Injection Molding Success Stories: Real-World Examples from Peakingtech
That’s the magic of injection molding—and at Peakingtech, we’ve seen it work wonders time and again. For designers and decision-makers in electronics development, this isn’t just a manufacturing process—it’s a lifeline to turning bold ideas into real, market-ready solutions.
2/24/20256 min read
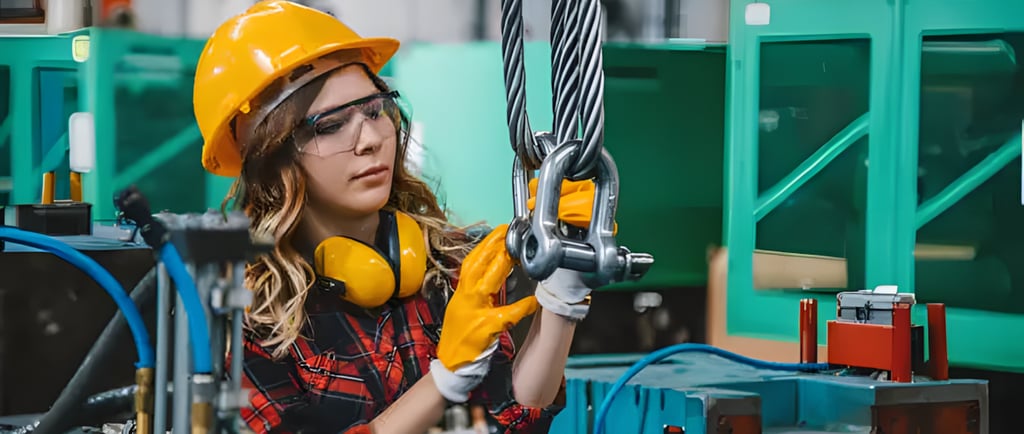
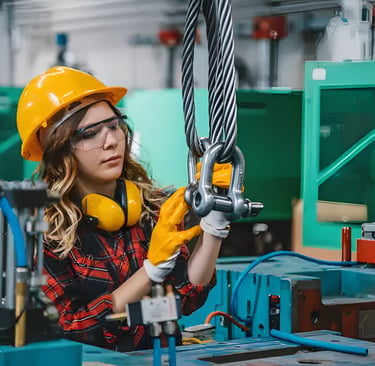
Imagine you’re holding a sleek, perfectly crafted circuit housing in your hand. It’s lightweight, durable, and fits like a glove around the electronics inside. Now picture this: that same piece might have saved a project timeline, slashed production costs, or even made a product launch possible. That’s the magic of injection molding—and at Peakingtech, we’ve seen it work wonders time and again. For designers and decision-makers in electronics development, this isn’t just a manufacturing process—it’s a lifeline to turning bold ideas into real, market-ready solutions.
Injection molding is the unsung hero of precision manufacturing, and we’ve had a front-row seat to its transformative power in the electronics space. From tight tolerances to high-volume runs, it’s how we help innovators like you bring concepts to life. Today, I want to walk you through three real-world success stories from Peakingtech that showcase what’s possible when you pair creative design with our molding expertise. These aren’t just case studies—they’re proof of what we can do together. Let’s dive in.
The Power of Injection Molding: Why It Matters in Electronics
If you’re in electronics development, you know the stakes are high. Your designs demand precision down to the micron, materials that can handle heat and stress, and timelines that don’t budge. Injection molding delivers on all fronts. It’s fast, scalable, and lets us churn out parts with consistency that hand-assembly could never touch. Whether it’s a tiny enclosure for a wearable device or a rugged housing for industrial controls, this process is the backbone of modern electronics manufacturing.
At Peakingtech, we’ve honed this craft specifically for your world. We’re not just molding plastic—we’re shaping solutions that fit your specs, your budget, and your vision. The stories I’m about to share show how we’ve tackled some hairy challenges and come out on top, all while keeping designers and decision-makers like you in the driver’s seat.
Success Story #1: The Wearable That Almost Wasn’t
Let’s start with a project that hit close to home for anyone designing wearables. A client came to us with a prototype for a fitness tracker—think Fitbit but with a twist: it had to be ultra-light, water-resistant, and stylish enough to wear 24/7. The catch? Their initial design had a housing with such tight tolerances that their previous supplier couldn’t make it work without insane costs or delays. Deadlines were looming, and they were starting to sweat.
We sat down with their team—designers, engineers, the whole crew—and got to work. The challenge wasn’t just the precision; it was the material. They needed something lightweight but tough, and the geometry of the part had these tricky undercuts that screamed “nightmare” for molding. Our solution? We paired a high-performance polycarbonate with a custom multi-cavity mold we designed in-house. Then we tweaked the gating system to ensure flawless flow—no warping, no weak spots.
The result was a game-changer. We delivered 50,000 units in under six weeks, shaving 25% off their expected production time. The client’s lead designer told me later, “You didn’t just save the project—you made it better than we imagined.” That tracker hit the market on time, racked up rave reviews, and even snagged a design award. For us, it was a reminder of why we love this work: turning “impossible” into “done.”
Success Story #2: The IoT Hub That Scaled Up Fast
Next up is a story for anyone who’s ever had to pivot mid-project. Picture this: an IoT startup designing a smart home hub reached out to us. Their device was a beauty—compact, with a glossy finish and a snap-fit assembly that had to feel premium. They’d nailed the prototype, but demand exploded after a successful Kickstarter. Suddenly, they needed to go from 1,000 units to 100,000 in a matter of months. Oh, and they wanted it sustainable, too—because why not add a little pressure?
The hurdle here was twofold: scaling production without sacrificing that premium look and feel, and finding a material that checked the eco-friendly box. We could’ve gone the easy route with a standard resin, but that’s not our style. Instead, we collaborated with their design team to tweak the mold for high-volume runs—think four cavities, optimized cooling channels, the works. For the material, we sourced a bio-based polymer that hit their sustainability goals without compromising strength or finish.
The outcome? We ramped up to 100,000 units in record time, and the hubs flew off the shelves. Their CEO sent us a note saying, “Peakingtech didn’t just meet our crazy deadline—you made us look good doing it.” That glossy finish? Spotless. The snap-fit? Perfect every time. And knowing we helped a startup grow while keeping things green felt pretty darn good.
Success Story #3: The Industrial Control That Took a Beating
Now, let’s shift gears to something a bit grittier. Anindustrial electronics firm tapped us for a control module housing—think of it as the brain for heavy machinery. This wasn’t a consumer gadget; it had to survive dust, vibration, and temperatures that’d make most plastics cry. Plus, it needed to meet strict UL certification standards, and their timeline was tighter than a drum. Their designers were stressed, and the decision-makers were watching the clock.
The challenge was brutal: the part had complex geometry with reinforced ribs, and the material had to be flame-retardant and impact-resistant. We rolled up our sleeves and got creative. First, we used 3D-printed prototypes to nail the design before committing to steel tooling—saved us weeks of back-and-forth. Then we went with a glass-filled nylon blend, fine-tuned the mold for even wall thickness, and ran simulations to ensure it’d hold up under stress.
When the dust settled, we delivered a housing that passed UL testing with flying colors and hit the production floor ahead of schedule. The client’s engineering lead pulled me aside at a trade show later and said, “Your team took a weight off our shoulders—we couldn’t have launched without you.” That module’s still out there, keeping machines humming in factories worldwide. For us, it’s a badge of honor.
What These Stories Reveal About Peakingtech
So, what ties these projects together? It’s not just that we’re good at molding plastic—though we are. It’s that we get the electronics world. We know you’re juggling deadlines, budgets, and specs that’d make lesser teams blink. At Peakingtech, we’ve got the tools—think cutting-edge presses and in-house mold design—and the know-how to make your vision real. But more than that, we’re in it with you. Every late-night call with a designer, every tweak to a mold, every “aha” moment—it’s personal for us.
These stories show we’re not just a vendor; we’re a partner. Whether it’s a wearable, an IoT hub, or an industrial beast, we bring precision, speed, and a little bit of grit to the table. Our clients trust us because we’ve been doing this long enough to know what works—and we’re still hungry enough to push the boundaries.
Lessons Learned: Tips for Injection Molding Success
If you’re a designer or decision-maker reading this, let me leave you with a few nuggets we’ve picked up along the way. First, get your molding team involved early. Those wearables? That IoT hub? They worked because we hashed out details upfront—no surprises later. Second, don’t skimp on material choice—it’s the difference between “good enough” and “great.” And third, test the heck out of your design before you scale. A quick prototype can save you a mountain of headaches.
These aren’t trade secrets—just hard-earned lessons from folks who’ve been in the trenches. We’re happy to share because we want your next project to shine, whether it’s with us or not (though we’d love to be part of it).
Conclusion
From a fitness tracker that beat the odds to a smart hub that scaled like wildfire to a control module that laughs at tough conditions—these are the stories that fuel us at Peakingtech. Injection molding isn’t just a process; it’s how we help electronics innovators like you turn sketches into successes. We’ve got the tech, the team, and the track record to prove it.
So, what’s your next big idea? A groundbreaking wearable? A game-changing IoT device? Let’s make it happen. Drop us a line, and we’ll sit down—virtually or over coffee—and figure out how to mold your vision into reality. Because at Peakingtech, your success story is the one we’re itching to tell next.