Injection Molding Tooling: How to Design Cost-Effective Molds
Molds aren’t cheap, and in an industry where margins are tight and timelines are tighter, every dollar counts. But here’s the good news: with some smart strategies, you can slash those costs and make your molds work harder for you, all without sacrificing quality.
2/23/20256 min read
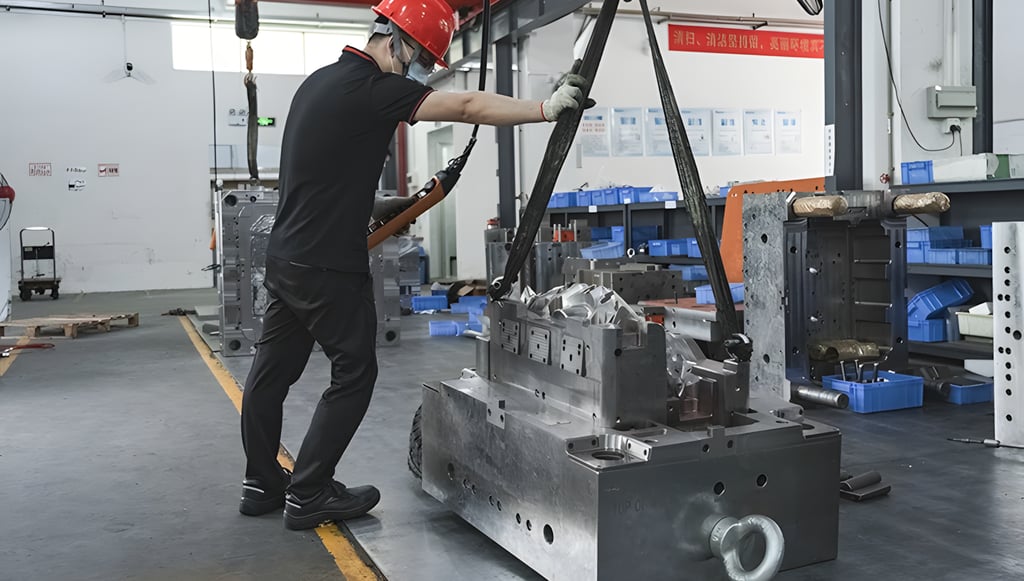
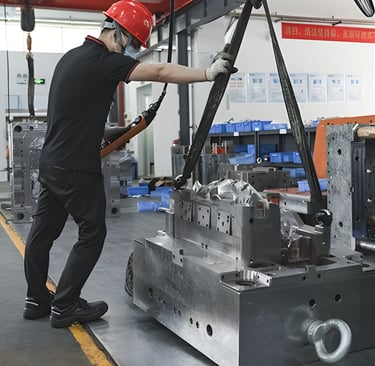
If you’re in electronics development, you’ve probably felt the sting of injection molding costs at some point. Designing plastic enclosures, connectors, or tiny components for your next big gadget is exciting—until you see the tooling bill. Molds aren’t cheap, and in an industry where margins are tight and timelines are tighter, every dollar counts. But here’s the good news: with some smart strategies, you can slash those costs and make your molds work harder for you, all without sacrificing quality.
I’ve been around the block with injection molding—worked with designers who’ve cried over budget overruns and decision-makers who’ve had to explain delays to impatient stakeholders. What I’ve learned is this: cost-effective molds start with thoughtful design. This isn’t about cutting corners; it’s about working smarter. So, let’s dive into how you, the designer or decider in electronics, can create molds that save money, boost efficiency, and keep your project on track.
Understand Your Product Requirements
First things first: know what you’re building and why. In electronics, every part has a job—whether it’s a sleek phone casing or a humble connector housing delicate pins. Before you even sketch a mold, ask yourself: How many units do I need? What’s the material? How precise does this have to be?
I’ve seen teams sink cash into over-engineered molds because they didn’t stop to think. Picture this: a designer specs a mold for a low-volume prototype run with tolerances tighter than a Swiss watch. Sure, it works, but it’s like buying a Ferrari to drive to the corner store—overkill. Keep it simple where you can. If your part doesn’t need aerospace-grade precision, don’t design the mold for it. Loose tolerances a bit where possible, and you’ll save on machining time and headaches down the line.
Optimize Part Design for Moldability
Here’s where the rubber meets the road—or, I suppose, where the plastic meets the mold. As an electronics designer, you’re probably juggling aesthetics, functionality, and manufacturability. That’s a lot, but small tweaks to your part design can make a huge difference in mold costs. This is Design for Manufacturability (DFM) in action, and it’s your best friend.
Start with uniform wall thickness. Uneven walls sound harmless, but they’re a cooling nightmare—some areas solidify faster than others, leading to warping or sink marks. For an electronics housing, aim for consistent walls (say, 1.5–2 mm for most thermoplastics like ABS or polycarbonate). It cuts material use and simplifies the mold, saving you cash.
Next, watch out for undercuts or tricky features. That cool snap-fit latch on your enclosure? If it needs a side action in the mold, you’re adding complexity and cost. Simplify where you can—maybe a slight redesign gets you the same function without extra mold parts. And don’t forget draft angles. A 1–2-degree taper on vertical walls makes ejection a breeze, reducing wear on the mold and keeping it running longer. I once worked with a team who skipped this step; their mold jammed after 500 cycles, and the repair bill wasn’t pretty.
Choose the Right Mold Type
Not all molds are created equal, and picking the right one can make or break your budget. In electronics, you might be prototyping a wearable device one day and mass-producing a USB hub the next. Match the mold to the mission.
Single-cavity molds are great for low volumes or testing—cheap to make, quick to tweak. But if you’re cranking out 50,000 enclosures, multi-cavity molds spread the cost per part and speed things up. I’ve seen decision-makers hesitate here, worried about the upfront price tag. Fair enough, but think long-term: a four-cavity mold might cost twice as much initially but halve your production time.
For small runs of related parts—like a set of connectors—consider a family mold. It’s one tool that makes multiple components in a single shot. Just be sure the parts have similar material and shrinkage rates, or you’ll be troubleshooting defects instead of celebrating savings.
Material Selection for Molds
Now, let’s talk mold materials. Steel or aluminum? It’s the classic debate. Steel molds (like P20 or H13) are tough as nails—perfect for high-volume runs of, say, millions of phone cases. They last forever but take longer to machine and cost more upfront. Aluminum, on the other hand, is softer but faster and cheaper to cut. For a prototype or a run of 10,000 units, it’s often the sweet spot.
In electronics, where timelines are brutal, I lean toward aluminum for early stages. I once had a client who needed a mold for a limited-run IoT device—aluminum got us from design to parts in half the time steel would’ve taken. For bigger jobs, though, consider a hybrid: an aluminum base with steel inserts in high-wear spots like ejector pins or sharp corners. You get durability where it counts without breaking the bank.
Leverage Efficient Cooling Systems
Cooling might sound boring, but it’s the unsung hero of injection molding. The faster your mold cools, the quicker you pop out parts—and in electronics, where production schedules are relentless, that’s gold. A poorly designed cooling system means longer cycles, warped parts, and a bigger electricity bill. No thanks.
Standard cooling channels—straight lines drilled through the mold—work fine for simple parts. But if your electronics component has complex geometry (think heat sinks or ribbed enclosures), optimize those channels. Place them closer to hot spots to avoid uneven cooling. For high-stakes projects, conformal cooling—channels that follow the part’s shape—can cut cycle times by 20–30%. Yes, it’s pricier to make (think 3D-printed mold inserts), but if you’re running 100,000+ parts, the savings add up fast. I’ve seen it firsthand: a team shaved 5 seconds off a 20-second cycle, and over a million parts, that’s real money.
Minimize Maintenance and Downtime
A mold that’s down for repairs is a mold that’s costing you. In electronics, where missing a product launch can tank your quarter, downtime is the enemy. Design your molds to last and be easy to fix.
Start with durability. High-wear areas—like where ejector pins hit or where molten plastic rushes in—benefit from hardened steel or coatings like titanium nitride. It’s a small upfront cost to avoid frequent replacements. I once saw a mold fail because the team skimped here; 10,000 cycles in, and the pins were toast.
Modularity is another trick. Design your mold with interchangeable inserts or components. If a cavity wears out, swap it instead of reworking the whole tool. It’s like Lego for manufacturing—fast, flexible, and cost-effective. Less downtime means more parts out the door, keeping your production line humming.
Collaborate Early with Mold Makers
Here’s a tip I wish someone had drilled into me earlier: don’t design in a vacuum. Your mold maker isn’t just a fabricator—they’re a goldmine of practical know-how. Bring them in before your design’s locked in, and they’ll spot cost traps you’d never see. That tricky rib you added for strength? They might suggest a tweak that avoids an expensive side action.
Better yet, use mold flow simulation software together. It’s like a crystal ball—showing how plastic will fill, cool, and shrink before you cut steel. I’ve watched teams skip this step, only to face $5,000 in rework when parts came out warped. Collaboration and tech upfront save you from costly do-overs.
Balance Upfront Costs vs. Long-Term Savings
This one’s for the decision-makers pulling the purse strings. It’s tempting to go cheap on a mold—lowest bidder, basic design, done. But pause and crunch the numbers. A $10,000 mold with a 30-second cycle might seem like a steal compared to a $15,000 mold with a 24-second cycle. Now run 100,000 parts: the cheaper mold takes 833 hours, the pricier one 667 hours. Factor in labor, machine rates, and lost time, and the “expensive” mold wins.
It’s about total cost of ownership. Spend a bit more on better cooling or tougher materials, and your per-part cost drops. I’ve pitched this to skeptical bosses before—show them the math, and they’ll see it’s not splurging, it’s investing.
Conclusion
Designing cost-effective molds isn’t rocket science, but it does take intention. Keep your part designs mold-friendly, pick the right mold type and materials, optimize cooling, and build for longevity. Loop in your mold maker early, and always weigh upfront costs against long-term gains.
In electronics, where innovation moves at warp speed, every penny and every minute counts. A well-designed mold doesn’t just save money—it keeps you competitive, letting you focus on what matters: building the next game-changing device. So, next time you’re sketching a part or signing off on a tooling budget, run through these tips. Your wallet—and your team—will thank you.