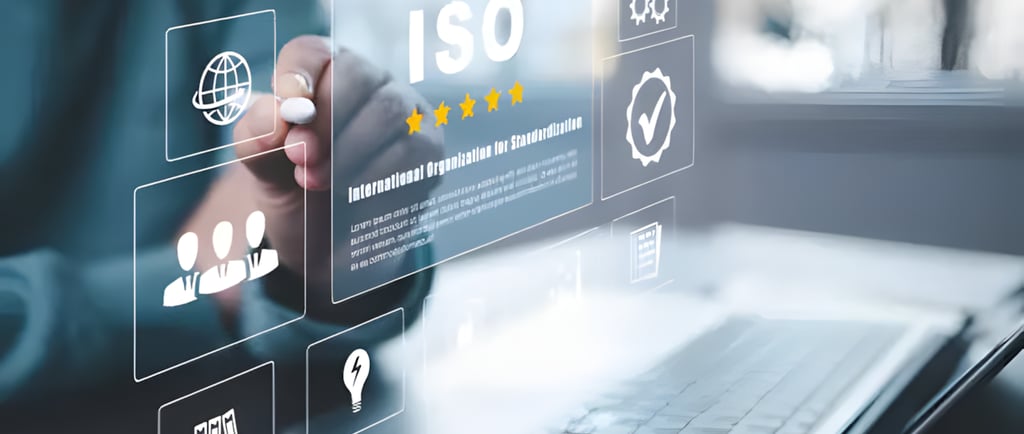
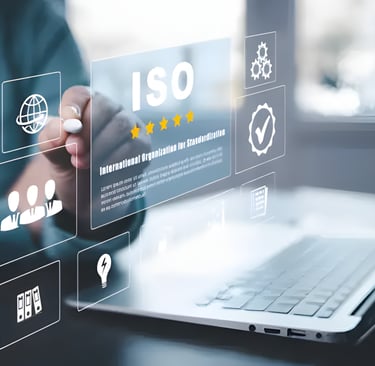
If you’re involved in electronics manufacturing—whether as a designer, engineer, or business decision-maker—you already understand the stakes. Quality isn’t just a buzzword; it’s the foundation of your reputation, customer trust, and bottom line. That’s where ISO 9001 comes in.
ISO 9001 certification isn't just a box to check—it’s a strategic move that can elevate your business, streamline operations, and open doors to new markets. But what does it really take to get certified? How does it impact your design and production processes? Let’s break it down in a way that’s practical and actionable.
1. Understanding ISO 9001 Certification
What is ISO 9001?
ISO 9001 is an internationally recognized standard for quality management systems (QMS). It provides a framework for businesses to consistently meet customer and regulatory requirements while driving continuous improvement.
For electronics manufacturers, this means ensuring every circuit board, sensor, or chip you produce meets high-quality standards—not just occasionally, but every time.
Why is ISO 9001 Crucial for Electronics Manufacturing?
Electronics manufacturing is a high-precision industry where minor defects can lead to major failures. ISO 9001 certification helps manufacturers:
Improve product reliability and reduce defects.
Streamline supply chain management.
Meet international regulatory requirements, making global expansion easier.
Gain a competitive edge in B2B partnerships, as many large companies require ISO 9001 compliance.
Create a culture of continuous improvement, benefiting both product quality and operational efficiency.
For example, companies like Foxconn, a leading electronics manufacturer, rely on strict quality control measures to ensure that their products meet the expectations of clients such as Apple and Dell. Without a robust QMS like ISO 9001, defects could lead to costly recalls and reputational damage.
2. The Benefits of ISO 9001 for Electronics Manufacturers
Enhanced Product Quality & Consistency
ISO 9001 ensures that your manufacturing process is built on repeatable, well-documented procedures. This reduces defects and improves reliability, which is crucial in electronics, where a single faulty component can compromise an entire system.
A real-world example is Intel’s microprocessor production, where even a minor defect in chip fabrication can result in massive performance issues. ISO 9001 helps companies implement rigorous quality control processes to prevent such failures.
Operational Efficiency & Cost Savings
By streamlining workflows, reducing rework, and minimizing waste, ISO 9001 directly improves efficiency and lowers production costs. Manufacturers often see significant improvements in yield rates and reductions in material waste after implementing ISO 9001 principles.
For instance, Sony’s TV production plants implemented ISO 9001-based lean manufacturing techniques, resulting in a 20% reduction in production waste and a notable increase in product reliability.
Regulatory Compliance & Market Access
Compliance with ISO 9001 often aligns with other industry regulations (such as IPC standards for PCB manufacturing or ISO 13485 for medical electronics). Being certified makes it easier to work with large corporations, government agencies, and international clients.
A good example is medical device manufacturers that must meet stringent regulations like the FDA’s Quality System Regulation (QSR). Many of these companies rely on ISO 9001 as a foundation to comply with ISO 13485, ensuring that life-critical devices meet safety standards.
Customer Trust & Brand Reputation
Electronics buyers—whether OEMs, distributors, or end users—prefer working with certified suppliers because it signals reliability. An ISO 9001 certificate can be a marketing tool that sets you apart from competitors.
Take Tesla, for example. While not exclusively reliant on ISO 9001, the company enforces strict quality control measures across its supply chain, ensuring all electronic components in its vehicles meet high standards.
Risk Management & Business Continuity
The standard encourages manufacturers to take a risk-based approach to quality, helping to identify potential issues before they become major problems. This proactive mindset minimizes disruptions and keeps operations running smoothly.
An example is Boeing’s supply chain management, where ISO 9001-aligned risk assessments help mitigate potential production delays and defects in avionics systems.
3. Key ISO 9001:2015 Requirements for Electronics Manufacturers
a. Quality Management System (QMS) Implementation
ISO 9001 requires companies to establish a formal QMS with documented procedures for quality control. This includes defining clear quality objectives, standardizing processes, and ensuring traceability of components and final products.
b. Process-Based Approach
Electronics manufacturers must identify and document all processes—from sourcing raw materials to final product testing. A process-driven approach ensures each stage in manufacturing is optimized for quality and efficiency.
c. Documented Information & Record-Keeping
Accurate documentation of work instructions, material traceability, testing procedures, and corrective actions is essential. This makes it easier to track defects, ensure compliance, and improve processes over time.
d. Leadership Commitment & Employee Involvement
Top management must be actively involved in the QMS. Additionally, employees need proper training on quality policies and procedures to ensure consistent application of ISO 9001 standards.
e. Risk-Based Thinking & Continuous Improvement
Manufacturers must proactively identify risks (such as component failures or supplier inconsistencies) and take preventive measures. Continuous improvement is a core part of ISO 9001, ensuring that quality processes evolve with technology and market demands.
4. How to Get ISO 9001 Certified: A Step-by-Step Process
Step 1: Conduct a Gap Analysis
Assess your current quality management processes against ISO 9001 requirements. Identify areas that need improvement before moving forward with certification.
Step 2: Develop a Quality Management System (QMS)
Create a formal QMS with well-documented processes, from design to production. This includes defining quality objectives, creating work instructions, and setting up traceability mechanisms.
Step 3: Train Employees
Ensure all employees, from engineers to production line workers, understand ISO 9001 requirements. Training helps foster a culture of quality and continuous improvement.
Step 4: Conduct Internal Audits
Perform internal audits to test your QMS effectiveness. This helps catch potential non-conformities before the formal certification audit.
Step 5: Undergo a Certification Audit
A third-party certification body will conduct an official audit to verify compliance. If successful, you’ll receive ISO 9001 certification. If there are gaps, corrective actions must be taken.
Step 6: Maintain Certification
ISO 9001 isn’t a one-time achievement—it requires ongoing audits and improvements to stay compliant. Regularly review and refine processes to maintain certification.
Conclusion
ISO 9001 certification is more than a formality—it’s a game-changer for electronics manufacturers. It enhances quality, improves efficiency, and builds customer trust. If you’re serious about delivering high-quality, reliable electronics, now is the time to take action.
Ready to start your ISO 9001 journey? Conduct a gap analysis, implement a QMS, and take the first step toward certification today!