Injection Molding vs. 3D Printing: Which is Right for Your Electronics Project?
The clock’s ticking, budgets are tight, and the manufacturing choice you make could make or break your project. In one corner, there’s injection molding, the tried-and-true titan of mass production. In the other, 3D printing, the nimble newcomer shaking up prototyping and customization.
2/22/20255 min read

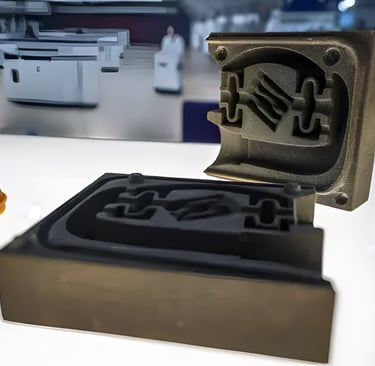
Imagine you’re an electronics designer at a startup, tasked with bringing a cutting-edge wearable to life—say, a fitness tracker with a sleek, ergonomic shell. Or maybe you’re a decision-maker at a firm like Texas Instruments, greenlighting enclosures for a new line of IoT sensors. Either way, the clock’s ticking, budgets are tight, and the manufacturing choice you make could make or break your project. In one corner, there’s injection molding, the tried-and-true titan of mass production. In the other, 3D printing, the nimble newcomer shaking up prototyping and customization. So, which one’s right for your electronics gig?
I’ve been down this road myself—agonizing over specs, costs, and timelines—so I know how high the stakes feel. Let’s dig into these two methods with a focus on electronics development, armed with real-world examples, hard data, and lessons from the field. By the end, you’ll have the clarity to pick the winner for your project. Let’s roll.
Understanding Injection Molding
What is Injection Molding?
Injection molding is like the industrial version of a chef’s perfect soufflé mold. You melt plastic—say, ABS or polycarbonate—at scorching temperatures (up to 300°C), shoot it into a precision-crafted steel or aluminum mold under pressures reaching 20,000 psi, let it cool, and out pops a part. It’s been a cornerstone since the 1940s, powering mass production for everything from phone chargers to car dashboards.
Key Features
This process is a stickler for detail—parts hit tolerances as tight as ±0.005 inches, critical for electronics where a misaligned connector can spell disaster. You’re working with materials like flame-retardant ABS (think laptop shells) or glass-filled nylon for extra strength. The catch? That mold isn’t cheap or fast—think weeks to design and machine, plus a hefty price tag.
Advantages
Injection molding shines when you’re scaling up. Take Apple: their AirPods cases are injection-molded, cranking out millions with flawless finishes and durability—drop one, and it barely scratches. At volume, costs plummet to cents per part. A 2022 study from Plastics Technology pegged per-unit costs at $0.10-$0.50 for runs over 10,000, a steal compared to alternatives. Plus, the surface quality? Smooth as glass, no post-processing needed.
Disadvantages
The upfront hurdle is real. A mold for a simple PCB enclosure might run $5,000; for a complex multi-part wearable, you’re looking at $20,000-$50,000, per MoldMaking Technology’s 2023 estimates. Lead times stretch 4-8 weeks—tough if your CES demo is next month. And design changes? A tweak to add a USB-C port could mean remachining the mold, costing thousands more and stalling production.
Understanding 3D Printing
What is 3D Printing?
Now picture this: no molds, just a printer building your part layer by layer from a digital blueprint. That’s 3D printing—additive manufacturing—born in the 1980s with stereolithography and now a darling of innovators. For electronics, it’s a game-changer: think custom drone mounts or prototype circuit housings printed overnight.
Key Features
You’re free from tooling shackles—upload a CAD file, tweak it, and print. Materials span PLA (cheap, easy) to ESD-safe PETG for static-sensitive electronics, even metal alloys via DMLS (Direct Metal Laser Sintering). It’s iterative heaven: I’ve tweaked a sensor case design three times in a day, reprinting each version. Speed’s decent—hours, not weeks—and complexity is no sweat.
Advantages
Low-volume runs and prototyping are where 3D printing flexes. Stratasys, a 3D printing leader, cites cases like NASA printing custom brackets for satellite electronics—10 units, intricate lattice designs, done in 48 hours. Costs are upfront-friendly: a $500 printer like the Creality Ender 3 plus $30 filament gets you started. For small batches or bespoke designs—like a one-off medical device—nothing beats it. A 2023 Gartner report noted 70% of companies now use 3D printing for prototypes, slashing development cycles by 25%.
Disadvantages
Scale’s the Achilles’ heel. Printing 1,000 fitness tracker shells? At 2-4 hours each on a mid-range printer, you’re tied up for months—or shelling out for a farm of machines. Costs hover at $1-$5 per part, per Formlabs’ 2024 data, dwarfing injection molding at volume. And finish? FDM prints often show layer lines—fine for prototypes, but your consumer gadget might need sanding or resin coating, adding labor.
Comparing Injection Molding and 3D Printing
Let’s pit these against each other, zeroing in on electronics needs—think enclosures, connectors, or wearable casings.
Cost
Injection Molding: High entry, low long-term. A mold for a smart thermostat case might cost $10,000, but at 50,000 units, you’re at $0.20 each. Fitbit’s Versa line likely leaned on this math.
3D Printing: Low entry, high per-unit. Printing 50 prototypes on a $1,000 printer with $50 filament totals $2-$3 each. Scale to 50,000? You’re bankrupt—or buying 100 printers.
Speed
Injection Molding: Mold prep takes 6 weeks, but production’s lightning—10-second cycles. Samsung churns out Galaxy Buds cases this way, hitting millions fast.
3D Printing: A single PCB housing prints in 3 hours—perfect for a pitch. But 500 units? Weeks, even with multiple machines.
Volume
Injection Molding: Built for mass. Logitech’s molded mouse shells flood stores—hundreds of thousands monthly.
3D Printing: Niche king. A startup I know printed 30 custom IoT sensor cases for a trade show—spot-on for small runs.
Design Complexity
Injection Molding: Simple shapes rule. A Raspberry Pi case? Easy. A hollowed-out, curvy wearable? Mold headaches galore—think draft angles and parting lines.
3D Printing: Complexity’s playground. Shapeways printed a fractal-inspired drone mount for a client—impossible with molds.
Material Options
Injection Molding: ABS, PC, POM—electronics staples. UL94 V-0 rated plastics for fire safety? Covered. But you’re mold-bound.
3D Printing: TPU for flexible clips, carbon-fiber blends for strength, even conductive PLA for circuits. Proto-pasta’s ESD filament protects sensitive boards—niche, but growing.
Scalability
Injection Molding: Scales effortlessly. One mold, endless output—think Anker’s power banks.
3D Printing: Scales clunkily. Formlabs’ Form 3 can print 5-10 parts daily; scale needs a fleet.
Which Should You Choose?
Your call hinges on your project’s DNA. Let’s break it down.
When to Choose Injection Molding
High-Volume Runs: Launching a consumer hit like Tile trackers? You need 100,000+ units—molding’s your lifeline. A 2023 Deloitte study found 85% of mass electronics rely on it.
Polished Quality: Need a glossy, durable finish for a smart speaker? Amazon Echo’s shells scream injection molding—zero post-work.
Budget Flexibility: If your VC-backed wearable has $50,000 for tooling, the ROI at scale is unbeatable.
When to Choose 3D Printing
Prototyping: Testing a new BLE module case? Print it, test it, tweak it. Dyson’s engineers 3D-printed 500+ vacuum prototypes before molding.
Low-Volume or Niche: A client needs 20 custom RFID reader housings? Printed, shipped, done. Medtronic uses this for surgical tool prototypes.
Speed to Market: Pitching at Electronica in two weeks? Print your demo unit now—no mold delays.
The Hybrid Play
Smart teams mix it up. Take Ring: early doorbell prototypes were 3D-printed to perfect the design—hundreds of iterations—before molding millions for retail. A 2024 McKinsey report found 40% of electronics firms now use this combo, cutting time-to-market by 30%. I’ve seen it firsthand: a pal’s startup printed IoT gateway shells, got user feedback, then molded the final run.
Real-World Examples
Injection Molding: GoPro’s Hero camera housings—rugged, precise, millions made. Molded ABS keeps costs low and quality high.
3D Printing: Lockheed Martin printed titanium brackets for F-35 electronics—20 units, complex geometry, no mold hassle. Or LulzBot’s open-source printer parts—small-batch perfection.
Hybrid: Sonos prototyped speaker grilles with 3D printing—50 versions—before molding the final design for Best Buy shelves.
Conclusion
Injection molding’s your mass-production beast—cost-effective, fast, flawless at scale, but it demands cash and patience upfront. 3D printing’s the agile innovator—quick, flexible, ideal for prototypes or small runs, yet it falters at volume. For electronics designers and deciders, it’s a gut-check: How many units? How fast? How complex? I’ve stared at these crossroads over late-night coffee, and here’s my take: prototype with 3D printing to nail your vision, then mold for the big leagues if it fits.
Your smartwatch, sensor, or speaker deserves the right path. Crunch your numbers—budget, timeline, scale—and choose boldly. Still wrestling? Toss your project in the comments—I’d love to hash it out with you. Let’s build something epic.