Interview with an Industry Expert: Future-Proofing Your Manufacturing Process
Whether you are a hardware startup, an OEM decision-maker, or an engineer designing the next breakthrough product, future-proofing your manufacturing process is no longer optional—it’s a necessity.
2/19/20254 min read
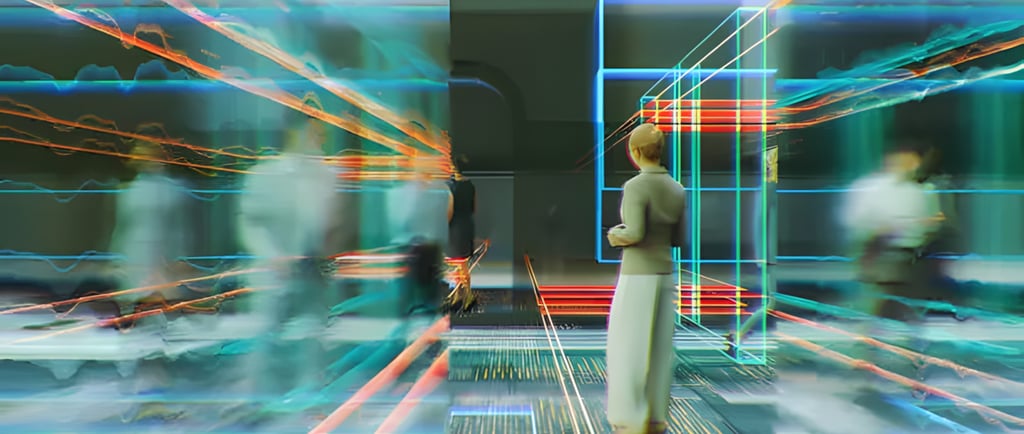
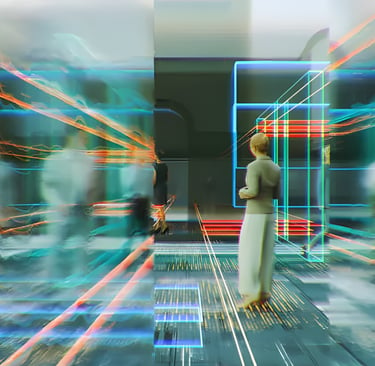
I. Introduction
In the fast-paced world of electronics development, manufacturing processes must evolve constantly to keep up with market demands, technological advancements, and unforeseen disruptions. Whether you are a hardware startup, an OEM decision-maker, or an engineer designing the next breakthrough product, future-proofing your manufacturing process is no longer optional—it’s a necessity.
To shed light on this critical topic, we sat down with Andrew Piaskow, a veteran in electronics manufacturing with over 50 years of experience in supply chain optimization, production scaling, and technology integration. In this interview, he shares insights on overcoming common industry challenges, embracing new technologies, and making strategic decisions that ensure long-term success.
II. Meet the Expert
Andrew has spent the last two decades working with global electronics brands and startups, helping them optimize their production pipelines, reduce costs, and navigate complex supply chains. With expertise spanning PCB assembly, component sourcing, and automation, he brings a well-rounded perspective on future-proofing strategies.
Why Should We Listen to Andrew?
Worked with leading EMS (Electronics Manufacturing Services) providers
Helped companies scale from prototypes to mass production
Deep experience in supply chain risk mitigation
Passionate about emerging technologies and their impact on manufacturing
Let’s dive into the conversation!
III. Current Challenges in Electronics Manufacturing
Before looking forward, it’s crucial to understand the present obstacles facing electronics manufacturers. Andrew identifies three major challenges that need immediate attention:
1. Supply Chain Disruptions
“The pandemic exposed how fragile our global supply chains are,” Andrew explains. “Many companies were caught off guard by component shortages, logistical delays, and geopolitical tensions.”
For instance, in 2021, the semiconductor shortage forced automotive and electronics companies, including Ford and Apple, to delay product releases. The crisis demonstrated the need for diversified supply chains and better inventory forecasting.
What this means for designers and decision-makers:
Relying on a single supplier is risky; diversifying is crucial.
Lead times for critical components (like semiconductors) are still volatile.
Regionalization is gaining traction—nearshoring can reduce risks.
2. Rising Costs and Shrinking Margins
Material and labor costs continue to rise, putting pressure on profitability. Manufacturers must find ways to increase efficiency without sacrificing quality.
For example, Foxconn, a leading electronics contract manufacturer, has invested heavily in automation to counter rising labor costs in China. By deploying AI-driven assembly lines, they have significantly reduced errors and increased output efficiency.
Key takeaways:
Automation and AI-driven optimization are becoming necessary investments.
Energy-efficient processes can help control costs in the long run.
Smart procurement strategies can mitigate price fluctuations.
3. Sustainability and Regulatory Compliance
Governments worldwide are pushing for stricter environmental regulations. E-waste laws, carbon footprint tracking, and sustainable material sourcing are no longer optional.
Companies like Apple and Dell have taken proactive steps by designing products with recyclability in mind and investing in closed-loop supply chains. Apple’s 2022 MacBook Air, for instance, uses 100% recycled aluminum, setting a standard for eco-friendly manufacturing.
Actionable insights:
Designers should prioritize energy-efficient components and modularity.
Manufacturers must adopt green production practices to stay competitive.
Companies with strong sustainability initiatives attract more investors and customers.
IV. Key Strategies for Future-Proofing Your Manufacturing Process
1. Embracing Advanced Technologies
AI & Machine Learning for Predictive Maintenance
Using AI-driven analytics, manufacturers can predict machine failures before they happen, minimizing downtime and improving efficiency.
For instance, Siemens has successfully implemented AI-powered predictive maintenance in its factories, reducing unplanned downtimes by 20% and saving millions in operational costs.
Automation & Robotics for Efficiency
Cobots (collaborative robots) enhance human labor, rather than replacing it.
Automated optical inspection (AOI) improves PCB defect detection.
SMT (surface-mount technology) automation accelerates production without sacrificing precision.
Foxconn’s "lights-out" factories in China are prime examples, where fully automated assembly lines produce components with minimal human intervention, increasing precision and reducing costs.
IoT-Enabled Smart Manufacturing
With IoT sensors monitoring production in real-time, manufacturers can:
Optimize energy consumption
Identify bottlenecks immediately
Ensure consistent product quality
GE’s "Brilliant Factories" initiative has leveraged IoT connectivity to enhance efficiency and reduce defects across multiple production sites.
2. Building a Resilient Supply Chain
Supplier Diversification
“We’ve seen too many companies suffer due to over-reliance on one supplier,” Andrew warns. “Work with multiple sources and establish backup suppliers.”
Tesla’s strategic move to source lithium and battery components from multiple suppliers has helped mitigate shortages and ensure steady EV production.
Digital Supply Chain Management
Real-time inventory tracking prevents stockouts.
AI-driven demand forecasting helps avoid overproduction.
Blockchain improves traceability and transparency.
IBM’s blockchain-based supply chain solutions have improved traceability in semiconductor manufacturing, reducing fraud and enhancing supplier accountability.
3. Sustainable Manufacturing Practices
Energy-Efficient Production
Investing in energy-efficient machinery reduces costs and aligns with global sustainability goals.
Intel has committed to achieving net-zero greenhouse gas emissions in its global operations by 2040, setting a precedent for sustainable manufacturing in electronics.
Circular Economy & E-Waste Reduction
Design for disassembly: Make products easier to repair and recycle.
Use recycled materials: Many big brands are moving towards this.
Optimize packaging: Reducing plastic and excess packaging benefits both the environment and costs.
HP has embraced circular economy principles by using recycled plastics in its ink cartridges and reducing packaging waste across its product lines.
4. Developing a Skilled Workforce
Upskilling for Industry 4.0
As automation rises, the need for skilled labor shifts towards programming, maintenance, and AI analytics.
Key initiatives:
Offer internal training programs for workers.
Partner with universities and technical schools.
Use AR/VR training tools for hands-on learning.
Siemens has partnered with multiple universities to create AI and automation training programs, ensuring a steady pipeline of skilled workers.
V. Real-World Case Studies
Case Study 1: How Cisco Reduced Lead Times by 40%
By implementing AI-powered inventory tracking and diversifying suppliers, Cisco overcame supply chain disruptions and improved delivery reliability during the 2020 chip shortage.
Case Study 2: Sustainability in Action—Tesla’s Gigafactories
Tesla’s Gigafactories leverage renewable energy, closed-loop battery recycling, and AI-driven automation to enhance production efficiency and reduce environmental impact.
Case Study 3: Workforce Transformation at Bosch
Bosch invested in Industry 4.0 training programs, leading to a 25% increase in production efficiency and reduced employee turnover.
VIII. Conclusion
Future-proofing isn’t about predicting the future; it’s about preparing for it. Electronics manufacturers that embrace innovation, resilience, and sustainability will not only survive but thrive in the coming years.
Are you ready to take the next step? Engage with industry experts, attend manufacturing expos, and explore new technologies that can transform your production process today.