Introduction to Metal Fabrication in Electronics Manufacturing
Understanding metal fabrication isn’t just a nice-to-have—it’s a must. It’s the backbone of creating the components that protect, support, and enhance the devices we rely on every day. In simple terms, metal fabrication is the art and science of turning raw metal into finished products through cutting, bending, and assembling.
2/25/20257 min read
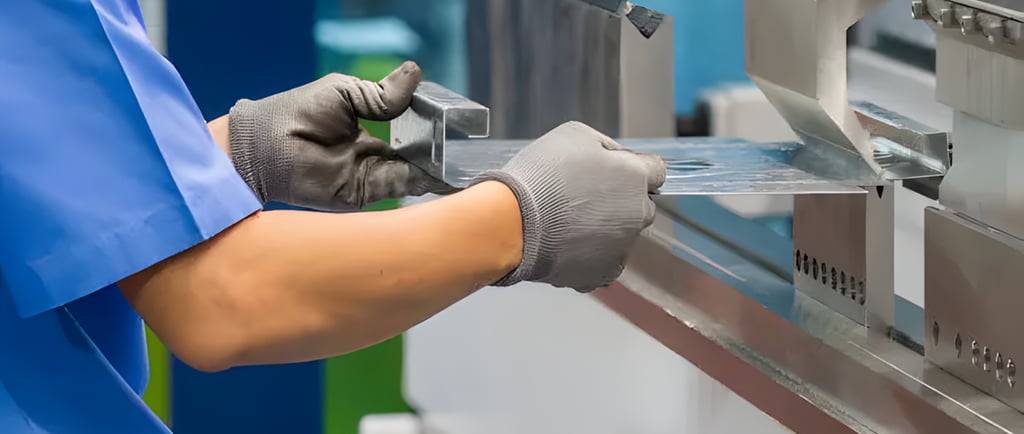
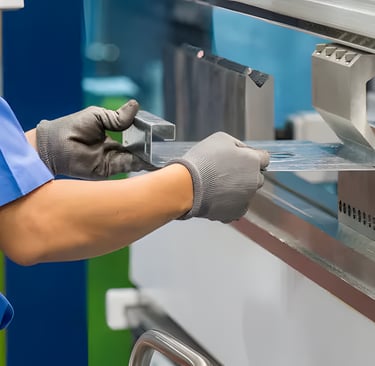
Have you ever picked up your smartphone, run your fingers over its sleek metal casing, and wondered how it got that way? Or maybe you’ve marveled at the sturdy frame of your laptop, feeling that satisfying heft that screams durability. I know I have. The first time I held a premium smartphone, I couldn’t help but admire how solid and well-crafted it felt—like it was built to last. Little did I know back then that behind that impressive exterior was a fascinating process called metal fabrication.
For designers and decision-makers in electronics development, understanding metal fabrication isn’t just a nice-to-have—it’s a must. It’s the backbone of creating the components that protect, support, and enhance the devices we rely on every day. In simple terms, metal fabrication is the art and science of turning raw metal into finished products through cutting, bending, and assembling. And trust me, it’s way more interesting (and critical) than it might sound at first.
In this article, we’re going to dive deep into metal fabrication in electronics manufacturing. We’ll explore what it is, why it matters so much in your field, and how it all comes together to create those enclosures, chassis, and heat sinks you spec out in your designs. I’ll keep it conversational, relatable, and packed with examples—because I want you to walk away feeling like you’ve got a solid grip on this process, whether you’re sketching concepts or signing off on production runs. So, let’s get started!
Why Metal Fabrication is a Big Deal in Electronics
If you’re designing or deciding on components for an electronics product, you’ve likely got a laundry list of priorities: functionality, reliability, cost, aesthetics. Metal fabrication ticks all those boxes and then some. Let’s break down why it’s such a game-changer in your world.
Protection and Durability: The Knight’s Armor for Your Tech
Picture this: your latest device—say, a tablet—is sitting on a table. Someone knocks it off (oops), and it hits the floor. Without a tough exterior, those delicate internals—circuit boards, chips, batteries—could be toast. That’s where metal fabrication steps in like a knight in shining armor.
Metal enclosures and chassis shield your electronics from the chaos of the real world: drops, dust, moisture, even the occasional coffee spill. I’ve seen it firsthand in a project where we had to ruggedize a control unit for a factory floor. The environment was brutal—vibrations, heat, airborne grit—and a flimsy plastic housing just wasn’t cutting it. We switched to a steel enclosure, and the difference was night and day. That’s the kind of protection metal brings to the table, ensuring your designs survive whatever users (or life) throw at them.
Precision and Functionality: Fitting Like a Glove
Designing electronics isn’t just about keeping things safe—it’s about making sure everything works together seamlessly. Metal fabrication delivers precision that’s hard to beat. Think of it like crafting a custom puzzle piece: every bracket, mount, or frame has to fit just right, holding components securely and keeping them aligned.
Take a laptop chassis, for example. It’s not just a metal box—it’s a meticulously shaped structure that cradles the motherboard, slots the hard drive into place, and ensures nothing shifts during a bumpy commute. A few years back, I worked on a prototype where a misaligned bracket caused overheating issues because the heat sink wasn’t sitting flush. A quick redesign with tighter tolerances fixed it, and that’s the kind of accuracy metal fabrication makes possible. For you, as a designer, it means your vision translates perfectly from CAD to reality.
Electromagnetic Shielding: Keeping the Noise Out
Here’s something you might not think about every day but definitely impacts your designs: electromagnetic interference (EMI). It’s the invisible gremlin that can make your device glitch, slow down, or fail entirely. Sources like Wi-Fi signals, nearby machinery, or even another gadget can throw off your electronics if they’re not protected.
Metal’s a superhero here. Fabricated metal parts—like enclosures or shielding plates—block EMI, acting like a Faraday cage. Imagine a metal box stopping radio waves from messing with a sensitive receiver. That’s what’s happening inside your devices. In critical applications like medical devices or aerospace electronics, where a glitch isn’t just annoying but potentially disastrous, this shielding is non-negotiable. It’s one more reason metal fabrication is a go-to for reliability-focused designs.
The Parts You Rely On
So, what exactly are we talking about when we say “metal fabricated components”? Here’s a quick rundown of the usual suspects in electronics:
Enclosures and Housings: The outer shells of phones, tablets, and industrial controllers.
Chassis and Frames: The internal skeletons that give structure and support.
Heat Sinks: Finned metal blocks that pull heat away from processors and chips.
Brackets and Mounts: Small but mighty pieces that keep everything where it belongs.
Connectors and Terminals: Metal bits that ensure solid electrical connections.
Each of these plays a starring role in your designs, and metal fabrication is how they come to life.
Metal vs. the Alternatives
Sure, plastics and composites have their place—lightweight, cheap, easy to mold. But metal? It’s the heavy hitter. It’s stronger (think steel), better at managing heat (hello, aluminum), and unbeatable for EMI protection. Plus, let’s be honest: metal just feels premium. When I pick up a device with a metal finish, it’s got that high-quality vibe that plastic can’t touch. For high-end consumer products or rugged industrial gear, metal’s advantages often outweigh the trade-offs.
How Metal Fabrication Works: From Raw Material to Finished Component
Alright, now that we’ve covered why metal fabrication matters, let’s get into the how. How does a sheet of aluminum or steel turn into that perfect enclosure or heat sink? It’s a multi-step journey, and each phase is crucial. Here’s the breakdown, explained in a way that’ll make sense whether you’re sketching designs or approving suppliers.
Step 1: Design and Planning—The Blueprint Phase
Every great component starts with a great plan. This is where you, the designer, shine. Using tools like CAD software, you map out every detail: dimensions, angles, tolerances. It’s like an architect drafting a blueprint for a house—except instead of walls and windows, you’re designing mounting points and ventilation slots.
I remember a project where we spent days tweaking a chassis design. The goal? Balance weight, strength, and manufacturability. We had to decide: go lightweight with aluminum and risk higher costs, or stick with steel for durability on a tighter budget? That’s the kind of real-world trade-off you’re navigating here, ensuring the design works for both the device and the production line.
Step 2: Material Selection—Picking the Right Metal
Not all metals are equal, and choosing the right one is like picking the perfect tool for a job. Here’s the lineup:
Aluminum: Light, rust-resistant, great for portable gadgets.
Steel: Tough as nails, ideal for heavy-duty applications.
Copper: Conducts heat and electricity like a champ, perfect for heat sinks or connectors.
Your choice depends on what the component needs to do. Designing a sleek wearable? Aluminum’s your friend. Building a server rack? Steel might be the way to go. It’s all about matching properties to purpose.
Step 3: Cutting—Shaping the Raw Material
Once you’ve got your metal, it’s time to cut it into shape. This is where raw sheets or bars get sliced up using methods like:
Laser Cutting: A high-tech beam zaps through metal with pinpoint accuracy.
Waterjet Cutting: Blasts water and abrasives to carve out shapes.
Shearing: Think giant scissors for metal—quick and straightforward.
It’s like a tailor cutting fabric to kick off a sewing project. I once watched a laser cutter slice through steel like butter—mesmerizing stuff. The precision here sets the stage for everything that follows.
Step 4: Forming—Bending It into Shape
Now, those flat pieces need to take on their final form. This is where forming comes in, using techniques like:
Bending: Folding metal along a line to create edges or angles.
Stamping: Pressing metal into a mold to shape it.
Rolling: Curving metal into cylinders or arcs.
Picture bending a paperclip to hook something—it’s that idea, but with industrial muscle. Forming’s where your design starts to look like the real deal.
Step 5: Joining—Putting It All Together
Next, those shaped pieces get assembled. Common methods include:
Welding: Melting metal edges to fuse them.
Riveting: Using metal pins for a secure hold.
Fasteners: Screws or bolts for a non-permanent join.
It’s like snapping together a model kit. I’ve tinkered with DIY projects where a solid weld made all the difference—there’s something satisfying about seeing parts become a whole.
Step 6: Finishing—The Final Polish
Last but not least, the component gets its finishing touches. This could mean:
Painting: Adds color and fights corrosion.
Anodizing: Toughens the surface (and looks cool doing it).
Plating: Coats the metal with something like nickel for extra perks.
Think of it like painting a wall—it’s both protective and aesthetic. A good finish can turn a functional part into something that looks as good as it performs.
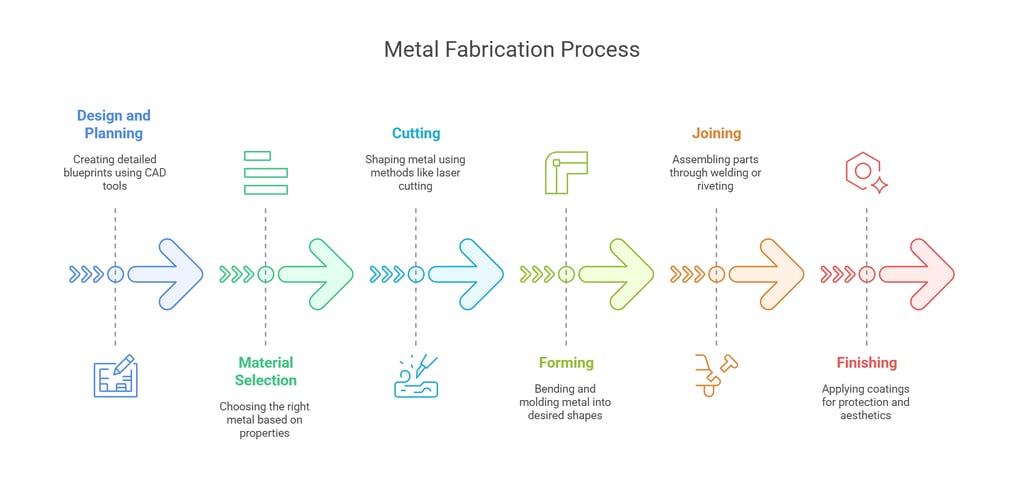
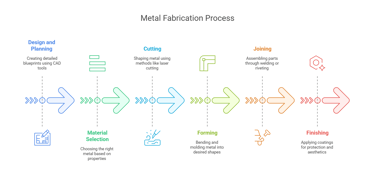
Wrapping It Up: Why This Matters to You
So, there you have it: metal fabrication in a nutshell. It’s the process that takes raw metal and transforms it into the enclosures, chassis, and connectors that make your electronics tick. For you—designers and decision-makers—it’s the key to creating products that are tough, precise, and reliable.
We’ve walked through:
What it is: Cutting, shaping, and assembling metal into finished parts.
Why it’s vital: Protection, precision, EMI shielding—the works.
How it happens: From design to finishing, step by step.
Metal fabrication isn’t just for big factories, either. Whether you’re mass-producing phone casings or prototyping a custom enclosure for a passion project, it’s a process that adapts to your needs. And with advancements like automated machining or even metal 3D printing, it’s more accessible than ever.
Next time you’re sketching a concept or reviewing a spec sheet, think about the craftsmanship behind those metal components. It’s not just engineering—it’s the art of bringing your ideas to life. Got a story about metal fabrication in your work? I’d love to hear it—drop a comment or shoot me a message. Let’s keep the conversation going!